H13 tool steel powder is a versatile material used in powder metallurgy and metal additive manufacturing applications. This guide provides a comprehensive overview of H13 powder – composition, properties, specifications, uses, suppliers, and pros/cons.
Overview of H13 Tool Steel Powder
H13 tool steel powder is an alloy steel powder used for making tooling, dies, and wear-resistant components. Key features:
- Excellent resistance to thermal fatigue and heat checking
- High hardenability for uniform through-hardening
- Good combination of toughness and high compressive strength
- Commonly used in hot work tooling applications
- Available in various size distributions for pressing and additive manufacturing
Its properties make H13 powder suitable for demanding tooling needs in hot work environments.
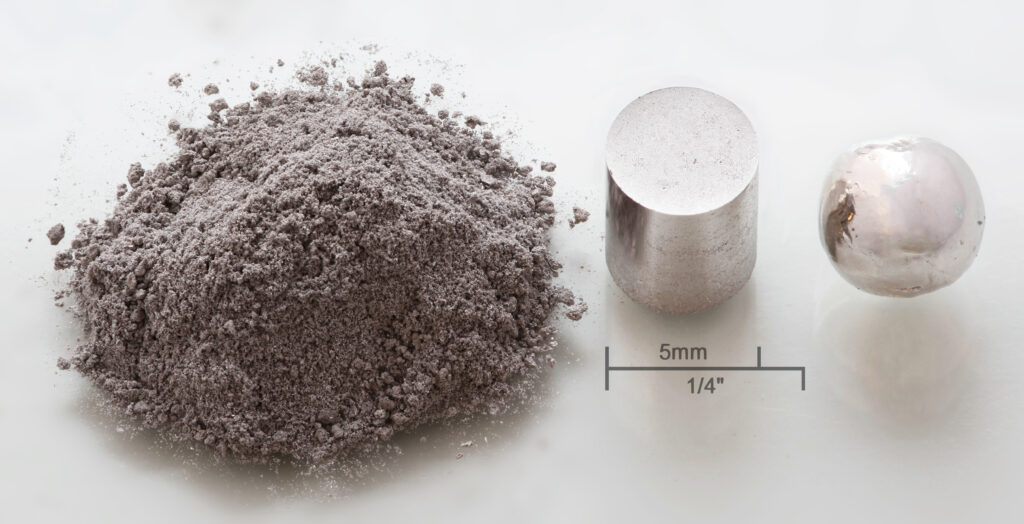
Composition and Properties of H13 Powder
H13 tool steel powder has the following nominal composition and properties:
Chemical Composition of H13 Powder
Element | Weight % |
---|---|
Carbon | 0.32-0.45 |
Chromium | 4.75-5.50 |
Molybdenum | 1.10-1.75 |
Vanadium | 0.80-1.20 |
Manganese | 0.20-0.50 |
Silicon | 0.80-1.20 |
Physical Properties of H13 Powder
- Density: 7.3 g/cm3
- Melting Point: 2640°F (1450°C)
- Thermal conductivity: 21 W/m-K at 68°F (20°C)
Mechanical Properties
- Hardness: 48-54 HRC when oil quenched and tempered
- Tensile strength: 1900-2100 MPa
- Yield strength: 1650 MPa
- Elongation: 8-10%
- Reduces hardness and ductility at temperatures above 1000°F
Its balanced alloying improves hardenability, heat resistance and toughness.
Powder Characteristics and Specifications
H13 tool steel powder is available in various size distributions:
H13 Powder Size Distributions
Size Range | Description | Typical Uses |
---|---|---|
15-45 μm | Finer powder for pressing small and complex tooling features | Compacts for metal injection molding |
45-106 μm | Coarser powder suitable for most press and sinter tooling | Conventional press and sinter process |
15-53 μm | Mixed powder for good packing density | Binder jetting or inkjet 3D printing |
45-150 μm | Larger particles for better flowability | Laser powder bed fusion additive manufacturing |
Specifications
- ASTM A581: Standard specification for free-machining stainless and heat-resisting steel bars, hot-rolled or cold-finished
- ISO 4957: Tool steels
- AWS A5.13: Specification for welding iron-base flux cored electrodes
H13 powder composition and size meets common standards for tool steel.
