Silicon carbide (SiC) powder is a highly versatile material used in various industrial applications, ranging from abrasive materials to high-performance ceramics. It’s known for its exceptional hardness, thermal conductivity, and chemical stability, making it one of the most sought-after materials in engineering, manufacturing, and technological applications. In this detailed guide, we will explore the ins and outs of SiC powder, delving into its composition, characteristics, applications, and more, with a focus on making it easy to understand, yet technically rich.
Overview of SiC Powder
Before we dive into the specifics, let’s get a quick overview of silicon carbide powder. SiC is a compound made from silicon and carbon, and it’s one of the hardest known materials. In its powder form, it can be utilized in numerous ways, from creating abrasives and cutting tools to providing the raw material for ceramics, semiconductors, and automotive applications. Its unique properties make it ideal for uses where durability, heat resistance, and toughness are required.
Property | Value |
---|---|
Chemical Formula | SiC |
Hardness | 9.5 on the Mohs scale |
Thermal Conductivity | 120 W/mK |
Melting Point | 2,730°C (under atmospheric pressure) |
Density | 3.21 g/cm³ |
Electrical Conductivity | Semiconducting properties |
Oxidation Resistance | Up to 1,600°C |
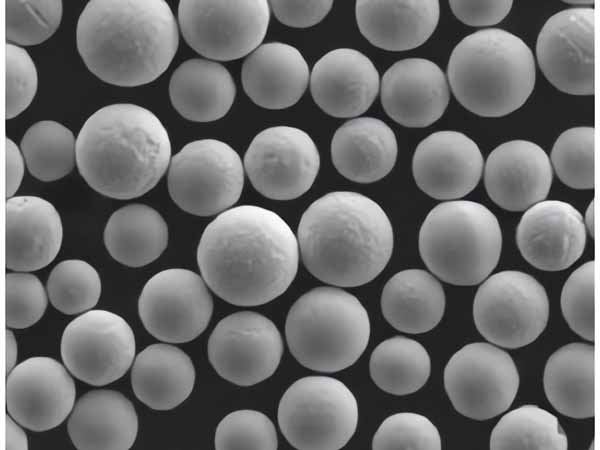
Composition of SiC Powder
Silicon carbide powder is produced through various methods, including the Acheson process, where silica sand and carbon are combined at high temperatures in an electric furnace. This process results in different grades of SiC powder, each with unique physical and chemical properties.
There are different types of SiC powders depending on the method of synthesis, purity levels, and intended applications. Some powders may have slight impurities like free carbon, silicon dioxide, or iron. Let’s break down the basic composition of SiC powder:
Type of SiC Powder | Composition |
---|---|
Black Silicon Carbide | 97% SiC, 3% impurities (mostly iron) |
Green Silicon Carbide | 99% SiC, extremely low impurities |
Nano-SiC Powder | 99.5% SiC, particle sizes between 1-100 nm |
Coarse-SiC Powder | 95-98% SiC, large grain sizes for abrasives |
Micro-SiC Powder | High-purity, fine powder used for electronics |
Characteristics of SiC Powder
SiC powder’s unique characteristics are what make it stand out as a superior material in various industries. Its hardness, heat resistance, and thermal conductivity make it indispensable for applications ranging from cutting tools to electronic devices.
Hardness and Durability
SiC is incredibly hard, ranking just below diamonds on the Mohs hardness scale, making it an excellent material for abrasives. It can cut through metals, ceramics, and even harder materials like titanium and tungsten.
Thermal Stability
Unlike many other materials, SiC powder maintains its strength and stability at very high temperatures, making it ideal for high-heat applications, including heat exchangers, furnace parts, and brake discs. Its ability to withstand temperatures of up to 2,730°C makes it a popular choice in extreme environments.
Chemical Resistance
SiC is chemically inert in most environments, meaning it doesn’t react with acids, alkalis, or other chemicals. This characteristic makes it suitable for use in chemically aggressive environments, such as in the production of semiconductors and industrial ceramics.
