Overview
Niobium powder is a refractory metal material valued for its unique combination of physical, chemical, and electrical properties. Also known as columbium, niobium offers excellent heat resistance, corrosion resistance, superconductivity at low temperatures, and stability in harsh environments.
As a powder, niobium facilitates fabrication of components via processes like metal injection molding, hot isostatic pressing, additive manufacturing, thermal spraying, and powder metallurgy pressing and sintering. Key applications include superconducting magnets, high-performance alloys, electronic devices, aerospace and defense components, chemical processors, and medical implants.
This guide provides a detailed overview of niobium powder, including production methods, compositions, characteristics, properties, specifications, applications, pricing, and major global suppliers. It also includes multiple tables summarizing key parameters to help engineers, product designers, and researchers understand niobium powder materials and select appropriate grades.
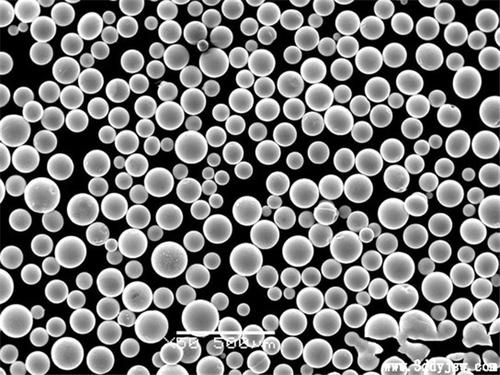
Production of Niobium Powder
Commercial production of niobium powder relies on extracting niobium ore minerals followed by chemical conversion processes to obtain niobium in powder form.
Niobium Powder Production Methods
- Extraction – Niobium ores are mined and concentrated through flotation to produce pyrochlore or columbite mineral concentrates.
- Conversion – Concentrates are chemically converted to crude niobium oxide or other niobium intermediates.
- Purification – Multiple processes applied to remove impurities from niobium chemical intermediates.
- Reduction – Niobium oxides/salts reduced with hydrogen, carbon, or metals to produce niobium metal powder.
- Condensation – Vaporized niobium metal condensed into fine spherical powders.
- Milling – Coarse niobium crushed into fine irregular powder particles.
Key production stages focus on removing impurities like tantalum, tungsten, iron, and other metals present in natural ores. This yields pure niobium powder suitable for advanced applications.
Types of Niobium Powder
Niobium powder is available in various compositions and morphologies to suit different fabrication processes and end-use requirements.
Niobium Powder Types
Type | Description | Particle Shape | Common Uses |
---|---|---|---|
Pure niobium | 99.8-99.99% niobium content | Spherical, irregular | Alloys, superconductors |
Niobium hydride | NbH2, niobium with atomic hydrogen | Irregular, porous | High purity alloys, additive manufacturing |
Niobium-titanium | Nb-Ti alloys with 10-50% Ti | Irregular | MRI magnets, superconductors |
Nickel niobium | Nb-Ni alloys, commonly 60:40 ratio | Spherical | Electronics, corrosion resistant alloys |
Tantalum niobium | Nb-Ta alloys containing 10-90% Ta | Angular | High temperature alloys, corrosion resistance |
Ferroniobium | Iron-niobium master alloys with 60-70% Nb | Irregular | Steel alloying addition |
Pure niobium provides optimal high temperature properties. Alloying additions like titanium or nickel enhance mechanical properties. Hydriding improves powder flow and sintering response.
Properties of Niobium Powder
Niobium powder offers a balance of physical, mechanical, electrical, thermal, and chemical properties that make it suitable for high performance applications.
Niobium Powder Properties
Property | Typical Values | Significance |
---|---|---|
Particle size | 1 – 150 microns | Compactibility, sintering behavior |
Apparent density | 2.5 – 5.0 g/cc | Pressing and handling characteristics |
Tap density | 3.5 – 7.0 g/cc | Indicator of compressibility |
Flow rate | 25 – 50 s/50g | Powder flowability, ease of die fill |
Oxygen content | 500 – 5000 ppm | Influence on mechanical properties |
Thermal conductivity | 54 W/m·K | Heat removal capability |
Melting point | 2469°C | Retains strength at high temperatures |
Electrical resistivity | 15-20 μΩ·cm | Conductive properties |
Tensile strength | 250 – 650 MPa | Resistance to fracture |
Hardness | 80 – 200 HV | Resistance to wear, deformation |
Very high melting point and stable microstructure confer excellent high temperature properties. Low electrical resistivity provides conductivity.
Powder characteristics like particle size, morphology, and oxygen content determine behavior during processing and final material performance.
Applications of Niobium Powder
The unique properties of niobium make it suitable for specialized applications including:
Niobium Powder Applications
Industry | Uses | Desired Properties |
---|---|---|
Aerospace | Jet engine components, rockets | High strength-to-weight ratio, heat resistance |
Medical | Implants, radiation therapy | Biocompatibility, corrosion resistance |
Electronics | Capacitors, conductive coatings | Electrical conductivity, superconductivity |
Automotive | Exhaust systems, fuel cell catalysts | Corrosion resistance, high temperature strength |
Chemical | Heat exchangers, reaction vessels | Corrosion resistance against acids and alkalis |
Defense | Missile components, armor | High strength, heat resistance |
Niobium alloys containing titanium or molybdenum provide elevated strength levels for aerospace turbines and rocket nozzles operating at extreme temperatures.
