Aluminium alloys powder refers to powder metallurgy forms of aluminium alloys. This powder can be used to manufacture parts and components through methods like metal injection molding, additive manufacturing, powder compacting, and more.
Overview of Aluminium Alloys Powder
Aluminium alloy powders provide advantages like ability to produce complex shapes, good finishing, and mechanical properties close to forged products. Key details:
- Alloying elements like silicon, magnesium, zinc, copper are added to enhance properties
- Particle size, morphology, flowability are key powder characteristics
- Gas atomization and mechanical alloying are common production methods
- Applications include automotive parts, aircraft components, electronics, etc.
Table 1: Key Details of Aluminium Alloys Powder
Parameter | Details |
---|---|
Base Metal | Aluminium |
Alloying Elements | Si, Mg, Zn, Cu, Mn, Ni, Fe, Cr |
Particle Size | 10 – 150 microns |
Production Methods | Gas Atomization, Mechanical Alloying |
Properties | Strength, Wear Resistance, Conductivity |
Applications | Automotive, Aerospace, Electronics |
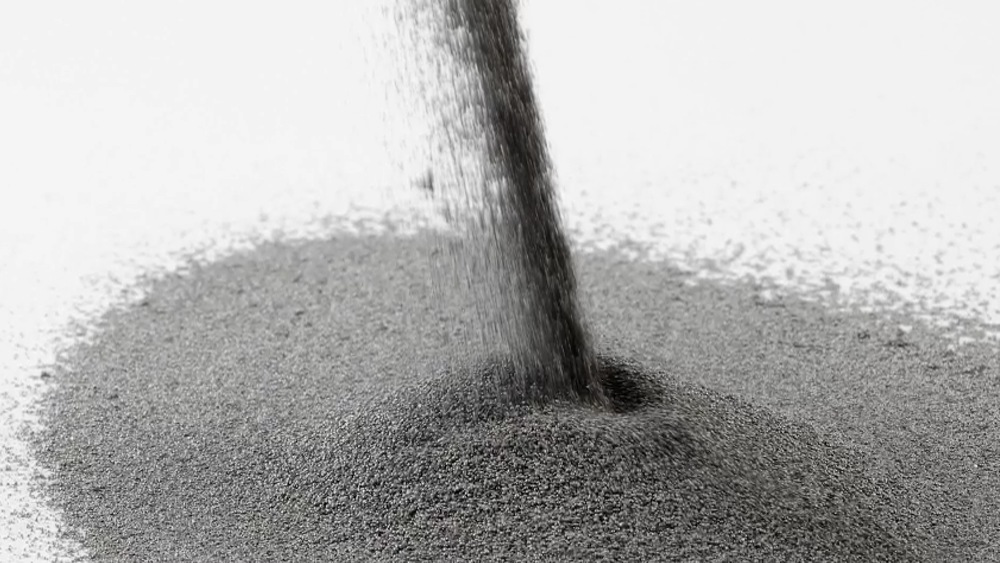
Types of Aluminium Alloys Powder
Many standardized and customised aluminium alloy powder compositions are available. Common alloy systems include:
Table 2: Major Types of Aluminium Alloys Powder
Alloy Family | Alloy Designations | Composition |
---|---|---|
1xxx Series | 1350, 1370 | 99% Al, Cu |
2xxx Series | 2024, 2219 | Al-Cu |
5xxx Series | 5052, 5083 | Al-Mg |
6xxx Series | 6060, 6061, 6063 | Al-Mg-Si |
7xxx Series | 7050, 7055, 7175 | Al-Zn |
These provide unique balances of corrosion resistance, strength, formability and other properties. Custom alloys tailored for additive manufacturing are also offered.
Composition and Powder Characteristics
Alloying elements, particle size distribution, morphology and flow rates are important powder parameters influencing manufacturing process and final part qualities.
