Partikelgrößenverteilung (PSD) ist ein grundlegendes Konzept in verschiedenen Bereichen, von der Pharmazie bis zur Metallurgie, und ist entscheidend für das Verständnis des Materialverhaltens, die Optimierung von Herstellungsprozessen und die Gewährleistung der Produktqualität. Ganz gleich, ob Sie mit Metallpulvern, Polymeren oder pharmazeutischen Inhaltsstoffen zu tun haben, die Kenntnis der Feinheiten der PSD kann den Erfolg Ihres Projekts erheblich beeinflussen. Dieser umfassende Leitfaden befasst sich mit den wichtigsten Aspekten der Partikelgrößenverteilung, insbesondere mit ihrer Bedeutung für Metallpulver, ihrer Messung und ihrer Bedeutung für Ihre Anwendungen.
Überblick über die Partikelgrößenverteilung
Die Partikelgrößenverteilung bezieht sich auf den Bereich und die Häufigkeit der Partikelgrößen innerhalb einer bestimmten Probe. Stellen Sie sich vor, Sie haben eine Handvoll Sand; einige Körner sind winzig, andere wiederum sind größer. Die Variation dieser Größen und die Häufigkeit, mit der jede Größe in der Mischung vorkommt, bilden die Partikelgrößenverteilung. In der Industrie ist die PSD von entscheidender Bedeutung, da sie Materialeigenschaften wie Fließfähigkeit, Packungsdichte, Oberfläche und Reaktivität beeinflusst.
Warum die Partikelgrößenverteilung wichtig ist
Das Verständnis der PSD ist von entscheidender Bedeutung, da sie verschiedene Materialeigenschaften und -verhaltensweisen beeinflusst:
- Fließfähigkeit: Feinere Partikel können zusammenkleben, was das Fließverhalten eines Materials beeinträchtigt.
- Reaktivität: Kleinere Partikel haben oft eine größere Oberfläche, wodurch sie reaktionsfreudiger sind.
- Packungsdichte: Die Mischung der Partikelgrößen bestimmt, wie dicht ein Material gepackt werden kann, was sich auf seine Festigkeit und Stabilität auswirkt.
- Produktkonsistenz: Bei Arzneimitteln beispielsweise beeinflusst PSD die Aufnahme von Medikamenten im Körper.
Verständnis der Partikelgrößenverteilung in Metallpulvern
Was sind Metallpulver?
Metallpulver sind feine Partikel aus Metallen oder Legierungen, die in verschiedenen Herstellungsverfahren verwendet werden, darunter in der additiven Fertigung, der Pulvermetallurgie und bei Beschichtungsanwendungen. Die Größe und Verteilung dieser Partikel kann die Qualität, Festigkeit und Leistung des Endprodukts drastisch beeinflussen.
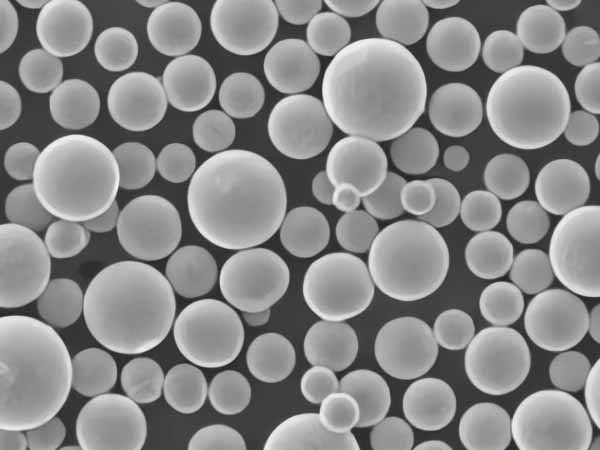
Die Bedeutung von PSD bei Metallpulvern
Die Partikelgrößenverteilung von Metallpulvern ist entscheidend für die Fließfähigkeit, die Packungsdichte und das Sinterverhalten bei der Herstellung. Zum Beispiel:
- Fließfähigkeit: Ideal für Verfahren wie den 3D-Druck, bei denen ein gleichmäßiger Fluss durch die Düsen erforderlich ist.
