Multi-material structures represent an exciting frontier in engineering and manufacturing. By integrating different materials within a single structure, these innovative designs unlock new possibilities in terms of strength, flexibility, and functionality. But what exactly are multi-material structures, and why should you care? Let’s dive into this fascinating topic.
Overview of Multi-Material Structures
Multi-material structures combine two or more distinct materials to leverage their individual strengths while compensating for their weaknesses. This approach allows engineers to design components that are lighter, stronger, more durable, and more versatile than those made from a single material.
Why Multi-Material Structures?
Imagine having the strength of steel with the lightweight properties of aluminum, or the flexibility of plastic with the durability of carbon fiber. Multi-material structures offer these benefits by merging different materials into a cohesive unit, leading to:
- Enhanced Performance: Combining materials to optimize performance.
- Cost Efficiency: Reducing costs by using less expensive materials in non-critical areas.
- Innovative Designs: Enabling new design possibilities that single-material solutions can’t achieve.
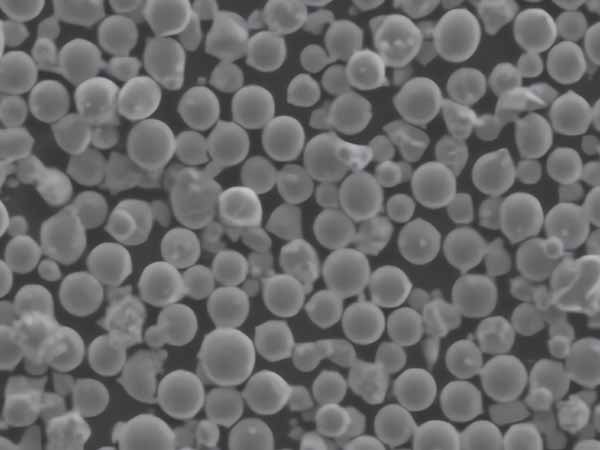
Types, Composition, and Characteristics of Multi-Material Structures
Types of Multi-Material Structures
Different combinations of materials can be used to create multi-material structures. Here’s a breakdown of some common types:
Type | Composition | Properties |
---|---|---|
Metal-Metal | Steel + Aluminum | High strength, reduced weight |
Metal-Polymer | Titanium + Plastic | Corrosion resistance, improved flexibility |
Metal-Ceramic | Aluminum + Ceramic | High temperature resistance, durability |
Polymer-Ceramic | Plastic + Ceramic | Electrical insulation, thermal stability |
Composite-Metal | Carbon Fiber + Aluminum | High strength-to-weight ratio, stiffness |
Characteristics of Multi-Material Structures
Multi-material structures exhibit a unique set of characteristics derived from their composite nature. These include:
- Strength and Durability: Enhanced load-bearing capacity.
- Weight Reduction: Lighter than traditional materials.
- Corrosion Resistance: Improved longevity in harsh environments.
- Thermal and Electrical Conductivity: Tailored properties for specific applications.
- Cost-Effectiveness: Efficient use of expensive materials.
Applications of Multi-Material Structures
Multi-material structures are transforming various industries. Here’s how they’re being used:
Industry | Application | Benefits |
---|---|---|
Automotive | Car Bodies, Chassis | Weight reduction, improved fuel efficiency |
Aerospace | Aircraft Fuselages, Wings | Increased strength, reduced weight |
Construction | Structural Components | Enhanced durability, cost savings |
Electronics | Circuit Boards, Casings | Improved thermal management, miniaturization |
Medical | Implants, Prosthetics | Biocompatibility, tailored mechanical properties |
Specific Metal Powder Models for Multi-Material Structures
In the realm of multi-material structures, specific metal powder models play a crucial role. Here are some notable examples:
- Ti-6Al-4V: A titanium alloy known for its high strength and excellent corrosion resistance, widely used in aerospace and medical applications.
- 316L Stainless Steel: Offers exceptional corrosion resistance and good mechanical properties, ideal for marine and chemical environments.
- Inconel 718: A nickel-chromium alloy with outstanding high-temperature strength and corrosion resistance, perfect for aerospace and gas turbines.
- AlSi10Mg: An aluminum alloy that combines good strength, hardness, and thermal conductivity, commonly used in automotive and aerospace industries.
- Maraging Steel: Known for its high strength and toughness, used in tooling and high-performance engineering applications.
- CoCrMo: A cobalt-chromium-molybdenum alloy with excellent wear resistance and biocompatibility, often used in medical implants.
- NiTi (Nitinol): A nickel-titanium alloy famous for its shape memory and superelasticity, used in medical devices and actuators.
- Hastelloy X: A nickel-based superalloy with excellent high-temperature strength and oxidation resistance, used in aerospace and industrial applications.
- CuCrZr: A copper-chromium-zirconium alloy that combines good electrical and thermal conductivity with high strength, used in electrical components and welding electrodes.
