Overview of Ti22Al25Nb Powder
Ti22Al25Nb is an alpha-2 titanium aluminide alloy powder containing 22% aluminum, 25% niobium and the balance titanium. It exhibits an attractive combination of properties:
- Low density – 3.7 g/cm3, almost half that of nickel superalloys
- Excellent high temperature strength and creep resistance
- Good oxidation and corrosion resistance
- Capability for service temperatures up to 750°C
These characteristics make Ti22Al25Nb suitable for manufacturing lightweight, high-performance components for aerospace, automotive, and other applications via additive manufacturing or powder metallurgy.
Types of Ti22Al25Nb Powder
Ti22Al25Nb alloy powder can be categorized into the following main types based on production method and morphology:
Type | Description | Particle Shape | Size Range | Production Method |
---|---|---|---|---|
Gas Atomized | Irregular spheroidal powder | Mostly spherical | 15-75 μm | Gas atomization |
Plasma Atomized | Highly spherical powder | Highly spherical | 10-45 μm | Plasma atomization |
Blended | Mixture of gas atomized and irregular particles | Mixed morphology | 15-125 μm | Mechanical blending |
Alloyed | Prealloyed powder with homogeneous composition | Spherical or irregular | 15-105 μm | Gas/plasma atomization of prealloyed melt |
Plasma atomized and prealloyed powders offer more homogeneous properties but are costlier. Blended and gas atomized powders provide a cheaper option.
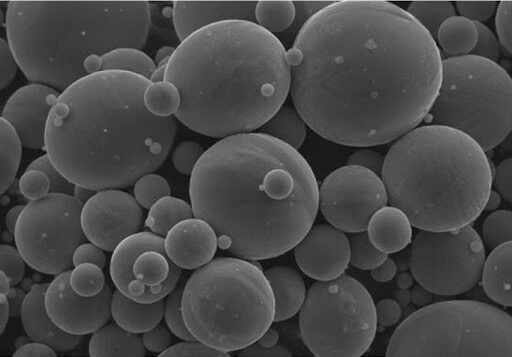
Characteristics and Properties of Ti22Al25Nb Powder
Ti22Al25Nb demonstrates an exceptional mix of physical, mechanical, and thermal properties:
Property | Description |
---|---|
Density | 3.7 g/cm3 |
Melting Point | 1540°C |
Electrical Resistivity | 182 μΩ-cm |
Young’s Modulus | 151 GPa |
Poisson’s Ratio | 0.34 |
Tensile Strength | 500-900 MPa |
Compressive Strength | 1000-1600 MPa |
Hardness | 350-450 HV |
Fracture Toughness | 25-35 MPa-m^1/2 |
Thermal Conductivity | 24 W/m-K |
Thermal Expansion Coefficient | 11 x 10^-6 K^-1 |
Oxidation Resistance | Excellent up to 750°C |
The properties make it suitable for high-stress elevated temperature applications in corrosive environments across sectors.
Applications of Ti22Al25Nb Alloy Powder
Ti22Al25Nb powder can be used to fabricate components for the following applications:
Aerospace: Turbine blades, discs, casings, heat shields, engine parts
Automotive: Turbocharger wheels, valves, connrods, springs, exhaust components
Industrial Gas Turbines: Combustor liners, nozzles, rotors, casings
Chemical Industry: Valves, pumps, heat exchangers for corrosive environments
Biomedical: Orthopedic and dental implants, surgical instruments
Sports & Leisure: Golf club heads, bicycle parts, motorcycling components
Electronics: Lead frames, connectors, packaging for thermal management
Energy: Nuclear, geothermal, solar thermal equipment demanding high temperature strength
The low density and high temperature properties provide significant benefits over conventional nickel and steel alloys in reducing weight and improving efficiency.
Specifications of Ti22Al25Nb Powder
Ti22Al25Nb powder must conform to the following specifications:
Parameter | Specification | Test Method |
---|---|---|
Particle size | 15-150 μm | Laser diffraction, sieve analysis |
Particle shape | Spherical, angular, or blended | SEM imaging |
Apparent density | > 2.5 g/cm3 | ASTM B212 |
Tap density | > 3.5 g/cm3 | ASTM B527 |
Flow rate | > 25 s/50g | ASTM B213 |
Composition | Al 20-23 wt%, Nb 23-27 wt%, Ti balance | ICP-OES |
Oxygen content | < 2000 ppm | Inert gas fusion |
Nitrogen content | < 500 ppm | Inert gas fusion |
Carbon content | < 1000 ppm | Combustion analysis |
Hydrogen content | < 100 ppm | Inert gas fusion |
The requirements ensure high powder quality for additive manufacturing, metal injection molding, and press and sinter processing.
