Overview
Pure Al powder, also known as aluminum powder, is a fine granular powder made from aluminum metal. It is commonly used for a variety of industrial applications including metallurgy, explosives, paints, pigments, rocket fuel, thermite reactions, and more.
Some key properties and details about pure Al powder:
- Composition – Nearly 100% aluminum metal, available in different grades
- Particle shape – Spherical, atomized, or flaked
- Particle size – Ranging from 1 micron to 100 microns
- Purity – Available in technical, commercial and high purity grades
- Production method – Mainly through atomization of molten aluminum
- Color – Silvery gray, can be various colors when oxidized
- Bulk density – Around 1 g/cc depending on particle size
- Specific surface area – Up to 10 m2/g for ultrafine powder
- Hazard class – Flammable solid, reacts with air and moisture
Below are tables summarizing the types, applications, specifications, suppliers, and more details about pure aluminum powder.
Types of Pure Aluminum Powder
Type | Characteristics |
---|---|
Atomized Al Powder | Most common type, spherical particles produced by inert gas atomization of molten Al |
Flaked Al Powder | Irregular flake shape, produced through stamping/milling |
Granulated Al Powder | Nodular particles produced by granulation process |
Al Nanopowder | Ultrafine particles under 100 nm, high surface area |
Al Alloy Powders | Al mixed with small amounts of other elements like Mg, Mn, Si, Cu, Zn |
Key Takeaways on Al Powder Types
- Atomized powder has excellent flowability desired for industrial use
- Flaked powder provides reflective metallic effect in paints
- Nanopowders display increased reactivity compared to micron sizes
- Alloying expands options for tailored powder properties
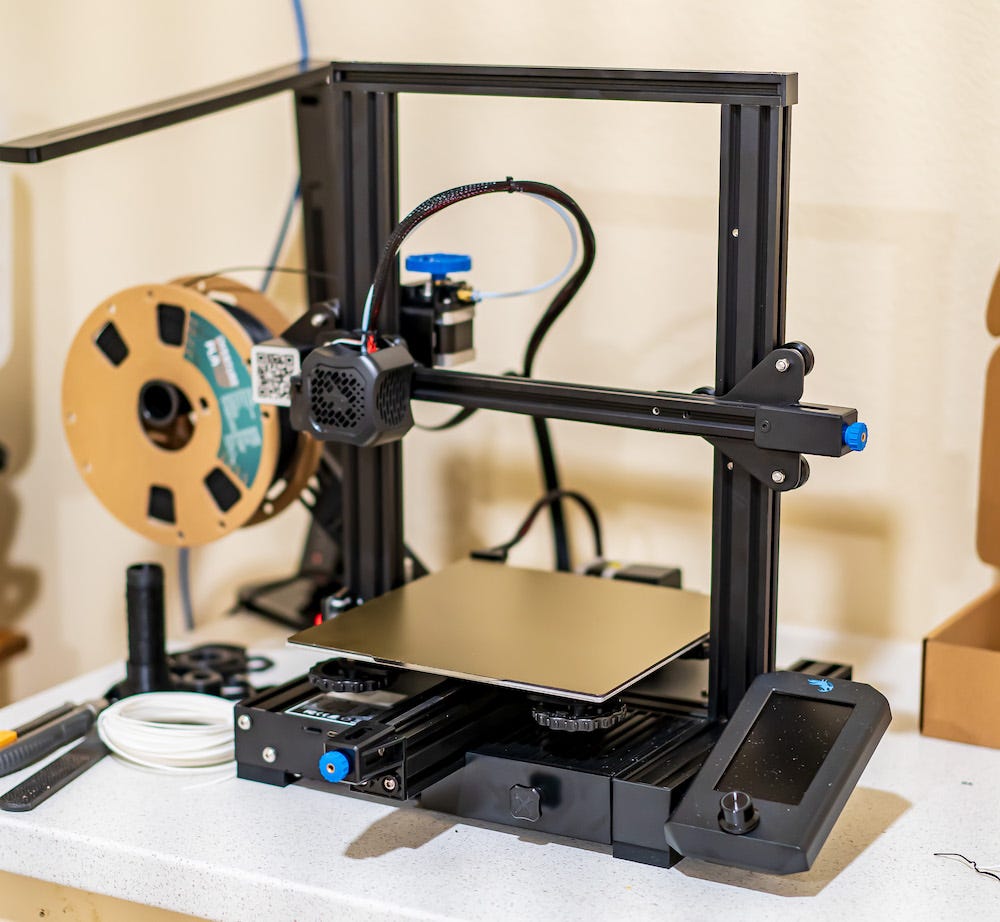
Applications and Uses of Pure Al Powder
Application | Use |
---|---|
Thermite reactions | Exothermic reaction with metal oxides to produce molten metal |
Explosives, pyrotechnics | Fuel component with high heat of combustion |
Rocket propellant | Combined with oxidizers for solid rocket fuel |
Welding | Exothermic reaction with metal oxide coatings |
Paints, pigments | Flaked powder for metallic, sparkling effect |
3D printing | Powder bed printing using laser melting process |
Ceramics | Sintering aid, grain growth inhibitor |
Composites | Reinforcement for aluminum matrix composites |
Pyrolysis | Converted to alumina by heating in air |
Notable Uses for Al Powder
- Thermites and explosives – High energy density makes it excellent fuel
- Pigments and paints – Provides shiny, metallic finish
- 3D printing – Spheroidal shape enables powder bed fusion
- Propellants – High heat and low molecular weight improve performance
Specifications of Pure Aluminum Powder
Parameter | Details |
---|---|
Composition | 98-99% Al, balance impurities |
Particle shape | Spherical, atomized powder preferred |
Particle size | 1 – 150 microns, application dependent |
Size distribution | Tight distributions around nominal size |
Purity | 99.7-99.9% for technical grade, higher for electronics |
Apparent density | Around 1 g/cc, varies with powder size |