- Packungsdichte: Beeinflusst die Dichte und Festigkeit des Endprodukts.
- Sintern: Kleinere Partikel sinken in der Regel bei niedrigeren Temperaturen, was sich auf die Energieeffizienz des Prozesses auswirkt.
Arten von Metallpulvern und ihre PSD-Eigenschaften
In der folgenden Tabelle sind einige gängige Metallpulver, ihre Zusammensetzung und ihre typischen PSD-Eigenschaften zusammengefasst.
Metall-Pulver | Zusammensetzung | Typisches PSD | Wesentliche Merkmale | Gemeinsame Anwendungen |
---|---|---|---|---|
Aluminium (Al) | Reines Aluminium | 10-100 µm | Leichtes Gewicht, gute Wärmeleitfähigkeit | Luft- und Raumfahrt, Automobilindustrie |
Rostfreier Stahl | Eisen, Chrom, Nickel | 15-150 µm | Korrosionsbeständig, langlebig | Medizinische Geräte, Küchengeräte |
Titan (Ti) | Reines Titan | 20-200 µm | Hohes Festigkeits-Gewichts-Verhältnis, biokompatibel | Luft- und Raumfahrt, medizinische Implantate |
Kupfer (Cu) | Reines Kupfer | 10-100 µm | Ausgezeichnete elektrische Leitfähigkeit | Elektronik, elektrische Verkabelung |
Nickel (Ni) | Reines Nickel | 15-150 µm | Hohe Korrosionsbeständigkeit, magnetische Eigenschaften | Batterien, Elektronik |
Bronze | Kupfer, Zinn | 20-200 µm | Hohe Verschleißfestigkeit, geringe Reibung | Lager, Buchsen |
Kobalt-Chrom | Kobalt, Chrom | 15-100 µm | Hohe Festigkeit, Korrosionsbeständigkeit | Zahnimplantate, Komponenten für die Luft- und Raumfahrt |
Eisen (Fe) | Reines Eisen | 10-120 µm | Magnetische Eigenschaften, hohe Festigkeit | Automobilindustrie, Bauwesen |
Inconel | Nickel, Chrom | 15-150 µm | Hohe Temperaturbeständigkeit, oxidationsbeständig | Luft- und Raumfahrt, chemische Verarbeitungsanlagen |
Magnesium (Mg) | Reines Magnesium | 20-150 µm | Leichtes Gewicht, gute Bearbeitbarkeit | Automobilindustrie, Elektronik, Luft- und Raumfahrt |
Faktoren, die die PSD in Metallpulvern beeinflussen
- Produktionsmethode: Durch Zerstäuben, Mahlen und Elektrolyse entstehen Pulver mit unterschiedlichen PSDs.
- Materialzusammensetzung: Verschiedene Legierungen können die Größenverteilung aufgrund unterschiedlicher Materialeigenschaften beeinflussen.
- Verarbeitungsbedingungen: Temperatur, Druck und andere Faktoren während der Pulverherstellung können die PSD beeinflussen.
Messtechniken für Partikelgrößenverteilung
Die genaue Messung der PSD ist für die Qualitätskontrolle in verschiedenen Industriezweigen unerlässlich. Es werden verschiedene Techniken verwendet, die jeweils ihre Vorteile und Grenzen haben.
