Hastelloy X powder is a nickel-chromium-iron-molybdenum alloy powder with excellent high temperature strength, oxidation resistance, and fabricability. This guide provides a comprehensive overview of Hastelloy X powder, including types, characteristics, applications, specifications, suppliers, installation, operation, maintenance, how to choose suppliers, pros and cons, and FAQs.
Overview of Hastelloy X Powder
Hastelloy X is a nickel-based superalloy powder used primarily in high-temperature applications up to 1150°C. Key features of Hastelloy X powder include:
- Excellent high-temperature strength and creep resistance
- Good oxidation and corrosion resistance
- High thermal fatigue strength
- Good fabricability like welding, brazing, and machining
- Can be made into various product forms like wire, rod, sheet, tube
Some key applications of Hastelloy X powder include gas turbine components, rocket engine parts, heat exchangers, and furnace components among others.
Hastelloy X gets its high-temperature strength from solid solution strengthening and precipitation hardening by coherent precipitates like Ni3(Ti,Al) called gamma prime. The addition of Mo, W, Co provides solid solution strengthening.
The high chromium and iron content imparts excellent oxidation and corrosion resistance to the alloy. The powder metallurgy route allows making complex parts with fine grains and uniform microstructure.
Types of Hastelloy X Powder
Hastelloy X powder is available in various types depending on composition, powder size, morphology, and manufacturing process:
Table 1: Types of Hastelloy X Powder
Type | Compositional Variants | Particle Size | Morphology | Manufacturing Process |
---|---|---|---|---|
Standard | Ni-22Cr-18Fe-9Mo | 15-45 microns | Spherical, irregular | Gas atomization |
Fine grade | Ni-22Cr-18Fe-9Mo | 10-22 microns | Spherical | Gas atomization |
Ultrafine | Ni-22Cr-18Fe-9Mo | 1-10 microns | Spherical | Plasma rotating electrode process |
Low carbon | Ni-22Cr-18Fe-9Mo + low C | 15-45 microns | Spherical, irregular | Gas atomization |
Custom alloys | Ni-22Cr-18Fe-9Mo-X (X= Co, W, Ta, Nb etc.) | 10-45 microns | Spherical, irregular | Gas atomization |
The standard grade with 15-45 micron particle size is most widely used. But for printing fine resolution parts, ultrafine 1-10 micron powder is preferred. The low carbon variants help to minimize strain-age cracking issues during welding and heat treatment. Custom alloys with additions like Co, W, Ta, Nb provide tailored properties.
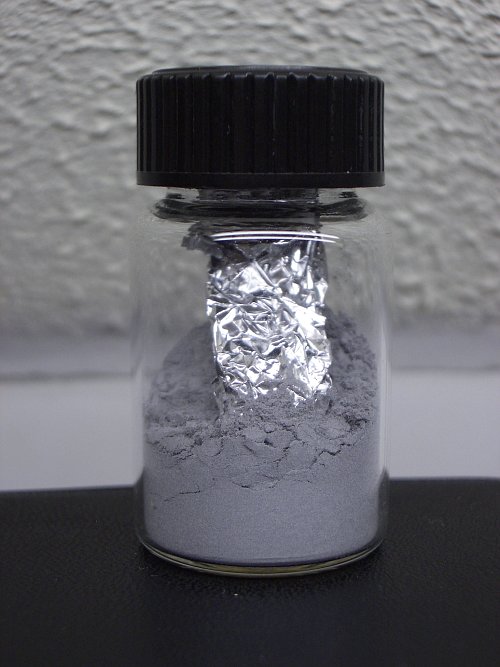
Characteristics of Hastelloy X Powder
Some key characteristics of Hastelloy X powder are:
Table 2: Characteristics of Hastelloy X Powder
Characteristic | Details |
---|---|
Composition | Nickel: Balance, Chromium: 8-10%, Iron: 15-20%, Molybdenum: 8-10%, Cobalt: 0-2%, Tungsten: 0-2%, Carbon: 0.05-0.15%, Manganese: 0-1%, Silicon: 0-0.5%, Sulfur: 0-0.015%, Phosphorus: 0-0.02% |
Density | 8.22 g/cc |
Melting point | 1350-1400°C |
Color | Metallic gray |
Crystal structure | Face centered cubic |
Powder particle size | 15-45 microns typically |
Powder morphology | Predominantly spherical, some irregular |
Flowability | Excellent due to spherical shape |
Apparent density | Typically 4.0-4.5 g/cc |
Tap density | Typically 4.5-5.0 g/cc |
The properties make Hastelloy X suitable for additive manufacturing, thermal spray, composite production, and press and sinter powder metallurgy.
