Molybdenum powder is a unique material with diverse applications in various industries. This guide provides a detailed overview of molybdenum powder including its properties, production methods, applications, pricing, and leading global suppliers.
Introduction to Molybdenum Powder
Molybdenum powder is a fine particulate form of molybdenum metal. Key features of molybdenum powder include:
- Pure molybdenum or molybdenum alloys
- Available in various particle sizes and morphologies
- Exhibits high strength, thermal/electrical conductivity, and corrosion resistance
- Used as an alloying additive, catalyst, conductor, and more
- Produced through processes like hydrogen reduction, thermal decomposition, electrolysis, etc.
- Supplied by major metal powder manufacturers globally
Molybdenum powder enhances the properties of steels and alloys. It also serves critical functions across electronics, chemicals, lubricants, and other sectors. This guide provides a detailed overview of molybdenum powder types, production, properties, applications, pricing, and leading suppliers.
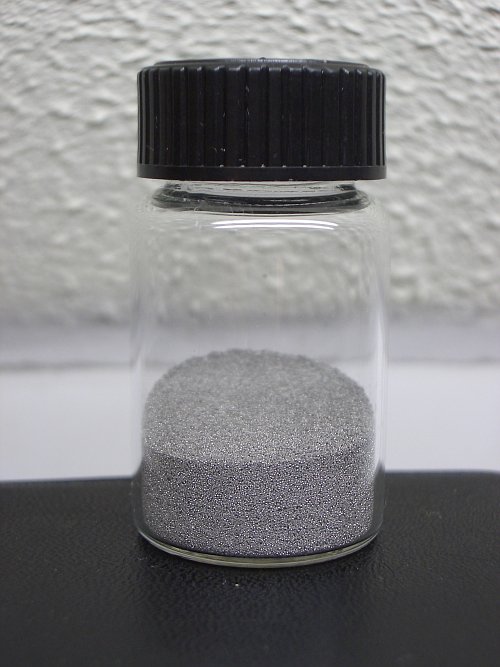
Types of Molybdenum Powder
Molybdenum powder is classified into different types based on composition, particle characteristics, production method, and applications:
Molybdenum Powder Types
Type | Description |
---|---|
Pure molybdenum | Over 99% Mo, impurities like C, O, N |
Molybdenum alloys | Mo with W, Re, Ti, Zr, C, Si, B, etc. |
Oxide molybdenum | MoO3 powder |
Spherical molybdenum | Near-spherical morphology |
Molybdenum nanopowder | Particles under 100 nm |
Electrodeposited molybdenum | Smooth morphology from electrolytic process |
Segmented molybdenum | Angular, irregular particles |
Thermally sprayed molybdenum | Roughed surface, porous structure |
- Pure molybdenum powder with over 99% Mo purity is most common.
- Alloying elements are added to tailor properties like strength, hardness, electrical resistivity, etc.
- Oxide molybdenum powder is used for pigments and other chemical applications.
- Spherical powder features smooth morphology for applications like metal AM.
- Nanopowders below 100 nm size enhance properties significantly.
- Different production processes yield powder with varying particle characteristics optimal for certain uses.
Production Methods for Molybdenum Powder
Some key industrial techniques used to produce molybdenum powder include:
Molybdenum Powder Production Methods
Method | Description |
---|---|
Hydrogen reduction | Reduction of MoO3 using hydrogen gas at 700°C |
Thermal decomposition | MoO3 heated to over 850°C in H2 atmosphere |
Electrolysis | Electrolytic process using aqueous solution of ammonium molybdate |
Atomization | Melted molybdenum atomized by gas or water |
Plasma rotating electrode process (PREP) | Rotating electrode in plasma arc to produce spherical powder |
Ball milling | Mechanical milling of molybdenum into powder |
- Hydrogen reduction of molybdenum trioxide is a common production route.
- Thermal decomposition in a hydrogen atmosphere also efficiently generates molybdenum powder.
- Electrolysis and atomization offer high purity powder. Plasma processing enables spherical morphologies.
- Mechanical milling methods like ball milling can comminute molybdenum material into powder.
- Secondary steps like screening, annealing, coating, compaction, etc. are used to achieve powder specifications.
- Alloying is done by mixing elemental or master alloy powders in correct proportions.
