Overview of Superalloy Powder
Superalloy powder is a high-performance material used to produce parts for demanding applications in aerospace, power generation, and industrial processes. Superalloys have excellent mechanical strength, resistance to thermal creep deformation, surface stability, and corrosion/oxidation resistance at high temperatures.
Superalloy powders are alloy compositions produced via gas atomization into fine powders with particle sizes suitable for powder metallurgy techniques. The most widely used superalloys are nickel, cobalt or iron-based alloys. Nickel-based superalloys make up over 50% of the total share. The grain structure and unique properties of superalloys are due to solid solution strengthening by refractory metals like molybdenum and tungsten along with precipitation hardening by intermediate phases.
Key properties and characteristics of superalloy powders:
Property | Characteristics |
---|---|
Composition | Nickel, cobalt, iron-based alloys with chromium, aluminum, titanium, tantalum etc. |
Alloying elements | Chromium, aluminum, titanium, molybdenum, tungsten, niobium, tantalum |
Manufacturing process | Gas atomization into fine spherical powders |
Particle shape | Spherical morphology ideal for powder metallurgy |
Particle size distribution | Typically 10 – 45 microns |
Powder flowability | Good flow characteristics |
Thermal stability | Retain strength at temperatures over 1000°C |
Density | Around 8-9 g/cm3 |
Strength | Very high strength up to 1300 MPa |
Corrosion resistance | Excellent oxidation and corrosion resistance |
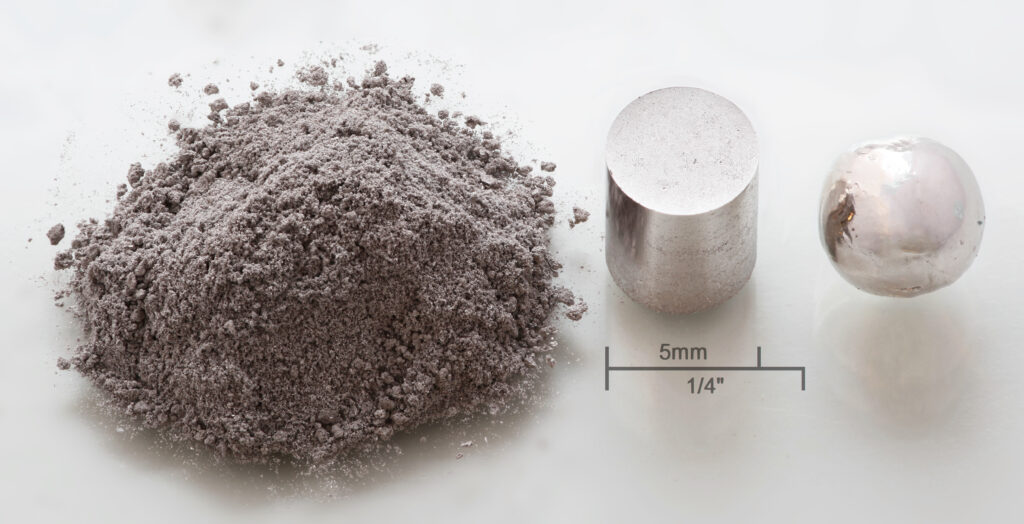
Applications and Uses of Superalloy Powder
Superalloy powder has become an indispensable material across aerospace, power generation, and general industrial sectors due to its high performance properties. Some key applications include:
Industry | Applications |
---|---|
Aerospace | Turbocharger wheels, turbine blades, discs, fasteners, rocket nozzles, thrust reverser systems |
Power generation | Turbine blades, discs, shafts for land-based gas turbines, generators |
Oil and gas | Downhole tools, valves, drill bits, completion tools |
Automotive | Turbocharger components, valves, rings, exhaust components |
General industry | Extrusion dies, forming tools, valve and pump parts, heat treatment fixtures |
Chemical processing | Heat exchangers, reaction vessels, valves |
The unique capability of superalloys to maintain mechanical strength, creep resistance, and oxidation/corrosion resistance at high temperatures above 1000°C makes them indispensable in jet engines, land-based gas turbines, as well as applications involving extreme environments. Their use continues rising across industries.
