산업용 재료에 관한 한, 거의 마법과도 같은 것이 있습니다. 플라즈마 품질 파우더. 하이테크 산업이나 첨단 제조에 익숙하다면 이 매력적인 소재에 대해 들어보셨을 것입니다. 하지만 플라즈마 품질 파우더란 정확히 무엇이며 오늘날의 제조 공정에서 왜 그렇게 중요한 것일까요?
이 가이드에서는 플라즈마 고품질 분말의 세계에 대해 자세히 알아보세요. 분말의 구성, 특성, 응용 분야 등을 살펴볼 것입니다. 또한 다양한 금속 분말 모델을 비교하여 각 분말의 복잡한 차이점을 이해하는 데 도움을 드립니다. 업계 전문가든 호기심 많은 독자이든 이 글을 통해 필요한 인사이트를 얻을 수 있을 것입니다.
플라즈마 품질 파우더란 무엇인가요?
플라즈마 품질 분말은 플라즈마 원자화 공정을 통해 생성된 금속 분말의 일종을 말합니다. 이 방법은 플라즈마 토치를 사용하여 금속을 녹여 미세한 분말 입자로 원자화합니다. 그 결과 3D 프린팅, 코팅, 적층 제조 등 첨단 제조 공정에 적합한 특정 특성을 가진 고품질 파우더가 탄생합니다.
플라즈마 품질 파우더의 주요 특성
플라즈마 품질 파우더의 중요성을 이해하려면 그 가치를 높이는 주요 특성을 이해하는 것이 중요합니다:
- 입자 크기 분포: 플라즈마 품질의 분말은 입자 크기 분포가 좁아 정밀 응용 분야에 이상적입니다.
- 구형성: 입자가 거의 완벽하게 구형이어서 유동성과 포장 밀도가 향상됩니다.
- 순도: 이 분말은 산화물이나 기타 불순물로 인한 오염을 최소화하여 순도 높은 수준을 자랑합니다.
- 밀도: 플라즈마 품질의 분말은 일반적으로 부피와 탭 밀도가 높아 일관된 성능을 보장합니다.
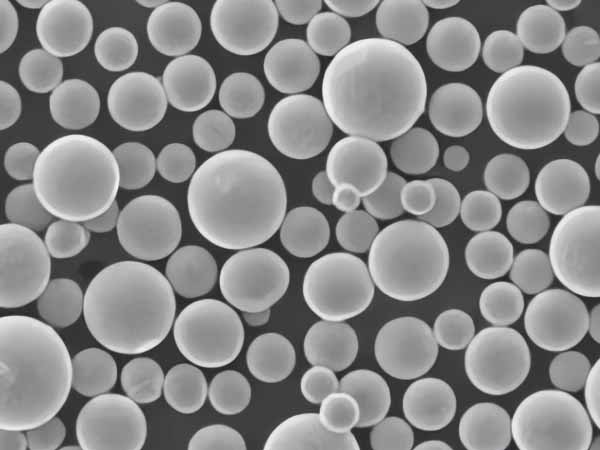
플라즈마 품질 파우더의 종류
플라즈마 품질 분말의 다양한 용도를 고려할 때 여러 가지 유형과 등급을 사용할 수 있습니다. 아래는 가장 대표적인 플라즈마 품질의 금속 분말을 특정 모델과 설명을 포함하여 자세히 나열한 표입니다:
모델 | 구성 | 특성 | 애플리케이션 | 주목할 만한 속성 |
---|---|---|---|---|
GKN 회가네스 PF-1 | 철 기반 합금 | 높은 구형도, 뛰어난 유동성 | 금속 사출 성형, 3D 프린팅 | 고순도, 낮은 산소 함량 |
샌드빅 오스프리 17-4 | 스테인리스 스틸 | 부식 방지, 높은 중량 대비 강도 비율 | 항공우주, 의료용 임플란트 | 저탄소, 고인장 강도 |
AP&C Ti-6Al-4V | 티타늄 합금 | 생체 적합성, 경량, 높은 인장 강도 | 항공우주, 의료, 자동차 | 뛰어난 내피로성 |
카펜터 LPW 316L | 스테인리스 스틸 | 우수한 내식성, 저탄소 | 해양, 화학 처리 | 높은 연성, 용접성 |
EOS 니켈합금 HX | 니켈 기반 합금 | 내열성, 내산화성 | 터빈, 고온 환경 | 뛰어난 크리프 저항성 |
회가나스 FeSi 75 | 철-실리콘 합금 | 높은 자기 투과성, 낮은 전기적 손실 | 전기 강철 부품 | 고순도, 일관된 입자 크기 |
Tekna Ti64 Gd23 | 티타늄 합금 | 고강도, 우수한 연신율, 고압 사용에 적합 | 자동차, 항공우주, 의료 기기 | 일관된 입자 크기 분포 |