Specialty niobium-tin wires enable superconducting magnets for MRI medical imagers and physics research equipment. Porous niobium structures serve as catalyst supports for fuel cell electrodes.
Niobium’s stability across a wide temperature range makes it well suited for furnace components, aerospace systems, and other challenging high-heat environments.
Specifications for Niobium Powder
International material standards help define composition limits, acceptable impurity levels, particle size ranges, and other test methods specific to niobium powder grades for different applications.
Niobium Powder Specifications
Standard | Description | Particle Size | Purity | Oxygen Content |
---|---|---|---|---|
ASTM B393 | Pure niobium powder | -325 mesh | 99.8% min | 2000 ppm max |
ASTM B394 | Niobium hydride powder | 10 – 75 microns | 98% min | 4500 ppm max |
AWS A5.18 | Niobium-titanium powder for welding | -100 mesh | Per alloy composition | 3000 ppm max |
ASTM B517 | Ferroniobium granules | 3 – 25 mm | 60-70% Nb | 1.5% max |
ISO 9001 | Quality management for Nb producers | Customer specified | 99.9% min | Application specific |
These help define quality criteria for using niobium powder in different fields like alloy welding, superconductors, steelmaking, or general industrial applications.
-
Ti48Al2Cr2Nb powder
-
Ti45Al8Nb Powder
-
Ti22Al25Nb Powder
-
TC18 Powder : Unlocking the Power of Titanium Carbide
-
TC11 Powder : A Comprehensive Guide
-
TC4 ELI Powder: Unlocking the Potential of Titanium Alloys
-
Best Ti-6Al-4V powder (TC4 Powder)for additive manufacturing
-
TA15 Titanium Alloy Powder
-
Titanium and aluminum TA7 powder
Niobium Powder Suppliers
Many companies produce and distribute niobium powder in various compositions, sizes, purity levels, and package quantities to suit user requirements.
Niobium Powder Suppliers
Supplier | Production Capacity | Products | Pricing |
---|---|---|---|
CBMM | 63,000 tonnes/year | Pure niobium, niobium hydride | $$/kg |
Solikamsk | 15,000 tonnes/year | Ferroniobium, niobium alloys | $$/kg |
AMG Superalloys | 10,000 tonnes/year | Nickel niobium, specialty alloys | $$$/kg |
Titanex | 3,000 tonnes/year | Pure niobium, mill products | $$/kg |
Edgetech Industries | 1,000 tonnes/year | Pure niobium, niobium oxides | $$/kg |
Pricing varies based on purity, particle size, alloy composition, and lot quantity from $50/kg up to $500/kg or more for high purity grades.
High volume niobium producers are located in Brazil and Russia close to ore supplies. Additional processors exist worldwide to serve regional markets.
Selecting Niobium Powder
Choosing the best niobium powder requires matching composition, properties, and particle characteristics to production methods and performance requirements.
Key selection criteria:
- Purity levels – Impacts mechanical properties and microstructure
- Alloying additions – Titanium, nickel, or tantalum to enhance properties
- Particle size and shape – Affects pressing and sintering behavior
- Apparent and tap density – Indicates powder compressibility
- Oxygen/nitrogen content – Lower is better for high temperature strength
- Powder production method – Determines particle characteristics and capabilities
- Supplier capabilities – Quality systems, sampling, customer service
Work closely with niobium powder suppliers to obtain the optimal material for your process and components. Minor variations in powder properties can significantly impact manufacturing behavior.
FAQ
What is the benefit of niobium hydride powder?
Niobium hydride powders contain atomic hydrogen in solid solution. The hydrogen gives improved powder flow and compressibility compared to pure niobium for easier processing. The hydrogen leaves on heating, so the sintered properties match pure niobium.
How does particle shape influence niobium powder properties?
Spherical powder produced via gas atomization delivers higher and more uniform compressed and sintered density. Irregular powder morphologies benefit green strength for handling after pressing but give less predictable shrinkage behavior.
What affects the price of niobium powder?
Purity is the primary driver of pricing. More extensive refining to achieve higher niobium content costs more. Smaller particle sizes also command higher prices due to sieving requirements. Minimum order quantities can significantly impact per-kilogram pricing.
What niobium content is typical in superalloys?
Superalloys utilize 1-5% niobium additions to provide solid solution strengthening. Higher niobium levels compromise ductility and weldability. Common examples are Inconel 718, Inconel 625, and Waspaloy.
Why is flow rate an important powder characteristic?
Flow rate gives insight into how freely niobium powder flows under standardized conditions. Smooth powder flow allows precise filling of die cavities and improves handling. Lower flow rates indicate potential issues with segregation or caking.
What is the benefit of alloying niobium with titanium?
Additions of 10-50% titanium to niobium significantly increase strength while retaining excellent conductivity and superconductivity properties. Niobium-titanium alloys enable high-field MRI magnets and particle accelerators.
How is ferroniobium used in steelmaking?
As a master alloy containing 60-70% niobium, ferroniobium allows economical introduction of niobium into stainless and high-strength low alloy steels. Niobium is a powerful grain refiner and carbide former in steels.
Conclusion
With its unparalleled thermal stability, corrosion resistance, alloy potential, and superconductivity, niobium fills essential roles in demanding applications. Niobium powder provides engineers flexibility to employ advanced fabrication techniques and tune properties using alloying elements. As new uses emerge for niobium’s capabilities, suppliers continue advancing powder production and characterization.