Types of Superalloy Powders
Many variants of superalloy powder have been developed over the decades to meet increasingly demanding property requirements. They can be categorized into several major alloy families:
Nickel-Based Superalloys
Nickel-based superalloys make up over 50% of all superalloys produced. Their high temperature strength comes from solid solution strengthening by refractory metals like Mo, Ta, W and precipitation hardening by intermediate phases like Ni3(Al, Ti). Common alloys are:
- Inconel 718
- Inconel 625
- Rene 65
- Waspaloy
Cobalt-Based Superalloys
These contain more than 50% cobalt and elements like chromium, tungsten and molybdenum. They have excellent high temperature strength up to 1100°C. Common alloys are:
- Haynes 25
- FSX-414
- Haynes 188
Iron-Based Superalloys
Iron-nickel and iron-nickel-cobalt alloys strengthened with additions of chromium, aluminum and yttrium. They are more ductile and cheaper but have lower strength than Ni and Co alloys. Examples are:
- A-286
- 901
- 903
Oxide Dispersion-Strengthened Superalloys
These contain highly stable oxide particles like yttria that hinder dislocation motion. This provides excellent creep resistance at extreme temperatures beyond 1100°C. Alloys are:
- MA-6000E
- MA-754
- MA-6000
Superalloy Powder Specifications
Superalloy powder is produced in various alloy grades and powder size distributions to meet requirements of different additive manufacturing processes and final part properties.
Parameter | Details |
---|---|
Alloy grades | Inconel 718, Haynes 282, Rene 65, Hastelloy X, 316L, 17-4PH etc. |
Powder size | 10 – 45 microns typical |
Particle shape | Spherical morphology |
Size distribution | Unimodal distributions like 10-25μm or bi-modalmixtures like 10-45 μm |
Flowability | Hall flowrate > 28 s/50g, AOR > 0.80 |
Apparent density | Around 2 – 5 g/cc loose powder to 60% dense parts |
Purity | >99.9%, gas atomization gives high purity |
Oxygen content | <100 ppm |
Hydrogen content | <5 ppm |
Critical parameters are powder size, shape, chemical composition, flow characteristics, apparent density, and purity levels. These determine processability as well as final part quality.
Superalloy Powder Design Standards
While superalloys were initially designed using empirical development, computational thermodynamics now allows predicting phase equilibria and properties.
Standard | Description |
---|---|
AMS 5383G | Standard specification for nickel-based superalloy powders for rhenium-free applications |
AMS 5662M | Carburization and heat treatment of nickel alloy parts |
AMS 2759/6 | Age hardening heat treatment for superalloy investment castings |
AMS 2774A | Heat treatment of cobalt alloy parts |
AMS 5664M | Preparation of cobalt alloy parts for thermal processing |
ASTM B214 | Standard for superalloy powder characterization |
ISO 4957:1999 | Method to determine powder flow rate |
Both ASTM International and ASM International provide extensive resources on recommended practices for superalloy powder production, thermal processing, quality control, testing procedures, and applications.
Superalloy Powder Manufacturing Process
Gas atomization is the primary technique for production of fine superalloy powder suitable for additive manufacturing. The process involves:
- Induction melting ingots of the alloy composition
- Pouring the melt stream into a close-coupled atomization nozzle
- Breaking up the melt into fine droplets by high pressure atomization gas (N2 or Ar)
- Solidification of powder as spherical particles in the spray chamber
- Collection of classified powder fractions
The cooling rate of 106 K/s gives a fine grained microstructure. Powders display spherical morphology critical for flowability.
