Refractory metals are a class of metals that have extremely high melting points, typically over 2000°C. They are known for their resistance to heat and wear, as well as their strength at high temperatures. Refractory metal powders refer to powders made from these heat-resistant metals through processes like gas atomization.
Refractory metal powders have become indispensable across industries like aerospace, automotive, tooling, and more due to their unique properties. This guide provides a comprehensive overview of refractory metal powders, their characteristics, applications, suppliers, and other key details.
Overview of Refractory Metal Powders
Refractory metal powders usually comprise the elements tungsten, molybdenum, tantalum, and niobium. They are produced through techniques like gas atomization where the molten metal is broken into fine droplets that solidify into powder particles.
The table below summarizes the basics of the main refractory metal powders:
Powder Type | Key Properties | Typical Uses |
---|---|---|
Tungsten | Highest melting point, density, tensile strength | Alloys, welding, electronics |
Molybdenum | High temperature strength, thermal/electrical conductivity | Alloys, lighting, electronics |
Tantalum | Corrosion resistance, biocompatibility | Alloys, capacitors, medical implants |
Niobium | Low density, superconductivity | Alloys, superconducting magnets |
The unique properties like high melting point, strength, hardness, and conductivity make them suitable for specialized, high-temperature applications across industries.
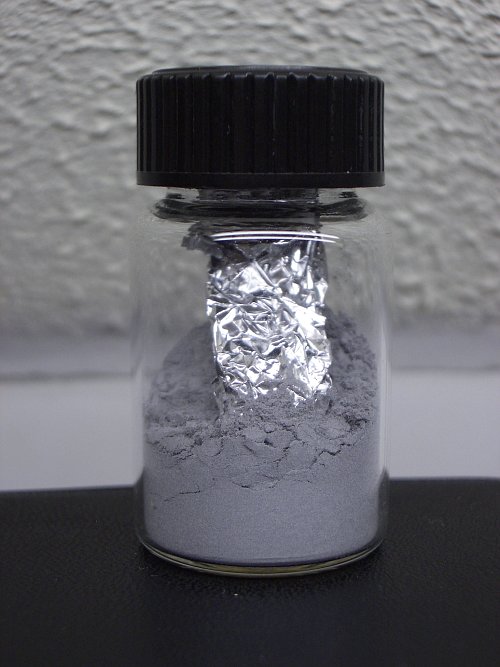
Applications and Uses of Refractory Metal Powders
Refractory metal powder find diverse uses across industries like automotive, aerospace, medical, electronics, and more. The table below summarizes some of their key applications:
Industry | Applications |
---|---|
Aerospace | Jet engine and turbine components, rocket nozzles, thrusters |
Automotive | Metal injection molding parts, friction materials |
Medical | Joint replacements, implants, radiation shields |
Electronics | Connectors, capacitors, heating elements, MEMS |
Tooling | Cutting tools, dies, presses, molds |
Chemical | Corrosion-resistant reactors and piping |
The automotive sector uses refractory metal powders for spark plug electrodes, electrical contacts, valves, and metal injection molded parts. The aerospace industry relies on them for extremely high temperature applications like jet turbine blades and rocket nozzles. Their biocompatibility makes tantalum and niobium suitable for medical implants and devices.
Overall, refractory metal powders are essential for specialty applications where high heat resistance, hardness, strength, and durability are critical. Their unique properties under high temperature conditions give them an edge over other metal powders.
Types of Refractory Metal Powder
Refractory metal powders are available in several compositions, sizes, and morphologies. The table below summarizes the main types available:
Type | Description | Typical Size Range | Morphology |
---|---|---|---|
Pure powder | Single metal like tungsten, tantalum | 1 – 100 microns | Irregular, spherical |
Alloy powder | Mixtures like tungsten heavy alloy | 1 – 100 microns | Spherical |
Nano powder | Particles under 100 nm | 10 – 100 nm | Spherical |
Composite powder | Metal + ceramic/carbide | 1 – 100 microns | Irregular |
Pure Metal Powders
These consist of a single refractory metal like tungsten or molybdenum powder. They are available in both spherical and irregular morphologies. Pure metal powders are used for applications where properties of that particular metal are desired.
