Introduction to Liquid Metal Jetting (LMJ)
Liquid Metal Jetting (LMJ) is a cutting-edge additive manufacturing technique that utilizes liquid metal droplets to create intricate and highly precise metal components layer by layer. This technology has garnered significant attention in recent years due to its potential for producing complex geometries with exceptional material properties. Unlike traditional metal manufacturing methods, LMJ offers unparalleled design freedom and material efficiency, making it a game-changer in various industries.
Overview of Liquid Metal Jetting (LMJ)
Liquid Metal Jetting (LMJ) operates on the principle of jetting fine droplets of molten metal onto a substrate to build up a part. This process is analogous to inkjet printing but uses metal instead of ink. The key advantage of LMJ lies in its ability to produce highly detailed and intricate parts without the need for molds or tooling, thus reducing production costs and lead times.
Key Features:
- Precision: LMJ allows for the creation of components with fine details and tight tolerances.
- Material Efficiency: By jetting only the necessary amount of metal, LMJ minimizes waste.
- Design Freedom: Complex geometries and internal features can be easily achieved.
- Scalability: Suitable for both small-scale prototypes and large-scale production.
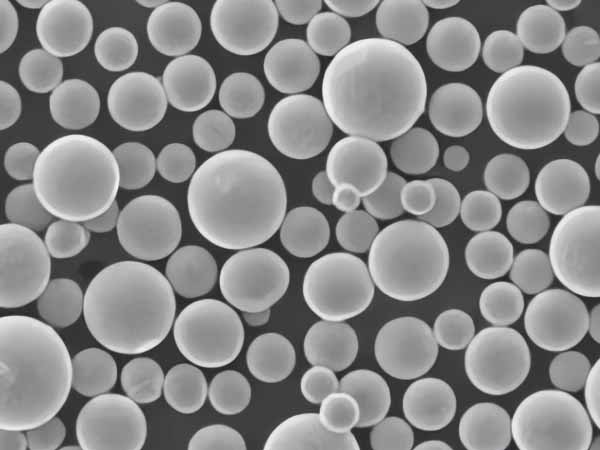
Types of Metal Powders Used in LMJ
The choice of metal powder is crucial in Liquid Metal Jetting, as it directly affects the mechanical properties, surface finish, and overall quality of the final product. Here are ten specific metal powders commonly used in LMJ:
Metal Powder | Composition | Properties | Characteristics |
---|---|---|---|
Stainless Steel 316L | Fe, Cr, Ni, Mo | High corrosion resistance, good mechanical properties | Ideal for medical and aerospace applications |
Titanium Ti-6Al-4V | Ti, Al, V | High strength-to-weight ratio, excellent biocompatibility | Widely used in medical implants and aerospace |
Aluminum AlSi10Mg | Al, Si, Mg | Lightweight, good thermal conductivity | Commonly used in automotive and aerospace industries |
Inconel 625 | Ni, Cr, Mo, Nb | High temperature resistance, excellent corrosion resistance | Suitable for high-performance applications |
Copper Cu | Cu | Excellent electrical and thermal conductivity | Used in electrical and heat transfer applications |
Cobalt-Chrome CoCr | Co, Cr, Mo | High strength, wear resistance, biocompatibility | Ideal for dental and orthopedic implants |
Tool Steel H13 | Fe, Cr, Mo, V | High hardness, wear resistance | Used for tooling and molds |
Nickel Alloy 718 | Ni, Cr, Fe, Nb | High strength, corrosion resistance | Suitable for aerospace and high-stress applications |
Bronze CuSn10 | Cu, Sn | Good corrosion resistance, wear resistance | Used in artistic and historical restorations |
Gold Au | Au | Excellent electrical conductivity, biocompatibility | Used in electronics and jewelry |
Applications of Liquid Metal Jetting (LMJ)
Liquid Metal Jetting is utilized in a wide array of industries due to its versatility and precision. Here are some of the prominent applications:
Application | Industry | Benefits |
---|---|---|
Prototyping | Various | Rapid iteration, cost-effective |
Medical Implants | Medical | Customization, biocompatibility |
Aerospace Components | Aerospace | Lightweight, complex geometries |
Automotive Parts | Automotive | High performance, durability |
Jewelry Making | Fashion | Intricate designs, material efficiency |
Electrical Components | Electronics | Precision, conductivity |
Tooling and Molds | Manufacturing | High durability, precision |
Artistic Sculptures | Art | Custom designs, material versatility |
Heat Exchangers | HVAC | Efficient thermal management |
Sensor Housings | Industrial | Protection, durability |
Composition of Liquid Metal Jetting (LMJ)
The composition of the metal powders used in LMJ significantly influences the properties of the final product. Understanding the elemental makeup helps in selecting the right material for specific applications.
