急速に進化するアディティブ・マニュファクチャリングの世界、 マルチマテリアル3Dプリンティング は革命的な技術として際立っています。もはや1つの素材でプリントするだけではなく、1つのプリントで複数の素材を組み合わせることで、比類ない機能性と美観を実現できるようになりました。このガイドでは、マルチマテリアル3Dプリントの用途、利点、詳細について深く掘り下げ、この最先端技術に関する詳細な洞察を提供します。
マルチマテリアル3Dプリンティングの概要
マルチマテリアル3Dプリンティングは、2つ以上の異なる材料を同時に使用して物体を製造することを可能にします。この機能により、より堅牢で機能的なプロトタイプの作成から、複雑な形状と複数の特性を持つ最終製品の製造まで、多くの可能性が広がります。硬質材料と軟質材料の組み合わせであれ、金属とポリマーの統合であれ、マルチマテリアル3Dプリンティングは、製造業の状況を一変させるものです。
主なメリット
- 素材の多様性による機能性の向上。
- 製品の耐久性と強度が向上。
- 複雑な部品をコスト効率よく生産。
- 設計の自由度と革新性の向上。
主な用途
- 航空宇宙部品。
- 医療機器と義肢装具
- 家電製品。
- 自動車部品。
- カスタマイズされた工具と治具。
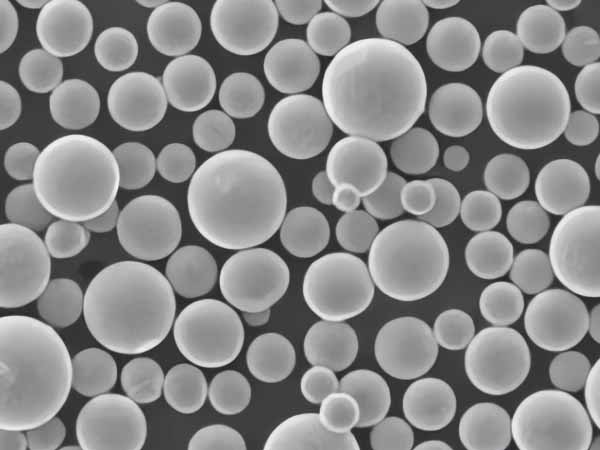
種類、組成、特性、特徴
の可能性を真に理解する。 マルチマテリアル3Dプリンティングそのためには、使用されるさまざまな種類の素材とその特性を調べることが重要である。
素材タイプ | 構成 | プロパティ | 特徴 |
---|---|---|---|
金属粉 | チタン、アルミニウム、スチールなどの合金。 | 高強度、耐久性、耐熱性 | 航空宇宙、自動車、工業用途に最適 |
ポリマー | ABS、PLA、PETG、ナイロン | 軽量、柔軟、耐食性 | 消費者向け製品や試作品に最適 |
セラミックス | ジルコニア、アルミナ、炭化ケイ素 | 高硬度、熱安定性、耐摩耗性 | 医療用インプラントや高熱環境で使用される |
複合材料 | ファイバーグラス, カーボンファイバー, ケブラー | 高い強度対重量比、剛性 | スポーツ用品や航空宇宙分野に最適 |
エラストマー | TPU、TPE | 弾性、耐衝撃性 | シール、ガスケット、フレキシブル部品に最適 |
マルチマテリアル3Dプリンティングのための特定金属粉末
- Ti-6Al-4V(チタン合金)
- 構成: チタン、アルミニウム、バナジウム
- プロパティ 高強度、軽量、耐食性
- アプリケーション 航空宇宙、生物医学インプラント
- 316Lステンレス鋼
- 構成: 鉄、クロム、ニッケル、モリブデン
- プロパティ 耐食性、高延性
- アプリケーション 化学処理、海洋用途
- インコネル718
- 構成: ニッケル、クロム、鉄
- プロパティ 高温耐性、優れた機械的特性
- アプリケーション ガスタービン、ジェットエンジン
- AlSi10Mg(アルミニウム合金)
- 構成: アルミニウム、シリコン、マグネシウム
- プロパティ 軽量、高熱伝導性
- アプリケーション 自動車、航空宇宙
- 銅
- 構成: 純銅
- プロパティ 高い電気伝導性と熱伝導性
- アプリケーション 電気部品、熱交換器
- マレージング鋼
- 構成: 鉄、ニッケル、モリブデン、コバルト
- プロパティ 高強度、機械加工が容易
- アプリケーション 工具、航空宇宙
- H13工具鋼
- 構成: クロム、モリブデン、バナジウム
- プロパティ 高靭性、耐熱性