Table 3: Aluminium Alloys Powder Composition and Characteristics
Parameter | Details | Role |
---|---|---|
Alloying Elements | Mg, Si, Cu, Zn, Ni, etc. | Modify strength, hardness, corrosion resistance, conductivity |
Particle Size | 10 – 150 microns typical | Affects densification, finishing |
Particle Morphology | Spherical, satellite, irregular | Impacts flow and packing density |
Flow Rates | Hall flow test > 12 s/50g | Ensure smooth feeding into equipment |
Gas atomized aluminium powders have spherical particles beneficial for flow and packing. Irregular shapes from mechanical production lower these metrics but allow economic alloying.
Properties and Performance
Following properties of aluminium alloys powder influence their role and manufacturing method selection:
Table 4: Properties of Aluminium Alloys Powder
Property | Role and Details |
---|---|
Strength | Varies from 100 – 700 MPa+ based on alloy, heat treatment |
Hardness | Between 50 – 200 HB; Increased by alloy selection, quenching |
Density | Around 2.7 g/cc |
Melting Point | 500°C – 660°C for common alloys |
Thermal Conductivity | Up to 200 W/mK, varies by alloy composition |
Electrical Conductivity | 30 – 40% of pure aluminium |
Corrosion Resistance | Fair, improved by surface treatments |
Cost | $5-50 per kg, depends on alloy and atomization method |
These represent typical properties – precise values depend on composition, powder size, part geometry and other specifics.
Applications and Uses
Key application areas taking advantage of aluminium alloys powder’s properties:
Table 5: Applications of Aluminium Alloys Powder
Industry | Application Examples | Benefits |
---|---|---|
Automotive | Pistons, connecting rods, gears | Light weighting, some strength |
Aerospace | Structural and transmission components | Strength-to-weight ratio |
Electronics | Heat sinks, connectors, encapsulations | Thermal management |
Defense | Grenades, projectiles, decoys | Fragmentation, radar confusion |
General | Gearboxes, luggage parts, antennas | Corrosion resistance, economy |
Aluminium metal injection molding in particular allows affordable medium-to-high volume manufacturing of complex, tight tolerance products across industries.
Specifications, Standards and Grades
Key aluminium alloy powder specifications, sizes and standards include:
Table 6: Specifications and Standards for Aluminium Alloys Powder
Standard/Specification | Details |
---|---|
ISO Standards | ISO 22068 – Powder sizes <150 μm |
ASTM Standards | ASTM B951 – Chemical compositions for metal injection molding |
Available Grades | Custom alloys, 2013, 2024, 2219, 5052, 6061, 7050, 7075 |
Particle Size Distribution | D10, D50, D90 measures in microns |
Apparent Density | In g/cc based on Hall flow meter test |
Tap Density | In g/cc, indicates packing density |
Flow Rates | Hall flow in sec/50 g, avalanche angle |
Chemistry | Al, Mg, Si, Fe, Cu content in % wt verified |
These help define product performance. Conformance certifications to company-specific specifications are also common in supply contracts.
Selecting Aluminium Alloy Powders
Consider these aspects when selecting appropriate grade:
Table 7: Criteria for Selecting Aluminium Alloys Powder
Parameter | Factors to Consider |
---|---|
Alloy Type | Required strength, ductility, corrosion resistance, conductivity |
Particle Size Range | Finish quality needed, manufacturing method constraints |
Particle Morphology | Impact on powder flow rates, density after compaction |
Apparent Density | Higher is better for high sintered density |
Cost | Purity, production method (atomization > mechanical alloying) |
Availability | Longer lead times for custom alloys |
Balance performance needs like strength and corrosion resistance against cost, availability and manufacturability considerations.
Suppliers and Pricing
A range of global specialty metal powder suppliers offer aluminium alloys:
Table 8: Aluminium Alloy Powder Suppliers and Indicative Pricing
Supplier | Indicative Pricing |
---|---|
Sandvik | $5 – $15 per kg |
Pometon | $10 – $40 per kg |
Carpenter Additive | $15 – $50 per kg |
AP&C | $25 – $45 per kg |
Rio Tinto Metal Powders | $20 – $60 per kg |
Large volume OEM contracts attract far lower rates. Prices depend on order volumes, alloy composition, atomization method and purity levels.
