レーザー積層造形技術は、レーザーを熱源とし、レーザーの高エネルギービーム集光効果を利用して金属粉末を素早く溶融させる製造方法である。
レーザーのエネルギー密度が高いため、航空宇宙などで使用されるチタン合金や高温合金などの難加工金属の製造を実現できる。また、レーザー積層造形技術は、部品の構造に制限されないという利点があり、複雑な構造、難加工、薄肉部品の加工・製造にも利用できる。
現在、レーザー積層造形技術は、チタン合金、高温合金、鉄系合金、アルミニウム合金、耐火合金、アモルファス合金、セラミックス、勾配材料などの材料に適用されている。航空宇宙分野での高性能複合部品や、バイオ製造分野での多孔質複合構造体の製造において、大きな利点がある。
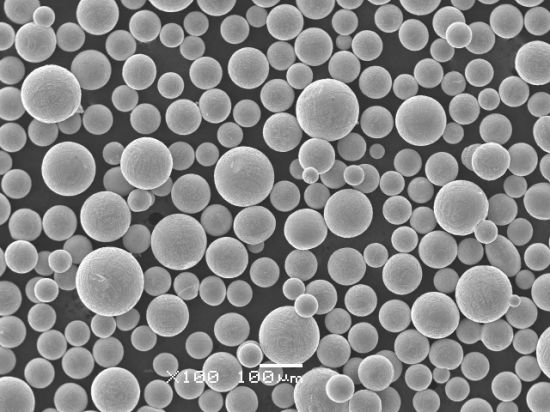
レーザーを熱源とする積層造形技術は、主に粉末供給によるレーザー堆積プロセスと粉末散布によるレーザー選択領域溶融技術に分けられる。
各ユニットの名称が異なるため、粉末供給ベースのレーザー溶融蒸着技術は、指向性エネルギー蒸着、DED、レーザー固体成形、LSF、直接金属蒸着、DMD、レーザー溶融蒸着、LMDなどとも呼ばれています。名称にかかわらず、原理はラピッドプロトタイピングの基本原理を使用することであり、原料として金属粉末を使用し、エネルギー源として高エネルギーレーザーを使用し、所定の処理経路に従って、金属粉末の同期化により、層ごとの溶融、急速凝固、層ごとの堆積を行い、金属部品の直接製造を実現します。
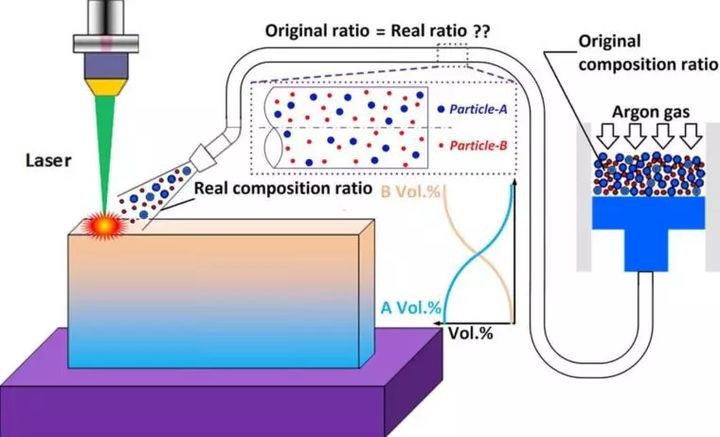
一般的に、レーザー金属成形システムプラットフォームは、下図に示すように、レーザー、CNCテーブル、粉末供給ノズル、高精度調整可能な粉末供給装置およびその他の補助装置で構成されています。パターン作成工程で使用可能なレーザーは、ビームパターンによって主に半導体連続レーザー、ファイバー連続レーザー、CO2連続レーザー、YAG:Ndパルスレーザーに分けられます。ノズルの配置により、主に同軸給粉ノズルグループと横方向給粉ノズルに分けられます。
レーザー選択溶融技術は、高輝度レーザーを使用して金属粉末材料をバインダーなしで直接溶融し、3Dモデルを鍛造品に匹敵する性能であらゆる複雑な構造部品に直接成形し、部品は表面仕上げだけで使用できる。主なレーザー積層造形技術には、選択的レーザー溶融(SLM)、粉末析出法などがある。
レーザーゾーン溶融の基本原理は、レーザービームが事前に計画された経路に従って走査され、事前に敷設された金属粉末を溶融することである。1レベルの走査を完了した後、作業室は高さが1層下がり、粉末層は粉末層を敷設し直すなど、必要な金属部品が製造されるまで、層ごとに繰り返し、全工程は真空環境下にあり、空気中の有害な不純物の影響を効果的に回避することができる。
レーザー選択溶融プロセスは、中間遷移を排除し、直接最終金属製品にすることができます。作成された部品は、高い寸法精度と良好な表面粗さ(Ra 10〜30μm)を持っており、様々な複雑な形状のワークピース、特に複雑な内部形状構造を持つ複雑なワークピースに適しています。伝統的な方法では製造できない。金型なしの単品および少量生産の複雑な構造部品に適しており、迅速な対応が可能である。 金型なしの単品および少量生産の複雑な構造部品に適しており、迅速な対応が可能である。