概要 真空誘導溶解 (ヴィム)
真空誘導溶解(VIM)は、高品質の金属合金の精密な製造を可能にする高度な冶金プロセスです。電磁誘導を使用して制御された真空雰囲気下で金属を溶解するこの技術は、高純度と特定の化学組成を必要とする材料の製造に不可欠です。チタン合金、超合金、または特殊鋼のいずれを扱う場合でも、VIMは溶解および精錬プロセスにおいて比類のない制御を提供し、高性能用途に合わせた優れた特性を持つ材料を生み出します。
では、なぜVIMが今日の産業界に不可欠なのだろうか?その答えは、厳格な仕様を満たし、汚染のない、構造と組成が均一な材料を製造する能力にある。これは、航空宇宙、医療用インプラント、高性能自動車など、材料性能が文字通り成功と失敗の分かれ目となる産業において特に重要である。
真空誘導溶解の仕組み
VIMの核心は、コイルに電流を流して磁場を発生させ、その磁場がるつぼ内に置かれた金属チャージに電流を誘導することである。この電流が金属を加熱し、溶融させる。この真空環境は、酸化を防ぎ、汚染を減らし、水素、窒素、炭素などの不要なガスの除去を可能にする。
要するに、VIMはクリーンで効率的、かつ高度に制御可能な溶解プロセスであり、品質に妥協できない場合に選択すべき方法なのである。
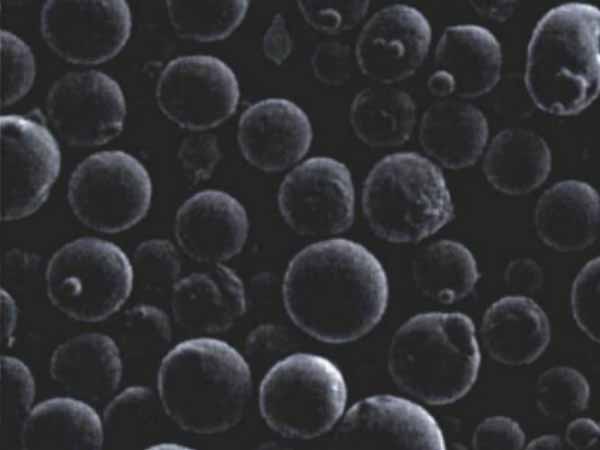
主な構成要素 真空誘導溶解
VIMで使用される機械と材料を理解することは、金属製造に携わる者にとって極めて重要である。以下は、主要部品の内訳である:
1.炉
VIM炉は、耐火物で内張りされたるつぼを取り囲む水冷式銅コイルで構成された操業の心臓部である。この炉は極端な温度にも耐えられるように設計されており、誘導溶解に必要な高強度の磁場を発生させることができる。
2.真空チャンバー
真空チャンバーは、汚染のない環境を維持するために不可欠である。必要な低圧状態を作り出す真空ポンプに接続され、溶融金属と反応する可能性のある空気やその他のガスを除去する。
3.るつぼ
るつぼは、溶解中の金属チャージを保持する。アルミナやジルコニアなどの耐火性材料で作られ、炉内で発生する高温や化学反応に耐性を持つ。
4.電源
電源は、誘導プロセスを駆動する電気エネルギーを供給する。最新のVIMシステムには高周波電源が装備されており、溶解プロセスを正確に制御することで、最終製品の均一性を確保することができます。
真空誘導溶解で製造される金属粉末の種類
VIMは幅広い金属粉末の製造に使用される汎用性の高いプロセスであり、それぞれが特定の用途に合わせたユニークな特性を有しています。以下では、VIMを使用して最も一般的に製造される金属粉末のいくつかを調査し、その主な特性と用途に焦点を当てます。
金属粉 | 説明 |
---|---|
チタン合金 (Ti-6Al-4V) | この合金は、その優れた強度対重量比と耐食性により、航空宇宙および生物医学用途に広く使用されています。VIMは医療用インプラントに必要な純度を保証します。 |
インコネル718 | 高い強度と高温下での耐食性で知られるニッケル・クロム合金で、ガスタービン部品や航空宇宙用途に最適。 |
コバルト・クロム合金 | 医療用インプラントに使用されるこの合金は、優れた生体適合性と耐摩耗性を提供します。VIMは、化学組成と微細構造の精密な制御を可能にします。 |
ニッケル基超合金 | ハステロイやワスパロイを含むこれらの合金は、強度と耐酸化性の両方が重要な、ジェットエンジンやガスタービンのような高温用途に不可欠である。 |
ステンレススチール(316L) | 316ステンレス鋼の低炭素鋼種である316Lは、化学処理や海洋用途など、耐食性が最も重要な環境で使用されます。 |