True density | 2.7 g/cc |
Specific surface area | 0.1 – 10 m2/g, higher for smaller sizes |
Color | Silvery gray, oxidizes in air over time |
Combustibility | Flammable solid, transports heat rapidly |
Solubility | Insoluble in water, soluble in acid/alkali |
Thermal conductivity | High, around 237 W/m-K |
Key Specifications
- Particle shape and size distribution are critical for performance
- High purity required for reactive applications like thermite
- Surface area increases exponentially as particle size decreases
- Oxidation and passivation must be minimized for reactivity
Aluminum Powder Manufacturing Processes
Process | Description |
---|---|
Atomization | Molten Al stream broken into droplets and solidified rapidly in inert gas |
Milling | Mechanical milling of Al flakes to reduce particle size |
Granulation | Smaller particles agglomerated into spherical granules |
Electrolysis | Al produced through electrolysis process, then ground |
Vapor phase | Al chloride vapors reduced with H2, producing fine powder |
Plasma synthesis | Al vaporized and condensed into nanoparticles |
Comparison of Production Methods
Method | Particle Morphology | Scale | Cost | Common Applications |
---|---|---|---|---|
Atomization | Spherical | Industrial | Low | Thermites, explosives |
Milling | Flakes/irregular | Small | High | Pigments, inks |
Granulation | Nodular | Bench | Medium | Press and sinter |
Electrolysis | Angular | Industrial | Medium | Metallurgy, pyrotechnics |
Vapor phase | Spherical | Small | High | Electronics, pyrotechnics |
Plasma | Spherical | Lab | Very High | Research, energetics |
Key Takeaways on Al Powder Production
- Inert gas atomization is the dominant industrial scale process
- Milling produces irregular flake shapes optimal for pigments
- Vapor phase and plasma methods allow nanoparticle synthesis
- Granulation and electrolysis offer medium scale, lower cost routes
Suppliers and Pricing
Supplier | Location | Grades | Particle Size | Price Range |
---|---|---|---|---|
Valimet | US | Commercial, technical | 1-150 microns | $5-15/lb |
Hognf | Norway | High purity | 1-10 microns | $50-150/lb |
BASF | Germany | Pigment, technical | 5-30 microns | $20-60/lb |
Reynolds | Canada | Pyrotechnic, fuel | 10-75 microns | $15-50/lb |
Atlantic Equipment | US | Commercial, moderate purity | 10-100 microns | $10-30/lb |
Price and Availability Considerations
- Ultrafine nanopowder can cost over $1000/lb
- High purity >99.99% Al adds significant cost
- Custom particle distributions and shapes also increase cost
- Overseas suppliers offer lower cost options
- Consider minimum order quantities which can be ~500-1000 lbs
Installation, Operation and Maintenance
Stage | Activities |
---|---|
Installation | Inspect equipment before use, install in cool, dry, well-ventilated indoor area, ensure proper grounding, provide explosion-proof electrical fittings |
Operation | Avoid dust generation and accumulation during handling and filling containers and equipment, ensure inert gas blanketing for storage tanks, follow controlled filling procedures, use grounded metal containers only |
