Al 3104 powder is an aluminum alloy powder used in various metal additive manufacturing processes like laser powder bed fusion and binder jetting. It has excellent mechanical properties, corrosion resistance, and weldability. Some key properties and applications of Al 3104 powder include:
Al 3104 Powder Types and Characteristics
Powder Type | Characteristics |
---|---|
Gas atomized | Spherical morphology, good flowability, common for AM |
Water atomized | Irregular shape, satellite particles, cheaper |
Plasma atomized | Very spherical, smooth surface, excellent flow |
Al 3104 Powder Size Range
Powder Size | Typical Range |
---|---|
Particle size distribution | 15 – 45 microns |
Mean particle size | 25-35 microns |
Al 3104 Powder Applications
Application | Details |
---|---|
Aerospace | Engine parts, structural components |
Automotive | Chassis, transmission parts |
Medical | Implants, prosthetics |
Consumer goods | Sporting equipment, electronics |
Al 3104 Powder Specifications
Parameter | Specification |
---|---|
Density | 2.73 g/cc |
Melting point | Around 615°C |
Composition | Al 97.5%, Mn 0.5-1.5%, Cu 0.8-1.3% |
Flow rate | >25 sec for 50 g (Hall flowmeter) |
Tap density | >80% of theoretical density |
Moisture content | <0.2 wt% |
Al 3104 Powder Suppliers
Supplier | Location | Price Range |
---|---|---|
AP&C | Canada | $50-$150/kg |
Carpenter | USA | $75-$200/kg |
EOS | Germany | $100-$250/kg |
LPW Technology | UK | $60-$180/kg |
The price range depends on order quantity and geographical location. Custom alloys are more expensive.
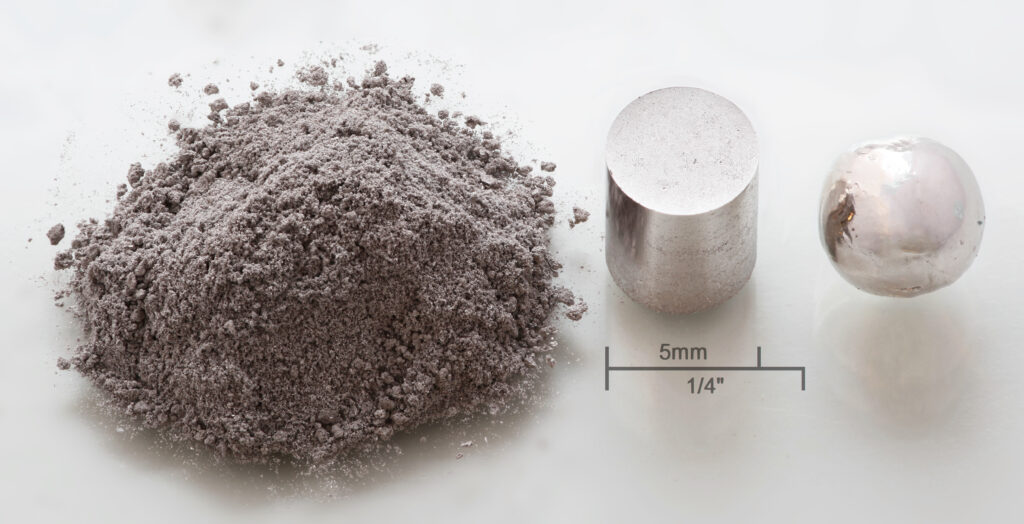
How to Install and Operate Al 3104 Powder Printers
The installation, operation, post-processing depends on the AM process used:
Process | Installation Needs | Operation | Post-Processing |
---|---|---|---|
Binder jetting | Stable platform, exhaust, software | Parameter optimization trials | Curing, sintering, infiltration |
DED | Power supply, positioning system, enclosure | Calibration, build parameter tuning | Cutting, machining, heat treatment |
PBF | Laser equipment, chamber, sieving system | Parameter selection, optimization | Support removal, stress relief, hot iso |
Al 3104 Powder Printer Maintenance
Activity | Frequency | Details |
---|---|---|
Storage | Always | Store in cool, dry area in sealed containers |
Sieving | Before reuse | 150-250 micron mesh to remove large particles |
Blending | As needed | Homogenize and eliminate segregation |
Powder recycling | Up to 10 times | Reuse mixed with fresh powder for consistent quality |
Choosing the Right Al 3104 Powder Manufacturer
When selecting an Al 3104 powder supplier, consider the following criteria:
- Quality control records and consistency in powder morphology and composition
- Technical expertise and customer service related to metal AM
- Ability to customize alloys and perform quality testing
- Scale of production capacity and lead times
- Competitive pricing and minimum order quantities
- Reputation and experience in AM industry