Metal Powder | Elemental Composition | Key Attributes |
---|---|---|
Stainless Steel 316L | Fe, Cr (16-18%), Ni (10-14%), Mo (2-3%) | Corrosion resistance, strength |
Titanium Ti-6Al-4V | Ti (88-90%), Al (6%), V (4%) | Strength-to-weight ratio, biocompatibility |
Aluminum AlSi10Mg | Al (90-92%), Si (9-11%), Mg (0.3-0.6%) | Lightweight, machinability |
Inconel 625 | Ni (58%), Cr (20-23%), Mo (8-10%), Nb (3.15-4.15%) | Heat resistance, corrosion resistance |
Copper Cu | Cu (99.9%) | Electrical conductivity, thermal conductivity |
Cobalt-Chrome CoCr | Co (60%), Cr (30%), Mo (5-10%) | Strength, wear resistance |
Tool Steel H13 | Fe, Cr (4.75-5.5%), Mo (1.1-1.75%), V (0.8-1.2%) | Hardness, toughness |
Nickel Alloy 718 | Ni (50-55%), Cr (17-21%), Fe (17%), Nb (4.75-5.5%) | Strength, corrosion resistance |
Bronze CuSn10 | Cu (89-91%), Sn (9-11%) | Corrosion resistance, wear resistance |
Gold Au | Au (99.9%) | Electrical conductivity, aesthetic appeal |
-
0# Pure Nickel powder
-
NiCoCrAlY alloys powders
-
Rene 142 alloy-Rene Powder
-
Haynes 25 Haynes Powder
-
FGH95 Ni-base Alloy Powder | Nickel Alloy Powder
-
CMSX-4 Nickel Alloy Powder | Nickel Alloy Powder
-
Ni-Fe-Mo Soft Magnetic Powder | Nickel Alloy Powder
-
Ni-Cr-Mo Alloy Powder | Nickel Alloy Powder
-
Nickel Titanium Alloy Powder | Nickel Alloy Powder
Characteristics of Liquid Metal Jetting (LMJ)
The success of Liquid Metal Jetting largely depends on its unique characteristics, which make it a preferred choice for various applications:
1. Precision and Detail:
LMJ can produce parts with extremely fine details and complex geometries that would be challenging to achieve with traditional manufacturing methods.
2. Material Efficiency:
By using only the required amount of metal powder, LMJ minimizes material waste, making it an environmentally friendly option.
3. Speed and Scalability:
LMJ can quickly produce both prototypes and production parts, making it ideal for rapid iteration and scalable manufacturing.
4. Surface Finish:
The droplets of molten metal create a smooth surface finish, reducing the need for post-processing.
5. Mechanical Properties:
Parts produced via LMJ exhibit excellent mechanical properties, including high strength and durability, due to the quality of the metal powders used.
Advantages of Liquid Metal Jetting (LMJ)
Liquid Metal Jetting offers numerous advantages over traditional manufacturing techniques and other additive manufacturing methods:
1. Design Freedom:
LMJ allows for the creation of intricate designs and complex geometries without the need for molds or tooling.
2. Reduced Lead Times:
The rapid production capability of LMJ significantly reduces lead times compared to conventional manufacturing.
3. Cost-Effectiveness:
By minimizing material waste and eliminating the need for tooling, LMJ can lower production costs.
4. High-Quality Parts:
The precision and detail achievable with LMJ result in high-quality parts with excellent mechanical properties.
5. Versatility:
LMJ is suitable for a wide range of applications across various industries, from aerospace to medical to artistic endeavors.
Specifications, Sizes, Grades, and Standards in LMJ
When selecting metal powders for Liquid Metal Jetting, it’s important to consider specifications, sizes, grades, and standards to ensure compatibility and performance:
Metal Powder | Specifications | Sizes | Grades | Standards |
---|---|---|---|---|
Stainless Steel 316L | ASTM A276, A240 | 10-45 µm | 316L | ISO 5832-1 |
Titanium Ti-6Al-4V | ASTM F1472 | 15-45 µm | Grade 5 | ISO 5832-3 |
Aluminum AlSi10Mg | EN AW-4047 | 20-63 µm | AlSi10Mg | ASTM B928 |
Inconel 625 | AMS 5666 | 15-45 µm | Inconel 625 | ASTM B443 |
Copper Cu | ASTM B216 | 15-45 µm | C11000 | ASTM B152 |
Cobalt-Chrome CoCr | ASTM F75 | 10-45 µm | CoCrMo | ISO 5832-4 |
Tool Steel H13 | ASTM A681 | 20-53 µm | H13 | ASTM A681 |
Nickel Alloy 718 | AMS 5662 | 15-45 µm | Inconel 718 | ASTM B637 |
Bronze CuSn10 | EN 1982 | 20-63 µm | CuSn10 | ASTM B427 |
Gold Au | ASTM B562 | 15-45 µm | 24K | ASTM B562 |
Suppliers and Pricing Details for Metal Powders
The choice of supplier and pricing can significantly impact the overall cost and quality of LMJ parts. Here are some reputable suppliers and indicative pricing details:
Supplier | Metal Powders Offered | Price Range (per kg) | Additional Services |
Höganäs | Stainless Steel 316L, Tool Steel H13 | $50-$100 | Custom alloys, technical support |
Carpenter Technology | Titanium Ti-6Al-4V, Inconel 625 | $100-$200 | Material certification, R&D support |
Erasteel | Stainless Steel 316L, Tool Steel H13 | $60-$120 | Customized powders, metallurgical advice |
Sandvik | Titanium Ti-6Al-4V, Nickel Alloy 718 | $120-$250 | Advanced testing, application support |
GKN Additive | Aluminum AlSi10Mg, Inconel 625 | $70-$150 | Powder optimization, post-processing services |
LPW Technology | Stainless Steel 316L, Cobalt-Chrome CoCr | $80-$180 | Powder lifecycle management, traceability |
Valimet | Aluminum AlSi10Mg, Bronze CuSn10 | $60-$130 | Customized particle sizes, blending services |
PyroGenesis | Titanium Ti-6Al-4V, Nickel Alloy 718 | $150-$300 | Plasma atomization, material consultation |
Tekna | Copper Cu, Gold Au | $90-$200 | High-purity powders, technical guidance |
Arcam | Titanium Ti-6Al-4V, Stainless Steel 316L | $110-$220 | Electron beam melting, material testing |
Comparing Pros and Cons of Liquid Metal Jetting (LMJ)
Understanding the advantages and limitations of Liquid Metal Jetting can help in determining its suitability for specific applications:
Pros | Cons |
---|---|
High Precision: LMJ produces parts with intricate details and tight tolerances. | Cost of Metal Powders: High-quality metal powders can be expensive. |
Material Efficiency: Minimizes waste by using only the necessary amount of metal. | Equipment Cost: Initial setup and equipment can be costly. |
Design Flexibility: Allows for complex geometries and custom designs. | Surface Finish: May require post-processing for a smoother finish. |
Speed: Rapid production of prototypes and small batches. | Material Limitations: Not all metals are suitable for LMJ. |
Reduced Lead Times: Faster turnaround compared to traditional methods. | Process Control: Requires precise control of process parameters. |
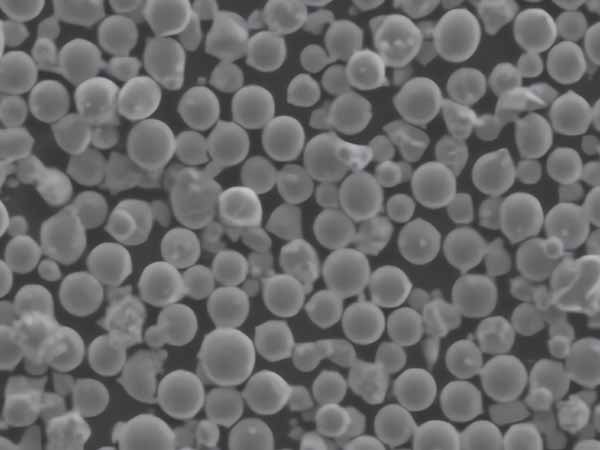
FAQ
Question | Answer |
---|---|
What is Liquid Metal Jetting? | Liquid Metal Jetting is an additive manufacturing technique that uses droplets of molten metal to build parts layer by layer. |
What are the benefits of LMJ? | LMJ offers high precision, material efficiency, design flexibility, and reduced lead times. |
What types of metals can be used in LMJ? | Metals such as stainless steel, titanium, aluminum, Inconel, copper, and more can be used. |
What industries benefit from LMJ? | Industries such as aerospace, medical, automotive, electronics, and art benefit from LMJ. |
Are there any limitations to LMJ? | High cost of metal powders, equipment cost, and the need for post-processing can be limitations. |
How does LMJ compare to traditional manufacturing? | LMJ offers faster production, reduced material waste, and greater design flexibility compared to traditional methods. |
What are some common applications of LMJ? | Applications include prototyping, medical implants, aerospace components, jewelry making, and more. |
What is the typical size range of metal powders used in LMJ? | Metal powders typically range from 10 to 63 micrometers in size. |
Who are some reputable suppliers of metal powders for LMJ? | Reputable suppliers include Höganäs, Carpenter Technology, Sandvik, GKN Additive, and more. |
What are the key considerations when selecting metal powders for LMJ? | Considerations include composition, size, grade, standards, and supplier reputation. |
Conclusion
Liquid Metal Jetting (LMJ) stands at the forefront of modern manufacturing technologies, offering unparalleled precision, material efficiency, and design flexibility. By understanding the composition, characteristics, and applications of LMJ, industries can leverage this innovative technology to produce high-quality, customized metal components. As the field continues to evolve, LMJ is set to revolutionize manufacturing processes, making it an indispensable tool in various high-performance applications. Whether you’re in aerospace, medical, automotive, or artistic fields, LMJ provides the capabilities to push the boundaries of what’s possible in metal fabrication.