TC18 powder refers to a tungsten carbide grade containing 18% cobalt binder widely used in manufacturing cutting tools, dies and wear parts. This guide provides an overview of TC18 powder including its properties, applications, manufacturing process, specifications, installation, operation and maintenance procedures, selection criteria, pros and cons, and FAQs.
Introduction to TC18 Powder
TC18 powder consists of:
- 82% tungsten carbide (WC) which provides extreme hardness and wear resistance
- 18% cobalt (Co) that acts as the ductile binder matrix
Key properties of TC18 powder:
- Excellent hardness in the 89-93 HRA range
- High strength and fracture toughness
- Wear and abrasion resistance
- Resistance to deformation at elevated temperatures
- Chemical inertness in most environments
TC18 finds wide usage in metal cutting tools, forming dies, wear parts and mining equipment.
Applications of TC18 Powder
TC18 powder is suitable for the following applications that require hardness and wear resistance:
Industry | Applications |
---|---|
Automotive | Cutting and milling tools, drawing dies |
Aerospace | Cutters, reamers, drilling tools |
Oil & gas | Seals, valves, downhole tools |
Mining | Crushers, drill bits, sieves, dies |
Metal fabrication | Punches, drawings dies, trim tools |
Woodworking | Cutters, saw blades, planning tools |
Benefits offered by TC18 parts:
- Long and consistent tool life
- High productivity machining and forming
- Dimensional stability at high temperatures
- Resistance to abrasive and adhesive wear
- Strength and fracture resistance
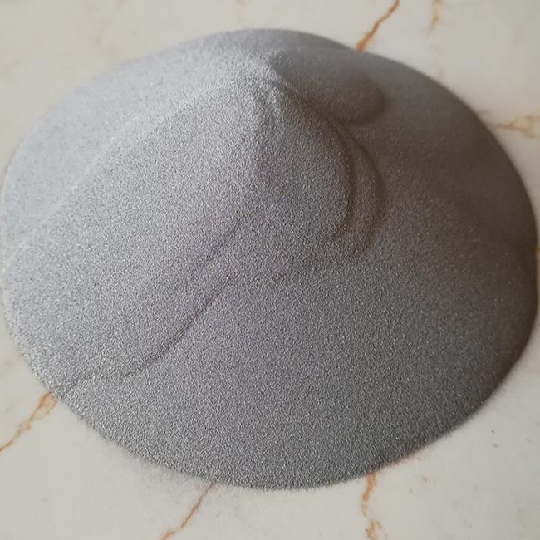
TC18 Powder Manufacturing Process
TC18 powder is manufactured through the following stages:
- Milling – Raw tungsten carbide and cobalt powders are wet milled to achieve uniform particle size of 1-5 microns.
- Drying – The milled powder slurry is dried to remove the milling liquid medium.
- Blending – The WC and Co powders are blended in the correct 82/18 ratio along with process additives.
- Compaction – The powder blend is compacted into a solid green part using pressures up to 2 tons/sq.in.
- Sintering – Green compacts are sintered at 1400-1500°C in a controlled atmosphere furnace to achieve partial melting and densification.
- Grinding – The sintered part is ground to the final dimensions with smooth surface finish.
Specifications of TC18 Powder
TC18 powder has the following technical specifications:
Parameter | Specification |
---|---|
Tungsten carbide | 82% |
Cobalt | 18% |
Carbon content | 5.5-6.2% |
Iron content | 1% max |
Density | 13.9-15.3 g/cc |
Porosity | Less than 2% |
Hardness range | 89-93 HRA |
Transverse rupture strength | 150,000 psi minimum |
The powder composition, particle size, carbon content and other characteristics can be customized as per application requirements.
TC18 Powder Suppliers
Some of the major global suppliers of TC18 tungsten carbide powder include:
Company | Location |
---|---|
Sandvik | Sweden |
Ceratizit | Luxembourg |
Mitsubishi Materials | Japan |
Hyperion Materials | USA |
Kennametal | USA |
Guangdong Xianglu | China |
Reputable suppliers use quality raw materials and advanced manufacturing processes to achieve powder consistency. Some provide customization services.
TC18 Powder Pricing
Price Range: $45 to $85 per kg
Pricing depends on factors like:
- Purity levels
- Required particle size distribution
- Order volumes
- Additional processing or quality checks
- Supplier brand value
Economical for medium to high production volumes due to long and consistent tool life.
Installation of TC18 Powder Equipment
Key factors for TC18 powder processing equipment installation:
Parameter | Guidelines |
---|---|
Ventilation | Dust extraction hoods at discharge points |
Explosion proofing | Prevent sparks in powder handling areas |
Grounding | Ground all conductive equipment and piping |
Safety systems | Leak detectors, fire and gas monitoring |
Utilities | Compressed air, inert gas, power supply |
Containment | Minimize spills and control leak points |
Automation | Automated powder feeding and controls |
Critical considerations are explosion prevention, operator safety from dust exposure, and preventing powder contamination during handling.
