IN939 Superalloy Powder enables high strength additive manufacturing across demanding aerospace, oil, and space applications requiring extreme temperature and wear resistance surpassing conventional metals. This guide provides composition details, specifications, properties data, pricing estimates and FAQs to inform powder procurement decisions.
Introduction to IN939 Superalloy Metal Powder
Key capabilities of IN939 powder include:
- Withstand 1100°C service temperatures
- Excellent fatigue, creep and rupture strength
- Oxidation and corrosion resistance
Common variants used in AM include:
- IN939V – Vacuum induction melted powder
- IN939HIP – Hot isostatic pressed pre-alloyed powder
This guide covers factors evaluating IN939 for part production:
- Composition and Powder Characteristics
- Mechanical Properties and Test Methods
- Particle Size Distribution Specs
- Test Certificate Data Sheet Requirements
- Pricing Models Based on Volume
- Thermal and Environmental Resistance
- Pros vs Cons: Powder vs Solid Bar
- FAQs on Parameter Optimization
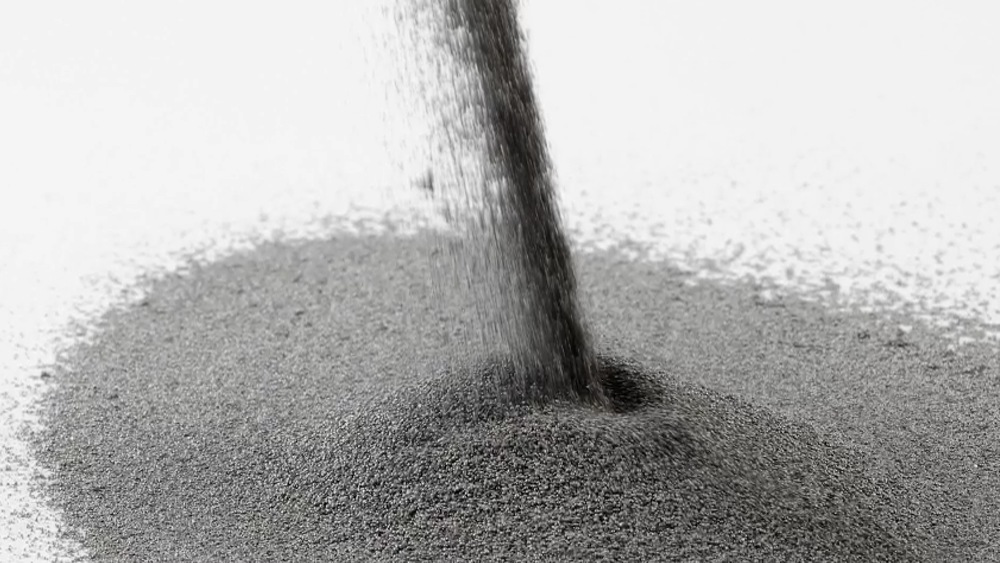
IN939 Superalloy Powder Compositions
Table 1 shows nominal IN939 compositions by weight percent. Actual limits vary slightly between powder suppliers.
Element | Composition (%wt) |
---|---|
Nickel (Ni) | Balance |
Cobalt (Co) | 15-25 |
Tungsten (W) | 4-6 |
Tantalum (Ta) | 11-15 |
Aluminum (Al) | 3.2-4.4 |
Titanium (Ti) | 0.6-2 |
Boron (B) | 0.003-0.02 |
Zirconium (Zr) | 0.02-0.15 |
Carbon (C) | 0.02-0.10 |
Yttrium (Y) | 0.005-0.040 |
Small additions like boron improve grain boundary strength. Zirconium getters impurities. Yttrium enhances oxidation resistance.
Mechanical Properties and Test Methods
Table 2 shows typical minimum mechanical properties met by IN939 powder alloys. Actual values vary based on build geometry, post-processing, and heat treatment.
Property | Minimum Spec | Test Method |
---|---|---|
Tensile Strength | 1310 MPa | ASTM E8 |
Yield Strength (0.2% offset) | 1210 MPa | ASTM E8 |
Elongation % | 8% | ASTM E8 |
Hardness | 44 HRC | ASTM E18 |
Suppliers can demonstrate improvements beyond minimums through deliberate parameter adjustments like Hot Isostatic Pressing (HIP) and modified age hardening heat treatments.
Carefully review test certificate data reports to align delivered powder with application needs before high volume production commitments.
IN939 Superalloy Powder Particle Size Specs
Table 3 shows common IN939 powder size distributions classified into standard mesh ranges and microns. Size range affects final part quality and accuracy.
Mesh Size | Micron Range | ASTM Size Name |
---|---|---|
-140 +325 | 44 – 105 | Extra Fine |
-100 +325 | 149 – 45 | Submicron |
-325 | 0 – 45 | Superfine |
Other key particle characteristics:
- Near spherical morphology
- Smooth surface
- High powder flow rates
For printing parameters, a good starting point is 30-45 micron mean powder size. Adjust based on specific machine capabilities and minimum feature resolution needed.
Powder Test Certificate Requirements
Each batch of IN939 alloy powder requires full certification package indicating:
- Chemical composition by weight percent
- Particle size distribution including mean and mesh passing
- True density and hall flow seconds as powder indicators
- SEM imagery verifying powder characteristics
- Mechanical properties test data aligning to specifications
- Production date, heat number, batch number
- Conformance to indication aerospace material specification
Ensure compliance with indication standards like AMS7000 and rigorously review all test reports prior to accepting powder lots.