Design Considerations for Ti22Al25Nb Parts
Several design factors must be optimized when using Ti22Al25Nb powder:
- Minimum wall thickness should be 1-2 mm to ensure sufficient strength
- Generous fillets and tangent transitions should be used to avoid stress concentrations
- Draft angles ≥ 2° are recommended for ease of powder removal
- As-sintered surfaces will have lower finish than wrought products; post-processing may be required
- Dimensional tolerances down to ±0.2% are possible but ±0.5-1% is more typical
- A sintered density ≥ 95% is needed to achieve mechanical properties close to wrought alloys
- Heat treatment can be used to further enhance strength through precipitation hardening
- Critical features may need post-processing through hot isostatic pressing or machining
Careful consideration of these aspects during design enables high performance Ti22Al25Nb parts to be manufactured successfully and economically using powder metallurgy techniques.
Standards for Ti22Al25Nb Powder
Ti22Al25Nb powder must comply with the following standards:
Standard | Description |
---|---|
ASTM B981 | Standard specification for titanium alloys in powder form for MIM |
EN 10204 | Chemical analysis and test report requirements |
ISO 9001 | Quality management system requirements |
ISO 13485 | Quality management for medical devices |
AMS 4967 | Composition limits for titanium alloy powder |
Certification to standards for chemistry, quality systems, and testing provides assurance to customers that the powder meets specifications for the target application. Medical and aerospace applications have additional requirements.
Suppliers of Ti22Al25Nb Powder
Some leading global suppliers of Ti22Al25Nb powder include:
Supplier | Particle Size | Production Method | Key Features |
---|---|---|---|
AP&C | 15-45 μm | Plasma atomization | Highly spherical, prealloyed |
TLS Technik | 10-75 μm | Gas atomization | Cost-effective irregular powder |
Sandvik Osprey | 45-150 μm | Gas atomization | Blended and prealloyed options |
Praxair | 15-105 μm | Gas atomization | Capacity for large orders |
Carpenter Additive | 15-75 μm | Gas atomization | Optimized particle size distribution |
Factors like lead time, minimum order quantity, and location should also be considered when selecting a supplier. Some additional customization of powder may be needed to meet application requirements.
Pricing Estimates for Ti22Al25Nb Powder
Ti22Al25Nb powder is more expensive than titanium grades like Ti-6Al-4V due to higher niobium content and lower production volumes:
Powder Grade | Particle Size | Price Range |
---|---|---|
Irregular | 15-75 μm | $200-300/kg |
Spherical | 15-45 μm | $250-450/kg |
Alloyed | 15-75 μm | $300-500/kg |
Plasma Spheroidized | 15-45 μm | $400-600/kg |
- Prices decline significantly for bulk orders exceeding 100 kg.
- Special screening or blending to customize particle size distribution commands a premium.
- Premium spherical and prealloyed powders carry higher pricing.
- Quoted prices may fluctuate over time due to raw material and energy costs.
Installation and Maintenance of Ti22Al25Nb Powder Equipment
Special practices should be followed when installing powder handling systems and processing Ti22Al25Nb powder:
Activity | Procedure |
---|---|
Storage | Store sealed containers in a dry (<50% RH) environment at 18-25°C. First-in-first-out inventory management. |
Handling | Use appropriate PPE – gloves, respirator, goggles. Carefully pour powder to avoid spills. Ground all equipment. |
Installation | Qualify and validate all equipment. Check weighing, mixing, feeding, and sieving operation. |
Processing | Closely follow all parameter guidelines provided. Frequently check powder condition. |
Maintenance | Establish preventive maintenance schedule. Check seals, controls, filters periodically. Promptly address anomalies. |
Safety | Ensure fire suppression and explosion prevention systems are operational. Install blast walls if needed. |
Proper installation, operation, and maintenance are vital for safe handling of titanium powder and preventing process disruptions.
