Molten Metal Deposition (MMD) is a fascinating and highly advanced additive manufacturing technology that has revolutionized the way we think about metal fabrication. It’s not just about melting metal and letting it flow; it’s about precision, control, and creating parts with intricate geometries that would be impossible to achieve through traditional manufacturing methods. So, buckle up as we dive deep into the world of MMD, exploring its intricacies, applications, and the magic it brings to the metal fabrication industry.
Overview of Molten Metal Deposition (MMD)
Molten Metal Deposition (MMD) is a type of 3D printing technology that involves the melting of metal powders and depositing them layer by layer to create a solid, three-dimensional object. This method allows for the creation of complex shapes and structures with high precision and excellent material properties. Unlike traditional manufacturing methods, which often involve cutting away material to achieve the desired shape, MMD builds up the shape from nothing, adding material only where it’s needed. This not only reduces waste but also allows for much greater design freedom.
Key Details of MMD
- Process: Involves the melting of metal powder using a high-energy heat source such as a laser or electron beam.
- Materials: Can use a wide range of metals, including titanium, aluminum, stainless steel, and more.
- Applications: Used in industries such as aerospace, automotive, medical, and manufacturing.
- Advantages: Allows for complex geometries, reduces waste, and can produce parts with excellent mechanical properties.
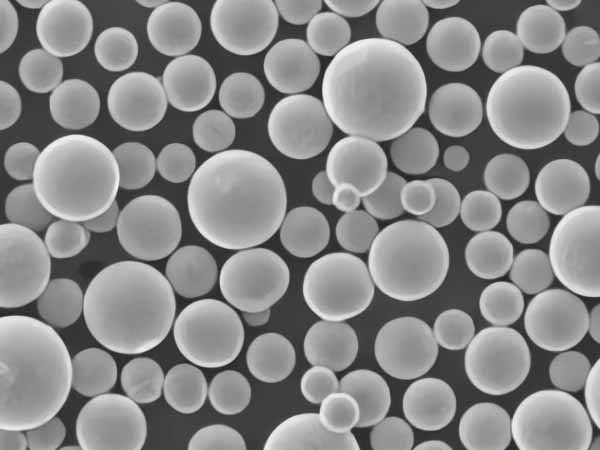
Types of Metal Powders Used in MMD
To better understand MMD, it’s essential to know the types of metal powders commonly used in this process. Here’s a table that lists some specific metal powder models, their compositions, and characteristics.
Metal Powder Model | Composition | Properties | Characteristics |
---|---|---|---|
Ti-6Al-4V | Titanium alloy (6% Aluminum, 4% Vanadium) | High strength, lightweight | Excellent corrosion resistance, used in aerospace |
AlSi10Mg | Aluminum alloy (10% Silicon, 0.3% Magnesium) | Lightweight, good thermal properties | Ideal for automotive and aerospace applications |
316L Stainless Steel | Iron, 16-18% Chromium, 10-14% Nickel | High corrosion resistance, good mechanical properties | Common in medical and food industries |
Inconel 718 | Nickel-Chromium alloy (50-55% Nickel, 17-21% Chromium) | High strength at high temperatures | Used in aerospace and gas turbines |
CuCr1Zr | Copper alloy (99.9% Copper, 0.8-1.2% Chromium, 0.06-0.15% Zirconium) | Excellent thermal and electrical conductivity | Used in electrical and thermal applications |
Maraging Steel | Iron-Nickel alloy (18% Nickel, 8-12% Cobalt) | Extremely high strength and toughness | Common in tooling and aerospace |
Hastelloy X | Nickel-based alloy (47% Nickel, 22% Chromium, 18% Iron) | Exceptional strength and oxidation resistance at high temperatures | Used in chemical and aerospace industries |
CoCrMo | Cobalt-Chromium-Molybdenum alloy | High wear resistance, excellent biocompatibility | Used in medical implants and dental applications |
NiTi (Nitinol) | Nickel-Titanium alloy (55% Nickel, 45% Titanium) | Shape memory, superelasticity | Used in medical devices and actuators |
17-4 PH Stainless Steel | Iron, 15-17% Chromium, 3-5% Nickel, 3-5% Copper | High strength, good corrosion resistance | Used in aerospace, chemical, and petrochemical industries |
Applications of Molten Metal Deposition (MMD)
Molten Metal Deposition has a wide range of applications across various industries. Here’s a table that outlines some of the key applications and uses of MMD technology.
Industry | Applications |
---|---|
Aerospace | Engine components, structural parts, complex geometries |
Automotive | Lightweight components, heat exchangers, prototype development |
Medical | Custom implants, surgical instruments, dental restorations |
Manufacturing | Tooling, molds, custom fixtures |
Energy | Turbine blades, heat exchangers, power generation components |
Defense | Armor, weapon components, custom parts |
Electronics | Heat sinks, electrical connectors, custom enclosures |
Jewelry | Custom designs, intricate patterns, rapid prototyping |
Specifications, Sizes, Grades, Standards in MMD
Different metal powders and MMD processes adhere to various specifications, sizes, grades, and standards. Here’s a comprehensive table to help you understand these parameters.