- Proximity and logistics for transportation and shipping
Pros and Cons of Using Al 3104 Powder
Advantages | Disadvantages |
---|---|
Excellent strength-to-weight ratio | Lower max temperature than steel alloys |
Good corrosion resistance | Post-processing can alter properties |
Weldable using fusion welding | Porosity defects can occur in AM builds |
Comparatively cheaper than titanium alloys | Lower hardness and wear resistance than steels |
Readily available from range of suppliers | Recycling can introduce impurities over time |
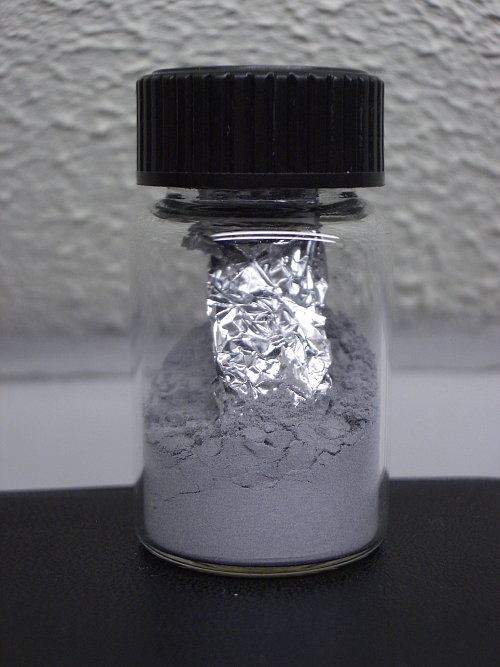
Applications of Al 3104 Powder in Additive Manufacturing
Al 3104 is commonly used to 3D print components for:
- Aerospace: Engine brackets, hydraulic manifolds, UAV parts
- Automotive: Brake discs, powertrain components, chassis parts
- Industrial: Robot arms, jigs, fixtures, process equipment
- Architecture: Decorative lattice structures, cladding panels
- Medical: Dental crowns, cranial implants, prosthetics
- Consumer: Electronics housings, sporting goods, drone bodies
The excellent strength, corrosion resistance, and weldability make Al 3104 suitable for demanding applications across industries. Parts can be optimized with lightweight lattice designs. The material is cheaper than exotic alloys for prototypes.
Al 3104 Powder Composition
The typical composition of Al 3104 powder used in AM is:
- Aluminum: 97.5 %
- Manganese: 0.5 – 1.5%
- Copper: 0.8 – 1.3%
Manganese enhances strength through solid solution strengthening. Copper improves machinability. Other alloying elements like magnesium, silicon, zinc, and titanium can also be present in trace amounts. Powder manufacturers maintain tight composition control for consistent properties.
How Alloying Elements Affect Al 3104 Properties
Alloying elements in Al 3104 powder influence its microstructure and properties when processed through AM:
- Manganese increases yield strength and hardness through solid solution strengthening. It also improves workability.
- Copper increases strength and facilitates precipitation hardening heat treatments. It lowers corrosion resistance slightly.
- Magnesium control aging kinetics during artificial aging to enhance strength. It also aids weldability.
- Silicon modifies the eutectic phase improving fluidity in fusion welding. It causes embrittlement if present above trace amounts.
Microstructure of As-Printed Al 3104 Parts
The microstructure of Al 3104 parts printed using PBF processes like DMLS and SLM consists of:
- Fine cellular subgrain structure from rapid solidification and epitaxial growth
- Small equiaxed grains in melt pool interiors surrounded by columnar grains
- High dislocation density and elemental segregation along cell boundaries
- Precipitation of alloying elements like CuAl2 and Al-Mn phases
- Lack of long range order due to non-equilibrium solidification
Post-processing like hot isostatic pressing and heat treatment can modify the grain structure and distribution of alloying elements significantly.