- アプリケーション 射出成形金型、ダイカスト
- コバルト・クロム
- 構成: コバルト、クロム、モリブデン
- プロパティ 耐摩耗性、生体適合性
- アプリケーション 歯科インプラント、整形外科インプラント
- ニッケル625
- 構成: ニッケル、クロム、モリブデン、ニオブ
- プロパティ 耐食性と耐酸化性
- アプリケーション 海洋、化学処理
- 工具鋼
- 構成: 鉄、炭素、クロムの各種合金
- プロパティ 高硬度、耐摩耗性
- アプリケーション 切削工具、金型
マルチマテリアル3Dプリンティングの応用と用途
マルチマテリアル3Dプリンティングは、さまざまな産業で多様な用途を見いだし、製品の設計や製造方法を変革している。
産業 | アプリケーション | メリット |
---|---|---|
航空宇宙 | 軽量構造部品、エンジン部品 | 軽量化、燃費向上 |
メディカル | カスタム義肢、インプラント、手術器具 | オーダーメイドのフィット感で、患者の予後を向上 |
自動車 | 複雑なエンジン部品、内装部品 | 性能の向上、組み立て時間の短縮 |
消費財 | カスタム・シューズ、電子ケーシング | パーソナライズされた製品、人間工学の改善 |
インダストリアル | 工具、治具、製造補助器具 | コスト効率の高い生産、迅速なプロトタイピング |
エレクトロニクス | カスタムPCB、ハウジング、コネクタ | 小型化、多機能の統合 |
仕様、サイズ、等級、規格
で使用される各素材。 マルチマテリアル3Dプリンティング 品質と性能を保証するために、特定の仕様と基準が設けられている。
素材 | 仕様 | サイズ | グレード | 規格 |
---|---|---|---|---|
Ti-6Al-4V | ASM1472、AMS4911 | パウダーサイズ15-45ミクロン | グレード5 | ASTM、ISO |
316Lステンレス鋼 | アストレムA240、アストレムF138 | パウダーサイズ:20~53ミクロン | マリン, 外科 | ASTM、ISO |
インコネル718 | AMS5662、ASM B637 | パウダーサイズ15-53ミクロン | UNS N07718 | ASTM、AMS |
AlSi10Mg | DIN EN 1706、ASM B85 | パウダーサイズ:20~63ミクロン | – | ASTM、DIN |
銅 | アストレムB216、アストレムB42 | パウダーサイズ10-45ミクロン | – | ASTM、ISO |
マレージング鋼 | AMS6514、ASM538 | パウダーサイズ10-45ミクロン | グレード250、300 | ASTM、AMS |
H13工具鋼 | A681, T20813 | パウダーサイズ:20~63ミクロン | – | ASTM、UNS |
コバルト・クロム | ASTM F1537、ISO 5832-12 | パウダーサイズ15-45ミクロン | – | ASTM、ISO |
ニッケル625 | ASMB443、AMS5599 | パウダーサイズ15-53ミクロン | – | ASTM、AMS |
工具鋼 | AISI等級D2、O1、A2 | パウダーサイズ:20~63ミクロン | 各種AISIグレード | AISI、ASTM |
サプライヤーと価格詳細
マルチマテリアル3Dプリント材料の価格は、材料の種類、品質、購入数量によって異なります。
サプライヤー | 素材 | kgあたりの価格 | MOQ | 納期 |
---|---|---|---|---|