Specification/Standard | Description | Applicable Metals |
---|---|---|
ASTM F2924 | Standard specification for Ti-6Al-4V powder | Titanium alloys |
ASTM B928 | Specification for high magnesium aluminum alloys | Aluminum alloys |
ISO 5832-1 | Specification for wrought stainless steels | Stainless steel |
AMS 5662 | Aerospace material specification for Inconel 718 | Nickel alloys |
DIN 17670 | Specification for copper and copper alloys | Copper alloys |
ASTM A579 | Specification for maraging steel | Maraging steel |
AMS 5798 | Aerospace material specification for Hastelloy X | Nickel-based alloys |
ISO 5832-4 | Specification for wrought cobalt-chromium-molybdenum | Cobalt-Chromium-Molybdenum alloys |
ASTM F2063 | Specification for nickel-titanium shape memory alloys | Nickel-Titanium alloys (Nitinol) |
ASTM A564 | Specification for precipitation hardening stainless steel | 17-4 PH Stainless Steel |
Comparing Advantages and Limitations of MMD
Understanding the pros and cons of Molten Metal Deposition helps in making informed decisions about its use in various applications. Here’s a table comparing the advantages and limitations of MMD.
Aspect | Advantages | Limitations |
---|---|---|
Design Flexibility | Can create complex geometries | Requires detailed design planning |
Material Efficiency | Minimizes waste, uses material only where needed | Metal powder can be expensive |
Mechanical Properties | Produces parts with excellent strength and durability | Requires post-processing for optimal properties |
Production Speed | Rapid prototyping and short production cycles | Can be slower for large, dense parts |
Cost | Cost-effective for small batches and prototypes | High initial setup cost for equipment |
Customization | Easy to customize and produce unique parts | Limited by current technology for some metals |
Environmental Impact | Reduces material waste, lower carbon footprint | Energy-intensive process |
Quality Control | High precision and accuracy | Requires stringent quality control measures |
Suppliers and Pricing Details for MMD
If you’re looking to source metal powders and MMD services, it’s essential to know the suppliers and their pricing. Here’s a table with some details.
Supplier | Metal Powders Available | Approximate Pricing |
---|---|---|
Höganäs AB | Ti-6Al-4V, 316L, Inconel 718 | $100 – $500 per kg |
Carpenter Technology | AlSi10Mg, Maraging Steel, Hastelloy X | $150 – $600 per kg |
GKN Additive | 17-4 PH Stainless Steel, CuCr1Zr | $120 – $550 per kg |
Sandvik | CoCrMo, NiTi (Nitinol) | $200 – $700 per kg |
AP&C | Titanium alloys, Nickel-based alloys | $180 – $650 per kg |
Renishaw | Stainless steel, aluminum alloys | $130 – $500 per kg |
EOS | Various metal powders including Inconel, Titanium | $150 – $600 per kg |
LPW Technology | Specialized powders for aerospace and medical | $200 – $700 per kg |
Arcam | Titanium and cobalt-chrome powders | $180 – $650 per kg |
Advanced Powders & Coatings | High-performance alloys and custom blends | $250 – $800 per kg |
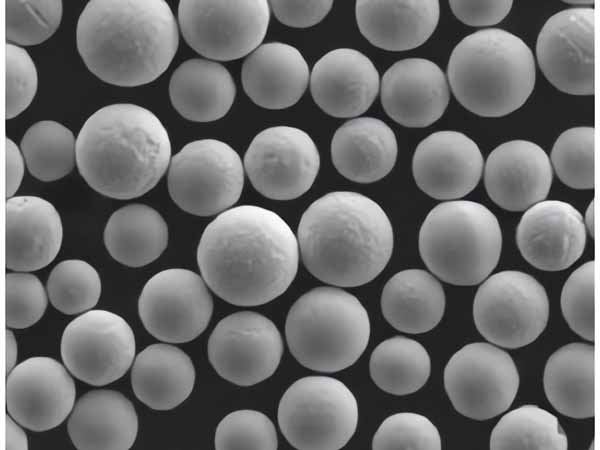
FAQs
Question | Answer |
---|---|
What is Molten Metal Deposition (MMD)? | MMD is a 3D printing technology that melts and deposits metal powders to create objects layer by layer. |
What metals can be used in MMD? | Metals like titanium, aluminum, stainless steel, nickel alloys, cobalt-chrome, and more can be used. |
What are the benefits of using MMD? | Benefits include design flexibility, material efficiency, high mechanical properties, and rapid prototyping. |
What industries use MMD technology? | Industries such as aerospace, automotive, medical, manufacturing, energy, defense, electronics, and jewelry use MMD. |
What are some limitations of MMD? | Limitations include high initial setup costs, expensive metal powders, and energy-intensive processes. |
How does MMD compare to traditional manufacturing? | MMD offers greater design freedom and material efficiency but may require more detailed planning and quality control. |
What post-processing is required for MMD parts? | Post-processing can include heat treatment, surface finishing, and machining to achieve optimal properties. |
Is MMD environmentally friendly? | MMD reduces material waste and has a lower carbon footprint compared to traditional manufacturing, but it is energy-intensive. |
Can MMD create large parts? | While MMD is excellent for small to medium-sized parts, creating large, dense parts can be time-consuming. |
How do I choose the right metal powder for MMD? | Choosing the right metal powder depends on the desired properties, application, and industry standards. |
Conclusion
Molten Metal Deposition (MMD) is an extraordinary technology that has opened new horizons in the field of metal fabrication. By understanding its process, materials, applications, and both its advantages and limitations, you can harness its potential to revolutionize your manufacturing processes. Whether you’re in aerospace, automotive, medical, or any other industry that requires precision and innovation, MMD offers a path to create complex, high-performance parts that meet the stringent demands of modern engineering.
Embrace the future of manufacturing with MMD, and unlock the possibilities of creating intricate metal parts with unparalleled precision and efficiency.