When it comes to industrial materials, there’s something almost magical about plasma quality powder. If you’re familiar with high-tech industries or cutting-edge manufacturing, you’ve likely heard about this fascinating material. But what exactly is plasma quality powder, and why is it so critical in today’s manufacturing processes?
In this guide, we’ll take you on a deep dive into the world of plasma quality powders. We’ll explore their composition, characteristics, applications, and much more. We’ll also compare different models of metal powders, helping you understand the intricacies that set one apart from another. Whether you’re an industry professional or a curious reader, this article will give you the insights you need.
What is Plasma Quality Powder?
Plasma quality powder refers to a type of metal powder created through a plasma atomization process. This method involves the use of a plasma torch to melt and atomize metal into fine powder particles. The result is a high-quality powder with specific properties tailored to advanced manufacturing processes, such as 3D printing, coating, and additive manufacturing.
Key Properties of Plasma Quality Powder
To appreciate the significance of plasma quality powder, it’s crucial to understand the key properties that make it so valuable:
- Particle Size Distribution: Plasma quality powders have a narrow particle size distribution, making them ideal for precision applications.
- Sphericity: The particles are almost perfectly spherical, which improves flowability and packing density.
- Purity: These powders boast high purity levels, with minimal contamination from oxides or other impurities.
- Density: Plasma quality powders typically have high bulk and tapped density, ensuring consistent performance.
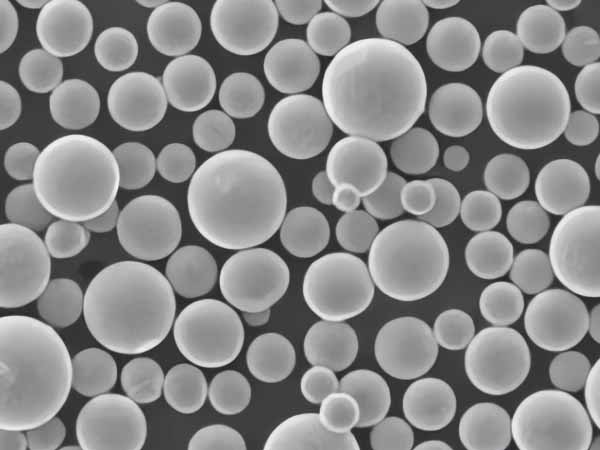
Types of Plasma Quality Powders
Given the various applications for plasma quality powders, several types and grades are available. Below is a detailed table listing some of the most prominent plasma quality metal powders, including their specific models and descriptions:
Model | Composition | Characteristics | Applications | Notable Properties |
---|---|---|---|---|
GKN Hoeganaes PF-1 | Iron-based alloy | High sphericity, excellent flowability | Metal injection molding, 3D printing | High purity, low oxygen content |
Sandvik Osprey 17-4 | Stainless steel | Corrosion-resistant, high strength-to-weight ratio | Aerospace, medical implants | Low carbon, high tensile strength |
AP&C Ti-6Al-4V | Titanium alloy | Biocompatible, lightweight, high tensile strength | Aerospace, medical, automotive | Superior fatigue resistance |
Carpenter LPW 316L | Stainless steel | Excellent corrosion resistance, low carbon | Marine, chemical processing | High ductility, weldability |
EOS NickelAlloy HX | Nickel-based alloy | Heat-resistant, oxidation-resistant | Turbines, high-temperature environments | Excellent creep resistance |
Höganäs FeSi 75 | Iron-silicon alloy | High magnetic permeability, low electrical losses | Electrical steel components | High purity, consistency in grain size |
Tekna Ti64 Gd23 | Titanium alloy | High strength, good elongation, suitable for high-pressure use | Automotive, aerospace, medical devices | Consistent particle size distribution |
Praxair Inconel 625 | Nickel-chromium | Outstanding fatigue and thermal-fatigue strength | Oil & gas, nuclear reactors | Superior weldability and corrosion resistance |
Metco 43VF-NS | Cobalt alloy | Wear-resistant, maintains strength at high temperatures | Turbine blades, wear parts | Excellent high-temperature properties |
Toyal AP10 | Aluminum alloy | Lightweight, high thermal conductivity | Aerospace, electronics | Superior oxidation resistance |
Composition of Plasma Quality Powder
The composition of plasma quality powder is what gives it its remarkable properties. Different metal powders are made up of different elements, depending on the desired application. Here’s a breakdown of the common compositions:
Metal Powder Type | Main Components | Typical Additives |
---|---|---|
Iron-based alloys | Iron (Fe), Carbon (C), Silicon (Si) | Manganese (Mn), Nickel (Ni), Chromium (Cr) |
Stainless steel | Iron (Fe), Chromium (Cr), Nickel (Ni) | Molybdenum (Mo), Carbon (C), Manganese (Mn) |