프렉스에어 인코넬 625 | 니켈-크롬 | 뛰어난 피로 및 열 피로 강도 | 석유 및 가스, 원자로 | 우수한 용접성 및 내식성 |
Metco 43VF-NS | 코발트 합금 | 내마모성, 고온에서도 강도 유지 | 터빈 블레이드, 마모 부품 | 뛰어난 고온 특성 |
토얄 AP10 | 알루미늄 합금 | 가볍고 높은 열 전도성 | 항공우주, 전자 | 뛰어난 내산화성 |
구성 플라즈마 품질 파우더
플라즈마 품질의 파우더의 구성은 놀라운 특성을 제공합니다. 원하는 용도에 따라 다양한 금속 분말은 서로 다른 원소로 구성됩니다. 다음은 일반적인 구성에 대한 분석입니다:
금속 분말 유형 | 주요 구성 요소 | 일반적인 첨가제 |
---|---|---|
철 기반 합금 | 철(Fe), 탄소(C), 실리콘(Si) | 망간(Mn), 니켈(Ni), 크롬(Cr) |
스테인리스 스틸 | 철(Fe), 크롬(Cr), 니켈(Ni) | 몰리브덴(Mo), 탄소(C), 망간(Mn) |
티타늄 합금 | 티타늄(Ti), 알루미늄(Al), 바나듐(V) | 산소(O), 질소(N), 탄소(C) |
니켈 기반 합금 | 니켈(Ni), 크롬(Cr), 몰리브덴(Mo) | 철(Fe), 알루미늄(Al), 티타늄(Ti) |
코발트 합금 | 코발트(Co), 크롬(Cr), 텅스텐(W) | 니켈(Ni), 몰리브덴(Mo), 탄소(C) |
알루미늄 합금 | 알루미늄(Al), 실리콘(Si), 마그네슘(Mg) | 구리(Cu), 아연(Zn), 망간(Mn) |
컴포지션 이해
플라즈마 품질의 분말을 다룰 때는 그 성분을 이해하는 것이 중요합니다. 예를 들어 다음과 같은 티타늄 합금은 AP&C Ti-6Al-4V 는 무게 대비 강도가 높아 항공우주 산업에서 인기가 높습니다. 반면에 스테인리스 스틸 316L 는 내식성이 뛰어나 해양 분야에서 널리 사용됩니다.
이러한 분말의 구성에 따라 물리적, 기계적 특성뿐만 아니라 다양한 제조 공정과의 호환성도 결정됩니다.
플라즈마 품질 파우더의 특성
플라즈마 품질의 분말은 첨단 제조의 요구 사항을 충족하도록 설계된 특정 특성으로 인해 두드러집니다. 아래에서는 이러한 분말이 바람직한 주요 특성을 자세히 살펴봅니다:
입자 크기 분포
플라즈마 품질 파우더의 두드러진 특징 중 하나는 입자 크기 분포가 엄격하게 제어된다는 점입니다. 이는 일관된 층 증착이 중요한 3D 프린팅과 같은 애플리케이션에서 균일성을 보장하는 데 필수적입니다. 예를 들어 AP&C Ti-6Al-4V 분말은 일반적으로 15-45미크론 범위의 입자 크기 분포를 가지며, 이는 적층 제조 공정에 이상적입니다.
구형성
구형도는 분말 입자가 얼마나 둥근지를 나타냅니다. 구형도가 높으면 유동성이 향상되어 분말이 뭉치지 않고 기계에 쉽게 공급될 수 있기 때문에 매우 중요합니다. 이는 플라즈마 분사 및 분말 야금과 같은 애플리케이션에서 특히 중요합니다. 다음과 같은 분말 GKN 회가네스 PF-1 는 구형도가 높아 최종 제품의 포장 밀도가 향상되고 기계적 특성이 개선되는 것으로 알려져 있습니다.
