Nickel alloys offer excellent corrosion resistance, heat resistance, and mechanical properties. This makes them suitable for additive manufacturing of complex components exposed to extreme environments. This article provides an overview of key nickel alloy powder grades, properties, applications, specifications, and suppliers.
Overview of nickel alloys powder
Nickel alloy powders can be used to print intricate metal parts with properties unmatched by other materials using powder bed fusion or directed energy deposition processes.
Alloy systems: Ni-based superalloys, stainless steels, alloy steels, nickel copper alloys, nickel cobalt alloys, and nickel titanium shape memory alloys.
Powder production: Mainly gas atomized with some plasma atomization; spherical morphology and controlled size distribution.
Powder sizes: From 15 microns to 150 microns depending on alloy; finer sizes for better resolution.
Key properties: Heat resistance, corrosion resistance, wear resistance, strength at high temperatures.
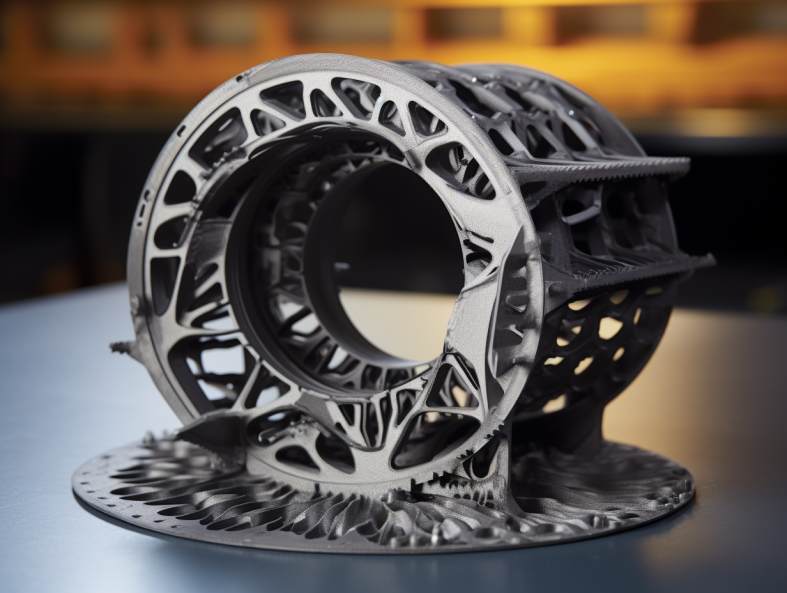
Composition and Microstructure
Nickel alloy chemistry, phases present, defects formed during printing, and microstructural features determine properties.
Common nickel alloys
Alloy | Nickel | Chromium | Iron | Niobium | Molybdenum | Aluminum + Titanium | Carbon |
---|---|---|---|---|---|---|---|
Inconel 718 | 50-55% | 17-21% | Bal. | 4.75-5.5% | 2.8-3.3% | 0.65-1.15% | 0.04% max |
Inconel 625 | 58% min | 20-23% | 2% max | 3.15-4.15% | 8-10% | 0.4% max | 0.1% max |
Hastelloy X | Bal. | 21-25% | 18% max | – | 8-10% | 0.3-1.0% | 0.15% max |
Microstructure: Mix of gamma nickel FCC matrix and carbide, boride, or intermetallic precipitates. Cooling rate affects grain size and precipitates.
Porosity and cracks: Process-induced lack of fusion defects degrade properties and fatigue resistance. Hot isostatic pressing (HIP) helps reduce porosity in nickel alloys.
Properties and Performance
Nickel alloy parts properties depend on composition, AM process variables, build orientation, heat treatment, HIP and testing direction.