Allgemeine Messtechniken
Technik | Grundsatz | Typischer Partikelgrößenbereich | Vorteile | Beschränkungen |
---|---|---|---|---|
Laserbeugung | Streuung von Laserlicht an Partikeln | 0,01-3000 µm | Schnell, weitreichend, nicht zerstörerisch | Unter der Annahme kugelförmiger Teilchen, teuer |
Siebung | Mechanische Trennung nach Maschenweite | 45-10000 µm | Einfach, kostengünstig | Begrenzt auf größere Partikel, zeitaufwändig |
Dynamische Lichtstreuung (DLS) | Schwankungen im Streulicht | 1 nm-6 µm | Hohe Empfindlichkeit, geeignet für Nanopartikel | Begrenzt auf kleine Partikelgröße, komplex |
Sedimentation | Sinkgeschwindigkeit in einer Flüssigkeit | 0,5-300 µm | Gut für feine Partikel | Langsam, abhängig von der Partikelform |
Mikroskopie | Direkte Beobachtung unter einem Mikroskop | 0,1-1000 µm | Sichtprüfung, Formanalyse | Zeitaufwendig, subjektiv |
Schar-Zähler | Die elektrische Impedanz ändert sich, wenn Partikel eine Öffnung passieren | 0,1-1200 µm | Präzise, große Reichweite | Teuer, erfordert leitfähige Flüssigkeit |
Die Wahl der richtigen Technik
Die Wahl der Messtechnik hängt von mehreren Faktoren ab:
- Partikelgrößenbereich: Einige Methoden sind besser für größere oder kleinere Partikel geeignet.
- Material: Die optischen Eigenschaften oder die Leitfähigkeit des Materials können die Methode bestimmen.
- Genauigkeit: Bei einigen Anwendungen kann eine höhere Genauigkeit erforderlich sein, was den Einsatz anspruchsvollerer Techniken rechtfertigt.
- Kosten: Aufgrund von Budgetbeschränkungen kann die Wahl auf kostengünstigere Methoden beschränkt sein.
Zusammensetzung der Partikelgrößenverteilung in Metallpulvern
Die Zusammensetzung der Partikelgrößenverteilung in Metallpulvern ist ein entscheidender Aspekt, der sich auf ihre Leistung in verschiedenen Anwendungen auswirkt. Dieser Abschnitt befasst sich mit den Besonderheiten der PSD-Zusammensetzung, einschließlich Faktoren wie der mittleren Partikelgröße, der Verteilungsbreite und dem Vorhandensein von feinen oder groben Partikeln.
Schlüsselparameter bei der PSD-Zusammensetzung
Parameter | Beschreibung |
---|---|
Mittlere Partikelgröße | Die durchschnittliche Größe der Partikel in einer Probe, oft in Mikrometern (µm) gemessen. |
Verteilung Breite | Der Bereich der Partikelgrößen innerhalb einer Probe, der auf Gleichmäßigkeit oder Variabilität hinweist. |
Feine Partikel | Partikel am unteren Ende der PSD, die die Fließfähigkeit und Reaktivität beeinträchtigen können. |
Grobe Partikel | Größere Partikel, die die Packungsdichte und Festigkeit beeinträchtigen können. |
Schrägheit | Die Asymmetrie der Verteilungskurve, die auf eine Tendenz zu feineren oder gröberen Partikeln hinweist. |
PSD in bestimmten Metallpulvern
Jedes Metallpulver weist eine einzigartige PSD auf, die seine Eigenschaften und seine Eignung für verschiedene Anwendungen beeinflusst. Hier sind einige Beispiele:
- Aluminium-Pulver: Typischerweise hat es eine schmale PSD mit einer mittleren Partikelgröße von etwa 20-30 µm, was es ideal für leichte Komponenten in der Luft- und Raumfahrt macht.
- Edelstahl-Pulver: Hat oft eine breitere PSD, die von 10 µm bis 100 µm reicht und ein ausgewogenes Verhältnis zwischen Festigkeit und Korrosionsbeständigkeit bietet.
- Titan-Pulver: PSD variiert stark, mit mittleren Größen von 15 µm bis 150 µm, zugeschnitten auf Anwendungen, die ein hohes Festigkeits-Gewichts-Verhältnis erfordern.
Anwendungen von Metallpulvern auf der Basis von PSD
Die Partikelgrößenverteilung spielt eine entscheidende Rolle bei der Bestimmung der Eignung von Metallpulvern für verschiedene Anwendungen. Nachfolgend finden Sie eine Tabelle mit einer Zusammenfassung gängiger Anwendungen und den jeweils bevorzugten PSD-Eigenschaften.