Superalloy Powder Pricing
Superalloy powder is a premium material with pricing depending on the alloy grade, quality level, lot size and manufacturer. Some typical price ranges are:
Superalloy | Price Range |
---|---|
Inconel 718 | $50 – $120 per kg |
Inconel 625 | $60 – $250 per kg |
Haynes 282® | $60 – $120 per kg |
Rene 65 | $150 – $200 per kg |
Prices depend on:
- Base metal prices – nickel, cobalt, chromium
- Purity levels
- Powder quality – particle size distribution, flowability, apparent density
- Order quantity – 1 kg to tonnage bulk orders
- Manufacturer’s proprietary composition, quality standards
Top Superalloy Powder Suppliers
Major global suppliers of high-performance superalloy powders include:
Supplier | Key Products |
---|---|
Sandvik Osprey | Rene 65, Inconel 718, 625, Hastelloy X |
Lockheed Martin | Ti-6Al-4V, Inconel 718, 316L |
Praxair | Ti-6Al-4V titanium, cobalt alloys |
AP&C | Rene 65 and 88, Astroloy, LSHR |
Tekna Advanced Materials | UDIMET 720, A286, 316L, 17-4PH |
Carpenter Additive | 17-4PH, IN625, Ti-6Al-4V |
Oerlikon Metco | Waspaloy, Hastelloy X, Haynes 282 |
Erasteel | Custom nickel and iron-based alloys |
Factors to consider when selecting a supplier include:
- Range of alloys offered
- Consistency in chemical composition and powder quality
- Lower oxygen and nitrogen impurity levels
- Batch testing data for critical parameters
- Pricing relative to quality level and properties
- Lead time and delivery schedules
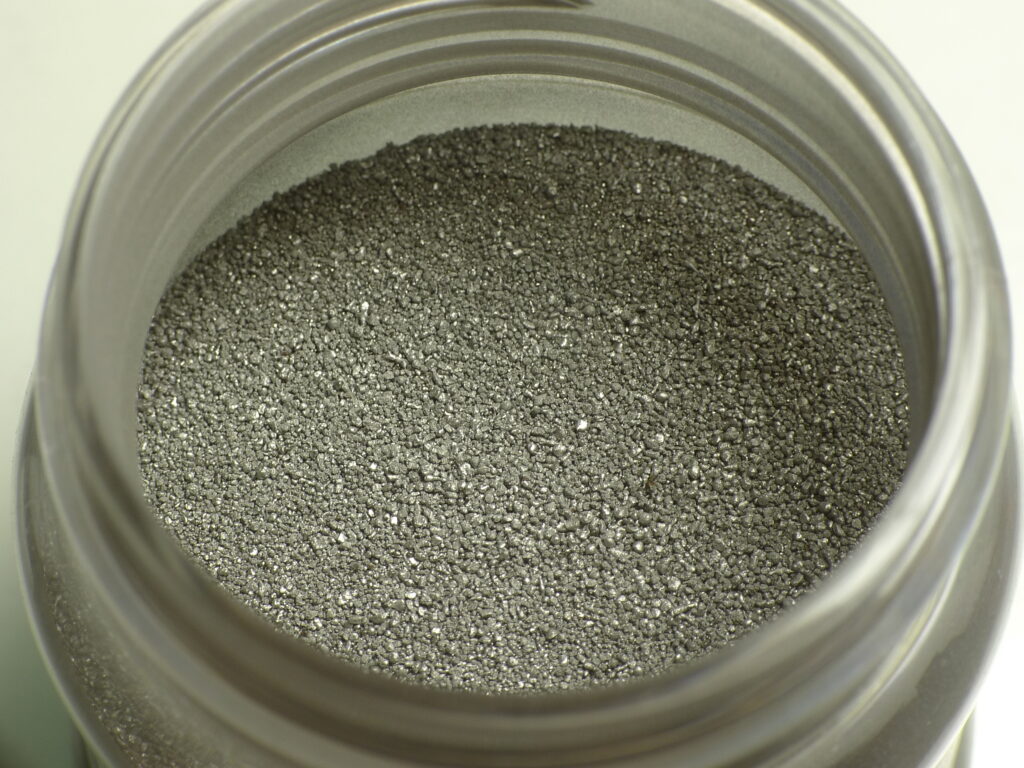
Installing Superalloy Powder Processing Equipment
Special precautions are needed when handling fine reactive superalloy powders to prevent contamination or explosions.