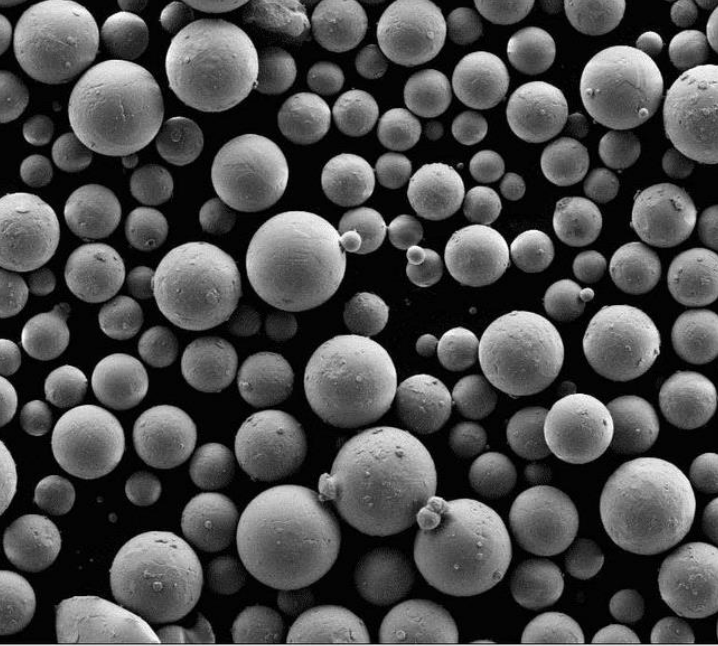
Selecting a Ti22Al25Nb Powder Supplier
Here are key factors to consider when selecting a Ti22Al25Nb powder supplier:
- Technical expertise in titanium powder production including alloying, gas atomization, quality control
- Range of powder types and sizes – spherical, prealloyed, blended, various particle size distributions
- Quality certifications – ISO 9001, ISO 13485, AS9100, etc. indicating rigorous quality control
- Batch testing capabilities – chemical assay, particle size analysis, microscopy, density, flow rate
- Customization capability – ability to provide special particle characteristics or tight tolerances
- Pricing – competitive pricing for both high and low volume purchases
- Lead time – short lead times essential for fast-paced research and prototyping
- Inventory – some stock availability for standard powders to avoid lead times
- Customer service – responsive technical support and open communication
- Distribution network – geographic proximity for reduced shipping time and cost
Established titanium powder producers with a broad product portfolio and inventory tend to best meet requirements.
Pros and Cons of Ti22Al25Nb Powder
Advantages
- Very high strength-to-weight ratio
- Excellent high temperature mechanical properties
- Good corrosion and oxidation resistance
- Enables lightweight engineered components
- Components can replace heavy steel or nickel parts
- Cost-effective compared to other titanium alloys
- Established supplier base for quality powder
Disadvantages
- Higher cost than steel, aluminum or nickel alloy powders
- Challenging to process due to reactivity of titanium
- Brittle behavior limits cold forming and machining
- Requires high levels of process control and operator skill
- Post-processing often needed to achieve final part properties
- Limited number of suppliers compared to common alloys
For applications where the benefits of low density and temperature capability outweigh the higher cost, Ti22Al25Nb powder is an attractive choice. But processing does require stringent controls.
Comparison of Ti22Al25Nb, TA15, and Ti6Al4V Powders
Ti22Al25Nb sits between TA15 and Ti6Al4V in terms of properties:
Alloy | Density | Strength | Ductility | Oxidation Resistance | Use Temperature | Cost |
---|---|---|---|---|---|---|
Ti22Al25Nb | Low | High | Medium | Good | High | High |
TA15 | Very low | Medium | Low | Excellent | Very high | Very high |
Ti6Al4V | Medium | Medium | High | Moderate | Medium | Low |
- Ti22Al25Nb provides the best all-round combination of strength, temperature capability, oxidation resistance and cost.
- TA15 is used for extreme temperature applications but is more brittle.
- Ti6Al4V offers higher ductility but lower service temperatures.
Thus, Ti22Al25Nb provides an optimal balance for most critical aerospace rotating components, turbine blades, and other high-performance applications.