Applications of H13 Powder
Typical applications taking advantage of H13’s properties:
H13 Powder Applications
Industry | Common Uses |
---|---|
Metal manufacturing | Die casting dies, extrusion dies, forging dies, injection molds |
Plastics manufacturing | Blow molds, compression molds, thermoforming molds, injection molds |
Automotive | Trimming and piercing punches, forming rolls |
Aerospace | Forming and molding tools |
Additive manufacturing | Laser powder bed fusion, binder jetting |
H13’s combination of heat resistance, hardness, and toughness make it ideal for hot work tooling applications up to ~600°F and short exposures above.
Suppliers and Pricing
H13 tool steel powder is available from major suppliers:
H13 Powder Suppliers
Supplier | Description |
---|---|
Sandvik | Global tool steel manufacturer. Wide range of Osprey H13 powders. |
Höganäs | Major iron and steel powder producer. H13 powder for pressing. |
Carpenter Additive | Produces H13 powder for additive manufacturing. |
CNPC Powder | Supplies H13 powder meeting common specifications. |
Erasteel | Provides customized size distributions of H13 powder. |
H13 Powder Pricing
As a specialty tool steel powder, H13 is more expensive than simple iron or stainless steel powders:
- 15-45 μm H13 powder: ~$14/lb
- 45-150 μm H13 powder: ~$12/lb
- Pricing varies based on size, quantity, supplier, and geographical region.
Contact suppliers directly for quantity discounts to optimize cost.
Pros and Cons of H13 Powder
Advantages | Disadvantages |
---|---|
Excellent resistance to thermal fatigue and heat checking | Limited hot hardness – starts losing strength above 1000°F |
Uniform hardening through larger cross sections | Prone to cracking if sections above 2-3″ are quenched |
Toughness for withstanding impact stresses | Requires post-hardening tempering treatment |
Dimensional stability in service | More expensive than carbon steel powder |
Widely available from major suppliers | Surface oxidation can be a problem above 1000°F |
H13 powder provides an optimal balance of properties for most hot work tooling uses despite some limitations.
H13 vs. H11 Powder Comparison
H13 and H11 are similar chrome hot work tool steels. Key differences:
Parameter | H13 Powder | H11 Powder |
---|---|---|
Composition | 5% chromium | 8% chromium |
Hot hardness | Moderate up to 1000°F | Better retention up to 1100°F |
Toughness | Higher | Lower toughness |
Thermal fatigue resistance | Excellent | Good, not as strong as H13 |
Cost | Moderate | Lower cost than H13 |
For the best combination of heat resistance, toughness and cost, H13 is generally preferred over H11 for most hot work tooling applications.
FAQ
What is H13 tool steel used for?
H13 is commonly used for hot work tooling applications like die casting dies, hot forging dies, extrusion tooling, plastic injection molds exposed to high temperatures.
What hardness is H13 after heat treatment?
Typical hardness for annealed H13 is 217 HB. Hardened and tempered H13 typically achieves 48-54 HRC depending on temper condition.
Can you machine H13 tool steel?
Yes, H13 can be machined in annealed or pre-hardened states using proper tooling and techniques. Hardness over 45 HRC requires grinding or EDM.
What is the difference between H13 and D2 tool steel?
H13 has better hot hardness and heat checking resistance than D2. D2 has higher wear resistance and achieves greater hardness when heat treated optimally.
Is H13 tool steel good for knives?
While very hardenable, H13 has lower toughness than steels like 440C or D2, making it less suitable for most knife applications.
With its balanced properties and availability, H13 tool steel powder is an excellent choice for hot work tooling needs.
Conclusion
H13 tool steel powder provides an ideal combination of heat and wear resistance, hardenability, and toughness for demanding hot work tooling applications. Its Chromium-Molybdenum-Vanadium alloy composition gives excellent thermal fatigue life and resistance to heat checking up to 600°F. H13 powder can be pressed and sintered or used in additive manufacturing to create durable tooling economically. Global suppliers provide H13 powder in various size distributions to suit different fabrication processes. With capabilities between conventional carbon steel and exotic super alloys, versatile H13 powder will continue seeing wide use in die casting, forging, extrusion, and injection mold tooling.