Properties of Molybdenum Powder
Molybdenum powder exhibits a unique combination of properties making it suitable for high performance applications:
Molybdenum Powder Properties
Property | Value |
---|---|
Density | 10.22 g/cm3 |
Melting point | 2623°C |
Electrical resistivity | 5.2 μΩ-cm at 20°C |
Thermal conductivity | 138 W/mK at 20°C |
CTE | 4.8 x 10-6 /K at 20°C |
Modulus of elasticity | 329 GPa |
Tensile strength | 620-1400 MPa |
Poisson’s ratio | 0.31 |
Maximum service temperature in air | 870°C |
- High density but relatively lightweight compared to other refractory metals.
- Exceptionally high melting point.
- High electrical and thermal conductivity.
- Low coefficient of thermal expansion.
- Good strength and stiffness properties.
- Alloying improves certain characteristics for target applications.
- Particle size and shape also affect the final powder’s properties and performance.
Applications of Molybdenum Powder
Thanks to its versatile material properties, molybdenum powder finds uses across the following key industries:
Molybdenum Powder Applications
Industry | Uses |
---|---|
Metallurgy | Alloying element in steels, superalloys, sputtering targets |
Electronics | Conductive coatings, thermal management, grids, contacts |
Chemicals | Catalysts for petroleum, polymers, ammonia production |
Lubricants | Solid lubricant, molybdenum disulfide coatings |
Aerospace | Rocket nozzles, turbine blades, lightweight alloys |
Defense | Armor materials, gun barrels, lubricants |
Medical | Radiation shields, implants, dental alloys |
- Steelmaking: Molybdenum enhances strength, hardness, toughness, and corrosion resistance in steels.
- Electronics: Molybdenum pastes are used in circuits and solar cells. Its thermal conductivity aids heat dissipation.
- Catalysts: Molybdenum compounds act as efficient catalysts in key industrial processes like hydrotreating and others.
- Coatings: Molybdenum disulfide coatings impart dry lubrication. Oxide coatings provide corrosion protection.
- Lightweighting: Molybdenum alloys with reduced density are used in aerospace components.
- Radiation shielding: Molybdenum’s high density shields against X-rays and gamma rays in medical and scientific applications.
Global Suppliers of Molybdenum Powder
Some of the major global producers and suppliers of molybdenum powder include:
Molybdenum Powder Manufacturers
Company | Location |
---|---|
H.C. Starck | Germany |
Molymet | Chile |
JDC Molybdenum | China |
Naei Shimizu | Japan |
Midwest Tungsten | USA |
Plansee | Austria |
Exploiter Molybdenum | China |
China Molybdenum Co. Ltd. | China |
Tritrust Industrial | China |
- Leading molybdenum mining and processing companies have large-scale powder manufacturing capabilities.
- Specialty metals companies also produce various grades of molybdenum and alloy powders.
- High purity spherical and nanoscale powder is offered for electronics and other critical applications.
- Powders can be customized in terms of composition, particle size and shape, coatings, etc.
- Major global suppliers have a global presence and distribution networks.
Cost Analysis of Molybdenum Powder
Molybdenum powder is considerably more expensive than iron or nickel powder. Prices depend on:
Cost Drivers for Molybdenum Powder
- Purity levels
- Particle characteristics
- Purchase volume
- Production process
- Supplier margins
- Raw molybdenum costs
- Location factors
Molybdenum Powder Price Ranges
Type | Price Range |
---|---|
Pure molybdenum, standard grade | $25-60 per kg |
High purity molybdenum | $80-150 per kg |
Molybdenum alloys | $30-100 per kg |
Nanoscale molybdenum | $100-500 per kg |
- Higher purity grades for critical applications are more expensive.
- Smaller particle sizes and spherical morphology command a premium.
- Molybdenum alloy prices depend on the alloying elements.
- Large volume purchases can significantly lower cost through discounts.
- Location factors like transportation and import duties affect price.
