Aluminum based alloy powders are widely used in various industries due to their lightweight, high strength, and corrosion resistance properties. This guide provides a detailed overview of aluminum alloy powder including types, characteristics, applications, specifications, suppliers, installation, operation, maintenance, how to choose suppliers, pros and cons, and other key information.
Overview of Aluminum Based Alloy Powder
Aluminum based alloy powder refers to powder metallurgy materials produced from aluminum alloys. They exhibit properties like high strength, light weight, resistance to corrosion, and ability to withstand high temperatures. Alloy powder can be produced through methods like gas atomization, water atomization, mechanical alloying, and electrolysis.
These powders find use in automotive parts, aircraft components, aluminum powder metallurgy parts, additive manufacturing, surface coatings, welding wires, electronics, and more. The most common aluminum alloys used are Al-Si, Al-Mg, Al-Zn, Al-Cu, and Al-Mn. The alloy composition and powder characteristics can be customized as per the application requirements.
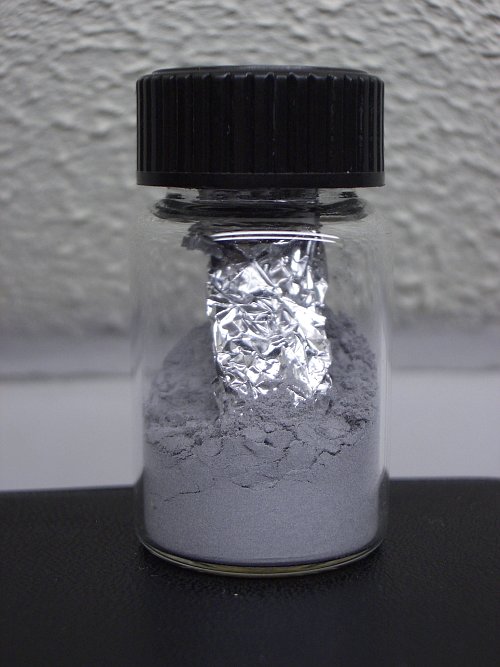
Types of Aluminum Based Alloy Powder
There are several classifications of aluminum alloy powder based on composition, production method, particle size, shape, and microstructure.
Table 1: Types of Aluminum Alloy Powder
Type | Description |
---|---|
Al-Si | Contains silicon as the major alloying element, good castability and weldability |
Al-Mg | Contains magnesium for strength, hardness and corrosion resistance |
Al-Zn | Zinc addition improves strength at elevated temperatures |
Al-Cu | Copper improves strength but decreases corrosion resistance |
Al-Mn | Manganese enhances strength without reducing ductility |
Gas atomized | Made by breaking up molten alloy into fine droplets which solidify into spherical particles |
Water atomized | Molten alloy stream is disintegrated by pressurized water jets |
Mechanically alloyed | Prepared by ball milling of elemental powder mixtures |
Electrolytic | Produced by electrolytic deposition process |
Ultrafine <10 μm | For precision PM parts, additive manufacturing |
Fine 10-45 μm | Most common size for press and sinter process |
Medium 45-150 μm | Used in refractory metallization and thermal spray |
Coarse >150 μm | Applications like surface coating and welding |
Spherical | Produced by gas or water atomization, good flowability |
Irregular | Flattened, angular or jagged particles produced mechanically |
Cryomilled | Fabricated at cryogenic temperatures for stable nanostructures |
Prealloyed | Homogenous alloy composition prior to powder making |
Blended elemental | Alloying by mixing powders of pure metals |
Characteristics of Aluminum Alloy Powder
The properties of aluminum alloy powder can be tailored by controlling composition, particle size distribution, shape, density, and microstructure.
Table 2: Characteristics of Aluminum Alloy Powder
Characteristic | Description |
---|---|
Particle shape | Spherical, irregular, angular, mixed morphology |
Particle size | Ultrafine, fine, medium, coarse range |
Size distribution | Wide or narrow range |
Density | Apparent density and tap density |
Flowability | Influenced by shape, size, surface structure |
Compressibility | Ratio of tap density to true density |
Sinterability | Ability to densify into consolidated part |
Alloy composition | Determines properties like strength, weldability etc |
Surface oxide | Thin oxide film affects powder properties |
Microstructure | Phases present, solid solution, intermetallics |
Contaminants | Levels of oxygen, nitrogen, carbon |
Applications of Aluminum Alloy Powder
The versatility of aluminum alloy powder makes it suitable for use in diverse applications across many industry sectors.