工具鋼(H13) | 硬度と耐熱疲労性で知られるH13は、ダイカストや押出用途によく使用される。VIMはその微細構造の均一性を保証します。 |
マルエージング鋼 (18Ni300) | 靭性と時効硬化能力で知られる高強度鋼で、航空宇宙、工具、構造用途によく使用される。 |
炭化タングステン | 切削工具や耐摩耗部品によく使用されるVIMで製造されたタングステンカーバイドは、優れた硬度と耐摩耗性を示します。 |
アルミニウム合金 (Al-Si10Mg) | この合金は軽量構造部品、特に軽量化が重要な自動車産業や航空宇宙産業で使用されている。 |
銅合金 (CuCr1Zr) | これらの合金は、電気接点や抵抗溶接電極など、高い導電性と強度を必要とする用途に使用される。 |
真空誘導溶解合金の組成
VIMが製造する合金の化学組成は、その特性と様々な用途への適合性を決定する上で非常に重要です。ここでは、VIMが生産するいくつかの主要合金の組成を詳しく見てみましょう。
合金 | 主要な要素 | アプリケーション |
---|---|---|
チタン合金 (Ti-6Al-4V) | 6%アルミニウム、4%バナジウム、バランスチタン | 航空宇宙、生物医学インプラント、高性能自動車部品 |
インコネル718 | 50-55% ニッケル、17-21% クロム、4.75-5.5% ニオブ、2.8-3.3% モリブデン、0.65-1.15% チタン | ガスタービン部品、航空宇宙エンジン、原子炉 |
コバルト・クロム合金 | 27-30% クロム、バランスコバルト、5-7% モリブデン | 医療用インプラント、歯科補綴物、耐摩耗部品 |
ニッケル基超合金 | ニッケル、クロム、コバルト、モリブデン、アルミニウムを含む。 | 高温タービンブレード、排気システム、燃焼室 |
ステンレススチール(316L) | 16-18% クロム、10-14% ニッケル、2-3% モリブデン、低炭素 | 化学処理装置、船舶用金具、手術器具 |
工具鋼(H13) | 5%クロム、1.5%モリブデン、1%バナジウム、バランス鉄 | ダイカスト金型、押出金型、熱間鍛造金型 |
マルエージング鋼 (18Ni300) | 18% ニッケル、7% コバルト、5% モリブデン、0.3% チタン | 高強度構造部品、工具、航空宇宙用ファスナー |
炭化タングステン | 主にタングステンとカーボン | 切削工具、鉱山機械、摩耗部品 |
アルミニウム合金 (Al-Si10Mg) | 10%シリコン、0.45%マグネシウム、バランスアルミニウム | 軽量構造部品、自動車部品、航空宇宙用ブラケット |
銅合金 (CuCr1Zr) | 0.7-1.2% クロム、0.06-0.15% ジルコニウム、バランス 銅 | 電気接点、抵抗溶接電極、熱交換器 |
の特徴 真空誘導溶解 合金
VIMは、高性能用途に適した様々な特性を持つ合金を製造しています。以下はVIM合金の主な特性です:
特徴 | 説明 |
---|---|
高純度 | 真空環境はコンタミネーションを最小限に抑え、介在物や不純物を最小限に抑えた超高純度合金を生み出す。 |
ユニフォームの構成 | 制御された溶融環境は、合金元素の均一な分布を保証し、合金全体に一貫した材料特性をもたらす。 |
優れた機械的特性 | VIMによって製造された合金は、多くの場合、引張強さ、硬度、耐疲労性などの機械的特性が向上し、要求の厳しい用途に適している。 |
制御された微細構造 | 冷却速度と凝固パターンを制御する能力により、オーダーメイドの微細構造が可能になり、靭性や耐クリープ性などの特性が最適化される。 |
低ガス含有 | VIMは、酸素、窒素、水素のような気体の含有量を著しく減少させるが、これらは気孔の原因となり、合金を弱める。 |
