In today’s fast-paced world of material science and engineering, innovation doesn’t come from sticking to the same old formulas. Instead, scientists are looking for entirely new combinations of elements to push boundaries, and that’s where materials like WMoTaNb powder come into play. WMoTaNb, also known as tungsten, molybdenum, tantalum, and niobium powder, is a Multi-Principal Element Alloy (MPEA), a material designed to offer superior performance in extreme conditions. Sounds fascinating, right? Let’s explore what makes this alloy powder so special and why it’s gaining attention in various industries.
Overview of WMoTaNb Powder
WMoTaNb powder belongs to a class of materials known as high-entropy alloys (HEAs) or Multi-Principal Element Alloys (MPEAs). These alloys differ from traditional alloys by being composed of multiple principal elements in near-equimolar ratios, rather than just one base metal. The WMoTaNb alloy contains a balanced composition of tungsten (W), molybdenum (Mo), tantalum (Ta), and niobium (Nb), and is engineered for superior strength, durability, and resistance to extreme environments.
What is WMoTaNb Powder?
WMoTaNb powder is a multi-element alloy that combines the properties of four refractory metals. Each of these metals brings something different to the table—whether it’s high melting points, excellent corrosion resistance, or incredible mechanical strength. When combined, they create a material that’s stronger, tougher, and more heat-resistant than traditional alloys.
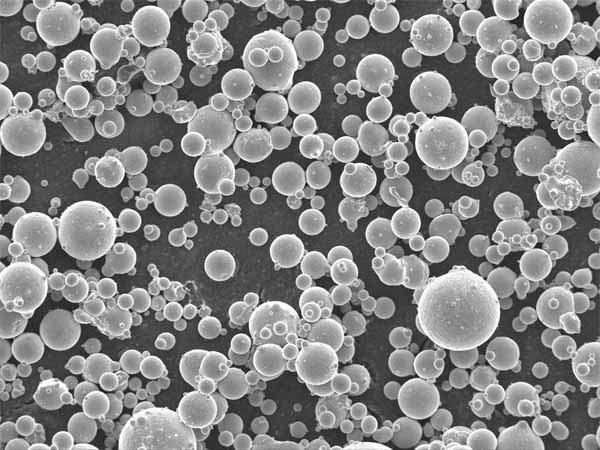
Composition of WMoTaNb Powder
WMoTaNb powder is typically made from four elements, each contributing unique properties to the overall alloy:
Element | Atomic Number | Contribution to Alloy |
---|---|---|
Tungsten (W) | 74 | High melting point, strength at elevated temperatures |
Molybdenum (Mo) | 42 | Thermal stability, hardness, and corrosion resistance |
Tantalum (Ta) | 73 | Resistance to corrosion, ductility, and toughness |
Niobium (Nb) | 41 | Enhanced strength, thermal conductivity, and oxidation resistance |
This balanced mixture results in a material that excels in high-temperature, high-pressure, and highly corrosive environments.
Characteristics of WMoTaNb Powder
When you’re considering using WMoTaNb powder in a project, understanding its core properties is essential. Each element contributes specific characteristics that define how the alloy behaves in different environments.
Characteristic | WMoTaNb Powder Performance |
---|---|
Melting Point | Very high melting point (above 3000°C) due to tungsten and tantalum content |
Corrosion Resistance | Excellent, particularly in corrosive environments like acids and alkalis |
Mechanical Strength | Strong mechanical properties, especially under high-stress conditions |
Thermal Conductivity | High, allowing it to dissipate heat efficiently |
Oxidation Resistance | Superior, with niobium enhancing resistance to oxidation at high temperatures |
Density | High density but still manageable for various engineering applications |
Ductility | Ductile enough for shaping, making it versatile for industrial uses |
In terms of complexity, these alloys can perform in areas where single-metal or binary-metal solutions would fail. WMoTaNb powder is particularly effective in scenarios that involve extreme heat or chemical exposure, making it perfect for industries like aerospace, nuclear energy, and high-performance electronics.
