概要
高真球度パウダー は、ほぼ完全な球形を持つように設計された特殊な粉末材料である。この特性は、様々な産業用途、特に積層造形(3Dプリンティング)、航空宇宙、自動車、電子機器、医療機器において非常に重要である。これらの粉末における真球度の重要性は、流動性、充填密度、さらには溶融特性にあり、これらは一貫した高品質の生産量を達成する上で極めて重要である。
この広範なガイドでは、高真球度粉末について知る必要があるすべてのことを探ります。高真球度粉末の組成や特性の理解から、様々な金属粉末モデルの比較まで、充実した詳細情報を提供することを目的としています。材料エンジニアの方、購買マネージャーの方、あるいは単に高真球度粉末の世界に興味がある方、この記事は教育と情報提供を目的としています。
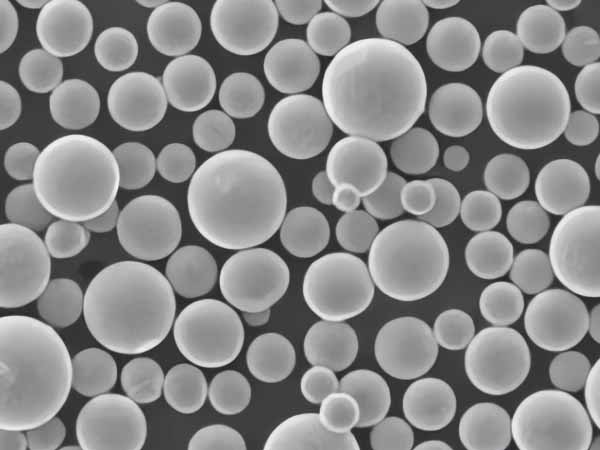
高真球度粉末を理解する
高真球度パウダーとは?
高真球度粉末とは、個々の粒子がほぼ完全な球体である粉末材料を指す。この形状は、ガスアトマイズ、プラズマアトマイズ、遠心アトマイズなどのさまざまな製造プロセスによって実現される。これらの粒子の球状性は、高い流動性と充填密度に寄与し、特定の高精度用途に理想的です。
球形度はなぜ重要なのか?
不規則な形の石を積み上げようとするのと、完全に丸いビー玉を積み上げようとするのを想像してみてほしい。ビー玉は隙間なくきれいに積み重ねられるでしょう?真球度の高いパウダーは、ミクロのレベルではそのような働きをするのです。球状にすることで、充填性が向上し、密度が高くなり、流動性が改善され、溶融や焼結の過程でより安定した挙動を示すようになるのです。
高真球度パウダーの主な利点
- 流動性の向上: 球状の粒子は、不規則な形状の粒子よりも流れやすく、3Dプリンティングのように粉体の安定供給が重要な用途に理想的である。
- より高い梱包密度: 均一な形状は、粒子をより密に充填することを可能にし、より高い密度をもたらし、ひいては最終製品の強度を高める。
- より優れた溶融特性: 球状パウダーは均一に溶融するため、最終製品に欠陥が生じるリスクを低減します。
種類と構成 高真球度パウダー
高真球度粉末は様々な金属や合金から作られ、それぞれが異なる用途に適しています。以下は、一般的な高真球度粉末の種類とその組成、特性、用途の詳細です。
パウダータイプ | 構成 | プロパティ | アプリケーション |
---|---|---|---|
316Lステンレス鋼 | Fe、Cr、Ni、Mo | 高耐食性、優れた機械的特性 | 医療機器、航空宇宙部品 |
AlSi10Mg | Al、Si、Mg | 軽量、高強度、優れた熱特性 | 自動車部品、航空宇宙 |
インコネル718 | Ni、Cr、Fe、Nb、Mo、Ti、Al | 高温強度、耐食性 | ガスタービン、航空宇宙、原子炉 |
Ti-6Al-4V | Ti、Al、V | 高い強度対重量比、耐食性 | 航空宇宙、生物医学インプラント |
CoCrMo | Co、Cr、Mo | 生体適合性、耐摩耗性、耐食性 | 医療用インプラント、歯科用途 |
銅(Cu) | 純銅 | 優れた電気伝導性、熱伝導性 | 電気部品、熱交換器 |
ハステロイX | Ni、Cr、Fe、Mo、Co | 耐酸化性、高温での強度 | ガスタービン、石油化学用途 |
マルエージング鋼 (18Ni300) | Fe、Ni、Co、Mo | 超高強度、優れた靭性 | 工具、航空宇宙、原子力用途 |