Physical properties
Alloy | Density (g/cc) | Melting point (°C) | Thermal conductivity (W/m-K) | Coeff. of thermal expansion (10-6/K) |
---|---|---|---|---|
Inconel 718 | 8.19 | 1260-1336 | 11.4 | 13.0 |
Inconel 625 | 8.44 | 1260-1350 | 9.8 | 13.1 |
Haynes 282 | 8.24 | 1310-1375 | 11.1 | 13.3 |
Mechanical properties
Alloy | Yield strength (MPa) | Tensile strength (MPa) | Elongation (%) | Hardness (HRC) |
---|---|---|---|---|
As-printed Inconel 718 | 500-900 | 900-1200 | 10-25 | 30-45 |
HIP Inconel 718 | 690-830 | 1035-1240 | 12-22 | 36-43 |
As-printed Hastelloy X | 450-650 | 760-900 | 30-35 | 25-35 |
Haynes 282 | 485-550 | 860-1030 | 25-40 | 30-36 |
High temperature properties: Excellent creep rupture, stress rupture, oxidation and hot corrosion resistance up to 700°C for nickel superalloys.
Applications of Nickel Alloy Additive Manufacturing
Unique geometries and properties expand uses for 3D printed nickel alloy components.
Aerospace: Turbine blades, combustors, thrust chambers
Oil and gas: Wellhead valves, subsea manifolds, separators
Nuclear: Reactor vessels and internals exposed to high temperatures, pressure and irradiation
Automotive: Turbocharger wheels and housings, supercharger rotors, fuel injector nozzles
Chemical: Pumps, valves, heat exchanger tubes, reaction vessels corrosion resistance
Tooling: Conformal cooling channels integrated into injection molds for plastics
Food and pharmaceutical: Hoppers, conveyors compatible with CIP/SIP and industry hygiene standards
Popular Nickel Alloy Powder Grades
Alloy | Printability | Corrosion Resistance | Heat Resistance | Cost |
---|---|---|---|---|
Inconel 718 | Excellent | Moderate | Excellent | High |
Inconel 625 | Very good | Excellent | Very good | Very high |
Hastelloy X | Moderate | Excellent | Excellent | High |
Haynes 282 | Good | Moderate | Excellent | Moderate |
17-4PH Stainless | Excellent | Moderate | Moderate | Low |
Specifications
Stringent quality standards enforced for aerospace, nuclear and food contact compliance.
Powder specifications
Parameter | Requirement | Test method |
---|---|---|
Particle size distribution | 15-100 μm for EBM; 5-45 μm for SLM | Laser diffraction |
Apparent density | ≥ 3 g/cc | Hall flowmeter |
Tap density | ≥ 4 g/cc | Tap density tester |
Flow rate | 15-25 s/50g | Hall flowmeter |
Composition | Certified COA | GDMS, ICP-OES |
Part qualification standards
Industry | Standard |
---|---|
Aerospace | AMS7000, ASTM F3056 |
Nuclear | ASME Section III Subsection NG |
Food | ASME BPE-2022 |
Medical | ISO 13485, ASTM F3122 |
Design Rules in Nickel Alloys AM
Optimize designs to fully exploit benefits of AM with nickel alloys.
- Reduce weight with lattices and thin walls
- Conformal cooling channels in tools
- Allow for HIP capsule access
- Minimize trapped powder
- Optimize support structures
- Accommodate stresses from rapid solidification
- Account for thermal distortion and warpage
Suppliers
Leading providers of nickel alloy powders for additive manufacturing.
Supplier | Materials Offered | Size Range (μm) |
---|---|---|
Carpenter Additive | IN625, IN718, Custom Age 625Plus®, 17-4PH, more | 10-105 |
Sandvik | Osprey® IN, NO, NB alloys | 5-150 |
Praxair | IN718, IN625, HX, Custom Alloys | 15-45 |
AP&C | IN625, IN718, IN713, Custom Alloys | 15-53 |
LPW Technology | IN718, CM247LC, Haynes 282® | 15-45 |
Cost: ~$100-$300 per kg for nickel alloy powders depending on order quantity, composition, size distribution and other requirements.
