Introduction
Overview of 3D printing technology
3D printing technology has revolutionized the manufacturing industry by allowing the creation of complex and intricate designs with ease. This technology utilizes metal powder to build three-dimensional objects layer by layer, resulting in highly precise and durable end products. The use of metal powder in 3D printing offers numerous advantages, including increased efficiency and cost-effectiveness. By maximizing the efficiency of the printing process, manufacturers can significantly reduce production time and costs, making it an ideal solution for various industries. Furthermore, the versatility of metal powder allows for the production of a wide range of products, from aerospace components to medical implants, further expanding the possibilities of 3D printing technology. In this article, we will explore the different ways in which metal powder is utilized to maximize efficiency in 3D printing and its impact on various industries.
Advantages of using metal powder for 3D printing
One of the key advantages of using metal powder for 3D printing is its ability to produce highly complex and intricate designs. The fine particles of metal powder allow for precise layering, resulting in intricate details and intricate geometries that would be difficult to achieve with traditional manufacturing methods. Additionally, metal powder offers a wide range of material options, including various alloys and metals, allowing for the production of parts with specific properties such as strength, durability, and conductivity. Furthermore, 3D printing with metal powder enables faster production times and reduced waste compared to conventional manufacturing processes, making it a highly efficient and cost-effective solution for industries such as aerospace, automotive, and healthcare.
Importance of efficiency in 3D printing
Efficiency plays a crucial role in the world of 3D printing, and it is particularly important when it comes to using metal powder. Metal powder is a valuable resource that can be costly, so maximizing efficiency is essential to minimize waste and maximize productivity. By optimizing the usage of metal powder, 3D printing manufacturers can reduce material costs and improve overall production efficiency. Additionally, efficient use of metal powder can also result in higher quality prints, as it allows for better control over the printing process and reduces the risk of defects. Therefore, understanding the importance of efficiency in 3D printing, especially with metal powder, is key to achieving successful and cost-effective 3D printing operations.
Types of Metal Powders for 3D Printing
Stainless steel powder
Stainless steel powder is a versatile material that plays a crucial role in maximizing efficiency with metal 3D printing. With its high strength and excellent corrosion resistance, stainless steel powder enables the production of durable and long-lasting 3D printed parts. Moreover, its fine particle size and uniform distribution allow for precise and intricate designs to be achieved. Whether used in aerospace, automotive, or medical applications, stainless steel powder offers unparalleled performance and reliability, making it an ideal choice for enhancing efficiency in the 3D printing process.
Titanium powder
Titanium powder is widely used in the field of 3D printing due to its exceptional properties and benefits. As a lightweight and high-strength material, titanium powder allows for the creation of complex and intricate designs with ease. Additionally, titanium powder has excellent corrosion resistance, making it suitable for applications in industries such as aerospace, medical, and automotive. With its ability to achieve high levels of precision and accuracy, titanium powder plays a crucial role in maximizing efficiency in 3D printing processes. By utilizing titanium powder, manufacturers can optimize their production capabilities and deliver superior quality products to their customers.
Aluminum powder
Aluminum powder is a crucial material in the field of 3D printing. It offers exceptional properties that make it ideal for various applications. With its high thermal conductivity and low density, aluminum powder allows for the production of lightweight and heat-resistant components. Additionally, its excellent flowability and ability to create intricate geometries make it a preferred choice for complex designs. Furthermore, aluminum powder is highly compatible with different 3D printing technologies, enabling efficient and precise manufacturing processes. Overall, the use of aluminum powder in 3D printing plays a significant role in maximizing efficiency and achieving high-quality results.
Properties of Metal Powders
Particle size and shape
Particle size and shape play a crucial role in maximizing efficiency with metal powder for 3D printing. The size of the particles determines the resolution and surface finish of the printed object. Smaller particles result in finer details and smoother surfaces, while larger particles may lead to a rougher finish. Additionally, the shape of the particles affects the flowability and packing density of the powder, which in turn impacts the printing process. By carefully controlling the particle size and shape, manufacturers can optimize the printing parameters and achieve higher printing speeds and better overall efficiency.