- Tool Steel (H13): Known for its high toughness, hardness, and wear resistance, used in die casting and extrusion tools.
Composition of Multi-Material Structures
Materials Used in Multi-Material Structures
Material | Composition | Primary Use |
---|---|---|
Titanium Alloys | Ti-6Al-4V, Ti-5Al-2.5Sn | Aerospace, Medical Implants |
Aluminum Alloys | AlSi10Mg, 7075 Aluminum | Automotive, Aerospace |
Stainless Steels | 316L, 304 Stainless Steel | Marine, Chemical Processing |
Nickel Alloys | Inconel 718, Hastelloy X | High-Temperature Applications |
Cobalt Alloys | CoCrMo | Medical Devices |
Copper Alloys | CuCrZr, Bronze | Electrical Components, Heat Exchangers |
Polymer Composites | Carbon Fiber Reinforced Polymers | Sports Equipment, Aerospace |
Ceramics | Zirconia, Alumina | Cutting Tools, Biomedical Applications |
Characteristics of Specific Metal Powder Models
Model | Composition | Properties |
---|---|---|
Ti-6Al-4V | 90% Titanium, 6% Aluminum, 4% Vanadium | High strength, corrosion resistance |
316L | 16% Chromium, 10% Nickel, 2% Molybdenum | Excellent corrosion resistance |
Inconel 718 | 50-55% Nickel, 17-21% Chromium | High-temperature strength, oxidation resistance |
AlSi10Mg | 90% Aluminum, 10% Silicon, 0.5% Magnesium | Good strength, thermal conductivity |
Maraging Steel | 18% Nickel, 8% Cobalt, 5% Molybdenum | High strength, toughness |
CoCrMo | 60% Cobalt, 27% Chromium, 5% Molybdenum | Wear resistance, biocompatibility |
NiTi | 55% Nickel, 45% Titanium | Shape memory, superelasticity |
Hastelloy X | 47% Nickel, 22% Chromium, 18% Iron | High-temperature strength, oxidation resistance |
CuCrZr | 98% Copper, 1.5% Chromium, 0.5% Zirconium | Electrical and thermal conductivity |
Tool Steel H13 | 0.4% Carbon, 5% Chromium, 1.5% Molybdenum | High toughness, hardness |
Advantages of Multi-Material Structures
Enhanced Performance
Multi-material structures can significantly enhance performance by combining the best attributes of different materials. For instance, using carbon fiber composites with aluminum can provide high strength and reduced weight, which is crucial for aerospace applications where every gram matters.
Cost Efficiency
By strategically using expensive materials only where necessary, multi-material structures can be more cost-effective. For example, in automotive manufacturing, using lightweight materials in the car’s body can reduce fuel consumption and, ultimately, operational costs.
Innovative Designs
The ability to combine materials opens up new design possibilities that were previously unattainable with single-material solutions. Engineers can now create complex shapes and structures that are optimized for performance, weight, and cost.
Disadvantages of Multi-Material Structures
Complex Manufacturing Processes
Creating multi-material structures often involves complex manufacturing processes that require advanced technology and expertise. This can increase production time and costs.
Compatibility Issues
Different materials have different properties, such as thermal expansion rates, which can lead to compatibility issues. Ensuring that materials work well together requires careful selection and engineering.
Recycling Challenges
Recycling multi-material structures can be more challenging compared to single-material products. Separating the different materials for recycling can be time-consuming and expensive.
Applications and Uses of Multi-Material Structures
Automotive Industry
In the automotive industry, multi-material structures are used to create lighter, stronger, and more fuel-efficient vehicles. For example, combining aluminum and high-strength steel in car bodies and chassis can significantly reduce weight while maintaining safety and performance standards.
Aerospace Industry
The aerospace industry benefits greatly from multi-material structures, where weight reduction is crucial. Using carbon fiber composites with metals like titanium and aluminum allows for the construction of lighter and more durable aircraft components, leading to better fuel efficiency and lower emissions.
Construction Industry
In construction, multi-material structures are used to build more resilient and durable structures. Combining concrete with steel reinforcements can create buildings that are not only strong but
also resistant to environmental stresses like earthquakes and high winds.
Electronics Industry
Multi-material structures are also prevalent in the electronics industry. Using materials like aluminum and polymers can improve thermal management in electronic devices, leading to better performance and longevity.
Medical Industry
In the medical field, multi-material structures are used to create implants and prosthetics that are biocompatible, strong, and lightweight. Combining materials like titanium and polymers ensures that these medical devices are both durable and comfortable for patients.