Applications of Hastelloy X Powder
Some major applications of Hastelloy X powder include:
Table 3: Applications of Hastelloy X Powder
Application | Details |
---|---|
Jet engine parts | Combustor cans, burner cans, transition ducts, spray bars, fuel nozzles, flame holders |
Rocket engine parts | Combustion chamber, nozzle throat, liners |
Gas turbines | Hot section blades and vanes, combustor liners |
Heat exchangers | For high temperature gases and corrosive fluids |
Furnace components | Trays, fixtures, fasteners for heat treating furnaces |
Chemical processing | Valves, piping, reaction vessels for corrosive chemicals |
Medical implants | Orthopedic implants due to biocompatibility |
Additive manufacturing | Aerospace and industrial components, tooling |
Thermal spray coatings | To resist wear, corrosion and high temperatures |
The excellent strength and oxidation resistance allow the use of Hastelloy X powder in the most demanding applications with temperatures up to 1150°C.
Specifications and Design Standards for Hastelloy X Powder
Hastelloy X powder conforms to the following specifications and standards:
Table 4: Specifications and Standards for Hastelloy X Powder
Standard | Description |
---|---|
AMS 5754 | Nickel Alloy, Corrosion and Heat-Resistant, Bars, Forgings, and Rings 62Ni – 21.5Cr – 9.0Mo – 1.5Co – 0.6W – 3.0Fe |
AMS 5837 | Nickel Alloy, Corrosion and Heat Resistant, Extrusions 57Ni – 23Cr – 8Mo – 1.5Co – 0.7W – 3.3Fe |
ASTM B435 | Standard Specification for UNS N06002, UNS N06230, UNS N12160, and UNS R30556 Plate, Sheet, and Strip |
AMS 5882 | Nickel Alloy, Corrosion and Heat-Resistant, Powder for Thermal Spraying Applications |
ISO 21809-2 | Petroleum and natural gas industries – External coatings for buried or submerged pipelines used in pipeline transportation systems – Part 2: Single layer fusion-bonded epoxy coatings |
These specifications cover the nominal composition, mechanical properties, grain size, hardness, and impurity limits for various Hastelloy X product forms.
Suppliers and Pricing of Hastelloy X Powder
Some of the major global suppliers of Hastelloy X powder include:
Table 5: Hastelloy X Powder Suppliers and Indicative Pricing
Supplier | Product Forms | Particle Size | Indicative Pricing |
---|---|---|---|
Sandvik | Powder, wire | 15-45 microns | $50-60/kg |
Carpenter Technology | Powder, wire, rod | 10-45 microns | $55-65/kg |
Praxair Surface Technologies | Powder | 15-45 microns | $52-62/kg |
Hoganas | Powder | 15-45 microns | $54-64/kg |
American Elements | Powder | 1-10 microns | $80-100/kg |
Prices vary based on order quantity, exact composition and particle size. Custom alloys with extra elements cost 20-30% more than standard grades. Ultrafine powder under 10 microns costs 50-80% higher compared to 15-45 micron size.