Chemical composition
The chemical composition of metal powders used in 3D printing plays a crucial role in maximizing efficiency. Different metals have varying compositions, which directly impact their properties and behavior during the printing process. For example, titanium powders are known for their high strength and corrosion resistance, making them suitable for applications in aerospace and medical industries. On the other hand, aluminum powders offer lightweight and excellent thermal conductivity, making them ideal for heat exchangers and automotive components. Understanding the chemical composition of metal powders allows engineers and designers to select the most appropriate material for their specific requirements, ensuring optimal performance and cost-effectiveness in 3D printing.
Flowability and density
Flowability and density are two important factors to consider when using metal powder for 3D printing. Flowability refers to the ability of the powder to flow freely and evenly through the printing nozzle, ensuring consistent and precise printing. A powder with good flowability will result in smooth and accurate prints. On the other hand, density refers to the compactness of the powder particles. Higher density powders can provide better mechanical properties and higher strength in the printed parts. Balancing flowability and density is crucial in order to achieve optimal printing results and maximize efficiency with metal powder for 3D printing.
Preparation and Handling of Metal Powders
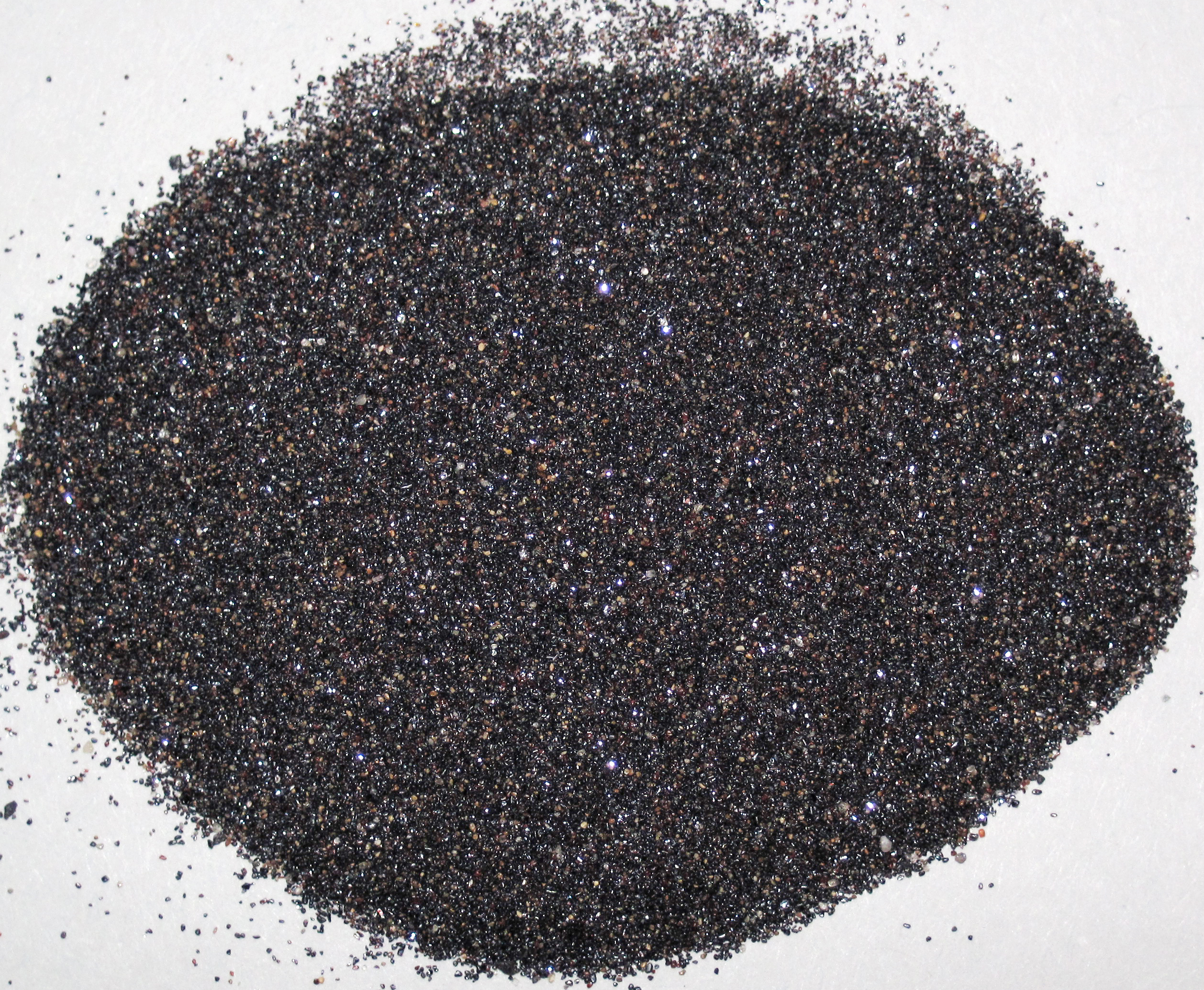
Powder production methods
Powder production methods play a crucial role in maximizing efficiency with metal powder for 3D printing. These methods involve the transformation of raw materials into fine powders that are suitable for additive manufacturing processes. One commonly used method is atomization, where molten metal is sprayed into a gas or liquid medium, resulting in the formation of small droplets that solidify into powder particles. Another method is mechanical milling, which involves the grinding and crushing of metal particles to achieve the desired size and shape. These production methods ensure that the metal powders used in 3D printing are of high quality, with consistent particle size distribution and excellent flowability. By carefully selecting and optimizing these methods, manufacturers can enhance the efficiency and performance of their 3D printing processes, leading to the production of high-quality, complex metal parts.
Powder handling and storage
When it comes to powder handling and storage in 3D printing, efficiency is key. Properly handling and storing metal powder is essential to ensure the quality and consistency of the printed parts. First and foremost, it is important to have a clean and controlled environment for powder handling. Any contamination can affect the performance of the powder and compromise the final product. Additionally, proper storage conditions, such as temperature and humidity control, are crucial to prevent powder degradation. Implementing efficient powder handling and storage practices not only maximizes the efficiency of the 3D printing process but also ensures the production of high-quality parts.