Anmeldung | Bevorzugtes Metallpulver | Idealer PSD-Bereich | Warum PSD wichtig ist |
---|---|---|---|
3D-Druck | Aluminium, Titan | 10-60 µm | Gewährleistet einen reibungslosen Ablauf und eine präzise Schichtung |
Pulvermetallurgie | Rostfreier Stahl, Eisen | 20-100 µm | Beeinflusst das Sinterverhalten und die Endfestigkeit |
Thermisches Spritzen | Nickel, Kupfer | 20-80 µm | Kontrolliert Schichtdicke und Gleichmäßigkeit |
Additive Fertigung | Kobalt-Chrom, Inconel | 15-50 µm | Kritisch für hochauflösende Teile |
Elektronik | Kupfer, Silber | 10-40 µm | Beeinträchtigt die Leitfähigkeit und die Integrität der Schaltkreise |
Automobilkomponenten | Magnesium, Eisen | 20-150 µm | Beeinflusst die Dichte und die mechanischen Eigenschaften der Teile |
Komponenten für die Luft- und Raumfahrt | Titan, Aluminium | 10-80 µm | Gleichgewicht zwischen Stärke und Gewichtseinsparung |
Medizinische Implantate | Titan, Kobalt-Chrom | 15-70 µm | Gewährleistet Biokompatibilität und Haltbarkeit |
Batterie-Materialien | Nickel, Lithium | 5-30 µm | Beeinflusst Energiedichte und Ladegeschwindigkeit |
Katalysatoren | Platin, Palladium | 1-20 µm | Maximiert die Oberfläche für chemische Reaktionen |
Die Auswirkungen der PSD auf spezifische Anwendungen
Bei jeder Anwendung kann die PSD des Metallpulvers die Leistung des Endprodukts erheblich beeinflussen. Zum Beispiel:
- 3D-Druck: Ein schmaler PSD sorgt dafür, dass das Pulver reibungslos durch die Druckdüse fließt, was eine präzise Beschichtung ermöglicht und Fehler minimiert.
- Pulvermetallurgie: Ein gut kontrollierter PSD führt zu einer gleichmäßigen Sinterung, was zu Bauteilen mit gleichmäßiger Dichte und Festigkeit führt.
- Thermisches Spritzen: Die PSD beeinflusst die Dicke und Gleichmäßigkeit der Beschichtung, was für Schutzbeschichtungen in rauen Umgebungen von entscheidender Bedeutung ist.
Vorteile von Optimized Partikelgrößenverteilung
Die Optimierung der Partikelgrößenverteilung in Metallpulvern bietet zahlreiche Vorteile für verschiedene Branchen. In diesem Abschnitt werden die wichtigsten Vorteile einer gut kontrollierten PSD hervorgehoben.
Verbesserte Materialeigenschaften
- Verbesserte Fließfähigkeit: Ein gleichmäßiger PSD verringert die Wahrscheinlichkeit von Verstopfungen in Fördersystemen und gewährleistet eine reibungslose Verarbeitung.
- Erhöhte Packungsdichte: Ein ausgewogenes PSD ermöglicht eine engere Packung, was zu dichteren und stärkeren Komponenten führt.
- Bessere Kontrolle der Oberfläche: Durch die Feinabstimmung der PSD kann die Oberfläche optimiert werden, was für Anwendungen wie Katalyse oder Batteriematerialien entscheidend ist.
Prozesseffizienz und Kosteneinsparungen
- Niedrigere Sintertemperaturen: Kleinere Partikel können bei niedrigeren Temperaturen gesintert werden, was den Energieverbrauch und die Kosten senkt.
- Weniger Abfall: Eine einheitliche PSD minimiert die Notwendigkeit der Wiederaufbereitung oder der Entsorgung von Off-Spec-Material, was zu Kosteneinsparungen führt.
- Verbesserte Ausbeute: Ein optimiertes PSD führt zu qualitativ hochwertigeren Produkten mit weniger Fehlern, was den Gesamtertrag erhöht.
Verbesserte Produktleistung
- Höheres Verhältnis von Festigkeit zu Gewicht: Besonders wichtig in der Luft- und Raumfahrt und in der Automobilindustrie, wo Gewichtseinsparungen entscheidend sind.
