High entropy alloys powder(HEAs) are a new class of advanced metallic materials that have attracted significant interest in recent years due to their unique properties compared to conventional alloys. HEAs are defined as alloys that contain at least 5 principal elements, each with a concentration between 5-35 atomic%. The high entropy of mixing in these multi-component alloys leads to unique properties such as excellent strength, hardness, wear resistance, corrosion resistance, and high temperature stability.
High entropy alloys powder are typically produced using techniques like vacuum induction melting, vacuum arc melting, laser engineered net shaping, selective laser melting, etc. Recently, powder metallurgy has emerged as a promising approach for manufacturing HEAs with more flexibility in composition and properties. This article provides a detailed overview of HEA powder, its production methods, characteristics, applications, suppliers, and other key aspects.
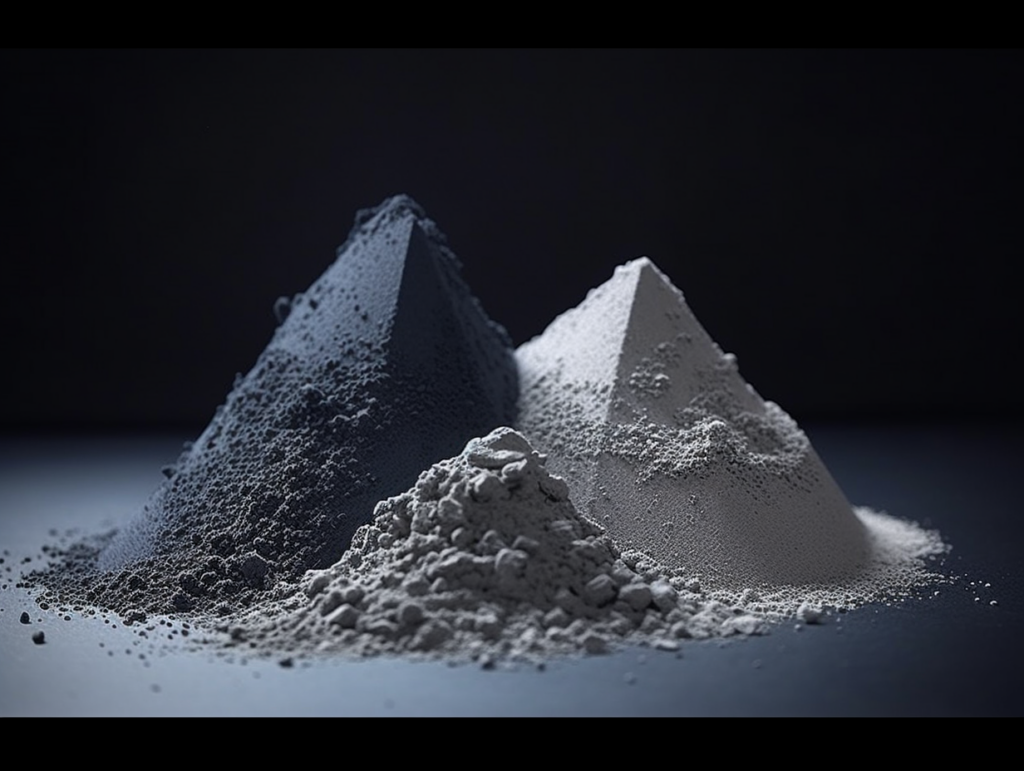
Overview of High Entropy Alloy Powder
High entropy alloy powder refers to powder forms of HEAs produced through gas atomization, mechanical alloying, electrolysis, chemical reduction, etc. HEA powder exhibits the characteristic properties of these advanced alloys in a powder form that enables manufacturing of HEA parts through methods like hot isostatic pressing, extrusion, metal injection molding, laser/electron beam melting, and thermal spraying.
Some key advantages of HEA powder include:
- Flexibility to tailor composition and tune properties
- Ability to produce novel HEA compositions difficult by ingot metallurgy
- Excellent consolidation and performance in powder consolidation processes
- Near-net-shape fabrication of intricate parts
- Unique microstructures and properties from rapid solidification during powder production
HEA powder has emerged as an important feedstock material for additive manufacturing of HEA parts with complex geometries for aerospace, automotive, biomedical etc. industries.