Specifications, Sizes, Grades, and Standards
Specifications and Sizes
Material | Common Sizes | Grade |
---|---|---|
Ti-6Al-4V | Sheets, rods, bars (0.5mm to 100mm) | Grade 5 |
316L | Sheets, tubes, wires (0.5mm to 50mm) | ASTM F138 |
Inconel 718 | Rods, bars, plates (1mm to 200mm) | AMS 5662 |
AlSi10Mg | Powder, sheets, rods (0.2mm to 50mm) | ISO 3522 |
Maraging Steel | Rods, bars, sheets (1mm to 150mm) | AMS 6512 |
CoCrMo | Rods, bars, plates (1mm to 100mm) | ASTM F75 |
NiTi | Sheets, wires, rods (0.1mm to 20mm) | ASTM F2063 |
Hastelloy X | Sheets, rods, bars (1mm to 100mm) | ASTM B435 |
CuCrZr | Rods, bars, sheets (1mm to 100mm) | RWMA Class 2 |
Tool Steel H13 | Rods, bars, plates (1mm to 100mm) | ASTM A681 |
Standards
Material | Standard |
---|---|
Ti-6Al-4V | ASTM B348, AMS 4928 |
316L | ASTM A240, ASTM A276 |
Inconel 718 | AMS 5662, AMS 5663 |
AlSi10Mg | ISO 3522, DIN 1725 |
Maraging Steel | AMS 6512, MIL-S-46850 |
CoCrMo | ASTM F75, ISO 5832-12 |
NiTi | ASTM F2063, ISO 5832-8 |
Hastelloy X | ASTM B435, AMS 5536 |
CuCrZr | RWMA Class 2, EN 12163 |
Tool Steel H13 | ASTM A681, SAE J438 |
Suppliers and Pricing Details
Key Suppliers
Supplier | Materials Offered | Contact Information |
---|---|---|
Advanced Powders | Ti-6Al-4V, Inconel 718, Maraging Steel | www.advancedpowders.com |
Metal Suppliers | 316L, Hastelloy X, Tool Steel H13 | www.metalsuppliers.com |
Alloy Tech | AlSi10Mg, CuCrZr, CoCrMo | www.alloytech.com |
Precision Metals | NiTi, Stainless Steels | www.precisionmetals.com |
Pricing Details
Material | Average Price per kg |
---|---|
Ti-6Al-4V | $100 – $150 |
316L | $20 – $30 |
Inconel 718 | $50 – $100 |
AlSi10Mg | $30 – $40 |
Maraging Steel | $60 – $120 |
CoCrMo | $80 – $150 |
NiTi | $100 – $200 |
Hastelloy X | $60 – $110 |
CuCrZr | $20 – $40 |
Tool Steel H13 | $30 – $50 |
Pros and Cons of Multi-Material Structures
Advantages
Advantage | Description |
---|---|
Enhanced Performance | Combining materials to optimize strength, flexibility, and durability |
Weight Reduction | Using lighter materials to reduce overall weight |
Cost Efficiency | Strategic use of materials to minimize costs |
Design Flexibility | Enabling complex shapes and innovative designs |
Improved Properties | Tailoring thermal, electrical, and mechanical properties |
Disadvantages
Disadvantage | Description |
---|---|
Complex Manufacturing | Requires advanced technology and expertise |
Compatibility Issues | Different properties can lead to material incompatibility |
Recycling Challenges | Difficult to separate materials for recycling |
Higher Initial Costs | Advanced manufacturing processes can be expensive |
Maintenance and Repair | May require specialized knowledge and tools |
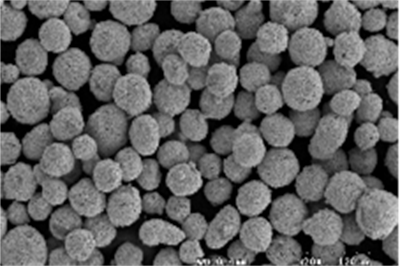
FAQs
Question | Answer |
---|---|
What are multi-material structures? | Structures combining two or more materials to optimize performance. |
Why use multi-material structures? | To enhance strength, reduce weight, and improve overall performance. |
What industries use multi-material structures? | Automotive, aerospace, construction, electronics, and medical. |
What are some common materials used? | Titanium, aluminum, stainless steel, polymers, ceramics, and composites. |
What are the benefits? | Improved strength, reduced weight, cost efficiency, and design flexibility. |
What are the challenges? | Complex manufacturing, material compatibility, and recycling difficulties. |
How are multi-material structures made? | Through advanced manufacturing techniques like additive manufacturing and bonding. |
Can multi-material structures be recycled? | Yes, but the process can be more challenging compared to single-material products. |
What is the future of multi-material structures? | Continued innovation in materials and manufacturing processes will drive adoption. |
Are multi-material structures expensive? | Initial costs can be higher, but long-term benefits often justify the investment. |
Conclusion
Multi-material structures are transforming the way we design and manufacture products across various industries. By combining different materials, engineers can create structures that are lighter, stronger, and more cost-effective than ever before. Despite the challenges, the benefits of multi-material structures make them an exciting area of innovation and development. Whether in automotive, aerospace, construction, electronics, or medical fields, these advanced structures are paving the way for a more efficient and sustainable future.