Installing and Operating Hastelloy X Powder Equipment
Key aspects related to installing and operating equipment for Hastelloy X powder handling and processing:
Table 6: Hastelloy X Powder Equipment Installation and Operation
Parameter | Details |
---|---|
Storage and handling | Store in cool, dry area in sealed containers to prevent contamination and oxidation. Use inert gas while handling powder. |
Mixing and blending | Use tumbler mixers for 15-60 minutes to homogenize custom powder blends. |
Compaction | Cold compaction in dies at pressures up to 1000 MPa. Warm compaction may aid particle bonding. |
Debinding and sintering | Debind in hydrogen at 500-600°C and sinter at 1080-1175°C for 1-3 hours under vacuum or inert atmosphere. |
Safety | Use PPE, ensure adequate ventilation and respiratory protection from fine metallic powder dust. |
Maintenance | Check equipment seals, gaskets, valves, container linings periodically. Replace worn parts proactively. |
Process monitoring | Measure powder characteristics like particle size, morphology, flow rate regularly for quality control. |
Proper PPE, storage, handling and atmospheric control are essential for quality powder processing to minimize contamination and maintain consistent results.
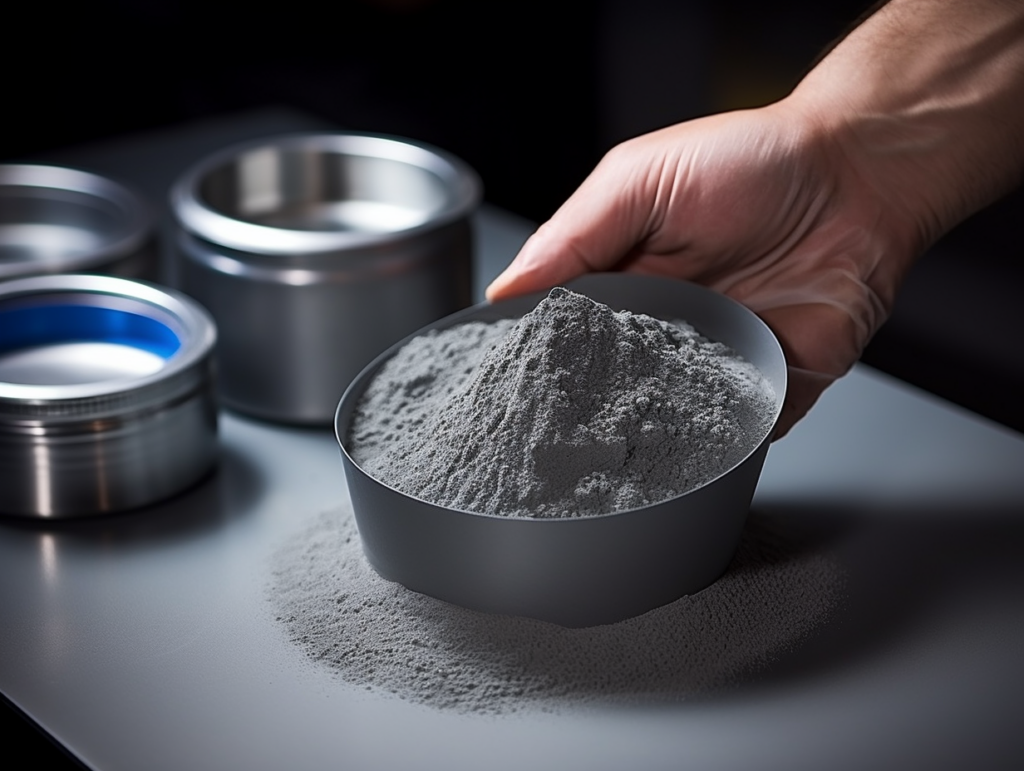
Maintenance of Hastelloy X Powder Equipment
Regular maintenance of Hastelloy X powder equipment is critical for maximizing uptime and attaining repeatable performance:
Table 7: Maintenance Guidelines for Hastelloy X Powder Equipment
Equipment | Maintenance Activities | Frequency |
---|---|---|
Powder storage containers | Inspect for corrosion, leaks | Monthly |
Powder handling system | Check valves, seals | Monthly |
Mixers | Check paddles, liners for wear | Monthly |
Compaction press | Lubricate rams and guides, inspect dies | Weekly |
Sintering furnace | Inspect heating elements, insulation | 6 months |
Gas supply systems | Leak test connections | 3 months |
Powder recovery system | Clean filters | Monthly |
It is recommended to establish a maintenance logbook to track equipment history for identifying problems early. Any corroded or worn components should be replaced immediately to prevent powder contamination.