Types of High Entropy Alloy Powder
Many different HEA systems and compositions have been developed into powder forms. The most common types of HEA powder include:
Alloy System | Compositions | Key Properties |
---|---|---|
AlCoCrCuFeNi | AlCoCrCuFeNi, AlCoCrCuNi, AlCoCrFeNi etc. | Excellent strength, ductility, fracture toughness |
AlCoCrFeNi | Al0.5CoCrFeNi, AlCoCrFeNi etc. | Outstanding yield strength, wear resistance |
AlCrFeMnNi | AlCrFeMnNi, AlCrFeNi etc. | Exceptional high temperature strength |
AlCrFeNiVx | AlCrFeNiV0.5, AlCrFeNiVx etc. | Superior hardness, wear resistance |
CoCrFeMnNi | CoCrFeMnNi, CoCrNi etc. | High strength, ductility, toughness |
CoCrCuFeNi | CoCrCuFeNi, CoCrFeNi etc. | Excellent mechanical properties at cryogenic temperatures |
CoCrFeNiPd | CoCrFeNiPd, CoCrFeNi etc. | Outstanding oxidation/corrosion resistance |
CoCrFeNiPd | Co0.5CrFeNiPd etc. | Excellent strength, ductility, fracture toughness |
High entropy alloys powder compositions can be tailored to achieve specific properties required for different applications. Popular HEA powder systems include AlxCoCrCuFeNi, AlxCoCrFeNi, AlCrFeNiVx, CoCrFeMnNi etc.
Characteristics of High entropy alloys powder
Key characteristics of HEA powder that determine their processing and performance:
Characteristic | Typical Values |
---|---|
Particle size | 10 – 150 μm |
Morphology | Spherical, satellite, irregular |
Flowability | Excellent, fair, poor |
Apparent density | 2 – 6 g/cc |
Tap density | 4 – 8 g/cc |
Oxygen content | 500 – 5000 ppm |
Nitrogen content | 100 – 1000 ppm |
- Particle size distribution and flowability are critical for powder consolidation processes. Smaller powder sizes (<45 μm) are preferred for better densification.
- Spherical morphology improves powder flow. Irregular powder can affect densification.
- Higher tap density improves powder packing and part density.
- Purity (low O and N) is important to achieve target compositions and properties.
Applications of High Entropy Alloy Powder
High entropy alloys powder has emerged as a key feedstock material for numerous applications:
Industry | Applications |
---|---|
Aerospace | Turbine blades, discs, gears, airframes |
Automotive | Pistons, valves, turbocharger parts |
Biomedical | Implants, prosthetics, medical devices |
Oil & gas | Well drilling parts, valves, downhole tools |
Power generation | Turbine blades, heat exchangers |
Tooling | Cutting tools, dies, tool inserts |
Some key advantages of HEA powder parts:
- Outstanding mechanical properties at elevated temperatures
- Improved hardness, strength, wear resistance
- Enhanced corrosion and oxidation resistance
- Parts with complex geometries made via AM
HEA powder has exceptional potential for fabricating high performance parts under extreme environments in aerospace, automotive, oil & gas, and power generation sectors.