Alloy Powders
Powders made by blending two or more refractory metals to get combined properties. Common examples are tungsten heavy alloys with 90-97% W, nickel-based superalloys, etc. These are usually spherical in shape.
Nano Powders
Ultrafine refractory metal particles under 100 nm in size exhibit unique properties like higher strength and reactivity. However, they pose risks of contamination, are more reactive, and require special handling.
Composite Powders
These combine refractory metals like tungsten with other materials like carbides, ceramics, etc. WC-Co cermet powders are a common example used in wear applications. They have irregular and porous morphology.
Characteristics of Refractory Metal Powders
The table below summarizes the typical characteristics of commercial refractory metal powders:
Characteristic | Details |
---|---|
Purity | 99% and above |
Particle size | 1 – 100 microns |
Morphology | Spherical, irregular, porous |
Oxide content | Under 1% |
Apparent density | Around 50% of theoretical density |
Flowability | Fair due to irregular shapes |
Compressibility | Moderate to poor |
- Purity – Most powders have purity levels over 99% with low oxygen and nitrogen levels. High purity is essential for consistency in material properties.
- Particle Size – Available across a wide range from 1 micron to around 100 microns. Finer powders improve density but can be pyrophoric.
- Morphology – Spherical powders offer better flow and packing but irregular and porous particles are also common.
- Oxide Content – Kept low, under 1%, through use of inert gas atomization and handling to prevent oxidation. High oxides can degrade material properties.
- Density – Only around 50% of theoretical density due to voids between particles. Requires sintering to reach full density.
- Flowability – Fair flowability due to irregular shapes. Nanopowders can agglomerate and are difficult to handle.
- Compressibility – Moderate to poor compressibility. Spherical and alloy powders are more compressible than irregular pure metal powders.
Specifications and Standards
Refractory metal powder composition, size, shape, purity, and other parameters are standardized by specifications like ASTM International standards. These help ensure quality and consistency.
Parameter | Standard | Typical Values |
---|---|---|
Composition | ASTM B771, ASTM F3049 | Over 99% purity |
Contaminants | ASTM B771 | Oxygen: 0.05-0.2%, Nitrogen: 50-400 ppm |
Particle size | ASTM B822 | 1 – 100 microns |
Morphology | ASTM B822 | Classified into types |
Flow rate | ASTM B213 | Angle of repose under 45° |
Apparent density | ASTM B212 | Around 50% of true density |
Key standards like ASTM B771 and ASTM F3049 standardize the chemical composition of common powders like tungsten, molybdenum, and tungsten heavy alloys. Contaminant levels of oxygen and nitrogen are also specified.
Physical characteristics like particle size distribution, morphology, flow rate, and density are standardized by tests described in standards like ASTM B822, ASTM B213, and ASTM B212 respectively.
These ASTM standards help define quality metrics for comparing and selecting refractory metal powders from different manufacturers.
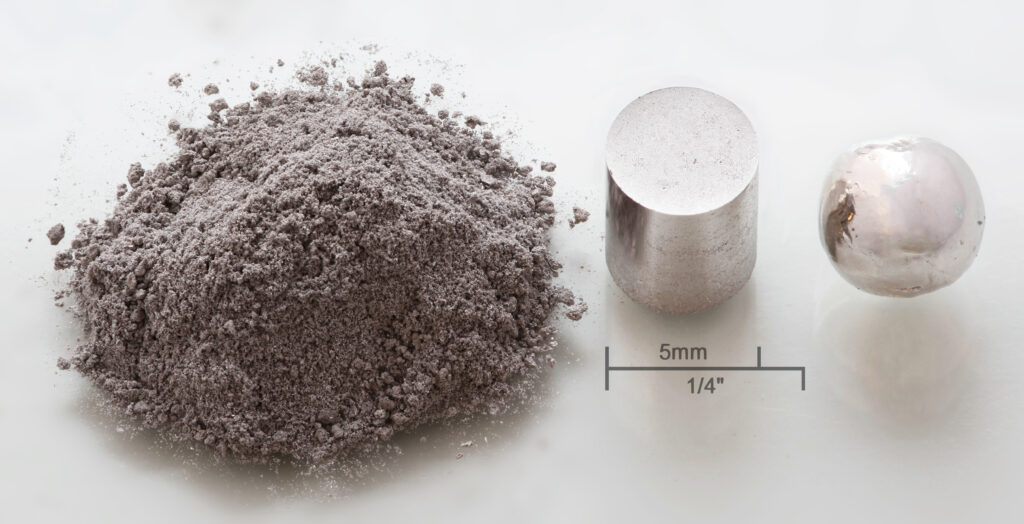
Design Considerations
Several factors must be considered when selecting refractory metal powders for an application:
Operating Temperature
The maximum operating temperature determines suitable metals. W and Ta have highest melting points.
