Overview of Stellite 12 Powder
Stellite 12 powder is a cobalt-based alloy powder known for its incredible wear resistance, heat stability, and toughness, making it a popular choice in industrial applications where performance under extreme conditions is a must. This particular alloy combines cobalt with chromium, tungsten, and other elements to provide a versatile balance of hardness and wear resistance without compromising on toughness, even at elevated temperatures. Stellite 12 is often applied in processes like hard-facing, plasma spraying, and thermal spraying to enhance the surface durability of components used in aerospace, energy, automotive, and manufacturing industries.
This guide dives into the specifications, applications, pros and cons, and unique qualities of Stellite 12 powder, examining why it’s often the preferred choice over other metal powders for specific industrial uses. Additionally, we will break down the distinct models available under the Stellite family, comparing their features and helping you find the best-suited powder for your needs.
What is Stellite 12 Powder?
Stellite 12 is part of the well-known Stellite family of alloys, which are known for their wear resistance, high-temperature strength, and hardness. While other Stellite alloys focus on maximizing specific traits, Stellite 12 strikes a balance that makes it useful across a wide range of applications. The powder form of Stellite 12 allows for application in thermal spraying and other coating methods, making it suitable for environments where surface durability is critical.
Let’s look deeper into the composition, properties, and characteristics of Stellite 12 powder in the following sections.
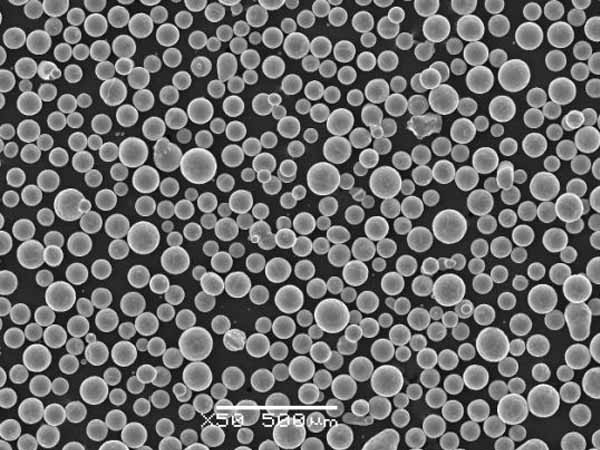
Composition of Stellite 12 Powder
The unique strength of Stellite 12 powder comes from its carefully balanced composition of cobalt, chromium, tungsten, and small amounts of other metals. Each element contributes specific properties to the alloy:
Element | Approximate Percentage (%) | Function |
---|---|---|
Cobalt (Co) | 50-70% | Base element providing high temperature strength and wear resistance |
Chromium (Cr) | 25-30% | Improves oxidation resistance and wear resistance |
Tungsten (W) | 4-5% | Increases hardness and toughness |
Carbon (C) | 1.5-2% | Adds hardness and enhances wear resistance |
Silicon (Si) | 1% | Enhances strength at high temperatures |
Nickel (Ni) | Up to 1% | Improves resistance to corrosion |
Key Properties of Stellite 12 Powder
Stellite 12 powder offers several distinct properties that make it an industry favorite for wear-resistant applications. Below are the critical properties of this alloy:
Property | Description |
---|---|
High Hardness | Stellite 12 maintains hardness in the range of 40-45 HRC, making it effective for abrasion resistance. |
Excellent Wear Resistance | Ideal for conditions that demand extreme abrasion and friction handling, like cutting tools. |
High-Temperature Stability | Performs well at elevated temperatures, up to approximately 600°C, without losing hardness. |
Oxidation Resistance | With high chromium content, it resists oxidation, making it durable in high-heat environments. |
Impact Toughness | Compared to harder Stellite powders, Stellite 12 offers moderate impact resistance, striking a balance between hardness and durability. |
Advantages of Stellite 12 Powder
So, why choose Stellite 12 powder over other metal alloys? Here are some benefits:
- Versatile Hardness and Toughness: Stellite 12 provides a rare mix of hardness and toughness, making it an excellent choice for wear applications that demand both properties.
- Heat Resilience: Unlike softer powders, Stellite 12’s strength doesn’t degrade under high temperatures, which is critical in industrial environments with high heat or friction.
- Corrosion and Oxidation Resistance: Its high chromium content protects against rust and oxidation, extending component life and reducing maintenance costs.
- Cost Efficiency: While Stellite alloys are not the cheapest, the balance Stellite 12 offers between price and performance makes it an economical choice for demanding applications.
