molybdenum disilicide powder is an intermetallic ceramic compound with high thermal conductivity, temperature resistance, and oxidation resistance. This guide provides an overview of MoSi2 powder properties, manufacturing methods, industry applications, and suppliers.
Introduction to molybdenum disilicide powder
Molybdenum disilicide is an inorganic chemical compound composed of molybdenum (Mo) and silicon (Si). Key properties include:
Table 1: MoSi2 powder overview
Properties | Details |
---|---|
Composition | Molybdenum – ~65% Silicon – ~35% |
Density | 6.24 g/cm3 |
Melting point | 2,630°C |
Thermal conductivity | ~100 W/m-K |
Electrical resistivity | 18-22 μΩ-cm |
Oxidation resistance | Up to ~1,650°C in air |
These attributes make MoSi2 useful for heating elements, contacts, and composites able to withstand extremely high temps under load in oxidizing environments.
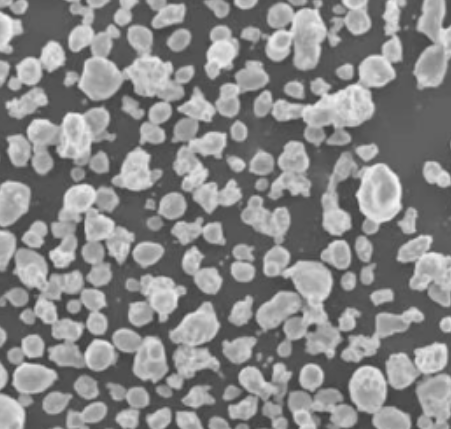
Chemical Composition and Crystal Structure
The stoichiometric chemistry of molybdenum disilicide consists of:
Table 2: MoSi2 standard composition
Element | Weight % |
---|---|
Molybdenum | ~65% |
Silicon | ~35% |
However actual composition can range from MoSi1.75 to MoSi2.2 to tailor properties. The tetragonal unit cell has a body-centered structure with Mo atoms surrounded by Si atoms.
Mechanical and Thermal Properties
Table 3: MoSi2 powder properties
Property | Value |
---|---|
Density | 6.24 g/cm3 |
Melting Point | 2,630°C |
Thermal Conductivity | ~100 W/m-K |
CTE | ~6.5 x 10-6/K |
Flexural Strength | ~340 MPa |
Compressive Strength | ~1,000 MPa |
Vickers Hardness | ~800 kgf/mm2 |
The refractory nature, oxidation resistance, thermal shock parameter, and thermal expansion coefficient make MoSi2 suitable for extreme heating element environments.
Production Processes for MoSi2 Powder
Common methods for producing MoSi2 powder include:
Table 4: MoSi2 powder production processes
Method | Description | Particle Characteristics |
---|---|---|
Self-propagating high-temperature synthesis (SHS)) | Combustion synthesis by highly exothermic redox reactions | Irregular morphology, wide distribution |
Arc-melting | Electrodes melted in water-cooled copper crucible | Spherical uniform powder |
Plasma spheroidization | Arc-melting variant with inert gas plasma | Highly spherical powder |
Silicothermic reduction | Reducing molybdenum trioxide with silicon | Agglomerated powder |
Advanced methods enable tailoring powder shape, size distribution, purity, density, and microstructure suitable for technical ceramics.
Applications of MoSi2 Powder
Thanks to its thermal and mechanical properties, molybdenum disilicide finds uses across:
Table 5: MoSi2 powder applications
Industry | Application | Components |
---|---|---|
Heating elements | High temperature furnaces, kilns, boilers | Ignitors, heating coils, plates, rods |
Electronics | Contacts, heating elements | Welding electrodes, metallizing contacts |
Coatings | Thermal spray, plasma coatings | Shields, inductors, heaters, electrodes |
Composites | Discontinuously reinforced composites with metals/ceramics | Crucibles, heat exchangers, radiant tubes |
These leverage the exceptional thermal conductivity and stability of MoSi2 for transferring and resisting heat.
MoSi2 Powder Specifications
Typical grades and specifications for molybdenum disilicide powder include:
Table 6: MoSi2 powder specifications
Parameter | Value |
---|---|
Purity | ≥ 99.5% |
Composition tolerance | MoSi1.75 – MoSi2.2 |
Particle size | 1 – 100 microns |
Morphology | Spherical, agglomerated |
Phases | α + β MoSi2, traces of Mo5Si3 |
Applications | Heating elements, contacts, composites |
Specialized variations can be produced through doping, alternative production methods, post-processing, and particle size/shape optimization.
Global Suppliers
Leading global producers of molybdenum disilicide powder include:
Table 7: Industrial MoSi2 powder manufacturers
Company | Location |
---|---|
Atlantic Equipment Engineers | United States |
Goodfellow | United Kingdom |
ESPICorp | United States |
Edgetech Industries | United States |
Stanford Advanced Materials | United States |
These offer MoSi2 powder for heating elements, contacts, and composites applications across grades, particle size distribution, and quantity.
