Introduction
What is metal powder?
Metal powder is a key component in the field of 3D printing, specifically for printing objects using metal materials. It is a finely ground substance that consists of tiny particles of metal. Metal powder is used as the raw material in the 3D printing process, where it is selectively melted and solidified layer by layer to create complex metal objects. The properties of the metal powder, such as its composition, particle size, and shape, play a crucial role in determining the quality and characteristics of the final printed object. Different types of metal powders, such as stainless steel, titanium, and aluminum, are available for various applications in industries like aerospace, automotive, and healthcare. The use of metal powder in 3D printing has revolutionized the manufacturing industry by enabling the production of intricate and customized metal parts with high precision and efficiency.
History of metal powder in 3D printing
The history of metal powder in 3D printing dates back to the early 1990s when the concept of additive manufacturing was first introduced. Initially, metal powders were not widely used due to technological limitations and high costs. However, with advancements in technology and the development of new alloys, metal powders became increasingly popular in 3D printing. Today, metal powder-based 3D printing is widely used in various industries, including aerospace, automotive, and healthcare, due to its ability to create complex and high-performance metal parts with precision and efficiency.
Advantages of using metal powder in 3D printing
Metal powder is widely used in 3D printing due to its numerous advantages. One of the key benefits of using metal powder is its ability to create complex and intricate designs that would be difficult or impossible to achieve with traditional manufacturing methods. Additionally, metal powder allows for greater design flexibility, as it can be easily customized and tailored to meet specific requirements. Another advantage is the superior mechanical properties of metal powder parts, which exhibit high strength, durability, and resistance to wear and corrosion. Furthermore, using metal powder in 3D printing can result in cost savings, as it reduces material waste and allows for efficient production. Overall, the use of metal powder in 3D printing offers a range of advantages that make it a preferred choice for various industries and applications.
Types of Metal Powders
Stainless steel powder
Stainless steel powder is a popular material used in 3D printing due to its excellent mechanical properties and corrosion resistance. It is commonly used in various industries, including aerospace, automotive, and medical. The powder is made by atomizing molten stainless steel into fine particles, which can then be used as feedstock for 3D printing processes such as selective laser melting (SLM) or binder jetting. The use of stainless steel powder in 3D printing allows for the production of complex and durable metal parts with high precision and accuracy. Additionally, the ability to customize the composition and properties of the powder further enhances its versatility in different applications. Overall, stainless steel powder is a key component in the advancement of metal 3D printing technology and continues to play a crucial role in the manufacturing industry.
Titanium powder
Titanium powder is one of the most commonly used materials in metal 3D printing. It offers excellent strength-to-weight ratio, corrosion resistance, and biocompatibility, making it a popular choice for a wide range of applications. Titanium powder is known for its high melting point, which allows for the production of complex and intricate designs. Additionally, it can be easily sintered and has good thermal conductivity, making it suitable for creating functional prototypes and end-use parts. With its unique properties, titanium powder is revolutionizing the field of additive manufacturing and opening up new possibilities for industries such as aerospace, medical, and automotive.
Aluminum powder
Aluminum powder is a widely used material in the field of metal powder for 3D printing. It is known for its excellent properties such as high strength, lightweight, and corrosion resistance. Aluminum powder is commonly used in various industries, including aerospace, automotive, and construction. Its ability to be easily shaped and formed makes it an ideal choice for manufacturing complex parts and components. Additionally, aluminum powder has good thermal conductivity, making it suitable for applications that require efficient heat dissipation. Overall, aluminum powder plays a crucial role in advancing the capabilities of 3D printing technology and enabling the production of innovative and functional metal parts.
