Overview of FeCoNiCr Powder
FeCoNiCr, also known as Stellite 21 alloy, is a multipurpose cobalt-based superalloy powder used for metal 3D printing applications across aerospace, oil and gas, automotive, and medical industries.
Key properties of FeCoNiCr powder include:
Attribute | Description |
---|---|
Composition | Iron, cobalt, nickel, chromium alloy |
Density | 8.2 g/cc |
Melting point | 1350°C |
Key characteristics | High strength, corrosion resistance, wear resistance |
Common trade names | Stellite 21, Haynes Stellite 21, Deloro 21, Tribaloy T-401 |
FeCoNiCr is widely used for printing parts that require high hardness, abrasion resistance, and biocompatibility like orthopedic implants, tooling, and oil & gas components. It offers a versatile combination of mechanical properties using conventional metal 3D printing processes.
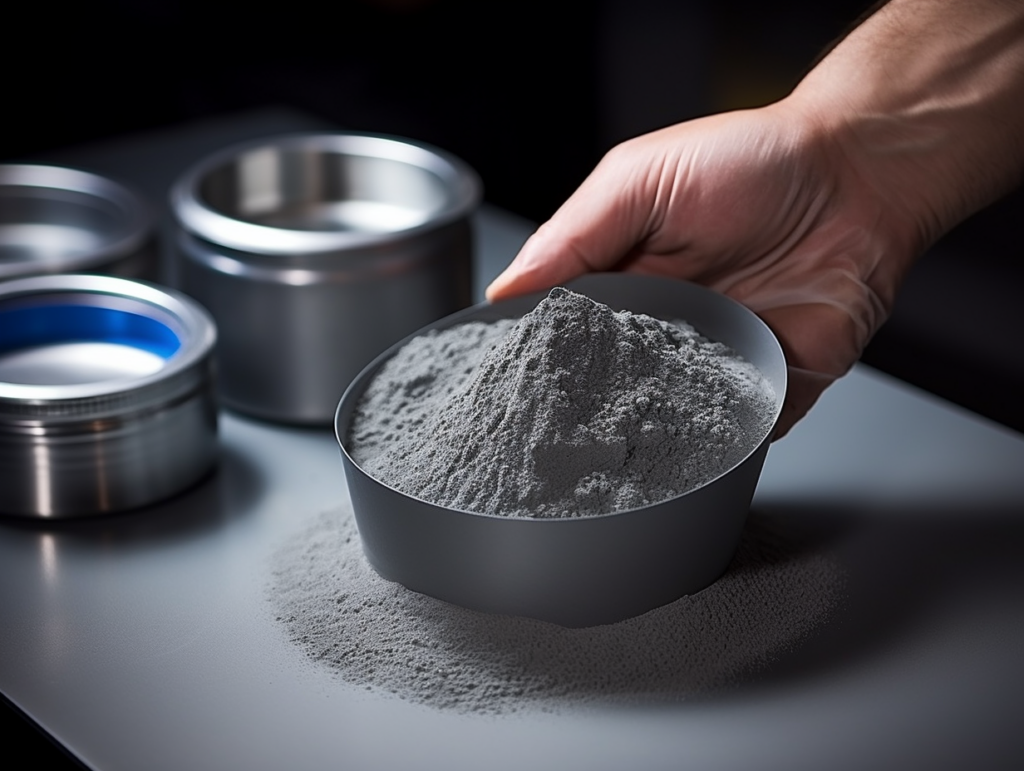
Applications of FeCoNiCr Powder
Thanks to its multipurpose material properties, FeCoNiCr has a diverse range of industrial applications:
Industry | Applications |
---|---|
Aerospace | Turbine blades, landing gear components, engine parts |
Oil and gas | Valves, wellhead components, downhole tools |
Automotive | Valve components, pistons, turbocharger wheels |
Industrial | Extrusion dies, injection molds, cutting tools |
Medical | Orthopedic implants, prosthetics, dental devices |
It is valued for critical applications exposed to abrasion, high temperatures, and corrosive environments. The ability to 3D print complex geometries out of FeCoNiCr grants additional design freedom.