Operation and Maintenance of TC18 Powder Systems
Activity | Instructions |
---|---|
Filling | Controlled inert gas purging, verify seals post filling |
Processing | Follow SOPs for pressure, temperature, flows |
Inspection | Check for blocked filters, equipment wear, leaks |
Maintenance | scheduled lubrication, replace worn components |
Housekeeping | Clean equipment and area regularly |
Safety | Ensure proper PPE, ventilation, compliance |
Key operation guidelines:
- Maintain inert atmosphere below 5% oxygen
- Prevent powder accumulation on surfaces
- Inspect transfer lines and filters for blockages
- Validate all safety interlocks and devices
- Follow protocols for TC powder material handling
Selecting a TC18 Powder Supplier
Factors to evaluate when selecting a TC18 powder supplier:
Criteria | Evaluation Parameters |
---|---|
Quality | Powder composition consistency, certification |
Technical expertise | Staff knowledge, test methods |
Manufacturing | Process controls, automation, QC |
R&D | New product development, customization skills |
Logistics | On-time delivery record, responsiveness |
Pricing | Competitive pricing, discounts for volume |
Compliance | ISO 9001 certification, regulatory standards |
Service | Technical support response time |
Pros and Cons of TC18 Powder
Pros | Cons |
---|---|
Excellent hardness and wear resistance | Brittle with lower fracture toughness than steel |
High strength across range of temperatures | Sensitive to strain variations |
Good chemical and corrosion resistance | Prone to oxidation at higher temperatures |
Stable microstructure up to 1000°C | Higher cost than simple tool steels |
Enables high productivity machining | Limited recyclability after use |
The extreme hardness and wear resistance justify using TC18 despite the higher cost in demanding applications.
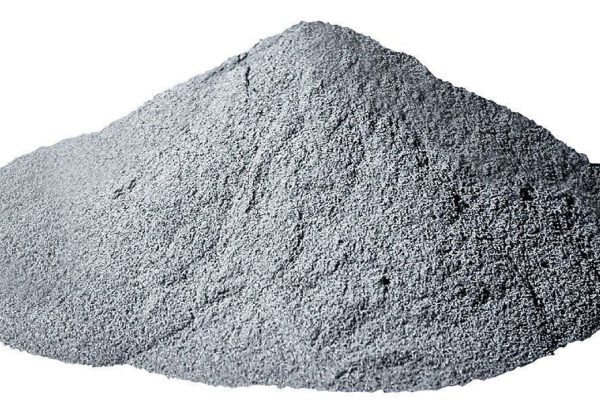
FAQs
Q: What is the typical grain size of TC18 powder?
A: The typical grain size of TC18 powder ranges from 1 to 5 microns after the milling stage. Ultrafine grain size improves performance.
Q: What is the role of carbon in tungsten carbide powder?
A: Carbon helps control grain growth of tungsten carbide particles during sintering. Optimum carbon content ensures fine grain size for maximum hardness and strength.
Q: What are the main applications of TC18 grade powder?
A: TC18 is widely used in cutting tools, milling inserts, drawing dies, woodworking tools, seal rings, bearings and other wear parts across industrial sectors.
Q: What are the safest methods for handling TC powder?
A: Use inert gas glove boxes, avoid ignition sources, ground equipment, employ spark detectors and explosion vents, follow fire safety protocols, and use PPE.
Q: How does TC18 compare to other tungsten carbide grades?
A: TC18 provides well-balanced hardness, strength and toughness. Lower cobalt grades like TC12 are harder but more brittle. Higher cobalt like TC22 provides increased toughness.
Q: What are the health risks associated with tungsten carbide powder exposure?
A: Possible lung diseases, asthma, breathing issues due to dust inhalation. Cobalt component linked to cancer with prolonged exposures. Strict safety protocols are essential.
Q: What standards apply to TC powder composition and quality testing?
A: Key standards are ASTM B771, ISO 513, and ISO 4499 that cover composition verification, hardness testing, microstructure analysis and other powder characteristics.
Q: Does TC18 require special storage or shelf life precautions?
A: TC18 powder is stable and does not degrade easily. But very dry storage conditions are recommended to prevent any moisture ingress.
Q: What are emerging trends in TC18 grade powder?
A: Nanoscale and ultrafine grain size TC18 powder, high-purity grades with lower impurities, and cobalt-free grades for special applications.
Conclusion
TC18 tungsten carbide powder possesses an exceptional combination of hardness, strength, and wear resistance necessary in cutting tools and wear parts used in demanding conditions. This guide summarizes TC18 powder composition, manufacturing, applications, specifications, installation factors, operation and maintenance protocols, supplier selection criteria, pros and cons, and common FAQs to support engineering and procurement teams adopt this material. With continuous advancements in powder quality and equipment design, TC18 is expected to proliferate across metalworking and general engineering sectors requiring reliable performance.