- Verbesserte Korrosionsbeständigkeit: Bestimmte PSDs können die schützenden Eigenschaften von Beschichtungen verbessern und so die Lebensdauer von Bauteilen verlängern.
- Bessere Wärmeleitfähigkeit: In der Elektronik kann ein optimiertes PSD das Wärmemanagement von Komponenten verbessern und Überhitzung verhindern.
Vergleich der optimierten mit der nicht optimierten PSD
Aspekt | Optimiertes PSD | Nicht-optimiertes PSD |
---|---|---|
Fließfähigkeit | Sanfter, gleichmäßiger Fluss | Möglichkeit der Verstopfung, unregelmäßiger Fluss |
Packungsdichte | Hoch, was zu starken Komponenten führt | Niedriger, was zu schwächeren Komponenten führt |
Kontrolle der Oberfläche | Präzise Steuerung, Verbesserung der Reaktivität | Unzureichend kontrollierte, uneinheitliche Leistung |
Sintertemperatur | Niedriger, energiesparend | Höhere, steigende Energiekosten |
Abfallreduzierung | Minimaler Abfall, kosteneffektiv | Mehr Abfall, höhere Kosten |
Qualität der Produkte | Hochwertige, fehlerfreie Produkte | Höhere Fehlerquoten, geringere Gesamtqualität |
Herausforderungen bei der Kontrolle der Partikelgrößenverteilung
Die Optimierung der PSD bietet zwar zahlreiche Vorteile, birgt aber auch einige Herausforderungen, die bewältigt werden müssen, um die gewünschten Ergebnisse zu erzielen.
Herausforderungen bei der PSD-Kontrolle
Herausforderung | Beschreibung | Auswirkungen | Strategien zur Schadensbegrenzung |
---|---|---|---|
Inkonsistente Produktion | Variabilität der Produktionsprozesse | Führt zu inkonsistenten PSD | Durchführung strenger Qualitätskontrollmaßnahmen |
Messgenauigkeit | Schwierigkeiten bei der genauen Messung der PSD | führt zu unzuverlässigen Daten | Einsatz fortschrittlicher Messtechniken |
Kosten der Optimierung | Hohe Kosten für das Erreichen einer einheitlichen PSD | Erhöht die Gesamtproduktionskosten | Gleichgewicht zwischen Kosten und Leistungsanforderungen |
Materielle Empfindlichkeit | Bestimmte Materialien sind empfindlich gegenüber PSD-Änderungen | Beeinflusst Materialeigenschaften und Leistung | Gründliche Tests und Validierungen durchführen |
Umweltfaktoren | Luftfeuchtigkeit, Temperatur und Verschmutzung | Kann PSD während der Produktion und Speicherung verändern | Umweltbedingungen genau kontrollieren |
Überwindung von Herausforderungen bei der PSD-Optimierung
Die erfolgreiche Optimierung von PSD erfordert eine Kombination aus fortschrittlichen Techniken, strenger Qualitätskontrolle und einem umfassenden Verständnis des Materialverhaltens. Einige Strategien umfassen:
- Erweiterte Messwerkzeuge: Einsatz von Instrumenten wie Laserbeugung oder dynamische Lichtstreuung zur Gewinnung genauer PSD-Daten.
- Strenge Prozesskontrolle: Strenge Kontrollen während der Produktion, um die Variabilität der PSD zu minimieren.
- Kontinuierliche Überwachung: Regelmäßige Überwachung der Umweltfaktoren, um sicherzustellen, dass sie sich nicht negativ auf PSD auswirken.
Die Auswahl des richtigen Metallpulverlieferanten
Die Wahl des richtigen Lieferanten ist entscheidend, um die Qualität und Konsistenz von Metallpulvern zu gewährleisten, insbesondere wenn es um spezifische PSD-Anforderungen geht.