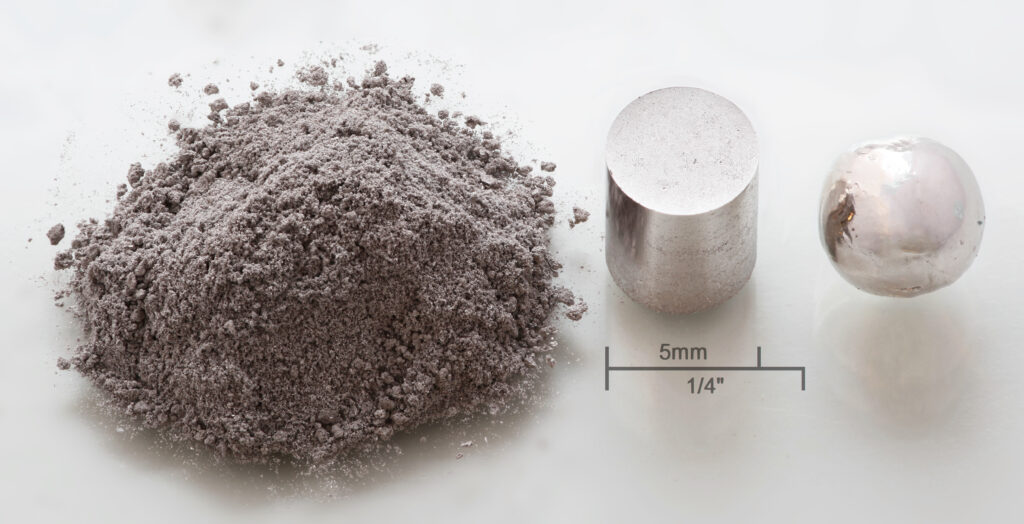
High entropy alloys powder Production Methods
High entropy alloys powder can be produced through gas atomization, mechanical alloying, chemical reduction, electrolysis and other methods.
Method | Description | Advantages | Limitations |
---|---|---|---|
Gas atomization | Rapid solidification of alloy melt into fine droplets | Spherical morphology, fine sizes | Limited alloys, high cost |
Mechanical alloying | Repeated welding and fracturing of powder mix | Simple, alloy flexibility | Contamination, agglomeration |
Electrolysis | Electrolytic reduction of aqueous salt mixture | Composition flexibility, purity | Slow production rate |
Chemical reduction | Chemical reduction of metal salt mixtures | Low cost, composition flexibility | Contamination, irregular powder |
- Gas atomization is the preferred method for clean, spherical HEA powder feedstock for AM. High cost limits composition flexibility.
- Mechanical alloying provides a simple, low cost route but with higher impurity levels.
- Electrolysis and chemical reduction offer greater flexibility in HEA compositions.
Specifications of High entropy alloys powder
Typical specifications of gas atomized High entropy alloys powder:
Parameter | Typical Range |
---|---|
Alloy compositions | AlxCoCrCuFeNi, AlxCoCrFeNi etc. |
Particle size distribution | 10 – 45 μm, 15 – 53 μm etc. |
Morphology | Spherical, near-spherical |
Apparent density | 2 – 4 g/cc |
Tap density | 4 – 6 g/cc |
Flow rate | 25 – 35 s/50g |
Oxygen | 300 – 1000 ppm |
Nitrogen | 50 – 150 ppm |
HEA powder intended for AM and other consolidation processes should meet strict specifications in terms of particle size distribution, morphology, flowability, density, and purity. Finer powder sizes between 10-45 μm are preferred.
High entropy alloys powder Suppliers
Some leading global suppliers of high entropy alloy powder include:
Supplier | Key Alloy Systems | Production Method | Particle Size | Pricing |
---|---|---|---|---|
Sandvik | AlCrFeNiCo, AlCrFeNiVx etc. | Gas atomization | 10 – 45 μm | $250 – $500/kg |
Praxair | AlCoCrCuFeNi, AlCoCrNi etc. | Gas atomization | 15 – 53 μm | $350 – $450/kg |
Carpenter | AlCoCrCuFeNi, CoCrNi etc. | Gas atomization | 10 – 45 μm | $300 – $600/kg |
LPW Technology | AlCoCrCuFeNi, AlCoCrNi etc. | Mechanical alloying | 10 – 150 μm | $100 – $250/kg |
Tekna | AlCoCrCuFeNi, AlCoCrFeNi etc. | Plasma spheroidization | 10 – 45 μm | $250 – $400/kg |
- Wide range in pricing based on production method, purity, particle size distribution, and alloy composition.
- Gas atomized HEA powder commanding higher prices due to spherical morphology and narrower size ranges preferred for AM.