순도
순도는 플라즈마 품질 파우더에 있어 타협할 수 없는 요소입니다. 불순물은 최종 제품의 결함으로 이어질 수 있기 때문에 이러한 분말은 엄격한 품질 관리 조치를 거칩니다. 예를 들어 샌드빅 오스프리 17-4 스테인리스 스틸 파우더는 탄소 함량이 낮아 부식 위험을 줄이고 재료의 전반적인 수명을 향상시키는 데 도움이 되는 것으로 알려져 있습니다.
밀도
플라즈마 품질 분말의 밀도는 제조된 부품의 최종 특성을 결정하는 데 중요한 역할을 합니다. 벌크 밀도가 높으면 최종 제품의 다공성이 낮아지므로 바람직하고, 탭 밀도가 높으면 유동성이 좋다는 것을 나타냅니다. 예를 들어 EOS 니켈합금 HX 는 밀도가 높아 부품의 구조적 건전성과 내구성을 보장하기 때문에 고온 애플리케이션에서 선호됩니다.
플라즈마 품질 파우더의 응용 분야
플라즈마 품질 파우더의 다목적성은 다양한 산업 분야에서 폭넓게 활용되는 데서 잘 드러납니다. 이러한 분말은 다음과 같은 여러 첨단 제조 공정의 근간이 됩니다:
산업 | 일반적인 애플리케이션 | 선호하는 파우더 모델 |
---|---|---|
항공우주 | 터빈 블레이드, 구조 부품, 엔진 부품 | AP&C Ti-6Al-4V, Metco 43VF-NS |
의료 | 임플란트, 보철물, 수술 기구 | AP&C Ti-6Al-4V, 샌드빅 오스프리 17-4 |
자동차 | 엔진 부품, 경량 구조 부품 | Tekna Ti64 Gd23, 카펜터 LPW 316L |
에너지 | 터빈 부품, 원자로 부품 | 프렉스에어 인코넬 625, EOS 니켈합금 HX |
전자 제품 | 방열판, 전도성 부품 | 토얄 AP10, 회가나스 FeSi 75 |
해양 | 프로펠러, 샤프트, 패스너 | 카펜터 LPW 316L, 샌드빅 오스프리 17-4 |
석유 및 가스 | 드릴링 장비, 파이프라인 구성 요소 | 프렉스에어 인코넬 625, Metco 43VF-NS |
자세한 애플리케이션
항공우주 산업
항공우주 분야에서 소재는 고온부터 극심한 기계적 스트레스까지 극한의 조건을 견뎌내야 합니다. AP&C Ti-6Al-4V 은 가볍고 강도가 높기 때문에 널리 사용되는 소재입니다. 성능과 신뢰성이 타협할 수 없는 터빈 블레이드와 같은 핵심 부품 제조에 사용됩니다.
의료 분야
의료 분야에서는 생체 적합성과 내식성이 핵심입니다. 샌드빅 오스프리 17-4 은 체액에 강하고 장기간 사용해도 안전하게 사용할 수 있어 수술 기구와 임플란트에 자주 사용됩니다. 다음과 같은 티타늄 합금은 AP&C Ti-6Al-4V 는 인체와의 호환성 때문에 임플란트용으로도 인기가 높습니다.
자동차 부문
자동차 산업은 강도와 무게 사이에서 균형을 이루는 소재를 찾습니다. Tekna Ti64 Gd23 는 부품의 무게를 가볍게 유지하면서 높은 강도를 제공하여 연비와 차량 성능을 향상시키는 이 분야에 이상적입니다.