Types and Models of Stellite Powder
Stellite comes in various formulations, each tailored to meet different industrial requirements. Below is a list of popular Stellite powders, including Stellite 12, with a summary of each model’s key characteristics:
Model | Composition | Key Feature | Common Applications |
---|---|---|---|
Stellite 1 | High Cobalt, Chromium, Tungsten | Maximum hardness and wear resistance | Cutting tools, wear-resistant overlays |
Stellite 6 | Cobalt, Chromium, Carbon | Balance of wear resistance and toughness | Valves, pump shafts, and aerospace components |
Stellite 6B | Similar to Stellite 6 with Boron addition | Improved corrosion resistance | Industrial machinery, chemical handling |
Stellite 12 | Cobalt, Chromium, Tungsten, Carbon | High heat and wear resistance | Plasma sprayed coatings, thermal spray applications |
Stellite 20 | Higher Carbon than Stellite 6 | Better wear resistance at high temperatures | Automotive valve seats, metal-on-metal wear surfaces |
Stellite 21 | Cobalt with lower carbon content | Good ductility and impact resistance | Medical implants, plastic injection molding |
Stellite 31 | Molybdenum addition | Increased corrosion resistance | Marine applications, chemical processing |
Stellite 3 | Very high hardness | Superior wear resistance in abrasive conditions | Sand and gravel industry, drilling equipment |
Stellite 4 | Harder than Stellite 6 | High wear resistance with toughness | Bearings, seal rings, and valve seats |
Stellite 190 | High Nickel alloy with Boron | Excellent corrosion and oxidation resistance | Aerospace, chemical, and food processing equipment |
Applications of Stellite 12 Powder
Stellite 12 powder is preferred for various industrial applications due to its unique combination of properties. Here’s a breakdown of its common uses and why it’s chosen for each:
Application | Why Stellite 12 is Used |
---|---|
Cutting Tools | High hardness and wear resistance make it ideal for heavy-duty cutting. |
Thermal Spray Coatings | Provides durable, heat-resistant coatings in industrial equipment. |
Aerospace Components | Performs well under high heat and friction in aircraft engines. |
Automotive Engine Valves | Stellite 12’s wear resistance prolongs valve life under high-temperature stress. |
Pump Shafts | Maintains structural integrity and resists abrasion in fluid-based machinery. |
Plasma Spray Processes | Ideal for surface-hardening, enhancing durability in extreme working environments. |
Specifications, Grades, and Sizes of Stellite 12 Powder
For industries that rely on precision materials, understanding the specifications, available grades, and sizes of Stellite 12 powder is crucial. Different grades and particle sizes suit various applications, from coatings to component manufacturing. Below is a comprehensive table detailing the specifications, common grades, and particle sizes available for Stellite 12 powder.
Specification Aspect | Details |
---|---|
Standard Specifications | Conforms to ASTM B815 for cobalt-chromium-tungsten alloys in powdered form |
Particle Sizes | Typically available in 15-45µm, 45-75µm, and 75-106µm ranges, depending on application requirements |
Grades | Stellite 12 powder is usually graded based on particle size distribution and purity levels |
Melting Point | Approximately 1,260°C (2,300°F) |
Hardness | 40-45 HRC when applied via spray or thermal coating |
Density | 8.5-8.9 g/cm³ |
Flowability | High flowability to ensure uniform application in thermal spraying processes |
Packaging | Available in 1kg, 5kg, and 25kg containers; bulk packaging may be offered by select suppliers |
Storage Requirements | Should be stored in a dry, cool place, with humidity-controlled environments to prevent clumping |
Suppliers and Pricing for Stellite 12 Powder
The price of Stellite 12 powder can vary based on supplier, region, order quantity, and packaging. Below is a table with details on some well-known suppliers and general pricing trends. Note that prices are approximate and may fluctuate based on market conditions.
Supplier | Approximate Price Range | Packaging Options | Special Offers |
---|---|---|---|
Kennametal Inc. | $120-$150 per kg | 1kg, 5kg, 25kg containers | Bulk discounts available |
Höganäs AB | $130-$160 per kg | Custom packaging available | Volume pricing for large orders |
Praxair Surface Technologies | $115-$145 per kg | 1kg, 10kg | Frequent-buyer discounts |
Oerlikon Metco | $125-$155 per kg | Standard and bulk packaging | Special pricing for frequent orders |
Carpenter Technology | $135-$165 per kg | Customizable packaging | Subscription-based pricing |
International Metal Powders | $120-$150 per kg | Flexible options | Special pricing for academic orders |
Pros and Cons of Stellite 12 Powder
Understanding the strengths and weaknesses of Stellite 12 powder can guide industries in choosing the best material for their applications. Here’s a rundown of the key pros and cons of using Stellite 12 powder.
Pros | Cons |
---|---|
High Wear Resistance: Stellite 12 powder has excellent abrasion resistance, ideal for demanding applications. | Cost: As a premium alloy powder, it can be more expensive than other metal powders. |
Heat Resistance: Performs well in high-temperature environments, maintaining its properties up to 600°C. | Hardness vs. Ductility: The high hardness means it’s less ductile, so impact resistance can be limited. |
Corrosion Resistance: Chromium in the composition provides strong oxidation and corrosion resistance. | Specialized Storage: Requires specific storage conditions to prevent clumping. |
Versatile Application: Can be used for coatings, hard-facing, and even high-wear components like valves and pumps. | Processing Requirements: May require specialized thermal spraying or coating equipment. |
Extended Component Life: Reduces maintenance costs by enhancing the durability of components. | Difficult to Machine Post-Application: Once applied, it’s tough to machine or rework. |
Comparison with Other Stellite Powder Models
Stellite 12 is not the only alloy powder in the Stellite family. To make the best choice, it’s essential to compare it with other Stellite models. Here’s how Stellite 12 stacks up against popular alternatives like Stellite 6, Stellite 20, and Stellite 21.