Safety precautions
When it comes to working with metal powder for 3D printing, safety precautions are of utmost importance. Metal powders can be highly flammable and pose a serious risk if not handled properly. It is essential to have a well-ventilated workspace and use appropriate personal protective equipment, such as gloves and safety goggles. Additionally, it is crucial to follow manufacturer guidelines for storage, handling, and disposal of metal powders. Regular cleaning and maintenance of equipment are also necessary to prevent the buildup of powder particles, which can lead to potential hazards. By taking these safety precautions, we can ensure a safe and efficient working environment when using metal powder for 3D printing.
Optimizing Efficiency in Metal Powder 3D Printing
Process parameters optimization
Process parameters optimization is a crucial step in maximizing efficiency with metal powder for 3D printing. By fine-tuning the various parameters involved in the printing process, such as the layer thickness, printing speed, and temperature, manufacturers can achieve optimal results. The right combination of parameters can lead to improved print quality, reduced printing time, and minimized material waste. Additionally, optimizing process parameters can help enhance the mechanical properties of the printed parts, ensuring their durability and functionality. With careful analysis and experimentation, manufacturers can unlock the full potential of metal powder 3D printing and drive advancements in various industries.
Post-processing techniques
Post-processing techniques play a crucial role in maximizing efficiency with metal powder for 3D printing. After the printing process is complete, various techniques can be employed to enhance the final product. One common post-processing technique is the removal of support structures. These structures are necessary during the printing process to provide stability, but they can be time-consuming to remove manually. Therefore, automated support removal techniques, such as using water or chemical baths, are often utilized to save time and improve efficiency. Additionally, post-processing techniques can include surface finishing methods, such as polishing or sandblasting, to achieve the desired aesthetics and smoothness of the printed object. Overall, by implementing effective post-processing techniques, manufacturers can optimize the quality, functionality, and appearance of metal 3D printed parts, ultimately leading to increased efficiency in the production process.