Environment
Consider oxidation risk, thermal cycling, stresses. May need alloying additions like La to improve oxidation resistance.
Mechanical Properties
Strength, hardness, ductility requirements at temperature. W is strongest while Mo has better workability.
Consolidation Method
Fine powders for pressing and MIM. Coarse powder for thermal spraying. Consider final part size and shape.
Purity Levels
High purity reduces contaminants and variability but increases cost. Assess tradeoffs for application.
Particle Shape
Spherical powders improve density and flow. Irregular powder for thermal spray. Consider post-processing steps.
Powder Recyclability
Recovery and reuse of powder from powder bed fusion AM can offset costs. assess recycling ability.
The right powder is selected by analyzing the operating conditions, mechanical property needs, manufacturing process limitations, purity requirements, and economics.
Refractory Metal Powder Suppliers
Most major metal powder suppliers offer refractory metal powder options. The table below lists some leading global suppliers and typical powder types they offer:
Supplier | Powder Types |
---|---|
H.C. Starck | W, W alloys, Ta, Nb, Mo |
AMETEK | W, Mo, Ta powders and alloys |
Global Advanced Metals | W, Mo, Ta, Nb |
Plansee | W, Mo, Ta powders and composites |
Stanford Materials Corporation | W, WC, Ta, TaC |
Zhuzhou Cemented Carbide Group Co. Ltd | W, WC, W alloys |
H.C. Starck, AMETEK, Global Advanced Metals, and Plansee are leading global commercial suppliers offering most refractory metal powder types and alloys.
Smaller companies may specialize in specific powders like Zhuzhou Cemented Carbides for tungsten and tantalum carbide powders. Custom alloy development is also offered by some companies.
Pricing
As rare metals, refractory metal powders can be expensive, especially for high purity levels. Indicative pricing for common powders is shown below:
Powder | Price Range |
---|---|
Tungsten | $40 – $1500 per kg |
Tantalum | $400 – $3000 per kg |
Molybdenum | $30 – $500 per kg |
Niobium | $60 – $1000 per kg |
- Tungsten pricing depends heavily on purity level (99 to 99.999%) and particle size. Nano powder is costliest.
- Tantalum powder is most expensive due to rarity. 99.9% pure powders start around $400/kg.
- Molybdenum has relatively low and stable pricing between $30-$500/kg for pure powder.
- Niobium powders range from $60 per kg for 99% grade up to $1000/kg for 99.99% purity.
For specialty alloys, powders with rare earth or precious metal additions can cost several thousands per kg. Recycling and reuse helps recover raw material and offset costs.
How to Select A Refractory Metal Powder Supplier
Choosing the right refractory metal powder supplier is crucial for getting high quality and consistent material. Here are key factors to consider in selection process:
Material Options
Range of refractory metal powders and alloys offered – W, Mo, Ta, Nb etc. Can they make custom alloys?
Quality Certifications
ISO 9001, ISO 13485, AS9100 certifications validate quality management system.
Testing Capabilities
In-house labs for powder characterization per ASTM standards – chemical, size, morphology tests.
Technical Expertise
Knowledgeable technical support team to assist with material selection for application.
Manufacturing Scale
Large established suppliers have higher and more consistent production volumes. Critical for demanding applications.
Lead Times
Large inventory allows faster delivery of standard materials. Custom alloys have longer lead times.
Pricing
Compare pricing between grades and suppliers. Consider discounts for large orders.
Recycling Services
Capabilities for accepting and reprocessing used powder from metal AM.
Leading suppliers like HC Starck, AMETEK, Plansee have the technical expertise, rigorous QC testing, and manufacturing scale to deliver high purity and consistent refractory metal powder suitable for critical applications across aerospace, medical, and industrial sectors.