Wichtige Überlegungen bei der Auswahl eines Lieferanten
Betrachtung | Warum es wichtig ist | Was zu beachten ist |
---|---|---|
Qualitätskontrolle | Sicherstellung einer einheitlichen PSD- und Materialqualität | ISO-Zertifizierungen, strenge Prüfprotokolle |
Technische Unterstützung | Bietet Unterstützung bei der Optimierung von PSD | Zugang zu Experten, individuelle PSD-Analyse |
Zuverlässigkeit der Lieferkette | Garantiert rechtzeitige Lieferung und Verfügbarkeit | Starkes Logistiknetz, Bestandsverwaltung |
Kosten und Preisgestaltung | Beeinflusst das Gesamtbudget des Projekts | Wettbewerbsfähige Preise, transparente Kostenstruktur |
Reputation und Bewertungen | Indikator für die Zuverlässigkeit des Lieferanten und die Kundenzufriedenheit | Positive Bewertungen, langjähriger guter Ruf |
Vergleich von Lieferanten für Metallpulver
Anbieter | Standort | Wichtige Produkte | Preisgestaltung (pro kg) | Qualitätszertifizierungen | Kundenrezensionen |
---|---|---|---|---|---|
ABC Metalle | USA | Aluminium, rostfreier Stahl | $50-$200 | ISO 9001, ASTM zertifiziert | 4.5/5 |
Global Powder Co. | Deutschland | Titan, Kobalt-Chrom | $80-$250 | ISO 13485, REACH-konform | 4.7/5 |
PowderTech | China | Kupfer, Nickel, Bronze | $30-$150 | ISO 9001, RoHS-konform | 4.3/5 |
Metallpulver Inc. | UK | Inconel, Magnesium | $100-$300 | ISO 9001, AS9100 zertifiziert | 4.6/5 |
Erstklassige Metalle | Japan | Rostfreier Stahl, Inconel | $90-$280 | ISO 14001, JIS-Normen | 4.8/5 |
Gleichgewicht zwischen Kosten und Qualität
Bei der Auswahl eines Lieferanten ist es wichtig, ein Gleichgewicht zwischen Kosten und Qualität zu finden. Niedrigere Preise mögen zwar verlockend erscheinen, können aber manchmal auf Kosten einer gleichbleibenden PSD- und Materialqualität gehen. Bedenken Sie Folgendes:
- Langfristiger Wert: Qualitativ hochwertigere Pulver können Fehler reduzieren und die Ausbeute erhöhen, was langfristig einen besseren Wert darstellt.
- Beziehung zu den Lieferanten: Der Aufbau einer starken Beziehung zu einem zuverlässigen Lieferanten kann zu besseren Konditionen, maßgeschneiderten PSD-Optionen und bevorzugtem Service führen.
Vergleichende Analyse: Optimierte PSD vs. Standard-PSD in Metallpulvern
Wenn Sie den Unterschied zwischen optimierten und Standard-PSDs verstehen, können Sie fundierte Entscheidungen über Materialauswahl und Verarbeitungstechniken treffen.
Optimiertes PSD
- Vorteile:
- Verbesserte Materialeigenschaften (z. B. Festigkeit, Reaktivität).
- Verbesserte Prozesseffizienz und Ausbeute.
- Bessere Kontrolle der Qualität des Endprodukts.
- Benachteiligungen:
- Höhere Produktionskosten.
- Erfordert fortgeschrittene Mess- und Kontrolltechniken.
Standard-PSD
- Vorteile:
- Niedrigere Produktionskosten.
- Einfachere Mess- und Kontrollverfahren.
- Benachteiligungen:
- Möglicherweise geringere Materialleistung.
- Höheres Risiko von Mängeln und Unstimmigkeiten.