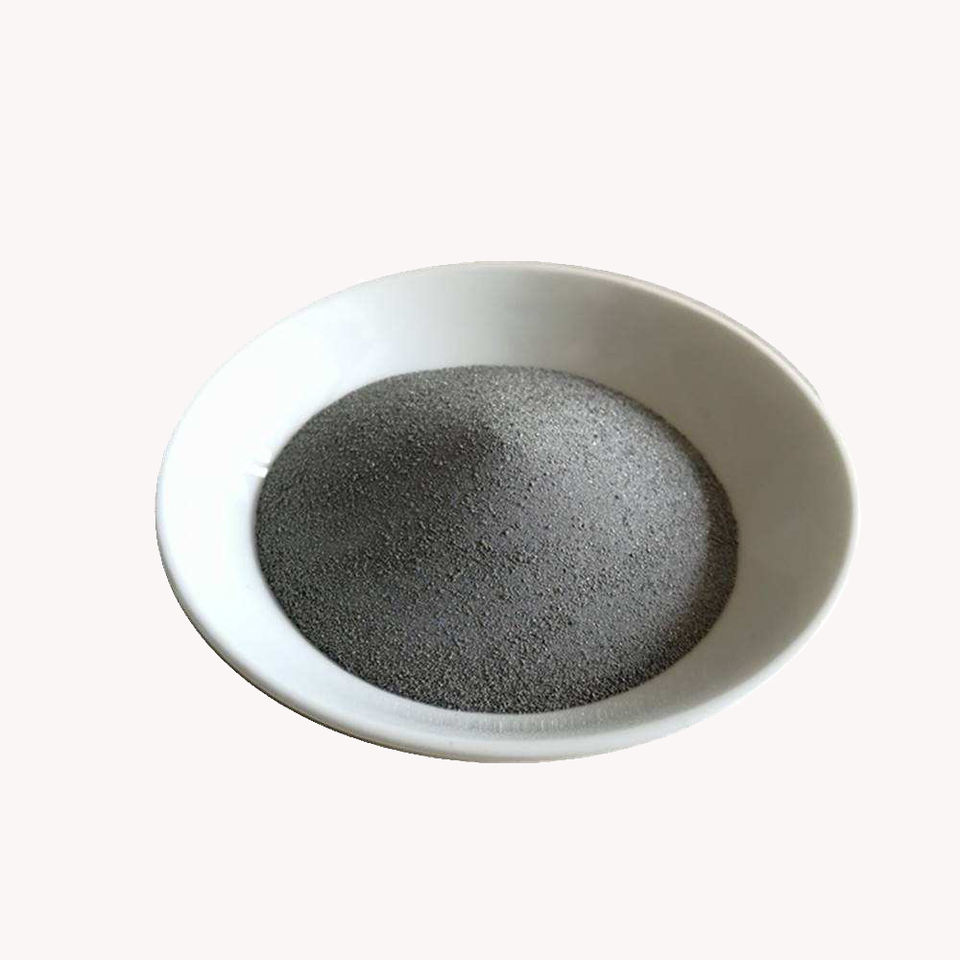
FAQ
What are the main benefits of Ti22Al25Nb over nickel superalloys?
Ti22Al25Nb offers a 40-50% lower density along with competitive high temperature mechanical properties up to 750°C. This provides significant weight savings.
What particle size range is recommended for additive manufacturing with Ti22Al25Nb?
A particle size range of 15-75 μm is typically recommended, with a majority between 45-75 μm, to achieve good powder bed packing and spreading. Finer particles below 10 μm can cause challenges.
Is hot isostatic pressing required after additive manufacturing with Ti22Al25Nb?
While not always necessary, HIPing can help maximize density, refine microstructure, and improve mechanical properties. HIP is recommended for critical aerospace components.
What type of powders provide the most homogeneous properties in Ti22Al25Nb?
Prealloyed gas or plasma atomized powders offer the most homogeneous distribution of alloying elements and stable properties.
How should Ti22Al25Nb powder be stored?
Ti22Al25Nb powder is highly reactive and must be stored in sealed containers under an inert argon atmosphere with moisture levels below 50% RH. Temperatures should be between 18-25°C.
What safety precautions are necessary for handling Ti22Al25Nb powder?
An enclosed system under inert gas, adequate PPE including respirators, electrically grounding all equipment, proper training of personnel, and fire suppression systems are essential when handling reactive titanium powder.