Installation and Operation of Refractory Metal Powder Systems
Handling and processing refractory metal powder requires special precautions due to material costs, health hazards, and fire/explosion risks.
Storage and Handling
- Store powder sealed in inert gas-purged containers to prevent oxidation
- Use spark-proof tools and minimise metal-metal contact during handling
- Avoid contamination from foreign particles or metals
- Prevent powder spillage; clean up immediately if spill occurs
Personnel Safety
- Use protective gear – respirators, gloves, full-body suits
- Avoid skin contact or inhalation of fine powders
- Provide proper ventilation andbreathing air supply if needed
Powder Loading
- Minimise exposure to air during transfers
- Inert gas glove boxes ideal for loading powder bed AM machines
- Use brushes, spatulas for cleaning rather than compressed air
AM Machine Operation
- Follow manufacturer’s safety, loading, setup, processing guidelines
- Use inert gas to reduce risk of powder ignition
- Optimize process parameters to ensure high quality
Maintenance
- Check system seals, change filters regularly
- Clean powder bed after each build thoroughly
- Safely remove, transport, and dispose unused powder
Proper protective gear, handling procedures, and equipment design are crucial for safe refractory metal powder processing. Training staff on risks and prevention is essential.

Refractory Metal Powder Processing Methods
Key techniques for consolidation of refractory metal powders into final components are:
Method | Description |
---|---|
Press and sinter | Compact at room temperature, sinter at high temperature |
Metal injection molding (MIM) | Mix powder + binder, shape, then sinter |
Additive manufacturing | Selective laser melting, binder jetting, etc |
Thermal spray | Heat and spray powder onto surface |
Press and Sinter
- Cold press powder into green compacts applying 10-20 tons/sq. inch
- Heat compacts up to 80% of melting point to sinter particles together
- Simple, versatile, but limited in resolution
Metal Injection Molding
- Mix powder with binder to prepare feedstock
- Inject into molds to form complex green shapes
- Remove binder and sinter; can achieve 98%+ density
Additive Manufacturing
- Selective laser melting most common technique
- Build parts by melting powder layer-by-layer using laser
- Excellent geometric freedom but slower build rates
Thermal Spray
- Heat and spray refractory powder at high velocity onto surface
- Forms protective coatings; not for complex parts
MIM and AM offer advantages of design flexibility and material savings but require more process control compared to traditional press-sinter approach.
Advantages of Refractory Metal Powders
- Withstand extremely high temperatures – above 2000°C
- Retain excellent strength, hardness, and corrosion resistance at high temperatures
- Enables performance gains in aircraft engines, space technology
- Higher electrical and thermal conductivity than other metals
- Inert, non-toxic nature allows use in medical implants
- Parts can be net shape manufactured through MIM and AM
Limitations of Refractory Metal Powders
- Very high cost, especially for high purity powders
- Rarity of some refractory metals like Ta, Nb
- Difficult to fully densify parts without sintering aids
- Prone to oxidation at elevated temperatures
- Fine powders are pyrophoric and require careful handling
- Refractory metals are dense and heavy
Proper design, protective coatings, alloying additions, and handling procedures can help overcome limitations like poor oxidation resistance. Overall, the unparalleled high temperature properties make refractory metal powders suitable for specialized niches despite higher costs.
Maintaining Refractory Metal Powder Systems
To ensure safe and optimal performance, refractory metal powder systems require proper maintenance procedures:
Storage Container Checks
- Inspect containers, seals, valves for damage allowing air/moisture ingress
- Confirm inert gas levels and dew point in containers is in spec
Leak Checks
- Regularly check powder handling system for any gas leaks
- Use helium leak testing to detect any points of leakage into system
Filter Changes
- Replace gas and vacuum line filters as scheduled
- Use filtration rating appropriate for powder size
Powder Quality Testing
- Perform quality checks like flow rate, composition periodically
- Discard powder exceeding oxygen content limits
Equipment Calibration
- Calibrate scales, density meters, pressure gauges per manufacturer instructions
Cleaning
- Fully remove powder residues after production runs or AM builds
- Avoid contamination between different powder materials
With careful maintenance and testing, refractory powder inventory stays in optimal condition over its usable shelf life. This reduces variation and improves end product quality.