Applications of WMoTaNb Powder
The potential applications for WMoTaNb powder are vast, and its ability to withstand some of the harshest environments makes it a prime candidate for cutting-edge industries. Let’s take a look at where this alloy powder is making an impact:
Industry | Applications of WMoTaNb Powder |
---|---|
Aerospace | High-temperature components such as turbine blades and rocket nozzles |
Nuclear Energy | Structural materials for reactors and radiation shielding |
Electronics | High-performance components, semiconductors, and transistors |
Chemical Processing | Equipment for handling corrosive chemicals and extreme temperatures |
Medical Devices | Advanced implants and medical tools that require biocompatibility and strength |
Automotive | Components for engines, particularly in motorsports and high-performance cars |
It’s clear that WMoTaNb powder is crucial for industries where standard materials simply can’t stand up to the environmental pressures.
Specific Models of WMoTaNb Powder
The world of WMoTaNb powder includes different grades and compositions, each tailored to suit various needs and applications. Here’s a breakdown of some of the most prominent models, and how they differ in their specific attributes:
Model Name | Description |
---|---|
WMoTaNb-01 | A general-purpose grade suitable for high-temperature industrial applications |
WMoTaNb-02 | High-strength alloy with enhanced thermal stability and oxidation resistance |
WMoTaNb-03 | Optimized for corrosive environments, used in chemical and oil processing |
WMoTaNb-04 | Lightweight version for aerospace components where weight is critical |
WMoTaNb-05 | Ultra-high temperature resistance, used in space exploration and nuclear applications |
WMoTaNb-06 | Enhanced ductility, ideal for medical devices and biocompatible applications |
WMoTaNb-07 | Electrically conductive variant for electronics and semiconductors |
WMoTaNb-08 | Shock-resistant, used in heavy-duty automotive and military equipment |
WMoTaNb-09 | Nano-powder version for additive manufacturing and 3D printing |
WMoTaNb-10 | Enhanced wear resistance, suited for machining tools and high-stress parts |
Each of these models has been designed to offer a balance of properties, making it easier to choose the right WMoTaNb powder for your specific project. Whether you need a material that can withstand the heat of a rocket launch or the corrosive chemicals in an industrial plant, there’s a version of WMoTaNb that fits the bill.
Specifications, Sizes, and Grades of WMoTaNb Powder
When selecting WMoTaNb powder, understanding the available grades, sizes, and specifications is crucial for achieving the best performance in your application.
Specification | Details |
---|---|
Available Particle Sizes | 1-10 microns, 10-50 microns, 50-100 microns |
Purity Levels | 99.9% or higher, with ultra-pure versions available for specific industries |
Grades | Industrial grade, aerospace grade, medical grade, electronics grade |
Standards | ASTM, ISO, and Mil-Spec standards followed |
Packaging | Available in various quantities, from small sample sizes to bulk orders |
The versatility of WMoTaNb powder lies in its adaptability across a wide range of particle sizes and purity levels, allowing it to be used in industries from aerospace to medical technology.
Suppliers and Pricing of WMoTaNb Powder
Pricing for WMoTaNb powder can vary significantly depending on the grade, size, and purity of the powder, as well as the specific supplier. Here’s a general comparison of suppliers and their typical pricing structures:
Supplier Name | Pricing (per kg) | Grade Offered | Notes |
---|---|---|---|
H.C. Starck Solutions | $1200 – $2000 | Aerospace, Medical, Electronics | High-purity powders with customizable particle sizes |
American Elements | $1500 – $2200 | Industrial, High-Purity | Offers bulk discounts and custom alloy compositions |
Advanced Metallurgy Group | $1100 – $1900 | Nano-powders, Medical | Specializes in nano-sized powders for additive manufacturing |
Zapp Materials Engineering | $1300 – $2100 | Aerospace, Nuclear | Known for stringent quality control and high-performance powders |
Stanford Advanced Materials | $1000 – $1800 | Industrial, Electronics | Focus on industrial applications with competitive pricing |
Goodfellow Corporation | $1400 – $2300 | Research Grade, Industrial | Offers smaller quantities suitable for research and R&D |
Oerlikon Metco | $1200 – $1900 | High-Temperature, Aerospace | Specializes in thermal spray applications and coatings |
It’s important to note that while these prices are indicative of the current market, fluctuations may occur depending on the global supply chain, availability of raw materials, and geopolitical factors.