EOS GmbH | Ti-6Al-4V | $400 | 10キロ | 2週間 |
GEアディティブ | 316Lステンレス鋼 | $150 | 5 kg | 3週間 |
カーペンター・テクノロジー | インコネル718 | $500 | 10キロ | 4週間 |
ヘガネスAB | AlSi10Mg | $80 | 20キロ | 2週間 |
サンドビック | 銅 | $90 | 15キロ | 3週間 |
GKNアディティブ | マレージング鋼 | $250 | 10キロ | 2週間 |
レニショー | H13工具鋼 | $120 | 5 kg | 3週間 |
アルカムEBM | コバルト・クロム | $600 | 5 kg | 4週間 |
LPWテクノロジー | ニッケル625 | $550 | 10キロ | 3週間 |
金属分析 | 工具鋼 | $100 | 20キロ | 2週間 |
マルチマテリアル3Dプリンティングの長所と短所
マルチマテリアル3Dプリンティングには多くの利点がありますが、その利点と限界の両方を考慮することが重要です。
アスペクト | メリット | デメリット |
---|---|---|
機能性 | 複数の材料特性を組み合わせる | 複数の材料特性を管理する複雑さ |
デザインの柔軟性 | 革新的なデザインと複雑な形状が可能 | 高度なデザイン・スキルが必要 |
コスト効率 | 材料の無駄を省き、部品を統合 | 高額な設備投資 |
生産スピード | より迅速なプロトタイピングと生産 | 複雑なマルチマテリアル部品の印刷時間を短縮 |
素材の選択 | 幅広い素材に対応 | プリンターの性能と材料の互換性による制限 |
カスタマイズ | 特定のニーズに合わせた製品の提供 | 少量生産では製造コストが高くなる |
マルチマテリアル3Dプリンティング・アプリケーションの構成
素材を組み合わせる際、その組成と相性を理解することは非常に重要です。異なる素材の相互作用は、最終製品の性能に大きな影響を与えます。
よくある組み合わせ:
- メタル+ポリマー: 電子回路を組み込んだ構造部品に最適。
- 硬質ポリマーと軟質ポリマー: ヒンジ、シール、ガスケットの作成に便利。
- メタル+セラミック: 熱安定性と強度を必要とする高温用途に使用される。
検討する:
- 熱適合性: 融点が異なると印刷工程が複雑になる。
- 接着特性: 材料同士がうまく接着するようにすることは、構造的に完全であるために重要である。
- 素材の挙動: 材料が応力下でどのように膨張、収縮、相互作用するかを理解することは不可欠である。
マルチマテリアル3Dプリンティング・アプリケーションの特徴
マルチマテリアル3Dプリンティング・アプリケーションの特徴は、機能性が向上し、複数の材料特性を1つの部品に組み込むことができることである。
主な特徴
- 汎用性がある: 機械的、熱的、電気的特性の異なる部品を製造する能力。
- 精度が高い: 材料配置の精度が高く、複雑な形状や機能的な統合を確実にします。
- カスタマイズ: 医療用インプラントから航空宇宙部品まで、特定の用途ニーズに対応。
- 効率が良い: 組み立てや後処理の必要性を減らし、時間とコストを節約。
例を挙げよう:
- 医療補綴: 生体適合性材料と構造部品を組み合わせたカスタムインプラント。
- 航空宇宙部品: 複数の機能を統合し、部品点数を削減する軽量で強固なコンポーネント。
- コンシューマー・エレクトロニクス フレキシブル・コネクタまたは回路を内蔵した、なめらかで耐久性のあるケーシング。
マルチマテリアル3Dプリンティング・アプリケーションの利点