Metal Powder Production
Atomization process
The atomization process is a crucial step in the production of metal powder for 3D printing. It involves the conversion of molten metal into fine droplets or particles. This process is typically achieved through various techniques such as gas atomization, water atomization, or plasma atomization. Gas atomization is the most commonly used method, where a high-pressure gas is used to break up the molten metal stream into small droplets. These droplets solidify rapidly as they cool down, resulting in the formation of metal powder. The atomization process plays a significant role in determining the characteristics of the metal powder, including its particle size, shape, and composition. It is essential to optimize this process to ensure the production of high-quality metal powder for 3D printing applications.
Gas atomization
Gas atomization is a commonly used method in the production of metal powders for 3D printing. This process involves injecting a high-pressure gas, such as nitrogen or argon, into a molten metal stream. As the gas interacts with the molten metal, it breaks it up into small droplets, which solidify into fine powder particles as they cool. Gas atomization offers several advantages for producing metal powders, including a high degree of control over particle size and shape, as well as the ability to produce powders with a high level of purity. Additionally, this method allows for the production of powders with a wide range of alloys and compositions, making it suitable for various applications in 3D printing.
Water atomization
Water atomization is one of the most commonly used methods for producing metal powders for 3D printing. This process involves the rapid cooling of molten metal by spraying it with water. As the molten metal comes into contact with the water, it solidifies and breaks up into small droplets, which then solidify into fine metal powders. Water atomization offers several advantages, including the ability to produce powders with a wide range of particle sizes and shapes, as well as excellent powder flowability. Additionally, this method is cost-effective and environmentally friendly, making it a popular choice in the 3D printing industry.
Metal Powder Properties
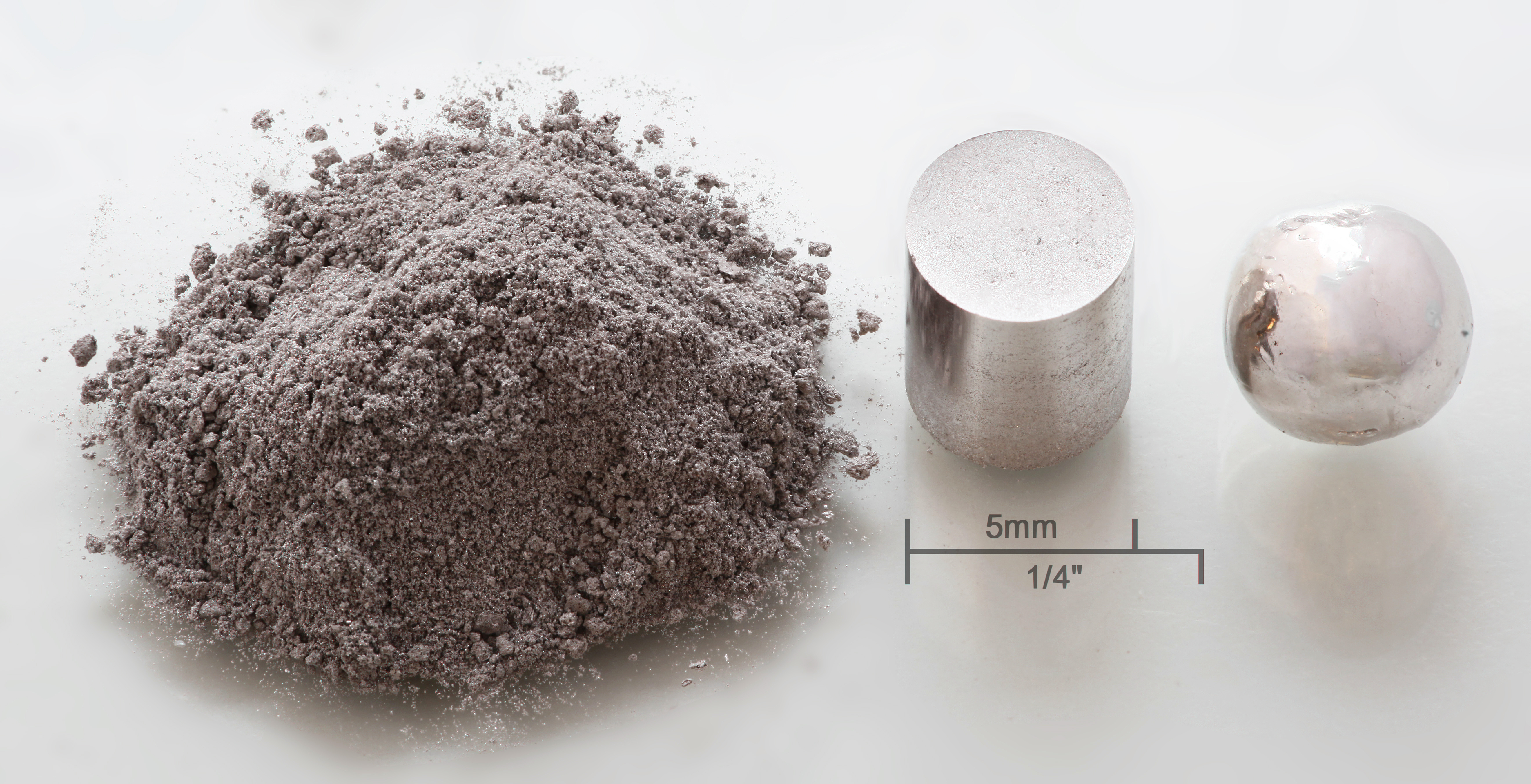
Particle size distribution
Particle size distribution is a crucial factor in metal powder for 3D printing. It refers to the range of particle sizes present in the powder. The particle size distribution directly affects the flowability, packing density, and sinterability of the powder. In 3D printing, an even particle size distribution is desirable as it ensures uniformity and consistency in the printed parts. A narrow particle size distribution allows for better control over the printing process, resulting in high-quality and accurate prints. Manufacturers carefully analyze and optimize the particle size distribution to meet the specific requirements of different printing techniques and applications. By understanding and manipulating the particle size distribution, engineers and designers can achieve desired mechanical properties, surface finish, and overall performance in their 3D printed metal parts.