Activity | Equipment/Supplies Needed |
---|---|
Powder delivery | Glove boxes, sealed containers |
Powder storage | Inert gas storage units, cabinets with argon/nitrogen |
Handling | Protective apparel, face masks, gloves |
Sieving | Enclosed sieves, cyclone sieving units |
Blending | Enclosed tumble/drum blenders |
Hopper loading | Glove box connections to printer hopper |
All powder handling systems should be oxygen-free and moisture-free to prevent contamination. Protective apparel and masks should be worn to avoid inhaling fine powder. Proper grounding must be ensured to prevent static charge buildup.
Best Practices for Operating Superalloy Powder Printers
Achieving defect-free prints with superalloy powder requires optimizing the entire AM workflow:
Stage | Best Practices |
---|---|
Superalloy powder | Use fresh powder with ideal size distribution and morphology |
Printer setup | Calibrate laser power, scan paths, recoating mechanism. Maintain inert gas levels. |
Software settings | Optimize process parameters – layer height, scan patterns, speeds |
Print job | Adjust orientation and supports. Monitor powder bed, laser paths and temperature. |
Post-processing | Stress relief, Hot Isostatic Pressing, heat treatment, HIP and machining to improve properties |
Critical factors are an optimal powder bed, calibrated energy input, and minimizing internal stresses. Matching software parameters to alloy type and target properties is key. Careful thermal post-processing enhances final part performance.
Maintaining Superalloy Powder Printers
Regular preventive maintenance of key components is essential for reliable operation and maximum printer uptime.
System | Maintenance Tasks | Schedule |
---|---|---|
Powder delivery | Inspect piston seals, replace worn seals | Monthly |
Recoating blades | Clean, replace worn parts | Weekly |
Laser optics | Clean lenses, mirror, maintain alignment | Before each production build |
Beam delivery system | Check galvanometers, focus lens motion | Monthly or per 500 hours |
Chambers | Seal checks, gas leak tests | Monthly or per 100 hours |
Sintering system | Check heating elements, thermocouples | Monthly or per 500 hours |
Gas delivery | Monitor pressure gauges and flow meters | Daily |
Vacuum system | Inspect pumps, seals and lines | Monthly or per 500 hours |
Strict adherence to OEM maintenance schedules is vital for reliable operation and best print quality over time.
How to Select a Superalloy Powder Supplier
Choosing the right superalloy powder supplier is crucial for manufacturing high-quality components via metal additive manufacturing. Here are key factors to consider:
- Range of alloy varieties available
- Consistent chemical composition from batch-to-batch
- Controllable particle size distribution based on nominal range
- Spherical morphology and flowability
- Low oxygen/nitrogen impurity levels
- Apparent density and hall flow rates as per specifications
- Detailed certificate of analysis for each powder lot
- Capability to customize alloys and particle size distribution
- Competitive pricing relative to quality level
- Reputation, experience, and customer reviews
- Lead time and delivery reliability
- Response to technical queries and support
Samples builds to assess powder performance first-hand are recommended. Prioritize quality consistency over lowest pricing to avoid print defects.
Advantages of Superalloy Powder
Superalloy powder offers unique benefits driving its expanded use for critical metal AM components:
- Retains high strength and modulus above 1000°C
- Resists creep deformation under load at high temperatures
- Withstands thermal fatigue and dynamic stresses
- Excellent oxidation and corrosion resistance
- Lower coefficient of thermal expansion than steels
- Fine microstructures from rapid solidification as powder
- Achieves complex shapes unfeasible by casting/machining methods
- Reduces raw material waste relative to subtractive methods
- Allows weight and performance optimization of designs
- Powder bed fusion AM enables complex passageways and cooling channels
The combination of outstanding mechanical properties at extreme environments, shape complexity, and minimized raw material waste make superalloys ideal for production parts via powder bed fusion additive manufacturing.