Optimiertes vs. Standard-PSD in wichtigen Anwendungen
Anmeldung | Optimiertes PSD | Standard-PSD | Auswirkungen auf das Endprodukt |
---|---|---|---|
3D-Druck | Sanfte Schichtung, präzise Details | Möglichkeit der Verstopfung, ungleichmäßige Schichten | Optimiertes PSD führt zu höherer Auflösung |
Pulvermetallurgie | Gleichmäßige Sinterung, hohe Dichte | Unterschiedliche Dichte, ungleichmäßige Sinterung | Standard-PSD kann zu schwächeren Teilen führen |
Thermisches Spritzen | Gleichmäßige Schichtdicke | Ungleichmäßige Beschichtung, mögliche Mängel | Optimiertes PSD gewährleistet besseren Oberflächenschutz |
Elektronik | Verbesserte Leitfähigkeit, Zuverlässigkeit | Inkonsistente Leitfähigkeit, mögliche Ausfälle | Optimiertes PSD verbessert die Schaltungsleistung |
Komponenten für die Luft- und Raumfahrt | Hohes Verhältnis von Festigkeit zu Gewicht | Geringere Festigkeit, Potenzial für Defekte | Optimierte PSD entscheidend für Sicherheit und Leistung |
Fallstudien: Real-World-Anwendungen der PSD-Optimierung
Fallstudie 1: Luft- und Raumfahrtindustrie
Herausforderung: Ein Hersteller der Luft- und Raumfahrtindustrie hatte Probleme mit der ungleichmäßigen Festigkeit von Turbinenschaufeln aus Inconel-Pulver. Das in der Produktion verwendete Standard-PSD führte zu einem variablen Sinterverhalten, was zu Schwachstellen in den Schaufeln führte.
Lösung: Der Hersteller wechselte zu einem optimierten PSD mit einer engeren Verteilung um die mittlere Partikelgröße. Diese Änderung führte zu einer gleichmäßigeren Sinterung und damit zu Turbinenschaufeln mit gleichmäßiger
Stärke und verbesserte Leistung.
Das Ergebnis: Durch die Umstellung auf optimierte PSD konnte die Fehlerquote um 30% gesenkt und die Lebensdauer der Turbinenschaufeln um 20% erhöht werden, was zu erheblichen Kosteneinsparungen und Leistungsvorteilen führte.
Fallstudie 2: Medizinische Implantate
Herausforderung: Ein Medizintechnikunternehmen, das Titanimplantate herstellt, kämpfte mit Unregelmäßigkeiten in der Oberfläche, die die Biokompatibilität der Implantate beeinträchtigten. Das Problem wurde auf eine breite PSD im Titanpulver zurückgeführt, was zu rauen Oberflächen führte.
Lösung: Das Unternehmen führte eine kontrolliertere PSD mit Schwerpunkt auf feinen Partikeln ein, um glattere Oberflächen zu erzielen.
Das Ergebnis: Die optimierte PSD führte zu glatteren Implantatoberflächen, die ihre Biokompatibilität verbesserten und die Abstoßungsrate um 15% reduzierten. Das Unternehmen stellte außerdem verbesserte Patientenergebnisse und eine erhöhte Nachfrage nach seinen Implantaten fest.
Fallstudie 3: Additive Fertigung
Herausforderung: Ein Hersteller, der 3D-Druck für Automobilteile einsetzt, stellte fest, dass die Teile aufgrund eines ungleichmäßigen Pulverflusses, der auf eine breite PSD im Aluminiumpulver zurückzuführen ist, fehleranfällig waren.
Lösung: Durch die Verengung des PSD verbesserte sich die Fließfähigkeit des Pulvers, was zu einer präziseren Schichtung während des 3D-Druckprozesses führte.
Das Ergebnis: Das verbesserte PSD führte zu weniger Fehlern und qualitativ hochwertigeren Teilen, so dass der Hersteller die Nachbearbeitungszeit um 25% reduzieren und die Produktionseffizienz steigern konnte.