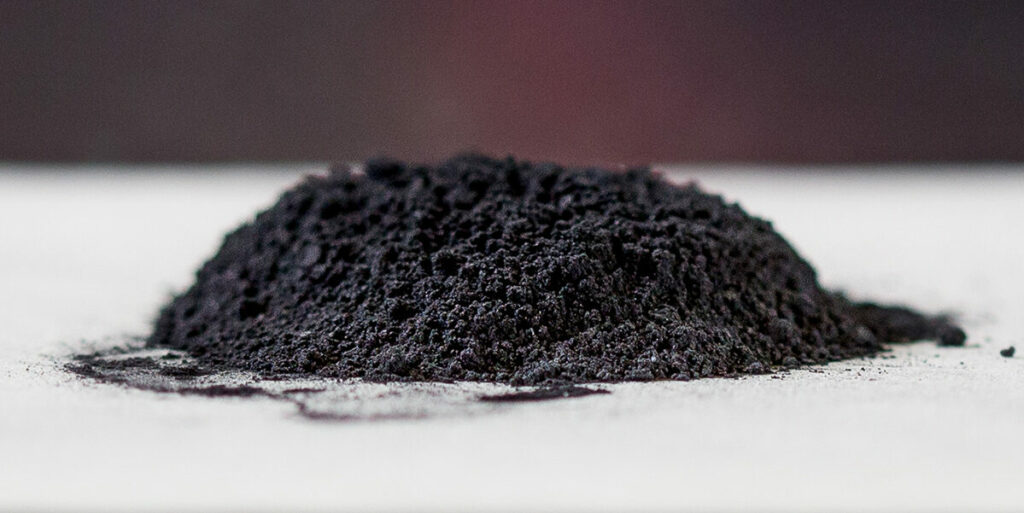
How Particle Shape Affects Al 3104 Powder Performance
- Spherical particles with smooth surface morphology exhibit good flowability, spreadability, and packing density. This results in consistent layer thickness and uniform melting.
- Irregular powder particles with satellite formations have poorer flow rates. This leads to scattering losses while deposition and improper melting.
- Particle size distribution with a mix of fine and coarse particles reduces entrapment of unmelted powders. Wider distributions above 30 microns can cause poor surface finish.
- Higher powder recyclability up to 10 times for spherical Al 3104 particles compared to irregular shapes which tend to accumulate impurities and deform with reuse.
Critical Process Parameters for Al 3104 Powder Bed AM
Parameter | Typical Range | Effects |
---|---|---|
Layer thickness | 20 – 50 μm | Resolution, build time, powder consolidation |
Laser power | 100 – 500 W | Energy input, melting, defects |
Scan speed | 500 – 2500 mm/s | Solidification kinetics, porosity |
Hatch spacing | 0.08 – 0.12 mm | Bonding between tracks, density |
Offset between layers | ~50% of layer thickness | Bonding strength between layers |
Post-Processing Methods for Al 3104 AM Parts
Post-processing is used to relieve stresses, improve properties, and achieve dimensional accuracy in Al 3104 AM parts:
Method | Purpose | Procedure |
---|---|---|
Hot isostatic pressing | Close porosity, refine structure | Heat under pressure at 550°C |
Solution treatment | Dissolve precipitates | Soak at 520°C, quench rapidly |
Artificial aging | Precipitation hardening | Heat to 170°C, hold for 10 hrs |
T6 heat treatment | Maximize strength | Solution treat, quench, artificial aging |
Surface finishing | Improve surface finish | Sand blasting, glass bead peening, CNC polishing |

FAQs
Q: What particle size is recommended for Al 3104 powder in AM?
A: A particle size range of 15-45 microns with a mean of 25-35 microns is typical for Al 3104 powders used in additive manufacturing. This provides good packing and flowability.
Q: Can you 3D print Al 3104 on desktop metal printers?
A: Yes, Al 3104 powder can be used with desktop binder jetting and PBF systems provided they meet the specifications like flow rate, density, particle size distribution etc. Suitable print parameters need to be developed.
Q: What are the mechanical properties of as-printed Al 3104 parts?
A: In the as-printed condition, Al 3104 parts usually have tensile strength 300-350 MPa, yield strength 220-270 MPa, elongation 5-8% and hardness around 80 HB. The properties can be further improved through heat treatment.
Q: Does Al 3104 powder require hot isostatic pressing after AM?
A: HIP helps close internal voids and pores in Al 3104 parts printed using PBF processes. It also alleviates residual stresses. HIP is recommended for fatigue critical applications. For non-critical uses, it may be optional.
Q: Can you weld Al 3104 AM parts using fusion welding?
A: Yes, Al 3104 has very good weldability using processes like MIG, TIG and laser welding. Care must be taken to avoid solidification cracking by controlling heat input and using filler material. Post-weld heat treatment can relieve stresses.
Q: How long can unused Al 3104 powder be stored for AM?
A: Unused Al 3104 powder can be stored for up to 1 year in properly sealed containers under cool, dry storage conditions while maintaining flowability and properties. Longer storage can cause oxidation and caking issues.
In summary, Al 3104 is an excellent aluminum alloy powder for demanding additive manufacturing applications across automotive, aerospace, industrial, and medical sectors owing to its versatile properties, weldability, corrosion resistance, and cost advantage versus exotic alloys. Proper powder characterization, AM process parameters, and post-processing are key to achieving full material capabilities for complex printed parts with this alloy.