Maintenance | Regularly inspect powder handling system for leaks and dust buildup, change filters as needed, check grounding connections, keep powder handling areas clean |
Safety and Handling Best Practices
- Avoid all ignition sources during powder handling
- Do not allow powder to accumulate in enclosed areas
- Metallic filters preferred over cloth or paper
- Ensure adequate ventilation and breathing protection
- Follow precautions against explosion and fire risk
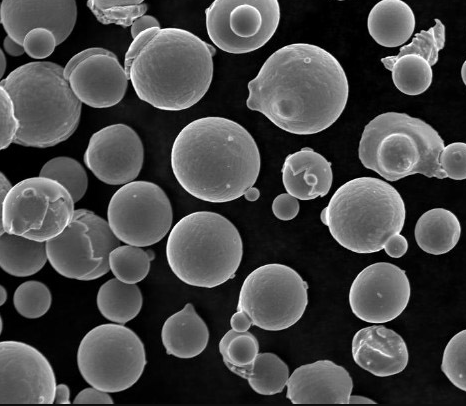
How to Select an Aluminum Powder Supplier
Parameter | Guidelines |
---|---|
Reputation and Experience | Select established suppliers with proven track record in industry |
Quality Certifications | ISO 9001 certification demonstrates commitment to quality |
Technical Expertise | Work closely with knowledgeable sales engineers for product selection |
Powder Properties | Ensure supplier can meet requirements for composition, size, shape, purity |
Testing Capabilities | Supplier should be able to provide composition and particle size distribution data |
Process Capabilities | Consider what production methods supplier has available – atomization, milling etc |
Inventory | Larger suppliers will have powder in stock for quick delivery |
Logistics Assistance | Supplier should support with compliant packaging, shipping dangerous goods |
Safety Information | Ask supplier for SDS, instructions for safe handling and precautions |
Customer Service | Responsive technical and sales support improves buyer experience |
Pricing | Compare pricing through quotes from multiple suppliers |
Key Criteria in Selecting Supplier
- Technical expertise to ensure the powder meets application requirements
- Quality systems and testing capabilities to verify powder properties
- Inventory availability and logistics assistance for fast delivery
- Strong safety expertise and data for safe handling
- Competitive pricing from established, reputable suppliers
Pros and Cons of Aluminum Powder
Advantages | Disadvantages |
---|---|
High heat of combustion | Explosive hazard requires careful handling |
Low molecular weight | Oxidizes readily in air over time |
High thermal and electrical conductivity | Limited shelf life due to oxidation |
Relatively inexpensive | Requires inert storage and handling conditions |
Readily available from suppliers | Powder dust creates housekeeping challenges |
Suitable for industrial scale production | Specialized production knowledge required |
Recyclable and reusable | Perceived as dangerous material by public |
Can be alloyed to customize properties | Some variants prohibited for commercial use |
Key Takeaways on Al Powder Pros/Cons
- Powerful fuel but handling risks require safety investment
- Recyclable but needs controlled atmosphere to prevent oxidation
- Tunable properties through alloying but added complexity
- Scalable production with cost advantages versus niche methods
- Public misperceptions about dangerous materials are a disadvantage
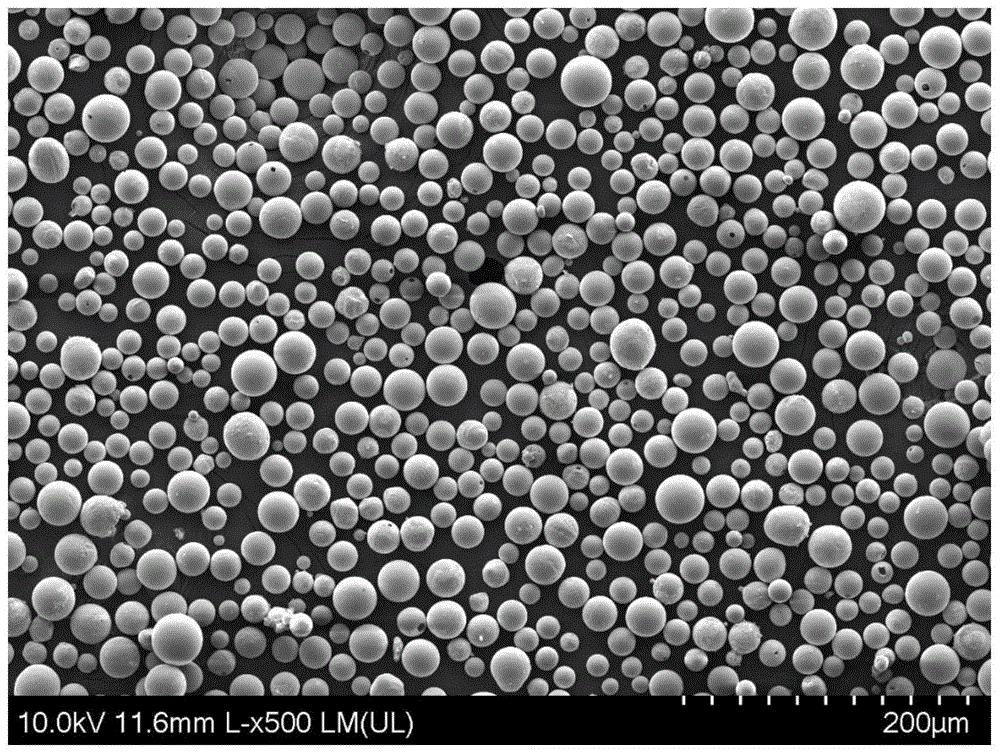
FAQ
What are the different types of aluminum powder?