IN939 Metal Powder Pricing Estimates
Table 4 provides rough IN939 powder price estimates at different volumes under typical market conditions:
Order Quantity | Price Estimate |
---|---|
10 kg | $450+/kg |
100 kg | $250+/kg |
500 kg | $175+/kg |
1000+ kg | Subkey pricing |
- Special alloys command premium $350+/kg baseline pricing
- Large volume commitments in 1000+ kg range enable >50% cost savings from list prices
- Actual market prices fluctuate with raw material indexes
- Narrow customer margins on powder; quality consistency vital
IN939 Powder Thermal and Environmental Resistance
IN939 powder printed alloys offer exceptional high temperature strength and corrosion resistance properties.
Table 5 shows typical use envelopes:
Environment | Service Temperature |
---|---|
Oxidizing | 1095°C (2000°F) |
Hot Corrosion | 980°C (1800°F) |
Aqueous Corrosion | Excellent |
The nickel and cobalt matrix resists oxidizing up to 2000°F in gas turbine environments. Elements like aluminum form protective oxide barriers preventing deterioration. Carbides reinforce grain boundaries. Carefully engineered compositions confer multi-property optimization – strength, ductility, fatigue, creep, corrosion and oxidation resistance up to 0.9 melting point temperatures.
Pros vs Cons: IN939 Metal Powder vs Solid Bar
Table 6
Advantages | Disadvantages | |
---|---|---|
IN939 Metal Powder | Complex shapes | Higher cost |
Advanced properties | Post-processing | |
Innovative geometries, weight savings | Handling challenges | |
Custom alloys | Parameter optimization | |
IN939 Solid Bar | Lower piece cost | Shape limits |
Availability | Much heavier | |
Machinability | Extensive waste |
In general, IN939 powder justifies premiums for low volume complex components where advanced properties are vital. Bar forms offer affordability for simpler shapes in high production volumes.
Combining both material supply forms strategically minimizes overall program costs based on application.
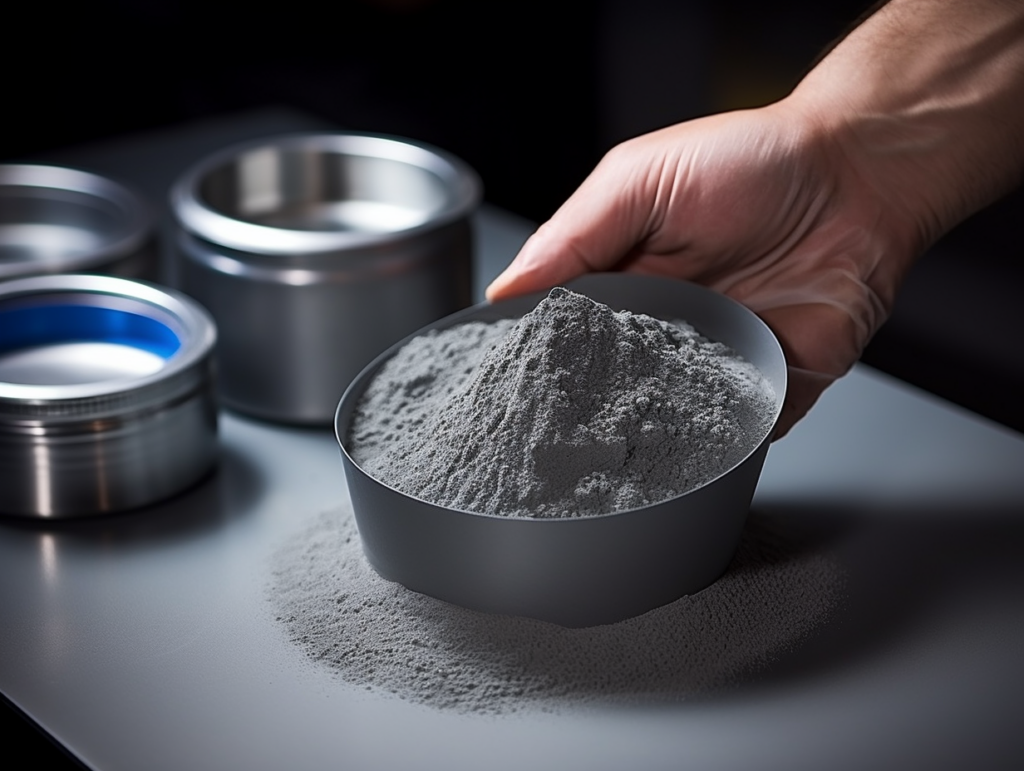
FAQs
Frequently asked questions on IN939 powder:
Table 7 – General questions:
FAQ | Answer |
---|---|
Should I request test reports? | Yes, review all certs to ensure powder quality |
What size powder particles should I use? | 30-45u good balance. Depends on printer used. |
Which process offers better consistency? | Vacuum Induction Melting (VIM) |
How much powder should I buy upfront? | Start small, buy more once print process is validated |
Table 8 – Application-specific advice:
FAQ | Answer |
---|---|
Is IN939V or IN939HIP better for cryogenic parts? | IN939HIP due to enhanced density and stability at extremes |
How should I adjust parameters for faster build speeds? | Carefully balance energy input and scan strategy to avoid defects |
What heat treatment maximizes yield strength >1300MPa? | Modified age hardening tailored for a application loading |
What post-processing is recommended for parts seeing cyclic loading? | Hot Isostatic Pressing (HIP) to minimize porosity-driven fatigue issues |