汎用性 | VIMは、鉄および非鉄金属から超合金まで、幅広い合金の製造が可能であり、それぞれが用途に合わせた特殊な特性を有している。 |
真空誘導溶解合金の用途
VIM合金は、材料性能が重要となる様々なハイテク用途で使用されています。ここでは、これらの材料がどのような分野で活躍しているかを紹介する:
産業 | 申し込み | 一般的に使用される合金 |
---|---|---|
航空宇宙 | タービンブレード、エンジン部品、構造部品 | インコネル718, ニッケル基超合金, チタン合金 (Ti-6Al-4V) |
メディカル | インプラント、補綴物、手術器具 | コバルトクロム合金、チタン合金(Ti-6Al-4V)、ステンレス鋼(316L) |
自動車 | 高性能エンジン部品、軽量構造部品 | アルミニウム合金(Al-Si10Mg)、チタン合金(Ti-6Al-4V)、マルエージング鋼(18Ni300) |
エネルギー | 原子炉、ガスタービン、発電設備 | インコネル718、ニッケル基超合金、ステンレス鋼(316L) |
工具 | ダイカスト金型、押出金型、切削工具 | 工具鋼(H13)、超硬合金、マルエージング鋼(18Ni300) |
マリン | 耐食性ハードウェア、構造部品 | ステンレス鋼(316L)、アルミニウム合金(Al-Si10Mg) |
エレクトロニクス | 電気接点、抵抗溶接電極 | 銅合金(CuCr1Zr)、ニッケル基超合金 |
ディフェンス | 装甲、ミサイル部品、構造部品 | チタン合金(Ti-6Al-4V)、マルエージング鋼(18Ni300)、ニッケル基超合金 |
真空誘導溶解合金の仕様、サイズ、等級および規格
VIM合金に関しては、材料の性能と信頼性を確保するために、特定の規格とグレードを遵守することが極めて重要です。以下はその詳細な概要である:
合金 | 仕様 | 一般的なサイズ | 業界標準 |
---|---|---|---|
チタン合金 (Ti-6Al-4V) | AMS4911、ASM B265、MIL-T-9046 | 0.5~4.0mm厚板、直径10~100mmの棒材 | ASM1472、AMS4928 |
インコネル718 | AMS5662、ASM B637、UNS N07718 | 0.5~6.0mm厚板、12~150mm径棒材 | AMS5663、ASM B670 |
コバルト・クロム合金 | アストムF75、ISO 5832-4、アストムF1537 | 0.5~3.0mm厚板、8~100mm径棒材 | ISO 5832-4、ASM F799 |
ニッケル基超合金 | AMS5666、ASM B435、UNS N06625 | 0.3~5.0mm厚板、直径10~200mmの棒材 | ASMB443、AMS5599 |
ステンレススチール(316L) | astmA240、ams 5501、uns s31603 | 0.4~6.0mm厚板、直径10~200mmの棒材 | アストレムA276、アストレムF138 |
工具鋼(H13) | A681, T20813、AMS 6430 | 直径20~200mmの棒材、金型用特注サイズ | A681, AISI H13 |
マルエージング鋼 (18Ni300) | ASM538、AMS6512、UNS K93120 | 直径12~200mmの棒鋼、航空宇宙用途の特注サイズ | AMS 6520、ASM A579 |
炭化タングステン | ISO 513、ASM B777 | 切削工具用の特注形状とサイズ、通常は直径10~50mmの棒材 | ISO 388-2、ASM B777 |
アルミニウム合金 (Al-Si10Mg) | ASMB209、AMS4037、UNS A96061 | 0.3~5.0mm厚板、直径10~150mmの棒材 | ASMB211、AMS4027 |