Model | Hardness (HRC) | Key Features | Best Suited Applications | Comparison with Stellite 12 |
---|---|---|---|---|
Stellite 6 | 35-40 HRC | Good balance of wear resistance and ductility | Valve seats, aerospace parts, pump shafts | Stellite 12 offers higher hardness, better for abrasion |
Stellite 20 | 40-45 HRC | High-temperature resistance and wear durability | Engine valves, high-wear surfaces | Similar hardness, but Stellite 20 has more carbon for high-temp stability |
Stellite 21 | 30-35 HRC | Superior impact resistance, lower carbon content | Medical implants, chemical processing | Stellite 12 is harder but less impact-resistant |
Stellite 1 | 50-55 HRC | Maximum hardness, less ductility | Cutting tools, extreme abrasion applications | Stellite 12 offers a middle ground between hardness and ductility |
Stellite 31 | 32-38 HRC | High corrosion resistance with molybdenum addition | Marine and chemical processing industries | Lower hardness than Stellite 12, better corrosion resistance |
Applications and Use Cases of Stellite 12 Powder
Stellite 12 powder is versatile, but where it truly shines is in applications demanding wear resistance and durability at elevated temperatures. Here’s an expanded look at some of its most common applications and why it’s selected for each:
Industry | Application | Reason for Choosing Stellite 12 |
---|---|---|
Aerospace | Jet engine components | Resists high temperatures and maintains strength under intense heat and pressure. |
Automotive | Engine valves, valve seats | High wear resistance to extend the life of engine components exposed to friction. |
Manufacturing | Cutting tools, milling tools | Hardness and abrasion resistance make it ideal for heavy-duty cutting processes. |
Oil and Gas | Drill components, pump shafts | Can withstand abrasive environments and retain hardness in high-pressure conditions. |
Medical | Surgical tools, implants | High biocompatibility in certain Stellite grades (notably Stellite 21). |
Chemical Processing | Valves, seal rings | Resists corrosion and wear, even in chemically harsh environments. |
Power Generation | Turbine blades, boilers | Maintains stability under thermal cycling, enhancing durability of power components. |
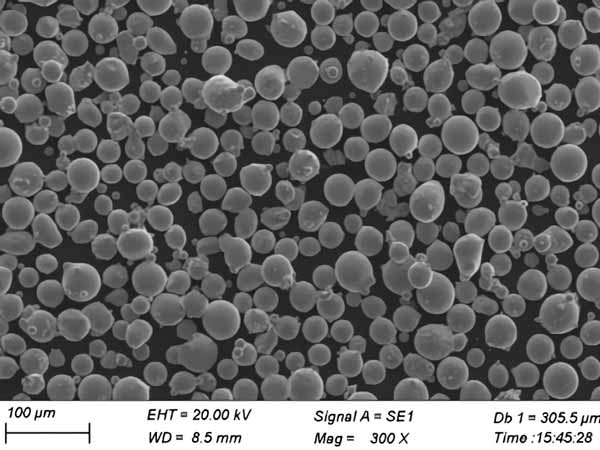
FAQ
For quick reference, here are answers to frequently asked questions about Stellite 12 powder:
Question | Answer |
---|---|
What is Stellite 12 powder mainly used for? | It’s widely used for coatings and overlays in high-wear and high-heat applications. |
How does Stellite 12 compare to Stellite 6? | Stellite 12 is harder, making it better for abrasive applications, while Stellite 6 has more ductility. |
What industries commonly use Stellite 12 powder? | Aerospace, automotive, oil & gas, and manufacturing industries are primary users. |
Can Stellite 12 be used for medical applications? | While Stellite 21 is preferred for biocompatibility, Stellite 12 may still be used in select cases. |
How should Stellite 12 powder be stored? | It should be stored in a cool, dry, and humidity-controlled environment to prevent clumping. |
What is the typical hardness of Stellite 12? | Stellite 12 typically has a hardness of 40-45 HRC. |
Is Stellite 12 resistant to corrosion? | Yes, it has high corrosion resistance due to its chromium content. |
Can Stellite 12 be used for thermal spray applications? | Absolutely, it’s commonly applied via plasma spray and other thermal spray methods. |
What are the main limitations of Stellite 12? | It is costly and can be difficult to machine once applied; specialized equipment is needed for application. |
Is Stellite 12 powder eco-friendly? | While durable, it is not inherently eco-friendly; disposal and production have environmental impacts. |