Limitations of Superalloy Powder
While superalloys deliver unmatched performance, certain limitations need consideration:
- Very high cost of raw superalloy powder material
- Limited number of qualified suppliers for aerospace-grade powder
- Variable powder composition, size distribution, and flow characteristics
- High sensitivity of properties to impurities and defects
- Tendency for porosity in as-printed components
- Requirement of HIP and heat treatment for requisite properties
- Anisotropy and internal stresses add machining requirements
- High manual labor requirement for support removal
- Limited sizes for powder bed fusion, typically under 500 mm
- Challenge in achieving tight dimensional tolerances in AM parts
The high cost of quality superalloy powder combined with additional post-processing are key limitations for wider adoption currently.
Superalloy Powder vs Traditional Manufacturing
Here is a comparison between using superalloy powder for AM vs conventional casting/forging methods:
Factor | Superalloy powder AM | Casting/forging |
---|---|---|
Raw material waste | Very low, only requires amount of powder to build part | High material losses from machining, shaping steps |
Cost per part | Higher, expensive powder plus multiple post-processing steps | Lower due to economies of scale |
Lead time | Longer due to post-processing requirements | Shorter, established industrial processes |
Value gain | Design freedom, weight reduction, performance gains | Mature technologies, predictable output |
Quality control | Critical assessment needed of powder and as-printed parts | Certified materials, validated processes |
Supply chain maturity | Still evolving with few qualified suppliers | Established industry with certified suppliers |
Applications | Complex parts, high performance, low volumes | Simpler geometries, mass production |
While powder AM enables breakthrough part designs and properties, conventional manufacturing still scores for supply chain maturity and per-part cost at production volumes. Both will continue evolving.

FAQs
What are the most common types of superalloy powder used in AM?
The most widely used superalloy powders for additive manufacturing are nickel-based alloys like Inconel 718, Inconel 625, and cobalt-based alloys like Haynes 282.
What particle size distribution is optimal for AM?
A particle size range of 15-45 microns is recommended, though size requirements depend on the specific additive manufacturing process. For binder jetting, sub-20 micron average size is preferred.
What factors affect the costs of superalloy powder?
The costs depend primarily on the base alloying elements like nickel and cobalt. Tighter controls on powder size distribution, impurities, and quality result in higher costs as well. Minimum order volumes from suppliers also affect per-unit pricing.
Why is shape important for superalloy powders?
Spherical particle shape allows uniform powder spreading and densification during printing. Irregular shapes make powder flow difficult and create defects in printed components.
How are superalloy powders kept from oxidizing during storage and handling?
Superalloy powders are highly sensitive to oxidation and moisture absorption. All handling steps are performed in sealed gloveboxes under inert argon or nitrogen gas to prevent oxidation.
What post processing steps are used on AM superalloy components?
Most as-printed superalloy components undergo solution annealing followed by aging heat treatments to achieve optimal microstructures and mechanical properties comparable to wrought materials. Hot isostatic pressing (HIP) is also used to eliminate internal voids and porosity.
What are some examples of parts made from superalloys using AM?
Additive manufacturing with superalloys is used to make combustion chamber liners, fuel nozzles, turbine blades and vanes, blades and disks for jet engines, tubes for petrochemical furnaces, turbomachinery components, and lightweight structural parts for aerospace.
What AM technologies are used with superalloy powders?
The most common methods are powder bed fusion processes including selective laser melting (SLM), direct metal laser sintering (DMLS) and electron beam melting (EBM). Binder jetting is also emerging for making superalloy components.
How does superalloy powder AM compare with subtractive methods?
AM enables lighter, more complex part geometries unattainable by subtractive methods like machining. But subtractive techniques have more mature supply chains and lower costs per part at production volumes currently. Both continue advancing rapidly.