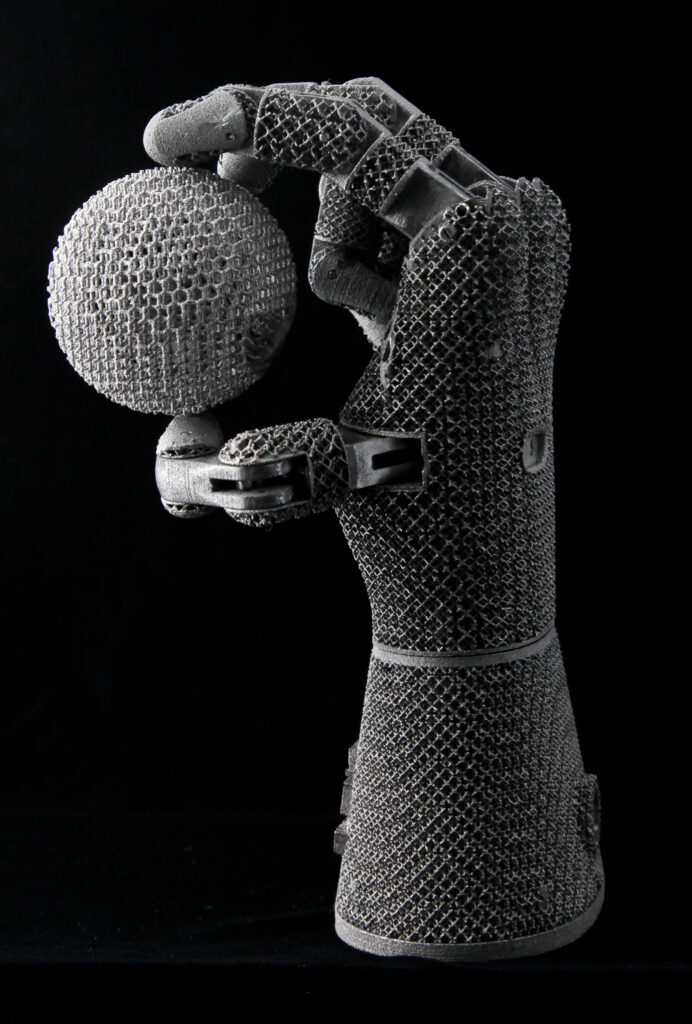
Pros and Cons of Aluminium Alloy Powder
Table 9: Advantages and Limitations of Aluminium Alloy Powder
Advantages | Limitations |
---|---|
Lightweight parts possible | Lower strength than steels |
Complex, net shape geometries feasible | Limited high temperature properties |
Range of alloy choices available | Post-processing often required |
MIM cost-effective for medium volumes | Powder can be expensive |
Good finishing and tolerances | Susceptible to corrosion in some alloys |
FAQs
Q: What are the most common aluminium alloys for powder metallurgy?
A: 6061, 6063, 7075 are most popular but many customized alloys optimized for additive manufacturing and metal injection molding are also used.
Q: Does aluminium alloy powder require special storage or handling precautions?
A: Inert gas blanketing and cool, dry storage is recommended. Handling systems should prevent ignition of fine powders.
Q: What particle size is best suited for metal AM vs injection molding of aluminium alloys?
A: Metal AM generally uses 20-65 microns while MIM aluminium powders are typically around 10-25 microns.
Q: What post-processing heat treatments are performed on aluminium MIM components?
A: Solution treatment, aging/precipitation hardening, quenching and tempering are often used depending on the alloy and properties needed.
Q: Is aluminium alloy powder reusable through reconditioning?
A: Yes, companies offer reconditioning and sieving services to salvage used powder for reuse. But properties may not be identical to virgin powder.