When it comes to achieving superior quality in metal products, post-atomization treatment of metal powders plays a crucial role. If you’re diving into this technical yet fascinating world, let’s break it down together. We’ll explore everything from the basics to specific models of metal powders, and dive deep into the characteristics, applications, and more. Ready? Let’s get started!
Overview of Post-Atomization Treatment
Post-atomization treatment involves processes that enhance the properties of metal powders after their initial atomization. Atomization is a process where molten metal is broken into fine particles. Post-atomization treatment can include processes like annealing, sieving, blending, and surface coating to improve the powder’s characteristics for various applications.
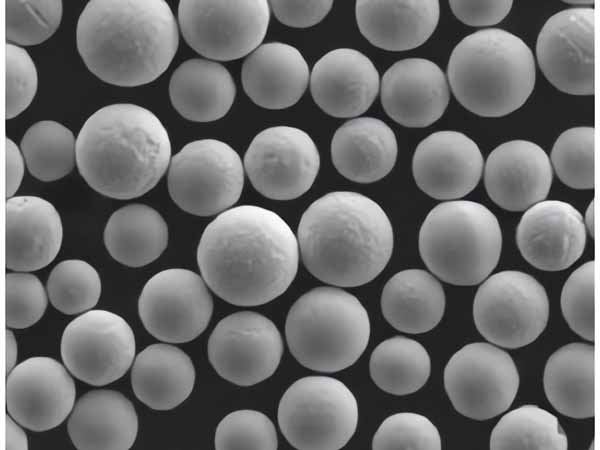
Types and Composition of Metal Powders for Post-Atomization Treatment
Understanding the types and compositions of metal powders is essential for selecting the right material for your needs. Here are some specific metal powder models and their detailed descriptions:
Metal Powder Model | Composition | Properties | Applications |
---|---|---|---|
AP-101 | Iron (Fe), Carbon (C), Silicon (Si) | High strength, good compressibility, wear resistance | Automotive parts, sintered components |
AP-202 | Copper (Cu), Zinc (Zn), Tin (Sn) | Excellent electrical conductivity, corrosion resistance | Electrical components, bushings, bearings |
AP-303 | Nickel (Ni), Chromium (Cr), Iron (Fe) | High temperature resistance, oxidation resistance | Aerospace components, turbine blades |
AP-404 | Titanium (Ti), Aluminum (Al), Vanadium (V) | Lightweight, high strength-to-weight ratio | Medical implants, aerospace structures |
AP-505 | Aluminum (Al), Magnesium (Mg), Silicon (Si) | Lightweight, good thermal conductivity | Heat exchangers, automotive parts |
AP-606 | Stainless Steel (Fe, Cr, Ni) | Corrosion resistance, good mechanical properties | Cutlery, kitchen appliances, medical instruments |
AP-707 | Tungsten (W), Cobalt (Co), Carbon (C) | High hardness, wear resistance | Cutting tools, abrasives |
AP-808 | Cobalt (Co), Chromium (Cr), Molybdenum (Mo) | High strength, excellent wear resistance | Dental and orthopedic implants, superalloys |
AP-909 | Iron (Fe), Nickel (Ni), Molybdenum (Mo) | Good magnetic properties, toughness | Magnetic cores, inductors |
AP-1010 | Copper (Cu), Nickel (Ni), Zinc (Zn) | Good strength, corrosion resistance | Marine applications, coinage |
Properties and Characteristics of Metal Powders for Post-Atomization Treatment
The properties and characteristics of metal powders are critical in determining their suitability for specific applications. Let’s dive into these in more detail:
Property | Description |
---|---|