Characteristic | Details |
---|---|
Hardness | 9.5 on the Mohs scale |
Thermal Conductivity | 120 W/mK |
Oxidation Resistance | Effective up to 1,600°C |
Electrical Conductivity | Semiconductor; can be doped to be more conductive |
Corrosion Resistance | Chemically inert in most environments |
Specific Types of SiC Powder Models
Different SiC powder models are tailored to specific uses based on their composition, particle size, and purity. Below are 10 specific models of SiC powders and their detailed descriptions:
- F230 Black Silicon Carbide
- Description: This model is typically used for abrasive applications, such as grinding and polishing. It has a fine grain structure and is highly durable.
- Purity: 97% SiC
- Applications: Abrasives, cutting tools.
- GC Green Silicon Carbide
- Description: Green SiC is purer than black SiC, typically used in high-precision ceramics and in the electronics industry for semiconductor devices.
- Purity: 99% SiC
- Applications: Precision cutting, electronics.
- SiC Nanopowder
- Description: Ultra-fine SiC powder with particle sizes between 1 and 100 nanometers, ideal for nano-composites and coatings.
- Purity: 99.5% SiC
- Applications: Nanotechnology, coatings.
- 80 Grit Silicon Carbide
- Description: Coarse-grained powder ideal for tough abrasive jobs, such as grinding stones or hard metals.
- Purity: 95% SiC
- Applications: Grinding, sandblasting.
- SiC Ultra High Purity
- Description: SiC powder with an exceptionally high level of purity used in the production of high-performance ceramics.
- Purity: 99.9% SiC
- Applications: High-performance ceramics, electronics.
- F360 Silicon Carbide Powder
- Description: This fine-grade powder is used in lapping and polishing applications, where smooth surface finishes are required.
- Purity: 98% SiC
- Applications: Lapping, polishing.
- Silicon Carbide Micropowder
- Description: Fine powder with micron-sized particles, mainly used in coatings and wear-resistant components.
- Purity: 98% SiC
- Applications: Coatings, wear resistance.
- SiC Powder for Sintering
- Description: Powder specifically designed for sintering processes in ceramic production.
- Purity: 99% SiC
- Applications: Ceramic sintering, high-performance components.
- Black Silicon Carbide for Refractory
- Description: Coarse-grade powder used in the production of refractory materials.
- Purity: 95% SiC
- Applications: Refractories, kiln furniture.
- SiC 1000 Mesh Powder
- Description: Superfine powder ideal for creating smooth finishes in polishing applications.
- Purity: 99% SiC
- Applications: Polishing, high-precision finishing.
Applications of SiC Powder
SiC powder’s versatility comes from its unique combination of hardness, thermal conductivity, and chemical stability. Its applications span across multiple industries:
Application | Details |
---|---|
Abrasives | SiC’s hardness makes it ideal for grinding and cutting metals and other hard materials. |
Ceramics | High-purity SiC powder is used to produce durable, heat-resistant ceramic materials. |
Semiconductors | SiC is a vital material in high-power, high-temperature semiconductor devices. |
Automotive Parts | SiC is used in brake discs, clutches, and as coatings to reduce friction and wear. |
Refractories | SiC’s high melting point makes it suitable for use in kiln linings and other refractory items. |
Nanotechnology | SiC nanoparticles are used in advanced coatings and composite materials for enhanced performance. |
Heat Exchangers | SiC’s thermal conductivity makes it a perfect material for heat exchanger components. |
Lapping and Polishing | Fine SiC powders are used for lapping and polishing applications in precision industries. |
Advantages of SiC Powder
When compared to other materials like alumina or tungsten carbide, SiC powder holds several advantages.
- Better Hardness: SiC is harder than most materials used in industrial applications, second only to diamond.
- Superior Thermal Conductivity: SiC can dissipate heat quickly, making it ideal for high-temperature environments.
- Resistance to Oxidation: SiC remains stable in the presence of oxygen up to 1,600°C, making it highly resistant to oxidation and degradation over time.
- Cost-Effective: SiC is less expensive than diamond but provides comparable levels of hardness for abrasive applications.