ニッケル625 | Ni、Cr、Mo、Nb | 優れた耐食性、高強度 | 海洋、化学処理、航空宇宙 |
アルミニウム6061 | Al、Mg、Si | 優れた機械的特性、軽量 | 航空宇宙、自動車、エレクトロニクス |
高真球度粉末の特徴
高真球度粉体特有の特性を理解することは、用途に適した材料を選択する上で非常に重要です。ここでは、高真球度粉末を定義する核となる特性について掘り下げます。
1.粒度分布
粒度分布とは、粉末のバッチに含まれる粒子径の範囲を指す。添加剤製造のような均一性が要求される用途では、一般的に粒度分布が狭い方が好ましい。
- 微粉末(1~10 µm): 滑らかな仕上げと高い精度が要求される用途に最適。
- ミディアムパウダー(10-50 µm): 一般的な3Dプリンティング用途に使用され、流動性と精度のバランスを提供する。
- 粗粉(50~150μm): 高い造膜速度を必要とするが、表面仕上げの品質が劣る用途に適している。
2.流動性
流動性とは、パウダーがスムーズかつ一貫して流れる能力のことである。この特性は、3Dプリンティングのように、均一な層を形成するために粉体を均一に分散させる必要があるプロセスでは非常に重要です。
- 高い流動性: アディティブ・マニュファクチャリングにおける一貫したレイヤリングを保証し、欠陥のリスクを低減する。
- 流動性が低い: 層が不均一になり、最終製品に欠陥が生じる可能性が高くなる。
3.純度
純度とは、粉末中に汚染物質が含まれていないことを指します。高い純度レベルは、特に医療用インプラントや航空宇宙部品のような重要な用途において、最終製品の完全性を維持するために不可欠です。
- 高純度(>99%): 最終製品が厳しい品質基準を満たしていることを保証し、故障のリスクを低減する。
- 低純度(<99%): コンタミネーションの問題を引き起こし、最終製品の性能と信頼性に影響を与える可能性がある。
4.密度
密度は最終製品の性能に重要な役割を果たします。高密度の粉末は、より強く耐久性のある部品になるため、一般的に好まれます。
- 高密度: より強く、より耐久性のある製品につながる。
- 密度が低い: その結果、製品が弱くなり、構造上の問題が生じる可能性がある。
高真球度粉末の用途
高真球度粉体は様々な産業で使用されており、それぞれが高真球度粉体のユニークな特性から恩恵を受けています。以下では、高真球度粉体の主な用途をご紹介します。
産業 | アプリケーション | 主なメリット |
---|---|---|
アディティブ・マニュファクチャリング(3Dプリンティング) | プロトタイピング、複雑形状の製造 | 高精度、安定した品質、機械的特性の向上 |
航空宇宙 | タービンブレード、構造部品 | 高強度、耐熱性、軽量素材 |
医療機器 | インプラント、手術器具 | 生体適合性、耐食性、機械的特性の調整 |
自動車 | 軽量部品、エンジン部品 | 燃費向上、排出ガス低減、高強度 |
エレクトロニクス | 導電性部品、ヒートシンク | 優れた電気伝導性と熱伝導性 |
ディフェンス | 高性能部品、装甲 | 高い強度対重量比、耐久性 |
エネルギー | タービン、原子炉、燃料電池 | 耐食性、高温安定性 |
仕様、サイズ、等級、規格
用途によって、高真球度粉末の仕様、サイズ、グレード、規格は異なります。以下は、これらの側面を概説した詳細な表です。
素材 | 粒子径(µm) | グレード | スタンダード | 代表的な用途 |
---|---|---|---|---|