Titanium alloys | Titanium (Ti), Aluminum (Al), Vanadium (V) | Oxygen (O), Nitrogen (N), Carbon (C) |
Nickel-based alloys | Nickel (Ni), Chromium (Cr), Molybdenum (Mo) | Iron (Fe), Aluminum (Al), Titanium (Ti) |
Cobalt alloys | Cobalt (Co), Chromium (Cr), Tungsten (W) | Nickel (Ni), Molybdenum (Mo), Carbon (C) |
Aluminum alloys | Aluminum (Al), Silicon (Si), Magnesium (Mg) | Copper (Cu), Zinc (Zn), Manganese (Mn) |
Understanding the Composition
When you’re dealing with plasma quality powders, understanding their composition is crucial. For instance, titanium alloys like AP&C Ti-6Al-4V are popular in the aerospace industry due to their high strength-to-weight ratio. On the other hand, Stainless Steel 316L is widely used in marine applications because of its excellent corrosion resistance.
The composition of these powders determines not just their physical and mechanical properties but also their compatibility with different manufacturing processes.
Characteristics of Plasma Quality Powder
Plasma quality powders stand out due to their specific characteristics, which are engineered to meet the demands of advanced manufacturing. Below, we delve into the primary characteristics that make these powders so desirable:
Particle Size Distribution
One of the standout characteristics of plasma quality powders is their tightly controlled particle size distribution. This is essential for ensuring uniformity in applications like 3D printing, where consistent layer deposition is critical. For example, AP&C Ti-6Al-4V powders typically have a particle size distribution in the range of 15-45 microns, which is ideal for additive manufacturing processes.
Sphericity
Sphericity refers to how round the powder particles are. High sphericity is crucial because it enhances flowability, meaning the powder can be easily fed into machines without clumping. This is particularly important in applications like plasma spraying and powder metallurgy. Powders like GKN Hoeganaes PF-1 are known for their high sphericity, which leads to better packing density and improved mechanical properties in the final product.
Purity
Purity is a non-negotiable factor when it comes to plasma quality powders. Impurities can lead to defects in the final product, which is why these powders are subjected to stringent quality control measures. For instance, Sandvik Osprey 17-4 stainless steel powders are known for their low carbon content, which helps in reducing the risk of corrosion and improving the material’s overall longevity.
Density
The density of plasma quality powders plays a crucial role in determining the final properties of the manufactured part. High bulk density is desirable as it leads to less porosity in the final product, while high tapped density indicates good flowability. For example, EOS NickelAlloy HX is favored in high-temperature applications because its high density ensures that the parts are structurally sound and durable.
Applications of Plasma Quality Powder
The versatility of plasma quality powders is reflected in their wide range of applications across various industries. These powders are the backbone of several advanced manufacturing processes, including:
Industry | Common Applications | Preferred Powder Models |
---|---|---|
Aerospace | Turbine blades, structural components, engine parts | AP&C Ti-6Al-4V, Metco 43VF-NS |
Medical | Implants, prosthetics, surgical instruments | AP&C Ti-6Al-4V, Sandvik Osprey 17-4 |
Automotive | Engine parts, lightweight structural components | Tekna Ti64 Gd23, Carpenter LPW 316L |
Energy | Turbine components, nuclear reactor parts | Praxair Inconel 625, EOS NickelAlloy HX |
Electronics | Heat sinks, conductive components | Toyal AP10, Höganäs FeSi 75 |
Marine | Propellers, shafts, fasteners | Carpenter LPW 316L, Sandvik Osprey 17-4 |
Oil & Gas | Drilling equipment, pipeline components | Praxair Inconel 625, Metco 43VF-NS |
Detailed Applications
Aerospace Industry
In aerospace, materials must withstand extreme conditions, from high temperatures to intense mechanical stress. AP&C Ti-6Al-4V is a go-to material due to its lightweight nature and high strength. It’s used in manufacturing critical components like turbine blades, where performance and reliability are non-negotiable.