銅合金 (CuCr1Zr) | アストムB552、UNS C18150 | 直径5~100mmの棒材、電気接点用カスタムサイズ | ASTM B577、EN 12420 |
真空誘導溶解合金の長所と短所
どんな製造工程にも長所と短所があり、VIMも例外ではありません。ここでは、VIM合金の利点と限界についてバランスよく見てみよう:
メリット | 制限事項 |
---|---|
高純度・高品質 | 高コスト |
VIM合金は、コンタミネーションを最小限に抑え、均一な組成を持つ、非常に優れた純度で知られています。これは、材料の一貫性が鍵となる高性能用途にとって極めて重要です。 | VIMには複雑さと精度が要求されるため、高価なプロセスとなり、最終製品のコストアップにつながる。 |
機械的特性の向上 | 限定生産 |
VIMの制御された環境は、強度、靭性、耐疲労性などの優れた機械的特性を持つ合金の製造を可能にする。 | VIMは通常、コストと複雑さのために小ロットに使用され、大量生産には適していない。 |
幅広い合金 | 専用機材が必要 |
VIMは、超合金から特殊鋼まで、特定の用途に合わせて特性を調整した多様な合金を製造することができる。 | 特殊な炉、真空システム、誘導装置が必要なため、中小メーカーにとっては参入障壁となりうる。 |
コンポジションの正確なコントロール | 熟練した操作が必要 |
合金元素と溶解プロセスを正確に制御する能力により、正確な仕様を満たす材料が得られる。 | VIMプロセスの複雑さは、高度に熟練したオペレーターを必要とするため、運用コストとトレーニング要件に拍車をかけることになる。 |
ガス含有量の低減 | 長い生産時間 |
VIMは、最終製品の欠陥の原因となる酸素、窒素、水素などのガスの含有量を大幅に削減する。 | VIMの綿密な性質は、他の溶解方法と比較して、材料のバッチ生産にしばしば時間がかかることを意味する。 |
真空誘導溶解プロセスステップ
VIMプロセスは、慎重に管理された一連の工程であり、それぞれが合金の最終的な品質に貢献しています。その工程を詳しく見てみよう:
1.充電
VIMプロセスの最初の工程は、原料(チャージ)をるつぼに投入することである。このチャージは通常、金属スクラップ、合金元素、および所望の組成を達成するために必要なその他の材料で構成される。
2.溶融
チャージが装填されると、るつぼが炉内に置かれ、真空が適用される。その後、炉の電源を入れ、電磁場を発生させて金属チャージに電流を誘導し、溶融させる。
3.精製
精錬段階では、溶融金属から不要な不純物が除去される。真空環境はガスの除去に役立つ一方、不純物と結合して表面に浮上させるためにスラグ剤が添加されることもある。
4.合金化
この段階で、特定の合金元素が溶融金属に添加され、所望の組成になる。VIMでは、温度と雰囲気を正確に制御することで、これらの元素を正確に組み込むことができる。
5.鋳造
所望の組成と純度が達成されると、溶融金属は鋳型に鋳込まれ、インゴット、ビレット、その他の形状が形成される。鋳造工程は、欠陥を避け、最終製品の均一性を確保するために注意深く制御される。
6.冷却
鋳造後、金属は制御された条件下で冷却・凝固させられる。この冷却プロセスは、合金の機械的特性に影響を与える特定の微細構造を達成するために調整することができます。
7.後処理
最後に、鋳造された金属は、合金の最終的な用途に応じて、熱処理、機械加工、表面仕上げなどの後処理を受ける。
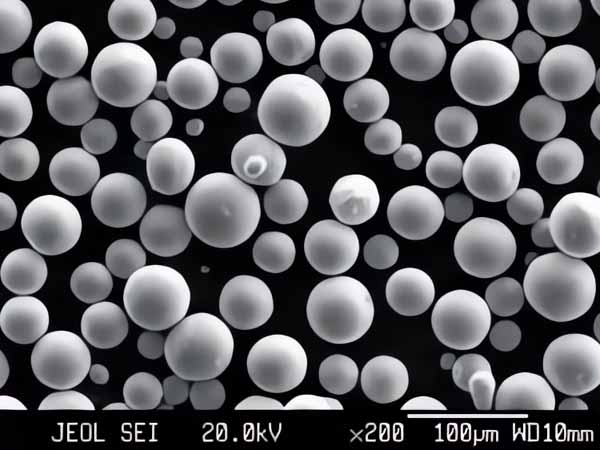
真空誘導溶解合金のサプライヤーと価格