How to Select a Hastelloy X Powder Supplier
Key considerations for selecting a Hastelloy X powder supplier:
Table 8: Hastelloy X Powder Supplier Selection Criteria
Parameter | Details |
---|---|
Powder quality | Spherical morphology, clean surface, controlled particle size distribution, no contamination |
Composition control | Tight compositional tolerances, certified analysis reports |
Production capacity | Ability to produce required powder quantities reliably |
Customization capability | Alloy modification, particle size and shape control |
Quality systems | ISO 9001 and AS9100 certification, strict quality control |
Regulatory compliance | RoHS, REACH, PFAS free materials declaration |
Delivery time | Ability to deliver fast reliably |
Customer support | Technical expertise for material selection and processing guidance |
Pricing | Cost effective and transparent pricing, discounts for bulk orders |
Payment terms | Flexible payment options |
Choosing suppliers with strict quality control, global certification and strong technical expertise can minimize production issues and rework related to substandard powder.
Pros and Cons of Hastelloy X Powder
Table 9: Advantages and Limitations of Hastelloy X Powder
Advantages | Limitations |
---|---|
Excellent high temperature strength | Relatively high material cost |
Good oxidation and corrosion resistance | Lower ductility than stainless steels |
High thermal fatigue strength | Composition control is critical |
Easy to weld and machine | Susceptible to strain-age cracking during welding or heat treatment |
Can be alloyed to tailor properties | Lower fracture toughness than nickel superalloys |
Many product forms available | Difficult to cast, forge or extrude |
Used for diverse applications | Requires controlled atmospheres during powder processing |
The main tradeoff is the higher cost versus superior high-temperature performance compared to stainless steels. But capabilities like additive manufacturing help mitigate the fabricability issues and allow producing complex geometries.
FAQs
Q: What is Hastelloy X used for?
A: Hastelloy X is used in applications like jet engine combustion cans, rocket engine nozzles, gas turbines, chemical processing equipment where temperatures reach up to 1150°C along with oxidation or corrosion.
Q: Is Hastelloy X stainless steel?
A: No, Hastelloy X is a nickel-based superalloy. It has much better high temperature strength than stainless steels due to nickel and other alloying elements.
Q: What is the difference between Hastelloy X and Hastelloy C?
A: Hastelloy C has higher ductility and fracture toughness owing to its lower strength. Hastelloy X has better high temperature strength and hardness due to additions of Mo, W, Co.
Q: What is the temperature limit of Hastelloy X?
A: The maximum temperature limit for Hastelloy X is about 1150°C. At higher temperatures, excessive oxidation and mechanical strength reduction occurs.
Q: Is Hastelloy X weldable?
A: Yes, Hastelloy X can be welded using processes like GTAW, GMAW and SMAW. Care must be taken to avoid strain-age cracking and conduct post-weld heat treatment.
Q: What is powder Hastelloy X used for?
A: Powder Hastelloy X enables additive manufacturing of complex parts, thermal spray coatings, and powder metallurgy like metal injection molding. It provides flexibility in composition and processing.
Q: Is Hastelloy X resistant to hydrochloric acid?
A: Yes, Hastelloy X offers excellent resistance to hydrochloric acid even at elevated temperatures owing to high chromium and molybdenum content. It outperforms stainless steels in HCl resistance.
Q: Is Hastelloy cheaper than stainless steel?
A: No, Hastelloy X is more expensive than stainless steels on a per pound basis owing to extensive alloying. But it offers vastly superior high temperature strength and corrosion resistance.
Q: What is the density of Hastelloy X?
A: The density of Hastelloy X is around 8.22 g/cc, which is marginally higher than stainless steels due to nickel, iron and molybdenum content.
In summary, Hastelloy X powder is an indispensable material for extreme temperature applications up to 1150°C needing good environmental resistance. With controlled processing, it enables high performance parts production via additive manufacturing and powder metallurgy. This guide covers all essential aspects of utilizing Hastelloy X powder for critical components and coatings.