Particle Size Distribution | Uniform particle size enhances packing density and reduces voids in the final product. |
Flowability | Good flowability is crucial for powder handling and consistent filling of molds. |
Compressibility | High compressibility ensures the powder can be compacted into a dense, solid mass. |
Apparent Density | Apparent density affects the volume-to-weight ratio, influencing the final product’s density. |
Purity | High purity levels are essential to avoid impurities that could affect the material’s performance. |
Surface Area | The specific surface area impacts sintering behavior and the powder’s reactivity during post-atomization treatments. |
Chemical Stability | Resistance to oxidation and corrosion is important for powders used in harsh environments. |
Mechanical Strength | High mechanical strength is necessary for structural applications. |
Thermal Conductivity | Good thermal conductivity is vital for applications requiring heat dissipation. |
Electrical Conductivity | Electrical conductivity is a key factor for powders used in electrical and electronic components. |
Applications of Metal Powders for Post-Atomization Treatment
The versatility of metal powders makes them suitable for a wide range of applications. Here are some common uses:
Application | Description |
---|---|
Automotive Industry | Metal powders are used to manufacture various automotive components, including gears, bearings, and engine parts, thanks to their high strength and durability. |
Aerospace Industry | Powders like titanium alloys are ideal for lightweight, high-strength components used in aircraft and spacecraft. |
Medical Industry | Biocompatible metal powders are used for medical implants, such as hip and knee replacements, due to their excellent mechanical properties. |
Electronics | Conductive metal powders are essential for producing electronic components, such as capacitors, resistors, and connectors. |
Energy Sector | Metal powders are utilized in the production of fuel cells, batteries, and other energy storage devices, due to their excellent conductivity and reactivity. |
Tool and Die Making | High-hardness metal powders like tungsten carbide are used to manufacture cutting tools, molds, and dies. |
3D Printing | Metal powders enable the production of complex and precise parts through additive manufacturing techniques. |
Oil and Gas Industry | Corrosion-resistant metal powders are used in components exposed to harsh environments, such as pipelines and drilling equipment. |
Defense Industry | High-strength, lightweight metal powders are used in military applications, including armor and weapons. |
Construction | Metal powders enhance the strength and durability of construction materials, such as concrete and coatings. |
