Titanium additive manufacturing (AM) powders enable 3D printing of strong, lightweight titanium components across aerospace, medical, and automotive sectors. This guide covers Ti AM powder compositions, characteristics, atomization production methods, applications, specifications, pricing, and comparisons.
Overview of Titanium AM Powders
Titanium AM powders refer to fine titanium particles specially optimized for additive manufacturing processes like laser powder bed fusion (L-PBF) and direct energy deposition (DED).
With high purity (>99% Ti), controlled particle size distribution, and good flow characteristics, titanium AM powders are precursor feedstock materials that are spread in thin layers, selectively melted by lasers layer-by-layer, and solidified into near-net shape 3D printed parts.
Key properties making titanium attractive for AM:
- High strength-to-weight ratio
- Excellent corrosion resistance
- Biocompatibility and non-toxicity
- Ability to withstand high temperatures
- Customized geometries possible
- Cost savings from design flexibility
- Buy-to-fly ratio improvements
AM expands titanium applications beyond forgings and castings across aerospace, medical, marine, and chemical process industry verticals.
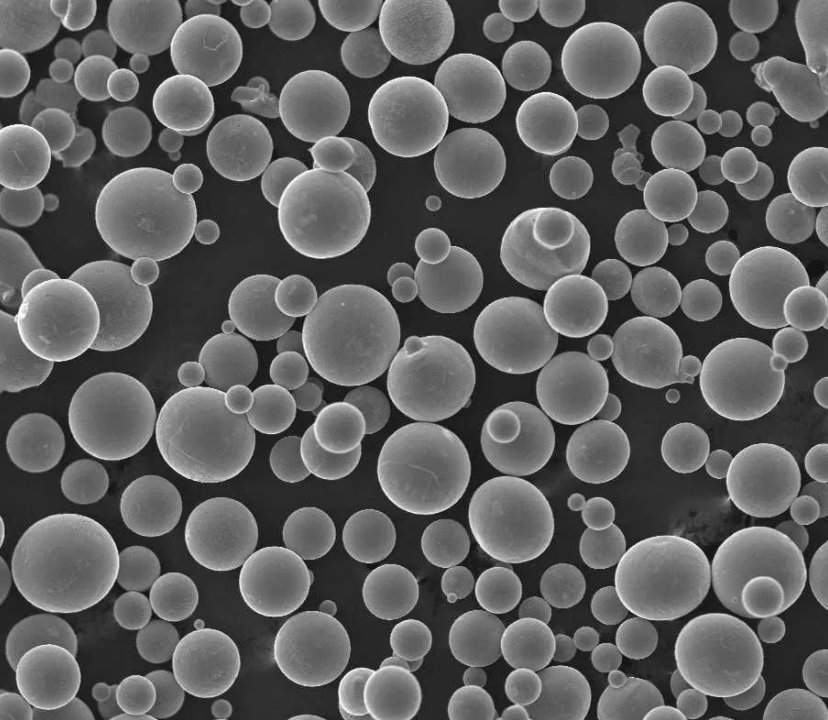
Compositions of Titanium AM Powder Variants
The common titanium AM powder variants by chemistry include:
Table 1: Main compositions of titanium AM powders
Grade | Composition | Characteristics |
---|---|---|
Ti 6Al 4V ELI | 6% Al, 4% V, 0.08% max O | Most widely used titanium alloy |
Ti 6Al 4V | 6% Al, 4% V, 0.2%max O | Aerospace extrusions alloy |
Pure titanium | 99.7% Ti, 0.10%max O | High chemical resistance suitable for implants |
Ti 5553 | 5% Al, 5% Mo, 4% V | Higher strength |
Ti 64 | 6% Al, 4% V | Heat treatable, used in jet engines |
Besides oxygen, other trace impurities like Fe, C, N and H are minimized. The alloys offer strength and temperature resistance while pure titanium provides biocompatibility.
Special alloys like Ti 5553 and Ti 64 suit niche applications in space and defense sectors needing capability enhancements.