Some specific uses cases include:
- Turbine blades – High strength and heat resistance at elevated temperatures
- Orthopedic implants – Biocompatibility and high wear performance
- Extrusion dies – Withstands wear from continuous operation
- Valves and seals – Corrosion resistance for oil and gas environments
- Cutting tools – Hardness and wear properties for machining applications
FeCoNiCr enables lighter, more consolidated parts with improved mechanical properties over traditional manufacturing methods.
Characteristics of FeCoNiCr Powder for 3D Printing
FeCoNiCr powder used for additive manufacturing has the following composition and characteristics:
Attribute | Details |
---|---|
Chemical composition | 27-38% Cr, 35-55% Co, 15-25% Ni, 3-5% Fe |
Particle shape | Spherical morphology with some satellites |
Particle size | 15-45 microns diameter |
Flowability | Excellent flow properties, not agglomerated |
Apparent density | Typically over 4 g/cc |
Melting point | 1260-1350°C |
Printing process | Binder jetting, powder bed fusion |
High powder quality and repeatable composition enables stable, high-density printing using FeCoNiCr. The spherical morphology provides smooth powder flow and uniform layer deposition.
Specialized gas atomization techniques produce FeCoNiCr powder meeting the strict size distributions required for metal AM processes. The ingredients are melted and spun into fine droplets that solidify into powder.
Metal 3D Printer Specifications for FeCoNiCr
Printing FeCoNiCr parts requires industrial metal 3D printers with the following typical capabilities:
Parameter | Specification |
---|---|
Build volume | 100-500 x 100-500 x 100-500 mm |
Laser power | 300-500 W |
Precision optics | 50-100 μm spot size |
Layer thickness | 20-100 μm |
Scanning speed | Up to 10 m/s |
Inert gas | Argon or nitrogen |
Powder handling | Closed-loop, automated systems |
Controls | Robust software for production |
Key requirements are high laser power for melting the FeCoNiCr alloy, fine layer thickness for resolution, and integrated powder handling systems.
Specialized hot-work tool steels or alumina ceramic build plates withstand the elevated temperatures. High performance inert gas filtration systems protect the optics from reactive metal powders.
Design Principles for 3D Printing with FeCoNiCr
To optimize parts printed from FeCoNiCr powder, the following design principles should be followed:
Design Area | Guidelines |
---|---|
Wall thickness | Minimum 1 mm walls, increase for load-bearing features |
Overhangs | Minimum 45° angles, use supports where needed |
Tolerances | Account for ±0.2% dimensional accuracy and post-machining |
Surface finish | As-printed is rough, machine, polish, or shot peen surfaces |
Residual stress | Design to minimize warping, use stress relief heat treatments |
Escape holes | Include drainage paths to remove loose powder |
Simulating builds using the actual parameters and powder characteristics will validate the design. Topology optimization software can light-weight FeCoNiCr parts for better performance.
Typical Mechanical Properties of FeCoNiCr Alloy
Printed FeCoNiCr components exhibit the following approximate mechanical properties:
Property | Value |
---|---|
Density | 8.2 g/cc |
Hardness | 50 HRC |
Tensile strength | 1050 MPa |
Yield strength | 880 MPa |
Elongation at break | 8% |
Young’s modulus | 210 GPa |
The properties make it well-suited for load-bearing components requiring high hardness and strength. Heat treatment can further enhance the alloy’s mechanical performance.