Medical Field
In the medical field, biocompatibility and corrosion resistance are key. Sandvik Osprey 17-4 is often used for surgical instruments and implants because it resists body fluids and can be safely used in long-term applications. Titanium alloys like AP&C Ti-6Al-4V are also popular for implants due to their compatibility with the human body.
Automotive Sector
The automotive industry seeks materials that offer a balance between strength and weight. Tekna Ti64 Gd23 is ideal for this sector, providing high strength while keeping components lightweight, thus improving fuel efficiency and vehicle performance.
Specifications, Sizes, Grades, and Standards
When choosing a plasma quality powder, it’s essential to consider the specifications, sizes, grades, and standards. The following table outlines some of the key specifications and standards relevant to different plasma quality powders:
Powder Model | Particle Size Range | Bulk Density (g/cm³) | Tapped Density (g/cm³) | Standards |
---|---|---|---|---|
GKN Hoeganaes PF-1 | 10-50 microns | 3.0-4.0 | 4.5-5.5 | ASTM B214, ISO 4497 |
Sandvik Osprey 17-4 | 15-45 microns | 4.0-5.0 | 5.5-6.5 | ASTM F75, ISO 5832-1 |
AP&C Ti-6Al-4V | 15-45 microns | 2.5-3.5 | 3.5-4.5 | ASTM F136, ISO 5832-3 |
Carpenter LPW 316L | 15-53 microns | 3.0-4.0 | 4.0-5.0 | ASTM A240, ISO 5832-1 |
EOS NickelAlloy HX | 20-63 microns | 4.5-5.5 | 6.0-7.0 | ASTM B168, ISO 15156-3 |
Höganäs FeSi 75 | 10-50 microns | 2.5-3.5 | 3.5-4.5 | ASTM A726, ISO 9001 |
Tekna Ti64 Gd23 | 15-45 microns | 2.5-3.5 | 3.5-4.5 | ASTM F136, ISO 5832-3 |
Praxair Inconel 625 | 20-63 microns | 4.5-5.5 | 6.0-7.0 | ASTM B443, ISO 15156-3 |
Metco 43VF-NS | 15-53 microns | 4.0-5.0 | 5.5-6.5 | ASTM F75, ISO 5832-1 |
Toyal AP10 | 10-50 microns | 2.5-3.5 | 3.5-4.5 | ASTM B557, ISO 9001 |
Choosing the Right Specifications
Selecting the right powder depends on your specific application needs. For instance, if you’re working in a high-temperature environment like the energy sector, EOS NickelAlloy HX might be your best bet due to its superior creep resistance. On the other hand, for medical implants, AP&C Ti-6Al-4V is preferable because of its biocompatibility and strength.
Suppliers and Pricing Details
Knowing where to source high-quality plasma powders and understanding their price points is essential for any business. Below is a table with information on some leading suppliers and general pricing details:
Supplier | Powder Models Available | Price Range (per kg) | Additional Services |
---|---|---|---|
GKN Hoeganaes | GKN Hoeganaes PF-1, FeSi 75 | $50 – $120 | Custom powder blends, technical support |
AP&C (GE Additive) | AP&C Ti-6Al-4V, Tekna Ti64 Gd23 | $200 – $500 | Powder recycling, quality certification |
Sandvik Osprey | Sandvik Osprey 17-4, Carpenter LPW 316L | $150 – $300 | Technical consulting, application support |
Praxair Surface Technologies | Praxair Inconel 625, Metco 43VF-NS | $100 – $250 | Custom alloys, R&D collaboration |
EOS GmbH | EOS NickelAlloy HX, Toyal AP10 | $200 – $400 | Application development, training programs |
Carpenter Technology | Carpenter LPW 316L, EOS NickelAlloy HX | $150 – $350 | Custom alloys, heat treatment services |
What to Look for in a Supplier
When selecting a supplier, consider not only the price but also the additional services they offer. For example, AP&C offers powder recycling services, which can significantly reduce waste and cost over time. Similarly, Sandvik Osprey provides technical consulting, helping you optimize your manufacturing processes to get the most out of your powders.