Production Methods for Titanium AM Powder
Gas atomization is the predominant commercial scale process used to produce spherical titanium powders suited for AM processes:
Table 2: Overview of titanium AM powder production via gas atomization
Step | Description |
---|---|
Feedstock melting | Titanium ingots/scarp melted using plasma arc in protective argon |
Melt pouring | Molten metal stream poured into atomizer nozzle |
Gas atomization | High velocity inert argon jets disintegrate molten stream into fine droplets |
Powder collection | Spherical particles solidify and collected in chamber |
Sieving | Specific particle size distributions separated using vibrating screens |
Atomization with argon instead of nitrogen minimizes powder contamination. The inert gas also prevents pyrophoric risks allowing safer powder handling.
Specialized systems enhance the number of <100 micron fines produced to increase AM process productivity through enhanced powder bed packing and layer resolution.
Key Properties and Characteristics
Salient characteristics of titanium AM powders are:
Table 3: Typical properties exhibited by titanium AM powders
Property | Characteristics |
---|---|
Purity | >99% titanium content |
Impurities | <1000 ppm oxygen preferred |
Particle shape | Predominantly spherical |
Particle size | 15-45 microns common |
Flow rate | 28-35 s/50g Hall flowmeter rate aids printability |
Tap density | ≥2.5 g/cc improves bed packing |
Hausner ratio | <1.25 ensures good powder flow |
Apparent density | Density range narrow distribution <5% for consistency |
Besides chemical composition, particle characteristics like consistent spherical morphology, smooth size distribution, powder flow rates, and density determine adoption rates for precise AM printing.
Meeting application needs related to biocompatibility, surface finishing, modulus ranges, hardness, and dynamic load bearing capacity depends on amenable powder quality.
-
NiCoCrAlY alloys powders
-
Rene 142 alloy-Rene Powder
-
Haynes 25 Haynes Powder
-
Best Hastelloy C-22 Powder-High temperature alloy Powder for 3D Printing
-
Best Hastelloy C-276 Powder-High temperature alloy Powder for 3D Printing
-
Best Hastelloy N Powder-High temperature alloy Powder for 3D Printing
-
Best Hastelloy B Powder丨High temperature alloy Powder for 3D Printing
-
FGH95 Ni-base Alloy Powder | Nickel Alloy Powder
-
CMSX-4 Nickel Alloy Powder | Nickel Alloy Powder
Applications and Uses of Titanium AM Powder
Complex, lightweight printed parts made using titanium AM powders serve critical application areas like:
Table 4: Major application areas for titanium AM powder
Industry | Applications |
---|---|
Aerospace | Turbine blades, impellers, airframe and engine parts |
Medical | Orthopedic and dental implants, prosthetics, surgical instruments |
Automotive | Connecting rods, valves, gearbox components |
Chemical | Columns, catalyzer housings, corrosion resistant vessels |
Oil and gas | Saltwater piping/pumps housings, subsea components |
Defense | Combat vehicle spares like helicopter spindles printed onsite |
Benefits over traditional titanium machining – reduced lead times from rapid prototyping, ability to create complex hollow or bionic shapes through topology optimization, less wastage with no subtractive processes needed.
Specification Standards for Titanium AM Powders
Globally accepted specifications that qualify titanium AM powder batches include:
Table 5: Major specification standards followed by titanium AM powders
Standard | Measurement Aspect and Acceptance Criteria |
---|---|
ASTM F3049 | Defines AM powder attributes tested via methods like laser diffraction, SEM, flowability, and composition analysis |
ASTM B809 | Outlines sieve analysis methodology for determining particle size distribution |
ISO 13879-1 | Specifies reversible permeability (Hausner) test procedure |
ASM F3301 | Standard for additive manufacturing titanium alloys like Eli grade compositions |
AMS 7008 | Aerospace materials specification covering gas atomized titanium alloy powder types |
These standards guide appropriate test methods, equipment calibration, measurement procedures, sampling plans and compliance criteria to characterize each powder lot.