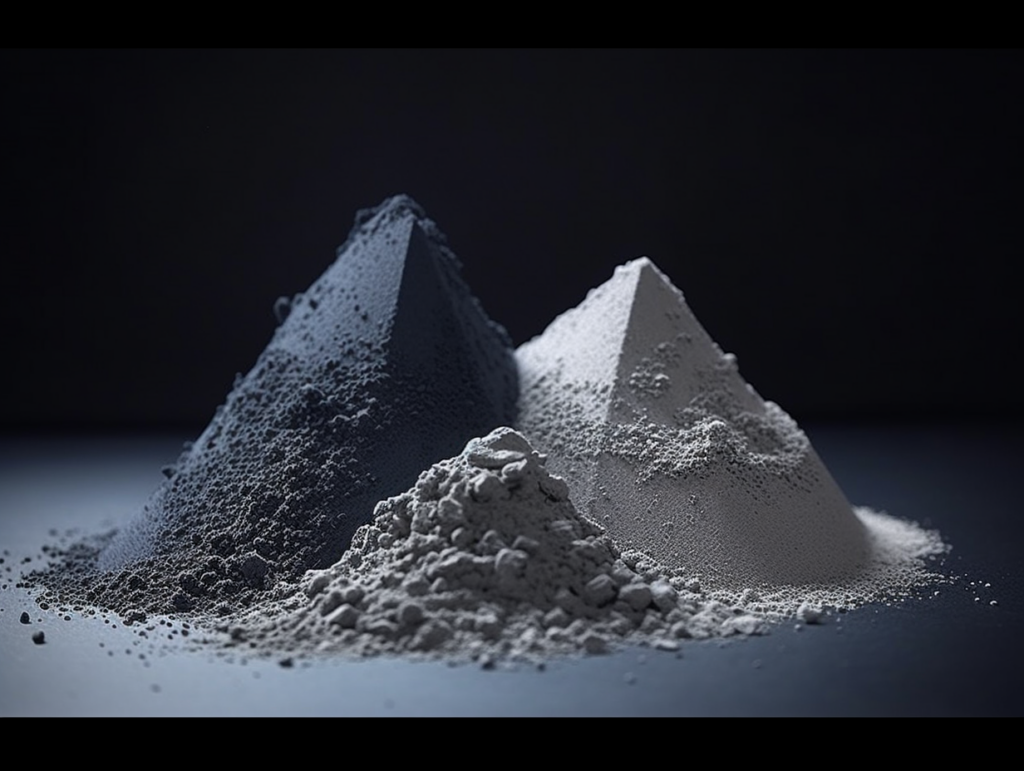
Suppliers of FeCoNiCr Powder for 3D Printing
Leading global suppliers of FeCoNiCr gas-atomized powder include:
Company | Product Grades | Typical Pricing |
---|---|---|
Carpenter Technology | Stellite 21 | $100-200/kg |
Sandvik | Osprey 21-IG | $120-250/kg |
AP&C | FeCoNiCr, CoNiCrW | $150-300/kg |
Praxair | Trillium 21 | $180-350/kg |
TLS Technik | Termo 21 | $130-220/kg |
Prices vary based on order volumes, composition, and particle size distribution. Custom alloys and particle characteristics may have higher pricing.
High quality FeCoNiCr powder tailored for AM processes is critical for achieving desired material properties in printed parts.
How to Choose a FeCoNiCr Powder Supplier
When selecting a FeCoNiCr powder supplier, the following factors should be considered:
Factor | Criteria |
---|---|
Composition control | Tight tolerances on elements like Cr, Co, Ni, C |
Manufacturing process | Gas atomization preferred over water atomization |
Particle size distribution | D50 from 20-45 μm, tight particle ranges |
Powder morphology | Spherical shape and smooth surface |
Technical support | R&D assistance, application data, testing |
Quality certifications | ISO 9001, AS9100, ISO 13485 |
Lead time and availability | Short lead times, no long-term contracts |
Reputation and references | Trusted brand, case studies, customer reviews |
Small trial samples can validate printability before purchasing large volumes of powder.
Printing Parameters for FeCoNiCr Alloy
To achieve high density parts when printing FeCoNiCr, typical laser powder bed fusion parameters include:
Parameter | Range |
---|---|
Layer thickness | 20-50 μm |
Laser power | 150-400 W |
Beam diameter | 50-120 μm |
Scan speed | 500-1000 mm/s |
Hatch spacing | 50-150 μm |
Shielding gas | Argon, nitrogen |
Build plate preheating | 200-400°C |
Fine hatch spacing is used to limit porosity. Preheating the build plate minimizes residual stresses and curling. trial builds are required to dial in optimal parameters.
For directed energy deposition, higher laser powers from 1-4 kW are used with larger melt pools and thicker layers around 0.5 mm. Wire feed rates range from 2-10 g/min depending on part features.
Post-Processing Methods for FeCoNiCr Parts
After 3D printing, common post-processing steps for FeCoNiCr components include:
Method | Purpose |
---|---|
Support removal | Removing support structures from the printed part |
Stress relieving | Reducing residual stresses through heat treatment |
Hot isostatic pressing | Removing internal voids and increasing density |
Surface finishing | Smoothing rough as-printed surfaces through grinding or polishing |
Joining | Welding multiple components together after printing |
Coatings | Electroplating or DLC coatings for wear resistance |
The right combination of post-processing depends on the application requirements. HIP and finishing are commonly used on functional FeCoNiCr parts see service.