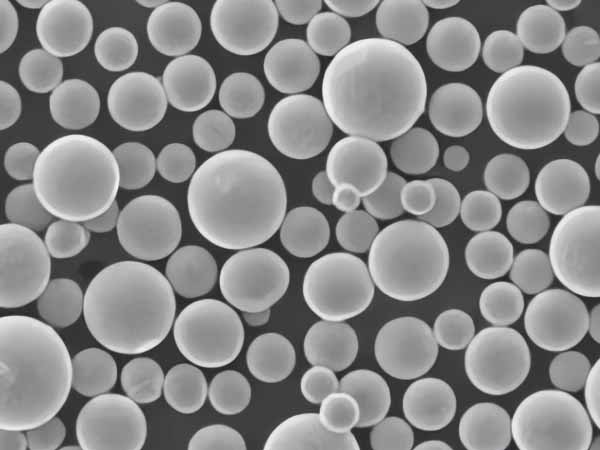
FAQ
1. Was ist die Partikelgrößenverteilung (PSD)?
Frage | Antwort |
---|---|
Was ist PSD? | PSD bezieht sich auf die Variation der Partikelgrößen innerhalb einer bestimmten Probe. |
Warum ist PSD wichtig? | PSD beeinflusst Materialeigenschaften wie Fließfähigkeit, Reaktivität und Dichte. |
Wie wird die PSD gemessen? | Zu den Techniken gehören Laserbeugung, Siebung, DLS und Mikroskopie. |
2. Wie wirkt sich PSD auf Metallpulver aus?
Frage | Antwort |
---|---|
Wie wirkt sich die PSD auf die Fließfähigkeit von Metallpulvern aus? | Ein gut kontrolliertes PSD sorgt für einen reibungslosen Ablauf und reduziert Probleme bei der Verarbeitung. |
Welche Rolle spielt das PSD beim Sintern? | PSD beeinflusst die Temperatur und die Gleichmäßigkeit des Sinterprozesses. |
Kann PSD die Festigkeit von Metallteilen beeinträchtigen? | Ja, eine konsistente PSD führt zu stärkeren, zuverlässigeren Komponenten. |
3. Wie wähle ich das richtige PSD für meine Anwendung?
Frage | Antwort |
---|---|
Welche Faktoren sollte ich bei der Auswahl von PSD berücksichtigen? | Berücksichtigen Sie Ihre Anwendungsanforderungen, Materialeigenschaften und Verarbeitungsmethoden. |
Kann ich das PSD für bestimmte Anwendungen anpassen? | Ja, viele Anbieter bieten maßgeschneiderte PSD-Optionen an, die auf Ihre Bedürfnisse zugeschnitten sind. |
Was sind die Vorteile einer optimierten PSD? | Zu den Vorteilen gehören verbesserte Materialleistung, Prozesseffizienz und Produktqualität. |
4. Was sind die Herausforderungen bei der PSD-Optimierung?
Frage | Antwort |
---|---|
Welche Herausforderungen bestehen bei der Kontrolle von PSD? | Zu den Herausforderungen gehören Messgenauigkeit, Produktionsschwankungen und Kosten. |
Wie kann ich diese Herausforderungen meistern? | Verwenden Sie fortschrittliche Messinstrumente, führen Sie strenge Qualitätskontrollen durch und überwachen Sie Umweltfaktoren. |
5. Wer sind die führenden Anbieter von Metallpulvern mit kontrollierter PSD?
Frage | Antwort |
---|---|
Wer sind einige zuverlässige Lieferanten von Metallpulvern? | Lieferanten wie ABC Metals, Global Powder Co. und PowderTech sind seriös. |
Worauf sollte ich bei einem Lieferanten achten? | Achten Sie auf Zertifizierungen für die Qualitätskontrolle, technische Unterstützung und wettbewerbsfähige Preise. |
Schlussfolgerung
Verstehen und Optimieren Partikelgrößenverteilung ist von entscheidender Bedeutung in Branchen, die von der Luft- und Raumfahrt bis zu medizinischen Geräten reichen. Das richtige PSD kann die Materialeigenschaften erheblich verbessern, die Prozesseffizienz erhöhen und die Produktqualität steigern. Auch wenn es bei der PSD-Optimierung Herausforderungen gibt, können diese mit den richtigen Strategien, Werkzeugen und Partnerschaften mit Lieferanten überwunden werden. Wenn Sie sich auf die spezifischen Anforderungen Ihrer Anwendung konzentrieren und das richtige PSD auswählen, können Sie bessere Ergebnisse, niedrigere Kosten und einen größeren Erfolg bei Ihren Projekten erzielen.