マルチマテリアル3Dプリンティングの利点は多岐にわたり、多くの産業で好まれている。
デザインの革新
マルチマテリアル3Dプリンティングは、従来の製造方法では不可能だった複雑な形状や統合された機能性の創出を可能にする。この技術革新は、新しい製品設計とエンジニアリング・ソリューションを育みます。
費用対効果の高い生産
複数の材料を1枚の印刷物に組み合わせることで、メーカーは組み立ての必要性を減らし、材料の無駄を減らし、生産時間を短縮することができる。このコスト効率は、少量生産でカスタマイズの多い製品に特に有益です。
製品性能の向上
マルチマテリアル3Dプリンティングで作られた製品は、優れた性能特性を示すことができる。例えば、外側は硬く、内側は柔軟な部品を設計したり、導電性材料と絶縁性材料を組み合わせたりすることができます。
ラピッドプロトタイピングとイテレーション
マルチマテリアル3Dプリントは、プロトタイピングプロセスを加速し、迅速な反復と改良を可能にします。このラピッドプロトタイピング機能は、製品をより早く市場に投入し、開発コストを削減するのに役立ちます。
持続可能性
マルチマテリアル3Dプリンティングの精度と効率は、材料の廃棄とエネルギー消費を最小限に抑えることで、より持続可能な製造方法に貢献します。
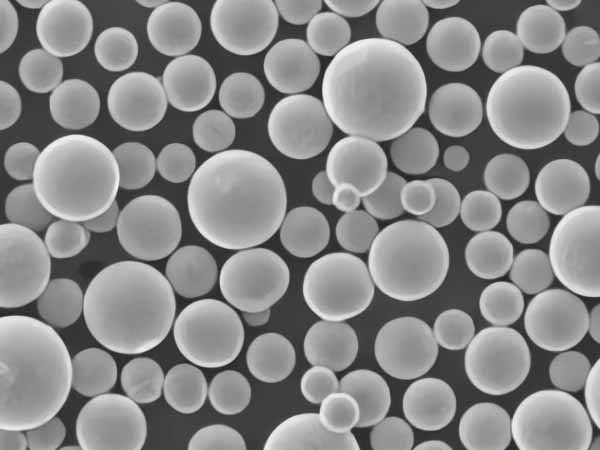
よくあるご質問
質問 | 回答 |
---|---|
マルチマテリアル3Dプリンティングとは? | これは、1つのプリントで2つ以上の素材を同時に使用できるプロセスである。 |
マルチマテリアル3Dプリンティングの利点は何ですか? | 機能強化、コスト削減、設計革新、性能向上などのメリットがある。 |
マルチマテリアル3Dプリンティングを使用する業界は? | 航空宇宙、医療、自動車、消費財、工業部門が著名なユーザーである。 |
マルチマテリアル3Dプリンティングで使用できる材料は何ですか? | 金属、ポリマー、セラミック、複合材料、エラストマーなどがよく使われる。 |
マルチマテリアル3Dプリンティングは製品設計をどのように改善するのか? | 従来の方法では実現できなかった複雑な形状や統合された機能性の創造を可能にする。 |
マルチマテリアル3Dプリンティングの課題は何ですか? | 課題には、材料の適合性、接着特性、複数の材料の挙動管理などがある。 |
マルチマテリアル3Dプリンティングは従来の製造と比べてどうですか? | 設計の柔軟性が高く、プロトタイピングのスピードが速く、組み立ての手間が省けるが、少量生産では割高になる可能性がある。 |
マルチマテリアル3Dプリンティングは大規模生産に使えるか? | 主にプロトタイピングや少量生産に使用されているが、進歩により、より大規模な用途にも使用できるようになってきている。 |
マルチマテリアル3Dプリンティングのコストへの影響は? | 初期の設備コストは高いが、時間の経過とともに材料の使用量や生産効率のコスト削減につながる。 |
マルチマテリアル3Dプリンティングの未来は? | 素材、技術、アプリケーションの継続的な進歩がその可能性を広げており、将来は有望である。 |
マルチマテリアル3Dプリンティング は、製造業で可能なことの限界を押し広げ、これまでにない設計の自由度と機能性を提供しています。テクノロジーが進化を続けるにつれて、革新的なアプリケーションがさらに増え、さまざまな業界で広く採用されることが予想されます。今日、このテクノロジーを取り入れることで、競争力を高め、製品開発と生産効率に新たな道を開くことができる。