Metallurgical Properties of Printed FeCoNiCr
Printing FeCoNiCr powder via laser powder bed fusion generates the following as-printed metallurgical characteristics:
Attribute | Typical Result |
---|---|
Microstructure | Dendritic, rapid solidification structure |
Porosity | Less than 1% with optimized parameters |
Alloy homogeneity | Consistent distribution of elements |
Hardness | 550-650 HV, 50-55 HRC |
Tensile strength | 1050-1200 MPa in XY plane |
Surface roughness (Ra) | Around 15 μm as-printed |
The rapid solidification leads to a fine grain structure and extended solid solubility of the alloying elements compared to conventional processing.
Common Defects in FeCoNiCr Printed Parts
Some potential defects when printing FeCoNiCr parts include:
Defect | Causes | Prevention |
---|---|---|
Warping | Residual stresses from thermal gradients | Optimize scan strategy, use preheating |
Cracking | Brittle alloy, high stresses | Modify geometry, heat treat for ductility |
Anisotropy | Directional microstructure | Rotate build orientation, stress relieve |
Surface roughness | Partially melted powder, balling | Adjust scan speed, beam focus, powder size |
Inclusions | Contaminants in powder | Use high purity powder, filter inert gas |
Dimensional accuracy | Shrinkage, thermal distortions | Calibrate machine, optimize support structures |
Parameter optimization trials and rigorous quality control of incoming powder reduce defects.
Applications of Heat Treated FeCoNiCr Parts
Solution heat treating and age hardening allows tailoring the properties of printed FeCoNiCr components for:
Application | Typical Heat Treatment | Benefits |
---|---|---|
Aerospace turbines | 1240°C solution, 850°C aging | Increased tensile strength, creep resistance |
Extrusion tooling | 1150°C solution, air cooled | Improved hardness, wear resistance |
Automotive valves | 1200°C solution, air quenching | Higher strength for fatigue resistance |
Cutting tools | 1080°C aging for 16 hours | Maximize hardness to resist abrasion |
Heat treatment tailors the microstructure and precipitate formation to achieve the desired properties. Printed FeCoNiCr offers flexibility in heat treatment response.
Qualifying Printed FeCoNiCr Parts
Printed FeCoNiCr components require the following testing and inspection to qualify parts for end-use:
Testing Method | Typical Acceptance Criteria |
---|---|
Visual inspection | No cracks, surface anomalies, powder inclusions |
Leak testing | Verify sealed components have no internal leaks |
Dimensional analysis | Critical dimensions within engineering tolerance |
Density measurement | Greater than 99% relative density |
Tensile testing | Mechanical properties meet or exceed minimum values |
Microstructure | Verify uniform, defect-free grain structure |
Non-destructive testing like CT scanning can find internal voids without cutting test coupons. Thorough testing ensures reliable performance in service.
Key Applications of FeCoNiCr Alloy
The unique properties of FeCoNiCr make it well-suited for:
Application | Benefits |
---|---|
Aerospace turbine blades | Withstands 700°C temperatures and wear |
Automotive valve seats and guides | Resists wear and high temperature exhaust gases |
Medical implants | Biocompatible with excellent corrosion resistance |
Extrusion tooling | Hardness and abrasion resistance at 900°C |
Downhole drilling components | High strength in corrosive, high pressure environments |
3D printing enables lighter, consolidated components with enhanced performance in these demanding applications.
Economic Benefits of FeCoNiCr vs. Traditional Materials
For many applications, printed FeCoNiCr provides cost and performance advantages over conventional materials like tool steel, stainless steel, and Inconel superalloys:
FeCoNiCr | Comparison Material | |
---|---|---|
Density | 8.2 g/cc | 7.5-8.4 g/cc |
Hardness | 50-55 HRC | 30-55 HRC |
Strength | 1050 MPa | 550-1200 MPa |
Wear resistance | Excellent | Moderate to excellent |
Corrosion resistance | Excellent | Poor to excellent |
Cost per kg | $100-300 | $20-500 |
FeCoNiCr provides an optimal balance of properties and cost, making it competitive for the most demanding applications.