316Lステンレス鋼 | 15-45 | A, B | ASTM F3184 | 医療機器、航空宇宙部品 |
AlSi10Mg | 20-63 | A | ISO 23510 | 自動車部品、航空宇宙 |
インコネル718 | 15-53 | B、C | AMS 5662 | ガスタービン、航空宇宙、原子炉 |
Ti-6Al-4V | 15-45 | A | ASTM F1472 | 航空宇宙、生物医学インプラント |
CoCrMo | 10-45 | B | ISO 5832-12 | 医療用インプラント、歯科用途 |
銅(Cu) | 20-60 | A | ASTM B212 | 電気部品、熱交換器 |
ハステロイX | 15-53 | C | AMS 5536 | ガスタービン、石油化学用途 |
マルエージング鋼 (18Ni300) | 20-63 | B | AMS 6514 | 工具、航空宇宙、原子力用途 |
ニッケル625 | 15-45 | B、C | ASTM B443 | 海洋、化学処理、航空宇宙 |
アルミニウム6061 | 20-70 | A | ASTM B221 | 航空宇宙、自動車、エレクトロニクス |
サプライヤーと価格詳細
高真球度粉末の市場は多様であり、サプライヤーは様々な価格帯で様々な材料を提供している。以下は、サプライヤー、提供材料、価格設定の詳細の比較である。
サプライヤー | 素材 | 価格(kgあたり) | MOQ(最小注文数量) | リードタイム |
EOS GmbH | 316Lステンレス鋼 | $250 | 10キロ | 4~6週間 |
AP&C(GEアディティブ) | Ti-6Al-4V | $400 | 5 kg | 3~4週間 |
カーペンター・テクノロジー | インコネル718 | $300 | 15キロ | 6~8週間 |
サンドビック | AlSi10Mg | $200 | 20キロ | 5~7週間 |
LPWテクノロジー | CoCrMo | $350 | 10キロ | 4~5週間 |
GKNホエガネス | アルミニウム 606 | $150 | 25キロ | 3~4週間 |
ヘガネス | マルエージング鋼 (18Ni300) | $450 | 10キロ | 6~8週間 |
プラクセア・サーフェス・テクノロジー | ニッケル625 | $320 | 20キロ | 5~6週間 |
テクナ | 銅(Cu) | $180 | 30キロ | 3~5週間 |
エリコンAM | ハステロイX | $400 | 10キロ | 4~6週間 |
のメリットとデメリット 高真球度パウダー
高真球度粉末を選ぶ際には、長所と短所を比較検討することが不可欠です。以下は、これらの材料の長所と短所を強調した比較表です。
メリット | デメリット |
---|---|
高い流動性: 扱いやすく、加工しやすい。 | コストだ: 一般的に、不規則なパウダーよりも高価である。 |
一貫したメルティング: 最終製品の欠陥を減らす。 | 空室状況 一部の特殊合金については、入手可能性が限られている。 |
高い梱包密度: より強く、より耐久性のある製品につながる。 | 処理の難しさ: 工程によっては特殊な設備が必要。 |
幅広い用途: 業種を問わず多目的に使用できる。 | 限定的なカスタマイズ: 標準的な等級とサイズは、すべてのニーズに適合するとは限りません。 |
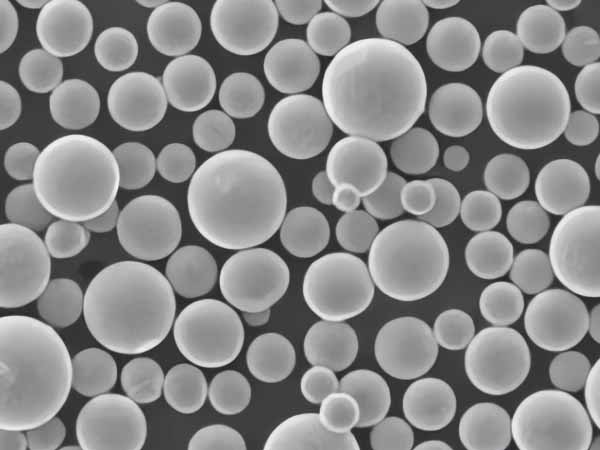
よくあるご質問
高真球度パウダーは何に使われるのですか?