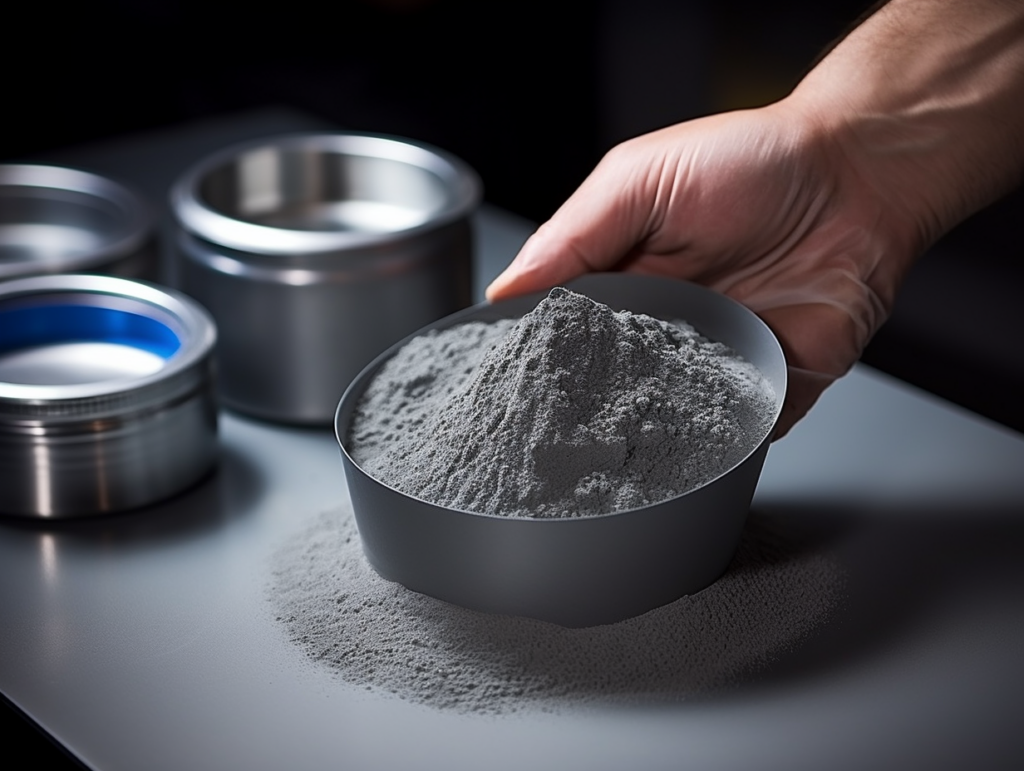
FAQs
Q: Why choose laser powder bed fusion over directed energy deposition for nickel alloys?
A: L-PBF methods like SLM and EBM offer better resolution, higher density, finer surface finish, and more precise metallurgy than DED which has higher build rates but poorer quality.
Q: Which heat treatment is used for additively manufactured nickel superalloys?
A: For Inconel 718, a standard aging treatment involves heating to 720°C, holding for 8 hours, then air cooling to precipitation harden the alloy with gamma prime and gamma double prime phases.
Q: Can all nickel alloys be easily 3D printed?
A: Alloys like nickel-titanium shape memory alloys present challenges due to their susceptibility to oxidation and complex solid-state phase transformations during printing. Special atmospheres or parameter modification is needed.
Q: How to minimize cracking in AM nickel alloy parts?
A: Carefully controlling the thermal gradient direction and peak temperatures reduces hot tearing. Using preheated platforms also lowers thermal stresses. Optimizing scan strategy helps if microcracks form from stresses between deposited layers.
Q: Which post-processing method gives the best surface finish on nickel alloy AM components?
A: Automated drag finishing gives Ra values under 0.4 microns while manual hand polishing allows intricate features or internal channels to be smoothed depending on accessibility needs. Anodizing can also improve surface finish. Match post-process method to application.