A100 steel alloy powder refers to a martensitic precipitation-hardening stainless steel powder used in powder bed fusion additive manufacturing processes like selective laser sintering (SLS) and direct metal laser sintering (DMLS).
With high strength, hardness and corrosion resistance, A100 alloy powder enables printing durable end-use components for demanding applications. Optimized particle size distributions, spherical morphology and controlled microstructures provide reliable processing and mechanical performance.
This guide covers A100 powder composition, properties, applications, specifications, printing parameters, suppliers, comparisons, and FAQs to consider when adopting A100 for production or prototyping needs.
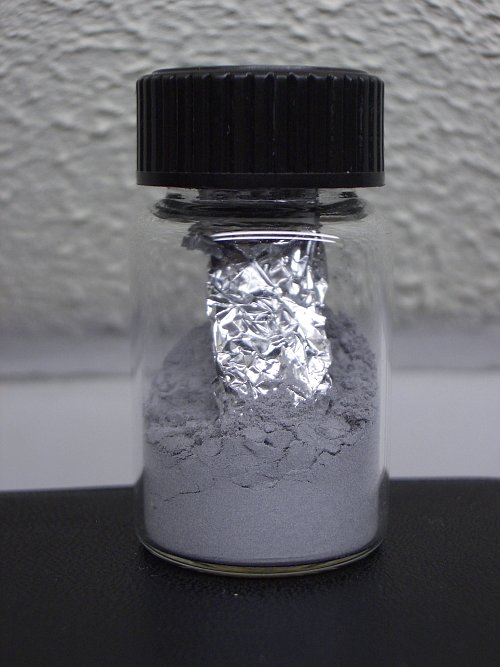
Composition of A100 Steel Alloy Powder
As a precipitation-hardening martensitic stainless steel, A100 contains:
Element | Weight % | Role |
---|---|---|
Iron (Fe) | Balance | Base metal |
Chromium (Cr) | 13-15% | Corrosion resistance |
Nickel (Ni) | 4-5% | Toughening |
Molybdenum (Mo) | 1-2% | Strength, hardenability |
Copper (Cu) | 3-5% | Precipitation hardening |
Niobium (Nb) | 0.15-0.45% | Grain refinement, precipitation hardening |
Trace elemental limits control cleanliness while the nickel and copper enable heat treating to achieve high hardness levels after processing.
Key Properties and Characteristics
In addition to composition, A100 exhibits:
Property | Description |
---|---|
Density | 7.7 g/cm3 |
Particle size distribution | 15-53 microns |
Apparent density | >4.0 g/cm3 |
Hall flow rate | <30 s/50 g |
Melting point | 1390-1440°C |
Tensile strength | 1150 MPa |
Elongation at break | 7% |
Hardness | >50 HRC |
Corrosion Resistance | High – PREN 35-38 |
The powder characteristics ensure printability while the mechanical performance supports functional components able to withstand substantial stresses.
Applications of A100 Steel Powder
As a high strength tool steel alloy powder resistant to wear, heat and corrosion, A100 suits:
Industry | Application Examples |
---|---|
Aerospace | Turbine blades, landing gear components |
Automotive | Cutting tools, high wear tooling, turbocharger parts |
Oil and gas | Valve components and bodies, wellhead parts |
Industrial | Extrusion tooling, injection molding components |
General | High hardness bushings/bearings, shafts, marine hardware |
The balanced properties make A100 a versatile high-performance material for metal additive manufacturing across sectors.
-
SCM 415 Low Alloy Steel Powder
-
AISI 4340 Low Alloy Steel Powder
-
Invar 36 alloy powder
-
52100 Alloy Steel Powder
-
2.25Cr1Mo alloy steel
-
Stainless Steel OP431 Powder
-
Best Stainless Steel 316L Powder for 3D Printing
-
stainless steel 304 Powder for 3D Printing
-
Best 17-4PH powder stainless steel powder for 3D Printing
A100 Steel Powder Specifications
Industry standards continue to evolve, but current nominal specifications include:
Parameter | Specification | Test Method |
---|---|---|
Particle size distribution | 15-53 microns | ISO 13320/ASTM B822 |
Apparent density | ≥ 4.0 g/cm3 | ISO 3923/ASTM B212 |
Flow rate | ≤ 30 s/50 g | ISO 4490/ASTM B213 |
Oxygen content | ≤ 0.3% | Inert gas fusion analysis |
Nitrogen content | ≤ 0.1% | Inert gas fusion analysis |
Carbon content | ≤ 0.1% | Combustion analysis |
Microstructure | Martensitic | Optical microscopy |
Prior particle process history | Virgin plasma atomized | Certification |
Chemistry, cleanliness, particle characteristics and microstructure all align to enable high density printing with good flow and spreadability.