Chemical composition
The chemical composition of metal powders used in 3D printing plays a crucial role in determining the properties and characteristics of the final printed parts. Different metals have varying compositions, which directly impact the strength, durability, and performance of the 3D printed objects. For example, titanium powders typically have a high percentage of titanium, along with small amounts of other elements to enhance specific properties. Similarly, aluminum powders may contain aluminum as the primary component, along with alloying elements such as copper or silicon. Understanding the chemical composition of metal powders is essential for selecting the right material for a desired application and achieving the desired mechanical properties in 3D printed parts.
Flowability and density
Flowability and density are important characteristics to consider when working with metal powder for 3D printing. Flowability refers to the ability of the powder particles to flow freely and evenly, ensuring a consistent and uniform distribution during the printing process. A powder with good flowability will result in better print quality and reduce the risk of clogging or uneven deposition. Density, on the other hand, determines the strength and durability of the final printed part. Higher density powders will produce stronger parts with improved mechanical properties. It is crucial to select a metal powder with the right balance of flowability and density to achieve optimal printing results.
Metal Powder Handling and Safety
Storage and transportation
Metal powders used in 3D printing need to be stored and transported with utmost care to ensure their quality and integrity. Due to their fine particle size and reactive nature, metal powders are susceptible to oxidation, moisture absorption, and contamination. Therefore, it is crucial to store them in a controlled environment with low humidity and oxygen levels. Additionally, proper labeling and documentation should be maintained to track the origin, batch number, and other important information of the metal powders. During transportation, measures should be taken to prevent any physical damage or exposure to extreme temperatures. By following these guidelines, manufacturers and users can ensure that the metal powders retain their desired properties and deliver consistent results in 3D printing applications.