Table 3: Applications of Aluminum Alloy Powder
Application | Details |
---|---|
Automotive | Engine blocks, pistons, gears, wheels |
Aerospace | Aircraft structural parts, engine components |
Additive manufacturing | Used in DMLS, binder jetting processes |
P/M parts | Press and sintered into high performance parts |
Surface coating | Thermal spray coatings for wear/corrosion protection |
Welding | Addition into welding wire and electrodes |
Refractory metallization | Protects steel from molten metals |
Electronics | Heat sinks, substrates, conductors |
Packaging | Aluminum flake powder in paints and primers |
Pyrotechnics | Aluminum powder in solid propellants and explosives |
The automotive sector uses aluminum alloy powder for lightweight and high strength parts. The aerospace industry relies on it for aircraft structural components. Additive manufacturing utilizes alloy powder feedstock for directly printing metal parts. Press and sinter technology consolidates the powder into high performance P/M parts. Thermal spraying applies alloy coatings for enhanced surface properties. It is also incorporated in welding consumables. Other uses include heat sinks in electronics, metallization, packaging, and pyrotechnics.
Specifications of Aluminum Alloy Powder
Aluminum alloy powder is produced and tested to meet established specifications as per international and national standards. This ensures it has the required composition, particle characteristics, microstructure, density, flow rate, compressibility and other parameters needed for the intended application.
Table 4: Specifications of Aluminum Alloy Powder
Specification | Details |
---|---|
Alloy grade | EN AW-1050, EN AW-6061, EN AW-7075 etc. |
Composition | Al, Mg, Si, Zn, Mn, Cu, Cr, Zr contents |
Particle size | D10, D50, D90 values |
Particle shape | Aspect ratio, morphology |
Tap density | 2-3 g/cc range |
Flow rate | Hall flowmeter test |
Compressibility | Green density after compaction |
Oxide film thickness | 1-10 nm range |
Contaminants | O, H, N, C thresholds |
Microstructure | Phases, grain size, defects |
Surface area | BET method for fine powder |
Standards | ASTM B964, ASTM B214, ISO 13318, etc |
The chemical composition is controlled as per the designated aluminum alloy grade like EN AW-6061 containing Mg and Si. Particle size distribution provides D10, D50 and D90 values. Tap density gives the apparent density after tapping. Hall flowmeter test measures flow rate through an orifice. Compressibility indicates how densely it packs during compaction. Surface oxides are limited to nanoscale thickness. Contaminants like oxygen and nitrogen are minimized. Microstructure, phases, and grain size are characterized. Surface area is measured for fine powder. International standards help ensure batch-to-batch consistency.
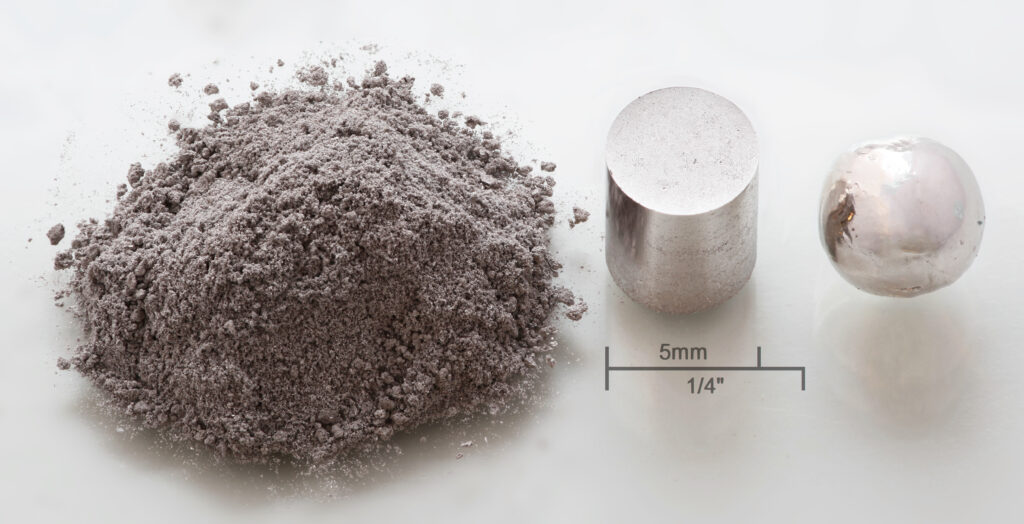
Aluminum Alloy Powder Suppliers
There are a number of reputable aluminum alloy powder manufacturers and suppliers that cater to the various industries. Buyers should evaluate suppliers based on product quality, reliability, prices, certifications and customer service.