Pros and Cons of WMoTaNb Powder
Choosing WMoTaNb powder for your application comes with both advantages and limitations. Let’s break down the pros and cons of using this material, so you can make an informed decision:
Advantages | Disadvantages |
---|---|
High-Temperature Resistance: With a melting point well above 3000°C, WMoTaNb powder excels in extreme heat environments, making it perfect for aerospace and nuclear applications. | Cost: The inclusion of multiple refractory metals makes WMoTaNb powder more expensive than simpler alloys. |
Corrosion Resistance: The addition of tantalum and molybdenum provides excellent resistance to chemical corrosion, making it ideal for use in harsh chemical environments. | Density: The high density of tungsten and tantalum can make components heavier, which might be a drawback for applications where weight is critical, such as in aerospace. |
Mechanical Strength: The combination of niobium and tungsten ensures superior strength under mechanical stress, making it durable even under high-pressure conditions. | Machinability: WMoTaNb is not as easily machinable as other materials, requiring specialized equipment and techniques. |
Oxidation Resistance: The presence of niobium provides enhanced resistance to oxidation, which is essential in high-temperature environments. | Availability: WMoTaNb powder is not as widely available as more traditional materials, which can lead to longer lead times. |
Versatility in Applications: WMoTaNb powder can be tailored to meet specific needs across various industries, from aerospace to electronics. | Complex Manufacturing Process: The production of multi-principal element alloys is more complex, which can drive up manufacturing costs. |
In summary, WMoTaNb powder offers exceptional performance in demanding environments, but its cost and complexity might make it less suitable for less critical applications. However, when performance and durability are non-negotiable, WMoTaNb powder proves its worth.
Comparison of WMoTaNb Powder to Other Metal Powders
Let’s look at how WMoTaNb powder stacks up against other popular metal powders in terms of performance, cost, and application range.
Metal Powder | Strengths | Weaknesses | Best Applications |
---|---|---|---|
WMoTaNb Powder | High-temperature resistance, corrosion resistance, mechanical strength | Expensive, difficult to machine, high density | Aerospace, Nuclear, Chemical Processing, Medical Devices |
Titanium Powder | Lightweight, high strength-to-weight ratio, corrosion resistance | Lower temperature limits, expensive | Aerospace, Medical Implants, Automotive |
Aluminum Powder | Lightweight, affordable, good conductivity | Poor strength at high temperatures, prone to corrosion | Automotive, Electronics, Additive Manufacturing |
Nickel Alloy Powder | Excellent corrosion resistance, good at high temperatures | Expensive, high density | Chemical Processing, Oil & Gas, Turbine Blades |
Copper Powder | High electrical conductivity, affordable | Poor corrosion resistance, lower strength | Electronics, Electrical Components, Conductive Coatings |
Steel Powder | Affordable, strong mechanical properties | Heavy, prone to rust | Automotive, Construction, Machining |
Compared to more traditional powders like aluminum or steel, WMoTaNb powder offers unparalleled resistance to heat and corrosion. However, its cost and machinability can make it less ideal for applications where budget constraints are a priority. In contrast, if you’re working in aerospace or nuclear environments where failure is not an option, WMoTaNb powder is a clear winner.
Advantages of WMoTaNb Powder in Various Industries
Each industry has specific needs, and WMoTaNb powder’s properties make it a compelling choice for several key sectors. Let’s break down its advantages across different industries:
Aerospace
Aerospace applications demand materials that can withstand extreme heat, pressure, and corrosion—qualities WMoTaNb powder delivers in spades. The alloy’s high melting point and strength under stress make it ideal for components like turbine blades and rocket nozzles, where traditional materials might fail under similar conditions. Compared to nickel alloys, WMoTaNb provides better resistance at higher temperatures, making it a more durable option in critical components.