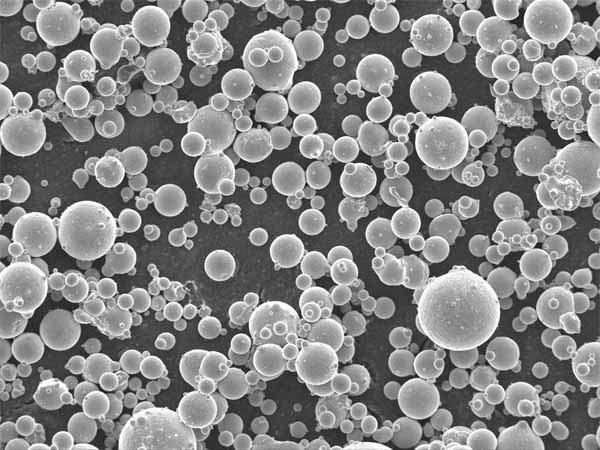
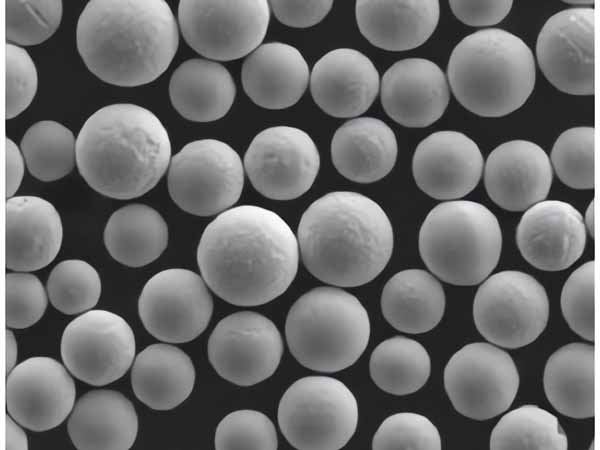
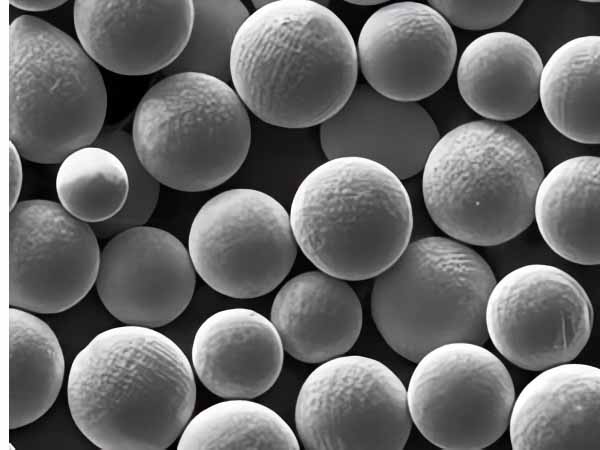
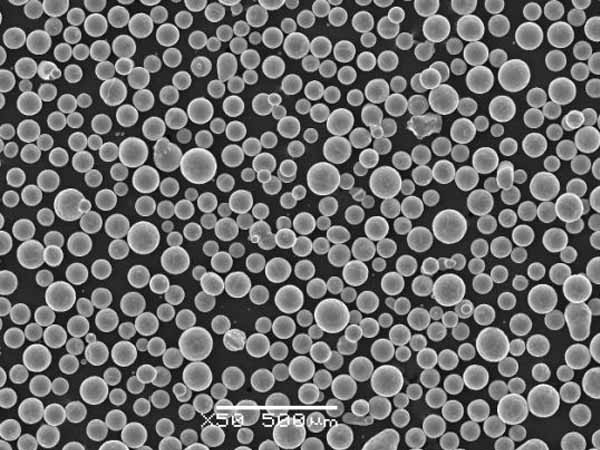
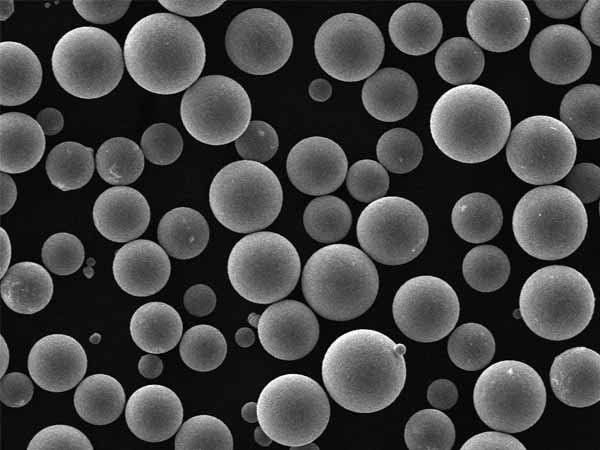
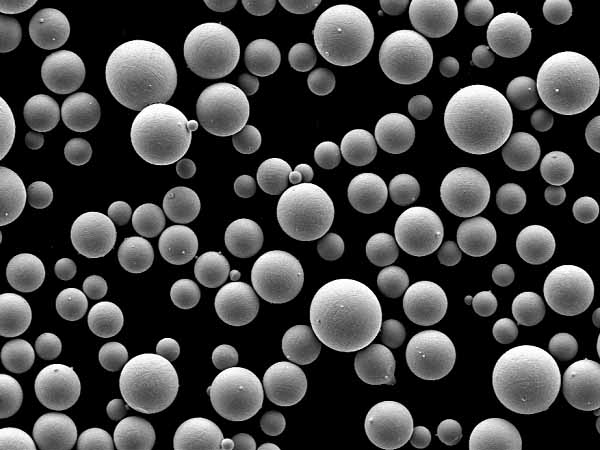
Specifications, Sizes, Grades, and Standards of Metal Powders
Specifications and standards ensure the quality and consistency of metal powders. Here are some typical specifications:
Specification | Details |
---|---|
Particle Size | Ranges from nano-scale (<100nm) to micro-scale (1-1000 microns) depending on the application. |
Grade | Grades vary based on purity and alloying elements, such as Grade 1 (high purity) to Grade 5 (alloyed). |
Standards | ASTM, ISO, and MIL standards specify the requirements for metal powders in various industries. |
Size Distribution | Uniform size distribution is often specified, such as D10, D50, and D90 values, indicating the particle size distribution percentiles. |
Purity Level | Purity levels typically range from 99% to 99.99%, depending on the application requirements. |
Apparent Density | Specified in g/cm³, this affects the packing density and final product properties. |
Flow Rate | Measured in seconds per 50 grams, indicating the powder’s flowability. |
Sintering Temperature | The temperature range required for effective sintering, typically specified in degrees Celsius. |
Suppliers and Pricing Details of Metal Powders
Choosing the right supplier is essential for obtaining high-quality metal powders. Here are some top suppliers and their pricing details:
Supplier | Metal Powder Model | Price (per kg) | Contact Details |
---|---|---|---|
Höganäs AB | AP-101 | $50 | Höganäs AB |
Sandvik Materials Technology | AP-202 | $70 | Sandvik Materials Technology |
Carpenter Technology Corporation | AP-303 | $100 | Carpenter Technology |
GKN Hoeganaes | AP-404 | $150 | GKN Hoeganaes |
ATI Powder Metals | AP-505 | $80 | ATI Powder Metals |
Praxair Surface Technologies | AP-606 | $60 | Praxair |
Arcam AB (GE Additive) | AP-707 | $200 | Arcam AB |
LPW Technology Ltd. | AP-808 | $180 | LPW Technology |
Erasteel | AP-909 | $120 | Erasteel |
Metco (Oerlikon Group) | AP-1010 | $90 | Oerlikon Metco |
Comparing Pros and Cons of Metal Powders for Post-Atomization Treatment
When selecting metal powders, it’s crucial to weigh the pros and cons. Here’s a comparison:
Metal Powder Model | Advantages | Disadvantages |
---|---|---|
AP-101 | High strength, wear resistance | Can be costly, requires precise processing |
AP-202 | Excellent conductivity, corrosion resistance | Lower mechanical strength compared to others |
AP-303 | High temperature resistance | Expensive, limited suppliers |
AP-404 | Lightweight, high strength | High cost, challenging to process |