사양, 크기, 등급 및 표준
플라즈마 품질 파우더를 선택할 때는 사양, 크기, 등급 및 표준을 고려하는 것이 중요합니다. 다음 표에는 다양한 플라즈마 품질 파우더와 관련된 몇 가지 주요 사양 및 표준이 요약되어 있습니다:
파우더 모델 | 입자 크기 범위 | 벌크 밀도 (g/cm³) | 탭 밀도 (g/cm³) | 표준 |
---|---|---|---|---|
GKN 회가네스 PF-1 | 10-50 미크론 | 3.0-4.0 | 4.5-5.5 | ASTM B214, ISO 4497 |
샌드빅 오스프리 17-4 | 15-45 미크론 | 4.0-5.0 | 5.5-6.5 | ASTM F75, ISO 5832-1 |
AP&C Ti-6Al-4V | 15-45 미크론 | 2.5-3.5 | 3.5-4.5 | ASTM F136, ISO 5832-3 |
카펜터 LPW 316L | 15-53 미크론 | 3.0-4.0 | 4.0-5.0 | ASTM A240, ISO 5832-1 |
EOS 니켈합금 HX | 20-63 미크론 | 4.5-5.5 | 6.0-7.0 | ASTM B168, ISO 15156-3 |
회가나스 FeSi 75 | 10-50 미크론 | 2.5-3.5 | 3.5-4.5 | ASTM A726, ISO 9001 |
Tekna Ti64 Gd23 | 15-45 미크론 | 2.5-3.5 | 3.5-4.5 | ASTM F136, ISO 5832-3 |
프렉스에어 인코넬 625 | 20-63 미크론 | 4.5-5.5 | 6.0-7.0 | ASTM B443, ISO 15156-3 |
Metco 43VF-NS | 15-53 미크론 | 4.0-5.0 | 5.5-6.5 | ASTM F75, ISO 5832-1 |
토얄 AP10 | 10-50 미크론 | 2.5-3.5 | 3.5-4.5 | ASTM B557, ISO 9001 |
적합한 사양 선택
적합한 파우더를 선택하는 것은 특정 용도에 따라 달라집니다. 예를 들어 에너지 분야와 같이 고온의 환경에서 작업하는 경우, EOS 니켈합금 HX 가 크립 저항성이 뛰어나기 때문에 가장 좋은 선택일 수 있습니다. 반면에 의료용 임플란트의 경우, AP&C Ti-6Al-4V 는 생체 적합성과 강도 때문에 선호됩니다.
공급업체 및 가격 세부 정보
고품질 플라즈마 파우더의 공급처를 파악하고 가격대를 이해하는 것은 모든 비즈니스에 필수적입니다. 다음은 몇 가지 주요 공급업체에 대한 정보와 일반적인 가격 세부 정보가 담긴 표입니다:
공급업체 | 파우더 모델 사용 가능 | 가격 범위(kg당) | 추가 서비스 |
---|---|---|---|
GKN 회가나에 | GKN 회가네스 PF-1, FeSi 75 | $50 – $120 | 맞춤형 파우더 블렌드, 기술 지원 |
AP&C(GE 애디티브) | AP&C Ti-6Al-4V, Tekna Ti64 Gd23 | $200 – $500 | 분말 재활용, 품질 인증 |
샌드빅 오스프리 | 샌드빅 오스프리 17-4, 카펜터 LPW 316L | $150 – $300 | 기술 컨설팅, 애플리케이션 지원 |
프렉스에어 표면 기술 | 프렉스에어 인코넬 625, Metco 43VF-NS | $100 – $250 | 맞춤형 합금, R&D 협업 |
EOS GmbH | EOS 니켈합금 HX, 토얄 AP10 | $200 – $400 | 애플리케이션 개발, 교육 프로그램 |
카펜터 기술 | 카펜터 LPW 316L, EOS 니켈합금 HX | $150 – $350 | 맞춤형 합금, 열처리 서비스 |
공급업체에서 살펴봐야 할 사항
공급업체를 선택할 때는 가격뿐만 아니라 공급업체가 제공하는 추가 서비스도 고려하세요. 예를 들어 AP&C 는 파우더 재활용 서비스를 제공하여 시간이 지남에 따라 낭비와 비용을 크게 줄일 수 있습니다. 마찬가지로 샌드빅 오스프리 기술 컨설팅을 제공하여 파우더를 최대한 활용할 수 있도록 제조 공정을 최적화할 수 있도록 지원합니다.