Pricing
Molybdenum disilicide powder pricing depends on:
Table 8: MoSi2 powder price drivers
Parameter | Impact |
---|---|
Quantity | Prices decline with volume from $/g at low quantity to $/kg for bulk |
Chemistry | Tighter tolerances and higher purity grades cost more |
Size distribution | Broader ranges less expensive than tight distributions |
Shape control | Highly spherical powder costs more to produce |
In general, MoSi2 powder ranges from $50/lb to $250/lb for specialty grades optimized for additive manufacturing or thermal spray.
Pros vs Cons
Table 9: Advantages vs disadvantages of MoSi2
Pros | Cons |
---|---|
Exceptionally thermally conductive and stable | Relatively brittle with lower strength than metals |
Resists oxidation in air to 1650°C | Susceptible to hydrolysis in humid/wet environments |
Refractory with high melting point | Very high density results in heavy components |
Bio-inert – suitable for food contact | Agglomerated powder can be challenging to fully densify |
Enables high energy efficiency electromechanical systems | Limited suppliers compared with metallic materials |
With sound design principles, MoSi2 enables lighter, smaller and higher efficiency extreme temperature applications ranging from sensors and semiconductors to aerospace.
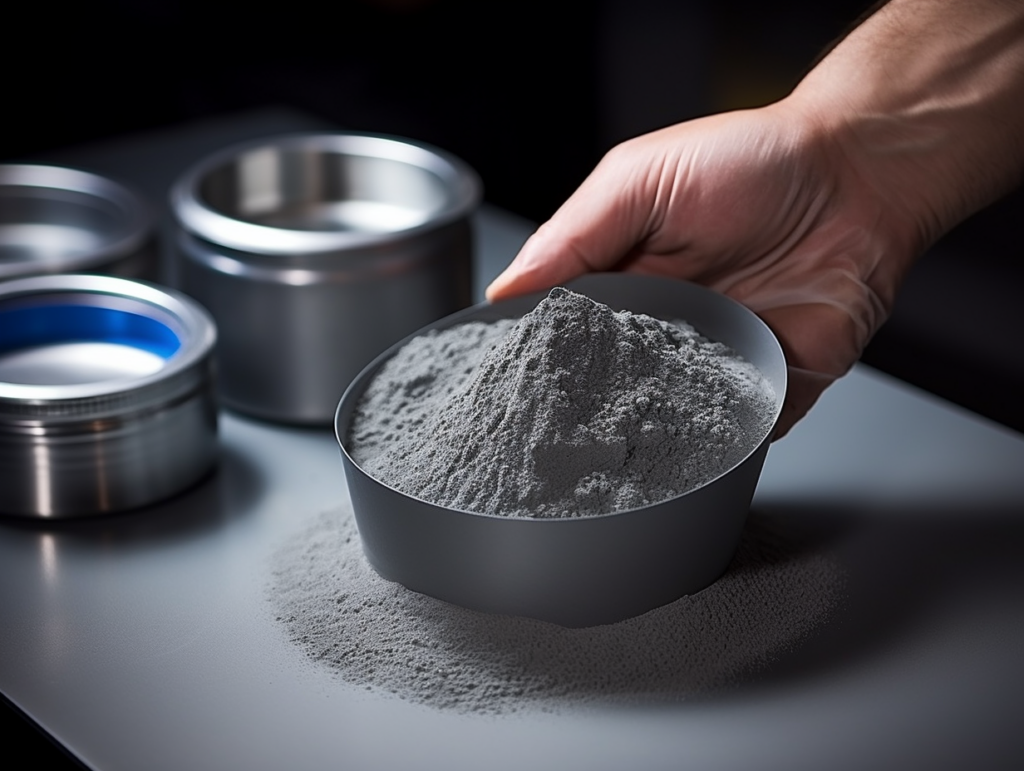
Frequently Asked Questions
Q: What is molybdenum silicide used for?
A: Thanks to outstanding thermal stability and conductivity combined with high temperature strength and creep resistance, the primary applications include heating elements, metallizing contacts, composites, and protective coatings.
Q: Is molybdenum silicide conductive?
A: Yes, molybdenum disilicide exhibits electrical resistivity ranging from 18-22 μΩ-cm, making it suitable for heating element contacts able to carry high current densities at extreme temperatures in oxidizing atmospheres.
Q: What is the difference between MoSi2 and MoS2?
A: MoSi2 (molybdenum disilicide) is an intermetallic ceramic compound composed of molybdenum and silicon whereas MoS2 (molybdenum disulfide) contains molybdenum and sulfur. They have vastly different properties, with MoS2 being a lubricant.