Printing Parameters for A100 Powder
Typical laser powder bed fusion processing windows for A100 include:
Parameter | Range |
---|---|
Layer thickness | 20-50 μm |
Laser power | 195-500 W |
Scan speed | 600-1250 mm/s |
Hatch spacing | 80-160 μm |
Bed temperature | 80-150°C |
Part properties depend heavily on optimized energy density and surrounding microclimate during printing. Post-processing like hot isostatic pressing (HIP) can further reduce internal stresses and defects while heat treating maximizes hardness, strength and ductility.
A100 Powder Suppliers
As a widely adopted high-performance printable stainless steel, various reputable suppliers offer A100 powder:
Supplier | Description | Pricing |
---|---|---|
Sandvik Osprey | Leading producer of stainless steel alloys for AM | $$$/kg |
Carpenter Additive | Producer of custom alloys and materials | $$$/kg |
Höganäs | Major global supplier of industrial metal powders | $$/kg |
Praxair | Reliable supplier for industrial gases and materials | $$/kg |
LPW Technology | Specialist in high end metal alloy AM powders | $$$/kg |
Price ultimately depends on order volumes, lead times, additional screening/blending, and bulk discounts.
Tradeoffs When Considering A100 Powder
Pros:
- High hardness/wear performance from precipitation strengthening
- Withstand heavy loads without distortion
- Thermal and corrosion resistance for harsh environments
- Mechanically robust from fine martensitic structure
- Qualified input material with uniform characteristics
Cons:
- Requires stress relief and hot isostatic pressing (HIP)
- Brittle compared to annealed materials without post-processing
- Challenging to conventionally machine in fully hardened state
- Costs more than standard alloys like 316L stainless
- Special handling given limited reusability
For extreme durability without fragility, A100 warrants consideration where applications demand the balanced capabilities.
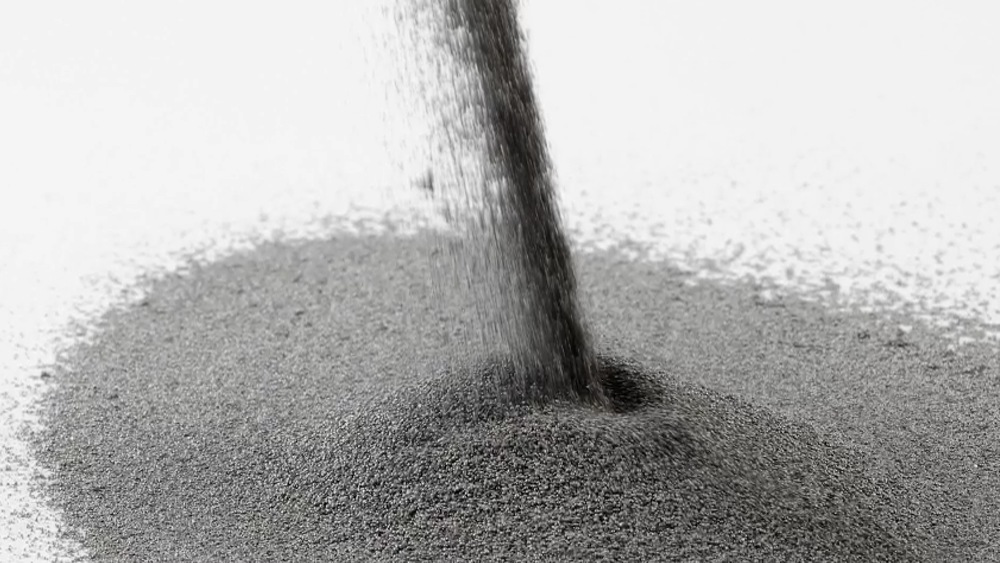
Frequently Asked Questions
What particle size range does A100 powder normally come in?
A100 is generally supplied in the 15-53 micron range to support crisp feature resolution in powder bed systems while ensuring spreadability. Particle optimization continues to push size ranges finer and tighter.
Does A100 powder require special storage or handling precautions?
Like most reactive alloy powders, A100 requires moisture-free handling in sealed argon filled containers to prevent oxidation. Storage areas should be cool, dry, and standardized for metal powders. Personal protective equipment like masks and gloves are mandatory as well.
Can you heat treat or machine A100 components after printing?
Yes, aging heat treatments can further enhance hardness and strength. However, in the precipitation hardened state, A100 is extremely difficult to conventionally machine so allowance should be made for this if combining additive and subtractive processes.
What causes cracking or internal defects when printing with A100?
Too high cooling rate, lack of appropriate thermal supports, and uncontrolled residual stresses from overly intense scanning strategies that create too steep thermal gradients in the powder bed as it solidifies. Optimizing parameters help avoid these root causes.
How should failed A100 prints be recycled?
Filter and sieve non-sintered A100 powder to remove large contaminates or spatter after print failures. Test flow rates and chemistry to ensure properties remain consistent before blending back into fresh powder at less than 30% contamination ratios.