Installation, Operation and Maintenance of High entropy alloys powder Production Equipment
Key aspects related to installation, operation and maintenance of HEA powder production systems:
Equipment | Installation Requirements | Operation Procedures | Maintenance |
---|---|---|---|
Gas atomization | Vibration isolation, chamber alignment, safety interlocks | Melting, nozzle flow rate, gas pressure, cooling | Nozzle cleaning, leak checks, spare parts |
Mechanical alloying | Mill alignment, cooling water, dust collection | Milling speed, time, ball-to-powder ratio | Barrel replacement, drive maintenance |
Electrolysis | Cell alignment, electrical connections, ventilation | Current density, temperature, electrolyte concentration | Electrode maintenance, electrolyte replacement |
Chemical reduction | Reactor setup, stirring, temperature control | Temperature, reagent concentrations and addition rate | Agitator servicing, reactor lining replacement |
- Powder production facilities require extensive installation to ensure proper configuration, safety, and controlled environments.
- Strict standard operating procedures during powder production runs are critical for quality, safety, and consistency.
- Regular preventive maintenance of all equipment is essential for maximizing production efficiency and minimizing downtime.
How to Select A High entropy alloys powder Supplier
Key factors in selecting a supplier for HEA powder:
- Expertise: Experience with wide range of HEA alloys and powder production processes
- Quality: Consistent powder characteristics meeting specifications
- Reliability: Proven capability for on-time delivery of orders
- Customization: Ability to tailor HEA compositions and powder attributes
- Pricing: Cost competitiveness, discounts for larger orders
- Testing: Complete in-house quality checks for each powder lot
- Certifications: ISO 9001 and other standards for quality assurance
- Technical support: Guidance on powder selection, storage, processing etc.
- Inventory: Ready stock availability for standard alloys
- Logistics: Infrastructure for timely worldwide delivery
It is critical to partner with a reputable HEA powder supplier having suitable expertise, quality systems, and production capacity to meet specific application needs reliably and cost-effectively.
Pros and Cons of HEA Powder
Advantages | Limitations |
---|
- Outstanding properties from high entropy effects| – High cost of gas atomized powder
- Flexible alloy compositions| – Limited availability of pre-alloyed powder
- Spherical morphology for excellent flowability|- Segregation during alloying for blended elemental powder
- Consolidation into full density parts|- Contamination issues in mechanical alloying
- Near-net-shape fabrication|- High oxygen/nitrogen pickup in gas atomization
- Microstructure control during rapid solidification|- Coarse powder for cast-and-crush mechanical alloying
- Performance benefits over ingot metallurgy alloys|- Inferior properties from improper processing

FAQs
Q: What are the main advantages of HEA powder over conventional alloys?
A: HEA powder provides unique advantages like exceptional strength-ductility combinations, high hardness, good wear resistance, high temperature stability, and corrosion resistance over conventional alloys.
Q: What particle size range is preferred for HEA powder in AM applications?
A: Finer HEA powder in the 10-45 μm range allows excellent flowability as well as facilitated melting and densification during AM processing.
Q: How is composition of the HEA powder controlled during manufacturing?
A: Strict process controls and quality checks are implemented during HEA powder production through methods like gas atomization to ensure that the intended alloy composition is achieved.
Q: What are the main challenges in HEA powder production?
A: Challenges include minimizing impurity pickup during processing, controlling particle size distribution, achieving spherical morphology, alloying of refractory elements, and preventing segregation in blended elemental powder.
Q: What safety precautions should be taken when handling HEA powder?
A: HEA powder may have hazards similar to conventional alloy powders. Precautions include using protective gear, avoiding skin contact, preventing dust inhalation, and using proper ventilation/containment during handling.
Conclusion
Key Takeaways:
- High entropy alloy powder provides a flexible feedstock for manufacturing advanced HEA components with unique properties.
- Gas atomization is the preferred method for clean, spherical HEA powder but is limited by high cost.
- Mechanical alloying allows flexibility in HEA compositions but causes impurity issues.
- HEA powder requires careful specification and quality checks by reputable suppliers before use in AM or other processes.
- Proper handling procedures are critical when working with HEA powder to minimize safety risks.
- With continued research and process improvements, HEA powder has exceptional potential for fabricating high performance components across industries.
In summary, high entropy alloy powder has emerged as an important new category of advanced metallic material providing unique opportunities to develop components with outstanding properties. Further advances in HEA powder quality, processing, applications and commercialization will enable widespread adoption of this novel class of alloys.