Sustainability Benefits of Metal 3D Printing with FeCoNiCr
Additive manufacturing with FeCoNiCr powder offers sustainability advantages versus conventional manufacturing:
- Reduced waste – Print only the required material instead of machining away material
- Lightweighting – Optimize designs for weight reduction and material savings
- Part consolidation – Combine assemblies into single printed parts
- On-demand production – Print parts as needed instead of mass production
- High scrap recyclability – Unused powder can be reused for future prints
- Localized production – Reduce shipping and logistics carbon footprint
The technology enables more sustainable engineering approaches across the product lifecycle. FeCoNiCr is an excellent green material choice.
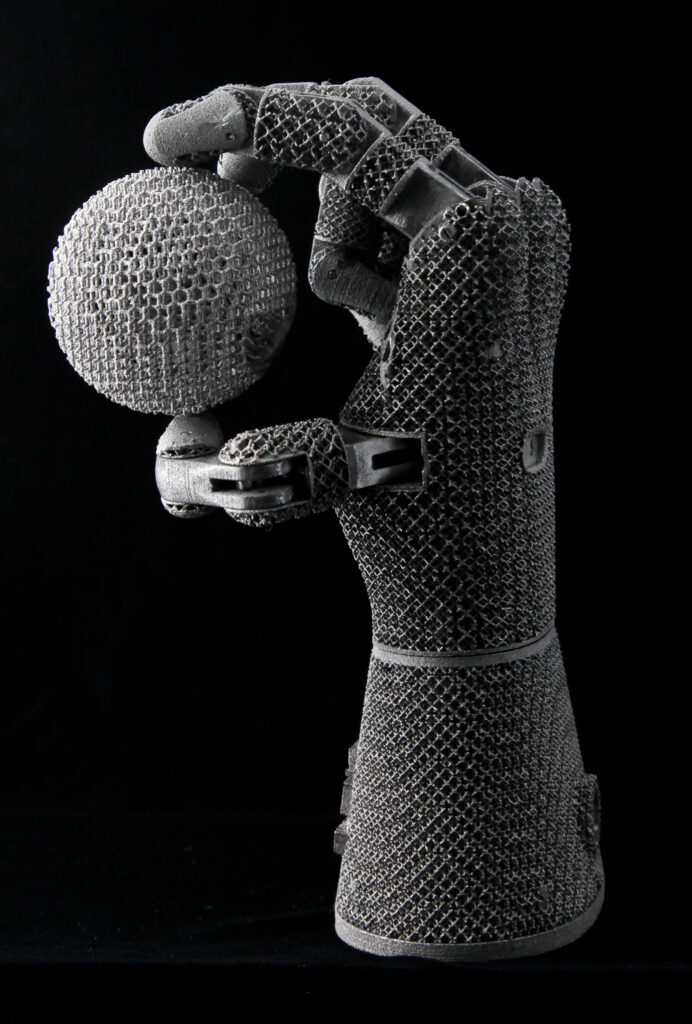
FAQ
Question | Answer |
---|---|
What particle size is best for printing FeCoNiCr? | 20-45 microns is optimal. Too fine causes poor flow, too coarse reduces resolution. |
What are some alternatives to FeCoNiCr alloy? | Inconel 718, stainless steel 316L, and 17-4PH offer similar properties. |
What finish can be obtained on printed FeCoNiCr parts? | As-printed surface is rough at Ra 15-20 μm. Polishing can achieve under 1 μm finish. |
Is FeCoNiCr susceptible to cracking during printing? | Yes, careful preheating and strategic scanning helps reduce cracking tendencies. |
What post-processing is required? | Support removal, stress relieving, HIP, and surface finishing are typically used. |
Summary
- FeCoNiCr alloy powder enables versatile properties for demanding applications via metal AM processes.
- Excellent wear resistance, strength, biocompatibility, and corrosion resistance.
- Widely used in aerospace, oil and gas, automotive, medical industries.
- Gas atomization provides optimal powder morphology and composition.
- Industrial printers with parameters tuned for FeCoNiCr are required.
- Strict quality control and testing required to qualify printed components.
- Offers performance and cost advantages over conventional materials.
- An economical choice for high value add metal printing applications.
The unique capabilities of FeCoNiCr powder make it an important material for advancing industrial metal 3D printing.