장단점: 장점과 한계 플라즈마 품질 파우더
플라즈마 품질의 파우더는 매우 다양하고 유용하지만 단점도 없는 것은 아닙니다. 다음은 장점과 한계를 비교한 것입니다:
측면 | 장점 | 제한 사항 |
---|---|---|
파티클 구형도 | 유동성 향상으로 부품 일관성 개선 | 복잡한 제조 공정으로 인해 비용이 약간 높음 |
순도 | 최종 제품의 결함 가능성 감소 | 고순도 분말은 더 엄격한 취급 조치가 필요할 수 있습니다. |
밀도 | 강력하고 밀도 높은 최종 결과물 | 고밀도 분말은 더 비쌀 수 있습니다. |
다용도성 | 다양한 산업에 적합 | 일부 파우더는 고도로 전문화되어 있어 일반적인 사용이 제한됩니다. |
사용자 지정 | 특정 애플리케이션에 맞게 조정 가능 | 맞춤형 분말은 리드 타임이 길 수 있습니다. |
환경 영향 | 재활용 가능, 폐기물 감소 | 플라즈마 원자화 공정은 상당한 에너지를 소비합니다. |
장단점에 대한 최종 생각
플라즈마 품질 파우더의 장점과 한계 사이의 상충 관계를 이해하면 보다 현명한 결정을 내리는 데 도움이 될 수 있습니다. 예를 들어, 다음과 같은 고순도 파우더는 샌드빅 오스프리 17-4 는 더 비싸지만, 특히 의료용 임플란트나 항공우주 부품과 같은 중요한 애플리케이션에서 최종 제품의 수명과 성능을 크게 향상시킬 수 있습니다.
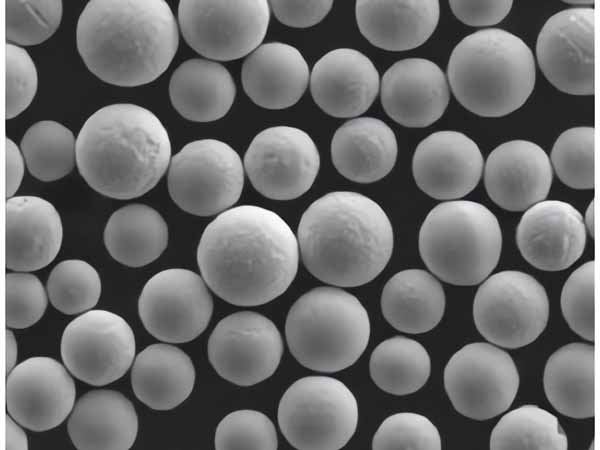
자주 묻는 질문
질문 | 답변 |
---|---|
플라즈마 분무의 주요 장점은 무엇인가요? | 플라즈마 분무는 입자 크기 분포가 일정한 고구형의 고순도 분말을 생산하므로 정밀 응용 분야에 이상적입니다. |
플라즈마 품질 파우더의 이점을 가장 많이 누릴 수 있는 산업은? | 항공우주, 의료, 자동차, 에너지 산업은 소재의 높은 성능과 신뢰성으로 인해 가장 큰 혜택을 누리고 있습니다. |
플라즈마 품질의 파우더를 재활용할 수 있나요? | 예, 많은 공급업체에서 파우더 재활용 서비스를 제공하여 비용과 환경에 미치는 영향을 줄일 수 있습니다. |
올바른 플라즈마 품질의 파우더를 선택하려면 어떻게 해야 하나요? | 필요한 구성, 입자 크기, 밀도, 업계 표준 등 애플리케이션의 특정 요구 사항을 고려하세요. |
플라즈마 품질의 파우더를 사용할 때 환경에 대한 우려는 없나요? | 분말 자체는 재활용할 수 있지만 플라즈마 분무 공정은 에너지 집약적이기 때문에 환경에 미치는 영향을 고려해야 합니다. |
플라즈마 품질 파우더의 주요 기준은 무엇인가요? | 일반적인 표준에는 분말이 특정 산업 요구 사항을 충족하도록 보장하는 ASTM 및 ISO 인증이 포함됩니다. |
입자 구형도는 최종 제품에 어떤 영향을 미치나요? | 구형도가 높을수록 파우더의 유동성이 향상되어 최종 부품이 더욱 균일하고 안정적으로 제작됩니다. |
플라즈마 품질의 파우더를 대체할 수 있는 비용 효율적인 대안이 있나요? | 가스 분무 분말과 같은 대안이 존재하지만, 특히 중요한 애플리케이션에서는 동일한 수준의 성능을 제공하지 못할 수 있습니다. |
이 문서에서는 다음 사항에 대해 자세히 설명합니다. 플라즈마 품질 파우더를 통해 분말의 특성, 용도, 필요에 맞는 분말을 선택하는 방법에 대한 전반적인 이해를 돕습니다. 항공우주, 의료, 자동차 산업 등 어떤 분야에 종사하든 이러한 분말에 대해 자세히 알면 제조 공정과 최종 제품 품질을 크게 향상시킬 수 있습니다.