VIM合金を調達する際には、サプライヤーと価格の両方を考慮することが重要です。以下は、いくつかの主要な供給業者とその提供品の比較です:
サプライヤー | 提供合金 | 価格 | 著名なクライアント |
---|---|---|---|
ATIメタルズ | ニッケル基超合金、チタン合金、特殊鋼 | プレミアム - カスタム仕様のため高コスト | ボーイング、GEアビエーション、ロッキード・マーティン |
カーペンター・テクノロジー | ステンレス鋼、工具鋼、コバルト基合金 | ミッドレンジ - 標準グレードの競争力のある価格 | エアバス, ロールス・ロイス, NASA |
PCCメタルズ | ニッケル基超合金、チタン合金 | プレミアム - 航空宇宙グレードの素材は高コスト | プラット&ホイットニー、サフラン、ハネウェル |
VSMPO-AVISMA | チタン合金 | ミッドレンジ~プレミアム - 合金と形状による | エアバス、ボーイング、ユナイテッド・テクノロジーズ |
日立金属 | 工具鋼、マルエージング鋼、特殊合金 | ミッドレンジ - コストと品質のバランスが良い | トヨタ、ホンダ、ゼネラルモーターズ |
サンドビック・マテリアル・テクノロジー | ステンレス鋼、ニッケル基合金 | ミッドレンジ~プレミアム - 幅広い品揃えと競争力のある価格 | シーメンス、ABB、アルストム |
よくあるご質問
質問 | 回答 |
---|---|
真空誘導溶解(VIM)とは? | VIMは、電磁誘導を利用して真空下で金属を溶解・精製するプロセスである。この方法は高純度合金の製造に不可欠である。 |
VIMの主な利点は何ですか? | VIMは、組成と微細構造を精密に制御した超高純度合金の製造を可能にし、高性能用途に理想的である。 |
VIM合金を使用する産業は? | VIM合金は、航空宇宙、医療、自動車、エネルギー、工具、海洋、エレクトロニクス、防衛産業で使用されている。 |
なぜVIMでは真空環境が重要なのか? | 真空環境は汚染を防ぎ、不要なガスを除去し、重要な用途に必要な高純度と品質を達成するのに役立つ。 |
VIMを使ってどのような材料を加工できますか? | VIMは、チタン合金、ニッケル基超合金、コバルトクロム合金、特殊鋼など、さまざまな材料を加工できる。 |
VIMは他の溶解プロセスと比較してどうですか? | VIMは、より高価で時間がかかるが、従来の溶融プロセスに比べ、最終製品の組成と品質に対する優れた制御を提供する。 |
VIM合金の典型的な用途は? | 代表的な用途としては、タービンブレード、医療用インプラント、高性能エンジン部品、航空宇宙・防衛産業の構造部品などがある。 |
VIMは大量生産に使えるか? | VIMはコストと精度が高く、大量生産には向かないため、一般的に少量生産に使われる。 |
VIMの限界とは? | 主な制限としては、他の溶融プロセスと比べてコストが高いこと、複雑であること、生産時間が長いことなどが挙げられる。 |
VIM合金のサプライヤーはどのように選べばよいですか? | サプライヤーを選択する際には、提供される合金の種類、価格、評判、アプリケーションの特定の要件などの要因を考慮してください。 |
結論
真空誘導溶解 は現代冶金学の礎石であり、高純度、高性能の金属合金の生産に比類のない制御を提供します。航空宇宙、医療、ハイテク産業など、どのような用途であっても、VIMが提供する精度と品質により、重要な材料に最適なプロセスとなっています。
この記事では、VIMの技術プロセスや主要コンポーネントから、VIMが製造する特定の合金やその用途に至るまで、VIMの複雑さを探ってきた。これらの詳細を理解することで、今日の世界を形成する材料の製造におけるVIMの役割をより理解することができる。