The main types of aluminum powder include atomized spherical powder, flaked powder, granulated powder, nanoscale powder, and aluminum alloy powders. Atomized and nanoscale powders have very fine, spherical particles. Flaked powder consists of irregular flakes with a large aspect ratio. Granules are nodular agglomerates of small particles. Alloy powders incorporate other elements like copper, zinc, or magnesium.
What is aluminum powder used for?
Major uses of aluminum powder include explosives and pyrotechnics, thermite reactions, solid rocket propellants, pigments and inks, welding and brazing fluxes, 3D printing powders, and metal matrix composites. The fine particle size and high reactivity make it an excellent fuel and ingredient in energetic formulations.
How is aluminum powder made?
The main industrial production method is inert gas atomization, where molten aluminum is broken into droplets, rapidly solidified, and collected as powder. Alternative methods include mechanical milling, granulation of particles into spherical granules, electrolytic production, vapor phase synthesis, and plasma synthesis methods.
Is aluminum powder dangerous?
Aluminum powder is flammable and presents an explosion hazard when suspended in air. It requires cautious handling and storage in an inert environment away from heat, flames, and other ignition sources. With proper safety precautions and procedures, the risks can be minimized.
How do I choose an aluminum powder supplier?
Key factors in choosing a supplier include technical expertise, quality and certifications, testing capabilities, production methods, inventory, logistics assistance, safety information provided, and customer service. Comparing multiple quotes from reputable suppliers is recommended.
What are the advantages and disadvantages of aluminum powder?
Main advantages are high energy density, thermal/electrical conductivity, tunable properties, scalable production, and recyclability. Disadvantages include fire and explosion hazards requiring investment in safety, tendency to oxidize limiting shelf life, and specialized handling.
What should I look for in an aluminum powder specification sheet?
Key parameters to look for include composition/purity, particle size and distribution, shape (spherical/flake), specific surface area, density, color, combustion and explosion risks, and recommended handling precautions. The spec sheet should be aligned with the application requirements.
What safety precautions should I take when handling aluminum powder?
Key precautions include eliminating ignition sources, avoiding dust accumulation, using inert gas blanketing and grounding, ensuring proper ventilation, wearing personal protective equipment, and following all recommended guidelines. Metallic filters, explosion proof lights and electrics, and avoiding paper/plastic bags also help improve safety.
How do I determine which aluminum powder size I need?
The optimal particle size depends on the application. Finer powders often improve reactivity but may be harder to handle. For explosives, 5-10 micron powder is common. Pigments use coarser powder up to 75 microns. Fuel powders for pyrotechnics use 10-45 micron sizes typically. Discuss requirements with suppliers to select the right size.