高真球度粉末は、主に積層造形、航空宇宙、医療機器、および高精度と一貫性を必要とするその他の産業で使用されます。球状であるため、流動性、充填密度、溶融特性が向上し、高品質で欠陥のない製品の製造に最適です。
なぜ粉の真球度が重要なのですか?
真球度は、粉末の流動性、充填密度、溶融特性に影響する。真球度が高いほど、加工時の流動性が向上し、充填密度が高くなるため最終製品の強度が向上し、溶融が安定するため欠陥が減少する。
高真球度パウダーはどのようにして作られるのか?
高真球度パウダーは通常、ガスアトマイズ、プラズマアトマイズ、遠心アトマイズなどのプロセスによって製造されます。これらの方法は、粒子がほぼ完全な球体であることを保証し、これは様々な用途における粉末の性能にとって極めて重要である。
高真球度粉末に使用される一般的な材料は何ですか?
一般的な材料には、316Lステンレス鋼、Ti-6Al-4V、インコネル718、AlSi10Mg、CoCrMoなどがあります。各材料には固有の特性があり、用途の特定の要件に基づいて選択されます。
真球度の高いパウダーは高価ですか?
高真球度パウダーは、一般的に不規則なパウダーよりも高価ですが、その理由は、パウダーを製造するために使用される特殊なプロセスと、パウダーが提供する優れた特性のためです。コストは、材料、粒度、供給業者によって異なります。
高真球度パウダーはカスタマイズできますか?
ほとんどのサプライヤーが標準的なグレードとサイズを提供しているが、カスタマイズは可能である。カスタマイズのオプションは、サプライヤーと特定の材料によって異なります。
高真球度パウダーが最も恩恵を受ける産業は?
最も恩恵を受ける産業は、航空宇宙、医療機器、自動車、エレクトロニクス、積層造形などである。これらの産業は、高真球度パウダーが提供する高精度、一貫性、特殊特性を持つ材料を必要とします。
高真球度粉末の限界は?
制限事項としては、コストが高いこと、特殊合金の入手が困難である可能性があること、特殊な加工設備が必要であることなどが挙げられる。さらに、標準的なグレードやサイズは、すべての用途に適合するとは限らないため、カスタマイズが必要となる。
用途に合った高真球度パウダーを選ぶには?
適切な粉末の選択は、要求される材料特性、用途要件、予算、利用可能な設備などの要因によって異なります。サプライヤーやこの分野の専門家に相談することで、特定のニーズに最適な選択ができるようになります。
結論
高真球度パウダー は、現代の製造業において、比類のない精度、一貫性、および性能を提供する重要なコンポーネントです。そのユニークな特性は、航空宇宙、医療機器、積層造形などのハイテク産業において不可欠なものとなっている。コストと入手性は困難ですが、特に品質と信頼性が最重要視される用途では、その利点がこれらの欠点を上回ることがよくあります。
ベテランの技術者であれ、材料科学の世界に足を踏み入れたばかりであれ、高真球度粉末を理解することは、今日の先端製造業において極めて重要です。テクノロジーが進化し続けるにつれて、この驚くべき粉末の用途と能力もまた進化し、製造業の未来において重要な役割を果たすようになるでしょう。