- Lightweight: Compared to metals like tungsten carbide, SiC is lighter, which is a significant advantage in automotive and aerospace applications.
Limitations of SiC Powder
While SiC is an exceptional material, it does come with a few drawbacks:
- Brittleness: SiC is quite brittle compared to metals, meaning it can fracture under extreme stress.
- Difficult to Machine: Due to its hardness, SiC is difficult to machine and requires specialized tools and techniques.
- Limited Ductility: SiC’s low ductility makes it unsuitable for applications where flexibility is required.
Advantages | Disadvantages |
---|---|
Harder than most materials | Brittle and prone to fracture under stress |
High thermal conductivity | Difficult to machine without specialized equipment |
Resistant to oxidation | Limited ductility |
Cost-effective compared to diamond | |
Lightweight compared to tungsten carbide |
Specifications of SiC Powder
When purchasing SiC powder, you’ll come across various specifications, such as grain size, purity, and surface area. Below is a breakdown of the key specifications to consider:
Specification | Value Range |
---|---|
Purity | 95% to 99.9% SiC |
Grain Size | 1 nm to 10,000 microns |
Surface Area | 10 to 100 m²/g |
Particle Shape | Irregular, angular, spherical |
Color | Black or Green |
Pricing and Suppliers
The price of SiC powder varies depending on the purity, particle size, and the supplier. High-purity or specialized SiC powders tend to be more expensive due to their enhanced properties.
Supplier | SiC Powder Model | Price (per kg) |
---|---|---|
Saint-Gobain | Green SiC, 99% | $40 – $100 |
Washington Mills | Black SiC, 97% | $20 – $60 |
Fiven | SiC Nanopowder, 99.5% | $100 – $500 |
ESD-SiC | Ultra-High Purity SiC | $200 – $600 |
Superior Graphite | Sintering SiC, 99% | $50 – $150 |
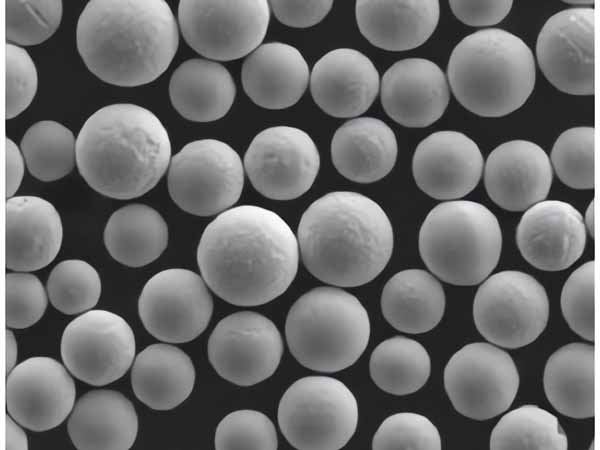
FAQs
Question | Answer |
---|---|
What is SiC powder used for? | SiC powder is used in a variety of industries for abrasives, ceramics, semiconductors, automotive parts, and heat exchangers. |
What is the difference between green and black SiC? | Green SiC is purer and used for high-precision applications like semiconductors, while black SiC is used for less demanding applications like abrasives. |
Is SiC powder expensive? | The price of SiC powder varies depending on purity and grain size. High-purity SiC is more expensive, while lower-purity options are more affordable. |
How is SiC powder produced? | SiC powder is typically produced through the Acheson process, which involves heating silica sand and carbon in an electric furnace. |
Can SiC powder be used in 3D printing? | Yes, SiC powder can be used in advanced 3D printing techniques, especially for creating ceramic and composite materials. |
Conclusion
SiC powder is an incredibly versatile material that plays a critical role in modern industries. Its hardness, chemical stability, and thermal conductivity make it invaluable in applications ranging from abrasives to semiconductors. By understanding its various forms, compositions, and uses, engineers and manufacturers can choose the best SiC powder model for their needs. Whether you’re looking for something to withstand high temperatures, cut through tough materials, or improve your ceramics, SiC powder is a material you can’t overlook!