What Is 3D Printing?
3D printing, also known as additive manufacturing, is a process that enables a three-dimensional solid object of any shape to be rapidly realized through a digital model. The essence of 3D printing is to generate a digital model file by editing a series of digital slices of a specific processing style through computer-aided design software, and then to use specific additives as bonding materials in accordance with the dimensions of the model drawing, using specific molding equipment, i.e., 3D printers, to make solid metal powders or highly malleable substances in powder, liquid or filament form. Layered processing, stacking molding so that the raw material will melt and increase these thin layers layer by layer, so as to finally “print” a real and three-dimensional solid object.
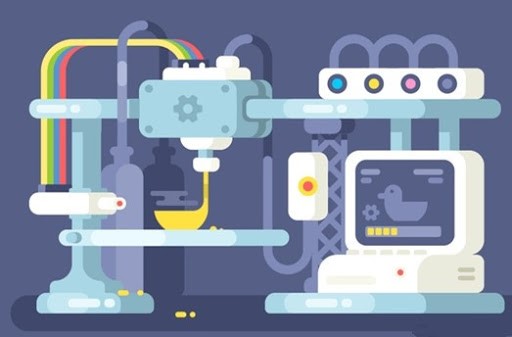
The 3D Printing Materials
The world’s leading experts in the 3D printing industry define metal powder for 3D printing as a group of metal particles less than 1mm in size. This includes single metal powders, alloy powders, and certain refractory compound powder alloys with metallic properties, bronze alloys, industrial steels, stainless steels, titanium alloys, and nickel-aluminum alloys. However, in addition to good plasticity, metal powders for 3D printing must also meet the requirements of fine particle size, narrow particle size distribution, high sphericity, good flowability, and high apparent density.
The influence of metal powder particle shape, particle size and its distribution on the finished 3D printed product
In the process of metal powder preparation, the powder particles will take different shapes with different preparation methods, such as spherical, subspherical, polygonal, porous spongy, dendritic, etc. The particle shape of the powder directly affects the flowability and bulk density of the powder, which in turn has an impact on the properties of the prepared metal parts.
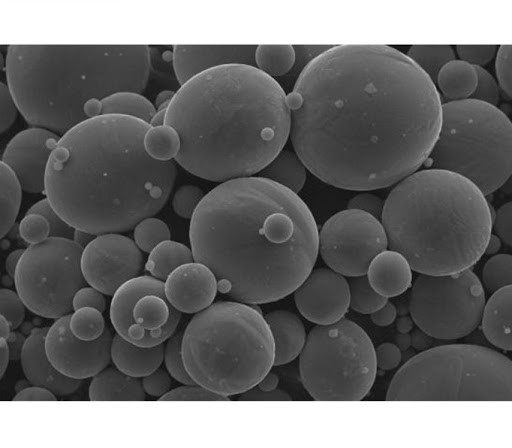
Spherical or nearly spherical powders have good fluidity, are less likely to clog the powder supply system during printing, and can be spread into thin layers, thereby improving the dimensional accuracy and surface quality of 3D printed parts, as well as the density and tissue uniformity of the parts, making them the preferred raw material shape type for 3D printing. However, it should be noted that spherical powders have low particle packing density and large voids, making the parts less dense, which also affects the forming quality.
The smaller the particle size of metal powder, the more conducive to the smooth sintering, because the smaller the particle size, the larger the specific surface area, the greater the driving force of sintering. In addition, the voids between the fine powder particles are small, and the connection between adjacent layered powder is tight, which is conducive to improving the sintering densification and sintering strength. Small particles of metal powder can also fill the voids of large particles, which can improve the stacking density of the powder, thus contributing to improving the surface quality and strength of the printed metal parts. However, not the finer the particles the better, if too many fine particles, in the sintering process is easy to appear “spheroidization” phenomenon, easy to cause the uneven thickness of the laying powder. The so-called “spheroidization” phenomenon, that is, in order to make the molten metal liquid surface and the surrounding media surface of the system with the minimum free energy, under the action of surface tension, the shape of the metal liquid surface to the spheroid surface transformation of a phenomenon. Spheroidization” usually prevents the metal powder from solidifying to form a continuous smooth pool after melting, thus forming a loose and porous part, resulting in molding failure.