Quality control measures
Quality control measures are essential in the process of 3D printing with metal powder. To ensure the highest level of efficiency, it is important to implement rigorous quality control procedures at every stage of the printing process. This includes carefully monitoring the quality of the metal powder used, conducting regular inspections of the 3D printer, and performing thorough testing of the printed objects. By adhering to these quality control measures, manufacturers can minimize defects, improve the overall quality of the printed products, and maximize efficiency in their 3D printing operations.
Applications and Future Trends
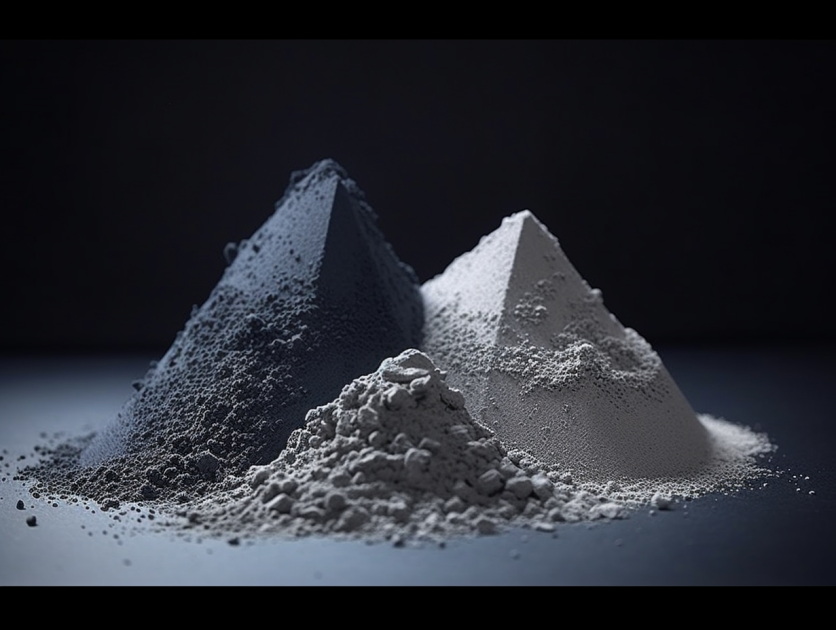
Current applications of metal powder 3D printing
Metal powder 3D printing has revolutionized various industries with its ability to fabricate complex and intricate designs. One of the current applications of metal powder 3D printing is in the aerospace industry, where it is used to create lightweight and durable components for aircraft and spacecraft. This technology has also found its way into the medical field, enabling the production of customized implants and prosthetics with enhanced strength and biocompatibility. Additionally, metal powder 3D printing is being utilized in the automotive industry to manufacture high-performance parts that improve fuel efficiency and overall vehicle performance. With its versatility and precision, metal powder 3D printing is paving the way for new possibilities in manufacturing and engineering.
Emerging trends in the field
Emerging trends in the field of metal powder for 3D printing are revolutionizing the manufacturing industry. With advancements in technology and materials, manufacturers are now able to produce complex and intricate designs with precision and efficiency. The use of metal powder in 3D printing allows for the creation of lightweight and durable parts, making it ideal for industries such as aerospace, automotive, and healthcare. Additionally, the development of new alloys and improved powder properties has opened up new possibilities for customization and enhanced performance. As the demand for high-quality, cost-effective manufacturing solutions continues to grow, the adoption of metal powder for 3D printing is expected to increase significantly in the coming years.
Potential future applications
Metal powder for 3D printing has revolutionized the manufacturing industry, allowing for the creation of complex and intricate designs with unparalleled precision. While its current applications are already impressive, the potential future applications of metal powder for 3D printing are truly groundbreaking. One such application is in the medical field, where metal powder can be used to create customized implants and prosthetics that perfectly fit a patient’s unique anatomy. Additionally, metal powder for 3D printing can be utilized in aerospace and automotive industries to produce lightweight yet durable components, improving fuel efficiency and overall performance. With ongoing advancements in material science and 3D printing technology, the possibilities for metal powder in the future are limitless, opening doors to new and exciting possibilities across various industries.