Nuclear Energy
In nuclear reactors, structural materials need to endure intense radiation, heat, and chemical exposure over long periods. WMoTaNb powder’s excellent resistance to oxidation and radiation embrittlement makes it a top choice for reactor components and radiation shielding. When compared to stainless steel, WMoTaNb exhibits far superior performance in high-radiation environments, making it the material of choice for next-generation reactors.
Medical Devices
Biocompatibility, along with strength and corrosion resistance, are critical for medical implants and surgical tools. WMoTaNb’s mechanical properties and its ability to resist wear and tear make it an excellent choice for high-performance medical devices. While titanium is commonly used for implants due to its lightweight properties, WMoTaNb powder offers better wear resistance and durability in environments where high stress is a factor, such as orthopedic implants.
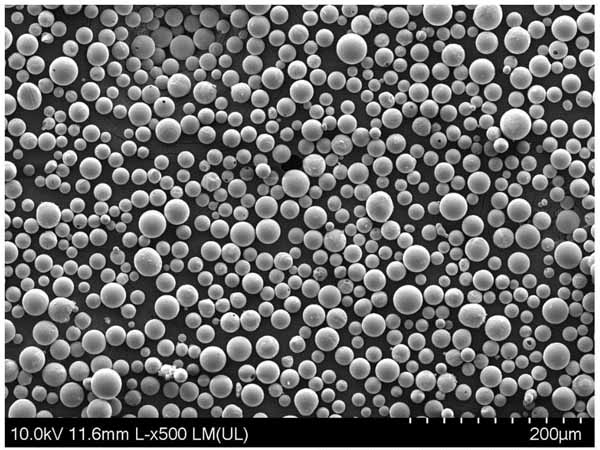
FAQ
Let’s dive into some common questions people have about WMoTaNb powder and its applications.
Question | Answer |
---|---|
What makes WMoTaNb powder unique compared to other alloys? | WMoTaNb powder is a Multi-Principal Element Alloy, meaning it consists of nearly equal proportions of multiple metals, giving it superior strength, corrosion resistance, and high-temperature performance. |
Why is WMoTaNb powder so expensive? | The high cost is due to the inclusion of rare and expensive metals like tungsten, tantalum, and niobium, as well as the complex manufacturing process required to blend these metals. |
In what industries is WMoTaNb powder most commonly used? | WMoTaNb powder is widely used in aerospace, nuclear energy, electronics, chemical processing, and medical devices because of its high-performance characteristics. |
Can WMoTaNb powder be used in additive manufacturing? | Yes, WMoTaNb nano-powder is used in 3D printing and other additive manufacturing techniques, allowing for the production of complex parts with high precision. |
How does WMoTaNb powder compare to titanium in medical applications? | While titanium is known for its lightweight properties, WMoTaNb offers superior wear resistance and mechanical strength, making it better suited for applications requiring long-term durability. |
Is WMoTaNb powder difficult to machine? | Yes, the alloy’s hardness and high melting point make it more challenging to machine compared to softer metals, requiring specialized tools and techniques. |
Are there alternatives to WMoTaNb powder for high-temperature applications? | Alternatives include nickel-based alloys and ceramic materials, but WMoTaNb offers superior performance at ultra-high temperatures, making it irreplaceable in certain scenarios. |
Conclusion
WMoTaNb powder represents a breakthrough in material science, combining the strengths of four refractory metals to create a Multi-Principal Element Alloy that can withstand the most extreme conditions. Its superior resistance to heat, corrosion, and mechanical stress makes it an invaluable material in industries such as aerospace, nuclear energy, and medical devices. While the cost and machining complexity may pose challenges, the benefits far outweigh the limitations when failure is not an option.
For those looking to push the boundaries of material performance, WMoTaNb powder is an alloy that demands attention. Whether it’s withstanding the heat of a rocket engine or the corrosive environment of a chemical reactor, this alloy is proving to be one of the most versatile and high-performance materials on the market today.