Table 5: Aluminum Alloy Powder Suppliers
Company | Location | Products |
---|---|---|
Hoganas | Sweden | Gas atomized aluminum alloy powder |
GKN Hoeganaes | USA | Water atomized & prealloyed powders |
Toyal | Japan | Spherical & irregular aluminum powder |
Kymera International | USA | Aluminum alloy powder for AM |
Sandvik Osprey | UK | Water atomized aluminum powder |
CNPC Powder | China | Aluminum & aluminum alloy powder |
AMETEK | USA | Automotive grade aluminum powder |
Hoganas in Sweden, GKN Hoeganaes in the USA, Toyal in Japan are the top global suppliers of aluminum alloy powders. Kymera and AMETEK offer aluminum alloys for additive manufacturing and automotive applications respectively. Sandvik Osprey and CNPC are other leading producers. Buyers can select suppliers based on factors like product consistency, quality control, logistics, and technical support.
Table 6: Aluminum Alloy Powder Price Range
Alloy Type | Particle Size | Price Range |
---|---|---|
Al 1050 | 15-63 microns | $ 5-8 per kg |
Al 6061 | 15-45 microns | $ 10-15 per kg |
Al 7075 | 10-75 microns | $ 15-25 per kg |
Al Si10Mg | 15-45 microns | $ 18-22 per kg |
Al Si12 | 5-15 microns | $ 25-35 per kg |
Prices depend on alloy composition, particle size distribution, shape, quantity, and manufacturer. Simple alloys like Al 1050 are cheaper. Complex alloys like Al 7075 and Al Si12 are more expensive. Ultrafine powder below 10 microns is costlier than coarse above 45 microns. Reduced prices for bulk order quantities.
Installation of Aluminum Alloy Powder Equipment
Proper equipment and expert installation is key for handling aluminum alloy powder safely and efficiently. Critical factors are highlighted below:
Table 7: Aluminum Alloy Powder Equipment Installation
Stage | Requirements |
---|---|
Safety | Respirators, protective gear, training |
Storage | Waterproof containers, inert gas purging |
Handling | Glove boxes, sealed containers |
Feed lines | Moisture-proof transfer hoses |
Metering valves | Accurate control of powder flowrate |
Mixing | Fast homogenization of powder batches |
hoppers | Smooth mass flow with no bridging |
Sintering furnace | Uniform heating in inert/reducing atmosphere |
Personnel must be equipped with respirators and protective apparel. Powder must be stored in sealed containers with moisture control. Leak-proof glove boxes and hoses provide containment during handling. Metering valves and hoppers prevent clogging and inconsistencies. Sintering under controlled atmospheres like argon prevents oxidation. Proper installation minimizes powder loss and ensures end product quality.
Operation and Maintenance of Aluminum Alloy Powder Equipment
Adequate operating procedures and maintenance of equipment is essential for safe powder processing and preventing downtime.
Table 8: Aluminum Alloy Powder Equipment Operation and Maintenance
Activity | Instructions |
---|---|
Loading | Carefully fill sealed containers with inert gas present |
Unloading | Ensure receiving vessel is ready before transfer |
Storage | First in first out (FIFO) stock rotation |
Sampling | Use airtight thiefs for representative samples |
Staff training | Conduct refreshers on safety procedures |
Equipment inspection | Check valves, gaskets, filters regularly |
Hopper vibration | Prevent powder settling and flow inconsistencies |
Leak checks | Verify hoses, connections are tight |
Overhaul | Major maintenance during planned shutdowns |
Part replacement | Swap worn parts like seals before breakdown |
Housekeeping | Clean equipment and work areas regularly |
Loading and unloading steps must be planned to prevent air ingress. Regular stock rotation and sampling preserves powder quality. Staff need recurrent training to maintain vigilance. Frequent inspections and vibration prevents problems like bridging. Leak checks and maintenance prevents unplanned outages. Overall cleanliness improves safety and powder flow.
How to Choose an Aluminum Alloy Powder Supplier
Choosing a reliable and high quality aluminum alloy powder supplier is an important process. Below are key factors for buyers to consider during selection.