Safety precautions
When working with metal powder for 3D printing, it is essential to take proper safety precautions. Metal powders can be hazardous if not handled correctly, as they can be flammable and pose a risk of respiratory irritation. It is important to wear appropriate personal protective equipment, such as gloves and a respirator, to minimize exposure to the powder. Additionally, working in a well-ventilated area and keeping the powder away from open flames or sparks is crucial. By following these safety measures, the risks associated with handling metal powder can be significantly reduced, ensuring a safe and productive 3D printing process.
Handling and disposal
Handling and disposal of metal powder is a crucial aspect when it comes to 3D printing. Due to its fine particle size, metal powder can pose health and safety risks if not handled properly. It is important to follow strict guidelines and protocols to ensure the safe handling and disposal of metal powder. This includes using appropriate personal protective equipment (PPE), such as gloves and masks, to minimize exposure to the powder. Additionally, metal powder should be stored in a secure and well-ventilated area to prevent the risk of fire or explosion. When it comes to disposal, it is recommended to consult local regulations and guidelines to determine the proper methods for disposing of metal powder waste. Proper handling and disposal of metal powder is essential for maintaining a safe working environment and minimizing any potential environmental impact.
Applications of Metal Powder in 3D Printing
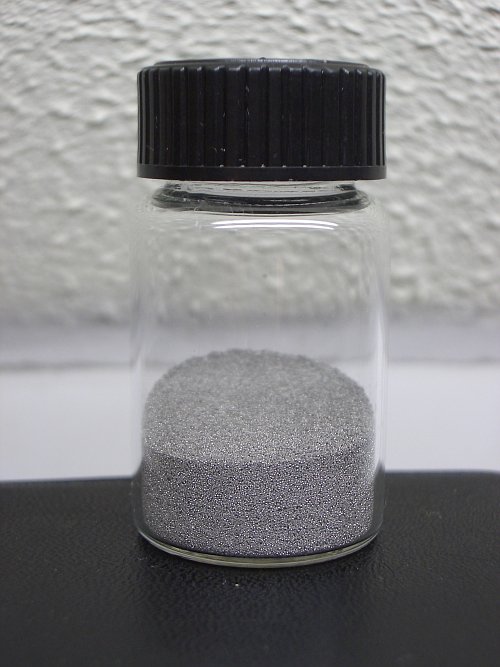
Aerospace industry
The aerospace industry is one of the key sectors benefiting from the advancements in metal powder for 3D printing. With its ability to produce complex and lightweight components, 3D printing has revolutionized the manufacturing process in aerospace. Metal powder used in 3D printing allows for the creation of intricate designs and shapes that were previously impossible or costly to produce. This technology has enabled aerospace companies to reduce weight, improve fuel efficiency, and enhance overall performance of aircraft. From engine parts to structural components, metal powder for 3D printing has opened up new possibilities for innovation in the aerospace industry.
Medical industry
The medical industry has greatly benefited from the advancements in metal powder for 3D printing. With the ability to create complex and customized medical implants, 3D printing has revolutionized the field of healthcare. Metal powders such as titanium and stainless steel are used to create implants that are biocompatible, durable, and lightweight. This has led to improved patient outcomes, reduced surgery time, and enhanced patient comfort. Additionally, 3D printing has enabled the production of personalized prosthetics, orthotics, and surgical instruments, allowing for better patient care and rehabilitation. The medical industry continues to explore the potential of metal powder for 3D printing, paving the way for innovative solutions in healthcare.
Automotive industry
The automotive industry has been one of the key adopters of metal powder for 3D printing. With the ability to create complex and lightweight parts, 3D printing has revolutionized the way automotive components are manufactured. From engine parts to customized car accessories, metal powder-based 3D printing has allowed for greater design flexibility, reduced production time, and improved overall performance. As the automotive industry continues to embrace additive manufacturing technologies, the use of metal powder for 3D printing is expected to grow exponentially, driving innovation and pushing the boundaries of what is possible in the world of automotive engineering.