Pros and Cons: Advantages and Limitations of Plasma Quality Powder
While plasma quality powders are incredibly versatile and useful, they aren’t without their drawbacks. Here’s a comparison of the advantages and limitations:
Aspect | Advantages | Limitations |
---|---|---|
Particle Sphericity | Enhances flowability, leading to better part consistency | Slightly higher cost due to the complex manufacturing process |
Purity | Reduces the likelihood of defects in final products | High purity powders may require more stringent handling measures |
Density | Results in strong, dense final parts | High-density powders can be more expensive |
Versatility | Suitable for a wide range of industries | Some powders are highly specialized, limiting their general use |
Customization | Can be tailored to specific applications | Custom powders can have long lead times |
Environmental Impact | Can be recycled, reducing waste | Plasma atomization process consumes significant energy |
Final Thoughts on the Pros and Cons
Understanding the trade-offs between the benefits and limitations of plasma quality powders can help you make more informed decisions. For instance, while high-purity powders like Sandvik Osprey 17-4 are more expensive, they can significantly improve the longevity and performance of your final product, especially in critical applications like medical implants or aerospace components.
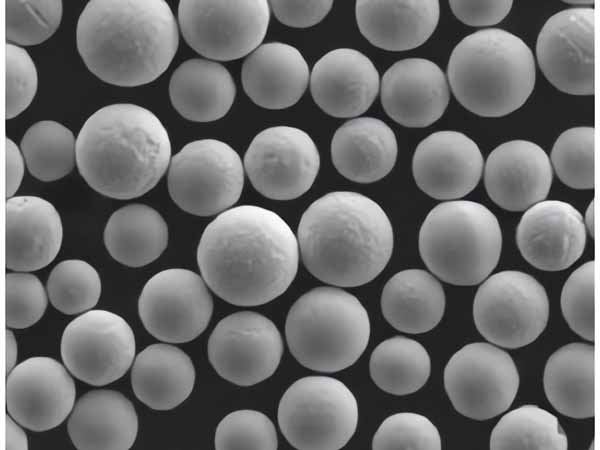
FAQs
Question | Answer |
---|---|
What is the main advantage of plasma atomization? | Plasma atomization produces highly spherical, high-purity powders with consistent particle size distribution, making them ideal for precision applications. |
Which industries benefit most from plasma quality powders? | Aerospace, medical, automotive, and energy industries benefit the most due to the material’s high performance and reliability. |
Can plasma quality powders be recycled? | Yes, many suppliers offer powder recycling services, which can help reduce costs and environmental impact. |
How do I choose the right plasma quality powder? | Consider the specific requirements of your application, including the necessary composition, particle size, density, and industry standards. |
Are there any environmental concerns with using plasma quality powders? | While the powders themselves can be recycled, the plasma atomization process is energy-intensive, so it’s essential to consider the environmental impact. |
What are the key standards for plasma quality powders? | Common standards include ASTM and ISO certifications that ensure the powder meets specific industry requirements. |
How does particle sphericity affect the final product? | Higher sphericity improves the flowability of the powder, resulting in more uniform and reliable final parts. |
Are there cost-effective alternatives to plasma quality powders? | Alternatives exist, such as gas atomized powders, but they may not offer the same level of performance, especially in critical applications. |
This article offers a deep dive into plasma quality powders, providing you with a well-rounded understanding of their properties, applications, and how to choose the right one for your needs. Whether you’re in aerospace, medical, or automotive industries, knowing the ins and outs of these powders can significantly enhance your manufacturing processes and final product quality.