Table 9: How to Choose an Aluminum Alloy Powder Supplier
Parameter | Criteria |
---|---|
Powder specification | Meets composition, size, shape needs |
Quality certifications | ISO 9001, IATF 16949, AS9100 |
R&D capabilities | Alloy development, characterization skills |
Manufacturing facilities | Modern machinery, process controls |
Testing equipment | For chemical, physical, structural testing |
Quality control | Statistical process control, sampling plans |
Technical support | Powder selection advice, application troubleshooting |
Logistics | Ability to securely ship hazardous goods |
Business standing | Years in business, financial stability |
Pricing | Economical budget and bulk order discounts |
References | Feedback from existing customers |
The powder product range must match the composition, particle size and shape needs of the application. Quality management certifications like ISO 9001 indicate supplier consistency. Advanced R&D and testing capabilities help customize alloys and characterize powder properties. Sophisticated manufacturing and stringent process controls are preferred. Strong technical assistance is invaluable during powder selection and application challenges. Established companies with sound finances reduce risk. Reasonable budget pricing and bulk discounts are ideal. Positive feedback from references builds confidence. Evaluating multiple criteria helps identify the ideal aluminum alloy powder supplier.

Pros and Cons of Aluminum Based Alloy Powder
Aluminum alloy powder has many benefits but also some limitations that must be considered when selecting materials for an application.
Table 10: Pros and Cons of Aluminum Alloy Powder
Pros | Cons |
---|---|
Lightweight | Relatively soft and lower strength |
High strength-to-weight ratio | Susceptible to corrosion and oxidation |
Good thermal and electrical conductivity | Not suitable for high temperature uses |
Excellent workability and machinability | Requires protective coatings |
Available in wide range of alloys | More expensive than steel powder |
Flows well for automated processing | Careful handling required to avoid fires |
Non-toxic | Recyclability issues with some alloys |
Non-magnetic | Limited weldability of certain alloys |
Advantages like low density, high strength-to-weight ratio, thermal/electrical properties, ease of fabrication, and alloy flexibility make aluminum very attractive for many applications. Limitations such as softness, oxidation tendency, cost, flammability hazards, recycling difficulty, and weldability challenges of some alloys must also be considered. Weighing both pros and cons allows optimal material selection.
FAQs
Q: What are the main alloying elements used in aluminum alloy powder?
A: The major alloying elements are silicon, magnesium, zinc, copper, and manganese which impart beneficial properties like strength, hardness, weldability, and high temperature performance.
Q: Does aluminum alloy powder require special storage precautions?
A: Yes, aluminum powder is highly reactive and flammable. It requires storage in tightly sealed containers with inert gas blanketing to prevent oxidation and explosion hazards. Low humidity is also recommended.
Q: How is aluminum alloy powder used in additive manufacturing?
A: In additive manufacturing processes like direct metal laser sintering (DMLS) and binder jetting, aluminum alloy powder is spread in thin layers and selectively fused by laser or binder to build up 3D metal parts layer by layer.
Q: What are some examples of aluminum alloy designations?
A: Some common wrought and powder metallurgy aluminum alloy designations are 2024, 6061, 7075, AlSi10Mg, AlSi12, Scalmalloy, and many others denoting composition.
Q: What influences the price of aluminum alloy powder?
A: Prices depend on alloy composition, particle size and shape, production method, order quantity, supplier, and powder properties. More complex alloys with finer size distribution tend to be more expensive.
Q: What are some key material properties of aluminum alloy powder?
A: Key properties are density around 2.7 g/cc, strength ranging from 200 to 700 MPa, hardness from 60 to 150 HB, thermal conductivity up to 250 W/m-K, electrical conductivity up to 45% IACS, and melting point around 500 to 650°C depending on alloy.
Q: What are some examples of aluminum alloy powder specifications?
A: Specifications include alloy composition like EN AW-6061, particle size distribution parameters like D50 of 30 microns, morphology like spherical shape, tap density of 2.2 g/cc, oxygen content below 0.6%, and standards like ASTM B214.
Q: How is aluminum alloy powder manufactured?
A: Main production methods include gas atomization, water atomization, mechanical alloying, and electrolysis. Gas atomization using an inert gas produces fine spherical powder with controlled size distribution.
Q: What are some key applications of aluminum alloy powder?
A: Major applications are automotive parts like pistons, aerospace components like airframe structures, additive manufacturing of metal parts, sintered P/M parts, thermal spray coatings, welding wire, explosives & pyrotechnics, electronics like heat sinks, and aluminum flake powder for paint pigments.
Q: What are some alternatives to aluminum alloy powder?
A: Alternatives include stainless steel powder, titanium powder, nickel alloy powder, tool steel powder, copper powder, and cobalt chrome powder which offer higher strength at elevated temperatures but at increased density and cost.