Global Suppliers and Pricing
As titanium AM is still an emerging market, powder costs between $70 to $270 per kg based on:
Table 6: Key determinants of titanium AM powder pricing
Parameter | Price Trend |
---|---|
Composition | Ti 6 4 Eli grade most expensive |
Production method | Gas atomized costs more than plasma atomized |
Sphericity consistency | Higher circularity distribution control adds cost |
Particle size distribution | Tighter distribution tolerance premium |
Purity levels | Lower oxygen and nitrogen impurities raise price |
Order quantity | Medium to high volumes warrant discounts |
Table 7: Major global titanium AM powder suppliers and price ranges
Company | Grades | Price range |
---|---|---|
AP&C | Ti 6 4, Ti 6 4 Eli | $100-270/kg |
Tekna | Ti 6 4, Ti 6 4 Eli | $150-250/kg |
Carpenter Technologies | Ti 6 4 Eli, Pure Ti grades | $80-220/kg |
VSMPO | Ti 6 4, Ti 6 Al 4 Vanadium | $75-180/kg |
ATI Powder Metals | Ti 6 4 Eli, Ti Al Mo alloys | $90-240/kg |
Prices depend on extent of buyer qualification trials, distribution channel markups and availability of suitable atomization capacity.
Comparative Pros and Cons of Titanium vs Alternate AM Powders
Table 8: Comparison between titanium and other metal AM powders
Parameter | Titanium | Stainless steels | Aluminum alloys | Inconel |
---|---|---|---|---|
Density | 4.5 g/cc | 7.9 g/cc | 2.7 g/cc | 8.4 g/cc |
Strength | High strength + stiffness combination | Stronger | Medium strength | Strongest |
Cost | $$ | Lowest | $ | $$$$ |
Thermal properties | Low conductivity | Resists higher temps | High conductivity | Highest temp resistance |
Chemical resistance | Excellent – including saltwater | Prone to some acids/chlorides | Degrades with salt exposure | Best corrosion resistance |
Magnetic | Non-magnetic | Ferritic grades are magnetic | Non-magnetic | Slightly magnetic |
Print complexity | Moderate; some support strategies needed | High complexity achieved | Tricky overhangs and bridges | Highly complex shapes printable |
For applications needing biocompatibility along with high hardened strength like dental implants and prosthetics, titanium AM powders provide tailored solutions. Stainless steels suit high temperature steam turbomachinery components better thermally. Inconel serves niche corrosion resistance needs.
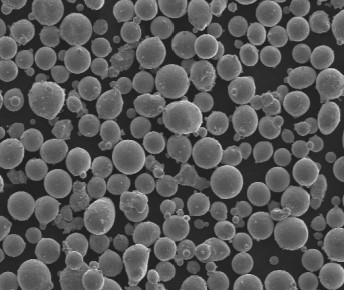
FAQ
Q: How is pricing and availability for titanium AM powder expected to change in the near future?
As more gas atomization capacity expands over the next decade to meet growth in AM part production, higher competition will improve titanium AM powder pricing and availability dynamics, making it more affordable. Machine price reductions will also catalyze AM adoption.
Q: What post-processing steps are commonly needed on as-printed AM titanium parts?
Post-processing includes – support removal via machining/blasting, surface treatment through abrasive tumbling or glass bead peening to relieve stresses and ensure finish requirements. Optional – Hot Isostatic Pressing (HIP) to further densify complex internal structures in critical components.
Q: How to avoid contamination when handling reactive titanium AM powder?
Use inert gas gloves to prevent contact with skin oils etc. Have dedicated sieves for titanium not used for steels. Store in original inert sealed containers. Limit exposure to room atmosphere. Prioritize processing over long term storage.
Q: What AM printing parameters typically need adjusting when changing titanium powder size or alloy?
Matching powder layer thickness relative to laser spot size affects optimal energy input. Transitioning between Ti 6 4 and 6 4 ELI affects thermal profiles. Larger powder sizes improve build speeds but reduce resolution – parameter tuning helps ensure part quality.