AP-505 | Good thermal conductivity | Lower strength than steel-based powders |
AP-606 | Corrosion resistance, versatile | Medium cost, moderate strength |
AP-707 | High hardness, wear resistance | Difficult to machine, very dense |
AP-808 | Excellent wear resistance, high strength | Expensive, complex processing |
AP-909 | Good magnetic properties, toughness | Limited applications, can be expensive |
AP-1010 | Good strength, corrosion resistance | Moderate cost, availability issues |
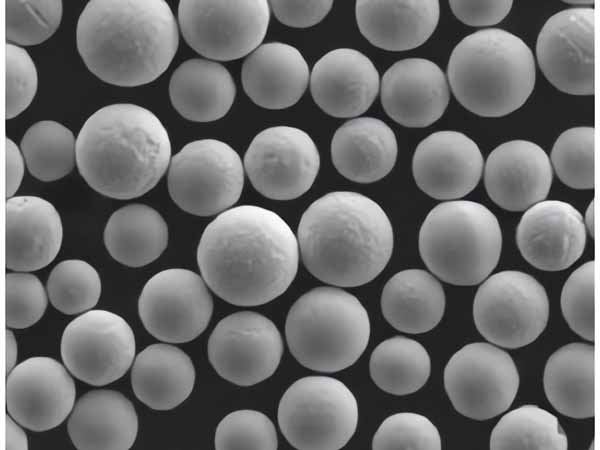
FAQ
Here are some frequently asked questions to help clarify common concerns about metal powders for post-atomization treatment:
Question | Answer |
---|---|
What is post-atomization treatment? | It refers to additional processes like annealing, sieving, blending, and coating that enhance the properties of metal powders. |
Why is particle size important? | Particle size affects the powder’s packing density, flowability, and final product’s properties. |
Which metal powders are best for 3D printing? | Titanium, stainless steel, and nickel-based powders are commonly used for their strength and versatility in additive manufacturing. |
How do I choose the right metal powder? | Consider your application requirements, including strength, conductivity, thermal properties, and cost. |
What are the main suppliers of metal powders? | Notable suppliers include Höganäs AB, Sandvik, Carpenter Technology, GKN Hoeganaes, and ATI Powder Metals. |
Are there standards for metal powders? | Yes, standards like ASTM and ISO ensure quality and consistency in metal powders. |
Can metal powders be recycled? | Yes, many metal powders can be recycled, reducing waste and cost. |
What is the cost range for metal powders? | Prices vary widely based on composition and supplier, ranging from $50 to $200 per kg. |
How are metal powders tested for quality? | Quality tests include particle size analysis, purity checks, and mechanical property evaluations. |
What are the environmental impacts? | Production and recycling processes can have environmental impacts, but advancements are being made to reduce these effects. |
Conclusion
Post-atomization treatment of metal powders is a sophisticated process that significantly enhances the quality and performance of various products. By understanding the types, properties, applications, and suppliers, you can make informed decisions that align with your technical and commercial needs. Whether you’re in automotive, aerospace, medical, or another industry, choosing the right metal powder and treatment process is crucial for success.
By keeping these insights in mind and utilizing the detailed comparisons and specifications provided, you’ll be well-equipped to navigate the complex world of metal powders for post-atomization treatment.