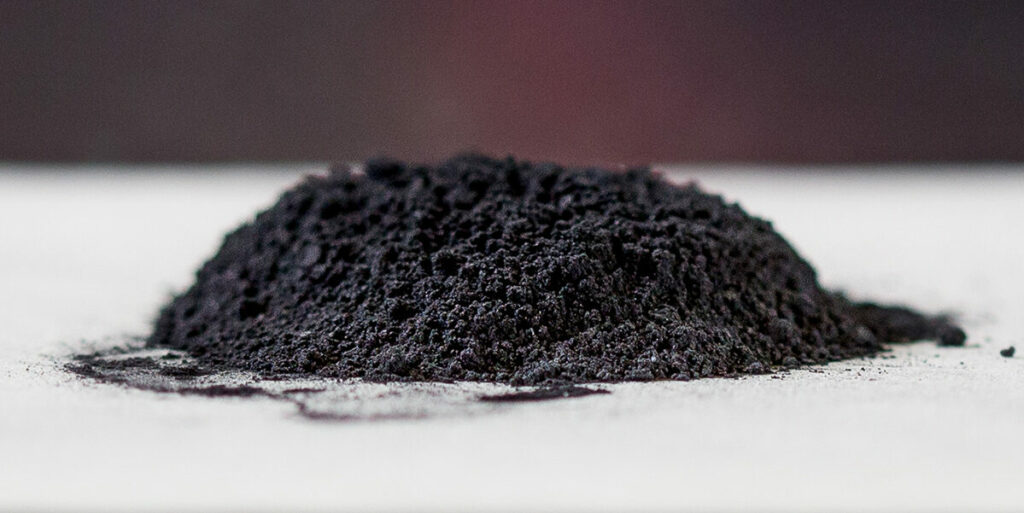
FAQs
Q: What are the main advantages of tantalum powder over tungsten?
A: Tantalum offers higher ductility, better corrosion resistance, and biocompatibility compared to tungsten. This makes it preferable for applications like medical implants. However, tantalum is more expensive and has lower hardness and strength than tungsten.
Q: Are refractory metal powders flammable?
A: Yes, refractory metal powders can pose fire or explosion risks due to their pyrophoric nature at very fine sizes. Proper protective equipment, inert gas use, and safe handling procedures are essential to mitigate powder ignition risks.
Q: What is gas atomization process for refractory metal powder production?
A: Gas atomization uses high velocity inert gas jets to break up a stream of molten refractory metal into fine droplets. These droplets solidify into powder particles with spherical morphology. Gas atomization allows control of particle size distribution.
Q: How are refractory metal powders characterized?
A: Key characterization tests per ASTM standards include chemical analysis using XRF/ICP-OES to determine composition, laser diffraction particle size analysis, SEM imaging for morphology, Scott volumeter for density, Hall flowmeter for flow rate, and oxygen/nitrogen analysis.
Q: What is the benefit of using refractory metal powders in metal injection molding?
A: MIM allows sintering of refractory powder compacts to full density. This achieves complex net shape parts with superior mechanical properties. MIM also has less material waste compared to machining from bulk metals.
Q: How are refractory metal powders safely handled in industry?
A: Stringent safety measures are followed including use of argon-filled glove boxes, automated powder handling between storage and processing equipment, specialized personal protective equipment for operators, and air quality monitoring.
Q: Why are high purity levels important for refractory metal powders?
A: Impurities can severely degrade material properties like ductility at high temperatures. Even ppm levels of oxygen can lower melting points considerably. High powder purity ensures consistent and reliable performance.
Q: What are common applications for molybdenum metal powder?
A: Molybdenum’s high temperature strength, corrosion resistance, thermal conductivity, and lubricity make it well-suited for furnace parts, lighting and electronics electrodes, nuclear reactors, welding, and more.
Q: How is oxidation and contamination prevented during handling?
A: Minimizing powder exposure to air using vacuum or inert gas environments, no metal-metal contact, slow powder transfers, avoiding mechanical abrasion, and storage in sealed containers prevents contamination and oxidation.
Q: What are the latest trends in refractory metal powder manufacturing?
A: Nanoscale and microscale refractory metal powders are enabling additive manufacturing of new high temperature alloys. There is also growing adoption of gas atomization and metal injection molding for net-shape fabrication.