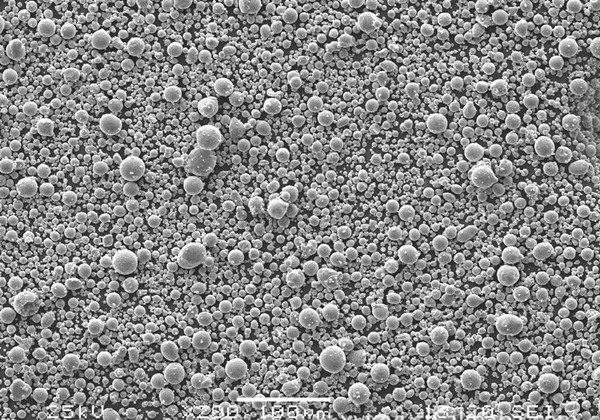
Standards and Certifications
Molybdenum powder compositions, quality, and production facilities must meet various international standards:
- ASTM B331: Standard Specification for Molybdenum Powders and Products
- ISO 28927: Molybdenum powders for thermal spraying
- AMS 7451: Molybdenum powder types for thermal spray coatings
- ASTM B839: Standard test methods for molybdenum powder
- ISO 9001: Quality management system for producers
- REACH, RoHS: Compliance for use in EU
Key considerations for purchasing:
- Reputable suppliers testing powder to ASTM/ISO standards
- Mill certificates validating composition, lot tests
- ISO 9001 certification of supplier facilities
- Industry-specific certifications may be required
Molybdenum vs. Tungsten Powder Comparison
Molybdenum Powder vs. Tungsten Powder
Parameter | Molybdenum Powder | Tungsten Powder |
---|---|---|
Density | 10.22 g/cm3 | 19.25 g/cm3 |
Melting point | 2623°C | 3422°C |
Strength | Moderate | Very high |
Thermal conductivity | 138 W/mK | 173 W/mK |
Electrical resistivity | 5.2 μΩ-cm | 5.5 μΩ-cm |
Cost | Moderate | High |
Toxicity | Low | Moderate |
Oxidation resistance | Good | Poor |
- Tungsten has higher density, melting point, strength, and conductivity but is more expensive.
- Molybdenum offers a better combination of cost, conductivity, and workability.
- Molybdenum powders have lower toxicity concerns during handling and processing.
- Molybdenum demonstrates better oxidation resistance compared to tungsten.
- Uses can overlap in alloys, heating elements, contacts, and other applications.
Key Takeaways on Molybdenum Powder
- Molybdenum powder provides high strength, thermal conductivity, temperature resistance, and corrosion resistance.
- Major production routes are hydrogen reduction, thermal decomposition, electrolysis, and atomization.
- It serves critical functions as an alloying additive, catalyst, conductor, and sputtering material.
- Electronics, chemicals, metallurgy, and energy are major application areas.
- Leading mining companies and specialty powder producers supply various grades.
- Pricing ranges from $25-500/kg based on purity, particle size, volumes, etc.
- Meeting standardized specifications ensures the powder’s suitability for intended uses.
FAQs
Q: What is molybdenum powder used for?
A: The main uses are as an alloying agent in steels, in electronics for conductivity, as catalysts in chemical production, lubricants/coatings, and in aerospace & medical sectors.
Q: What are the advantages of molybdenum powder?
A: Key advantages are high strength, thermal/electrical conductivity, corrosion resistance, high temperature stability, low thermal expansion, and ability to enhance alloy properties.
Q: Is molybdenum powder toxic?
A: Molybdenum metal powder has low toxicity levels. But precautions should be taken during handling and processing to minimize exposure. Mo compounds can have higher toxicity.
Q: What is the difference between molybdenum and tungsten powder?
A: Tungsten has higher density, strength, and melting point whereas molybdenum offers better oxidation resistance and lower cost. Their conductivity and uses overlap in many applications.
Q: How is molybdenum powder made?
A: Major production methods are hydrogen reduction of molybdenum trioxide, thermal decomposition, electrolysis, and atomization. Alloying, milling, and heat treatment can further tailor the powder.
Q: Is molybdenum powder magnetic?
A: Molybdenum is generally non-magnetic in its pure form. But some molybdenum alloys demonstrate ferromagnetic behavior depending on composition and processing.
Q: What particle size is molybdenum powder available in?
A: Molybdenum powder can range from coarse size of 10-150 microns down to ultrafine nanopowder under 100 nm. Finer powder provides more uniform properties.
Q: What are some molybdenum powder alloys?
A: Common alloys include Mo-Re, Mo-W, Mo-Ti, Mo-Zr, Mo-Si-B, Mo-TiB2, and others. Alloying elements enhance strength, hardness, ductility, and other properties.
Q: Does molybdenum powder oxidize quickly?
A: Molybdenum has good oxidation resistance up to around 500°C. But fine powder can oxidize faster and may require inert storage. Annealing can reduce oxidation.
Q: What standards apply to molybdenum powder?
A: Key standards are ASTM B331, ISO 28927, AMS 7451, ASTM B839, ISO 9001, REACH, and RoHS. These cover composition, quality, testing procedures, certifications, and regulatory compliance.