IN939 is a popular nickel-based superalloy powder used in various high-temperature applications such as gas turbines and aircraft engines. This guide provides a comprehensive overview of IN939 powder, including its properties, applications, suppliers, prices, installation, operation and maintenance.
Overview of IN939 Powder
IN939 is a precipitation-hardened nickel-based superalloy that offers excellent mechanical properties and resistance to thermal fatigue and creep at high temperatures. Some key features of IN939 powder include:
- High strength and hardness – Offers superior tensile and yield strength compared to other alloys. Hardness ranges from 35-45 HRC.
- Outstanding creep resistance – Excellent creep rupture strength up to 1300°F (700°C).
- Thermal fatigue resistance – Resists cracking from repeated heating and cooling cycles.
- Oxidation resistance – Forms protective oxide layer to prevent corrosion and oxidation.
- Weldability – Can be welded using conventional welding methods. Requires post-weld heat treatment.
- Versatile applications – Used for combustion liners, transition ducts, turbine blades, vanes, rocket nozzles, etc.
IN939 is available in powder form for additive manufacturing, allowing complex geometries to be fabricated directly from the powder. Key properties and applications of IN939 powder are highlighted below:
Properties of IN939 Powder
Properties | Details |
---|---|
Composition | Nickel base with titanium, aluminium, chromium additions |
Density | 8.2 g/cm3 |
Melting Point | ~1350°C |
Thermal Conductivity | 11 W/m-K at 20°C |
Coefficient of Thermal Expansion | 13.0 x 10<sup>-6</sup> /°C |
Tensile Strength | 1310 MPa at 20°C |
Yield Strength | 1210 MPa at 20°C |
Elongation | 16% at 20°C |
Hardness | 35-45 HRC |
Oxidation Resistance | Excellent up to 1150°C |
Corrosion Resistance | Resists hot corrosion and oxidation |
Applications of IN939 Powder
Applications | Details |
---|---|
Gas Turbines | Combustion liners, transition ducts, nozzles |
Aircraft Engines | Turbine blades, vanes, combustors, afterburners |
Rocket Engines | Rocket nozzles, combustion chambers |
Power Generation | Heat exchangers, recuperators |
Chemical Processing | Valves, piping, heat exchangers |
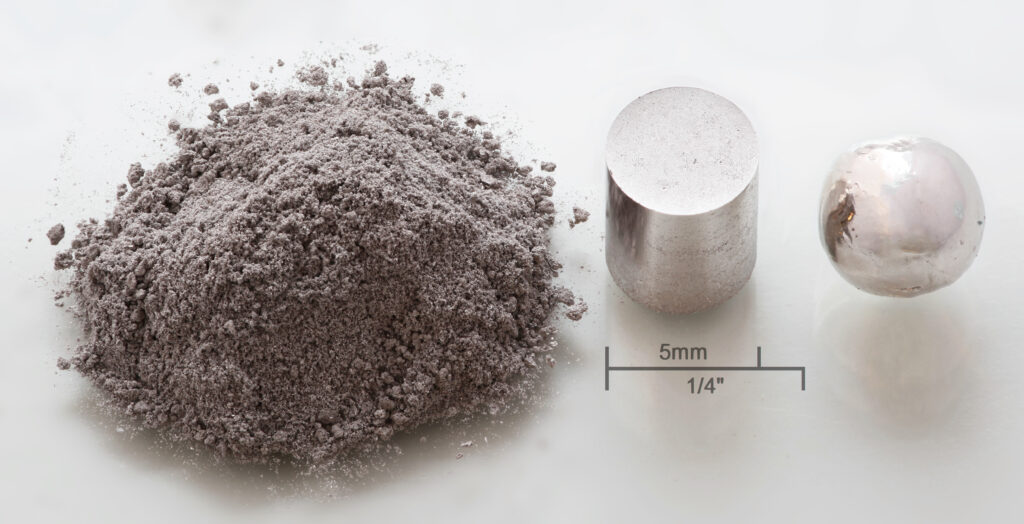
IN939 Powder Types
IN939 powder is commercially available in various size ranges optimized for different additive manufacturing processes:
- Laser powder bed fusion: 15-45 microns
- Binder jetting: 38-106 microns
- Directed energy deposition: 45-150 microns
Finer powder particles allow higher resolution but can be challenging to handle and flow. Coarser particles have better flowability but offer lower resolution.
IN939 Powder Characteristics
Parameter | Typical Range |
---|---|
Particle shape | Spherical |
Apparent density | 2.5-4.5 g/cm3 |
Tap density | 4-5.5 g/cm3 |
Flow rate | 25-35 s/50g |
Residual carbon | <0.1 wt% |
Residual oxygen | 0.06 wt% |
- Spherical morphology allows smooth powder flow and spreading.
- Higher tap density improves powder bed packing and reduces porosity.
- Faster flow rates mean better handling and spreading on the powder bed.
- Low impurity levels like oxygen and carbon prevent defects.
Applications of IN939 Parts
Additively manufactured IN939 components are used in the following high-temperature applications:
Gas Turbine Parts
- Combustion liners
- Transition ducts
- Turbine nozzles
- Shroud liners
Withstand hot combustion gases up to 1150°C with strength, creep and oxidation resistance. Complex cooling channels can be fabricated into the parts.
Aircraft Engine Components
- Turbine blades and vanes
- Afterburner parts
- Fuel nozzles
- Combustion chambers
Used for higher thrust and performance requirements. Offers lightweight yet durable components. Resists fatigue cracking from engine cycles.
Rocket Engine Nozzles and Chambers
Fabricate intricate nozzle geometries with enhanced heat transfer. Handle extreme temperatures and pressures during rocket launches and operations.
Heat Exchangers and Recuperators
Optimize complex heat exchanger designs with conformal channels and no internal supports needed. Improved efficiency of heat transfer between fluids.
IN939 Powder Suppliers
IN939 powder is supplied by leading metal powder manufacturers and specialized additive manufacturing powder producers:
Supplier | Description |
---|---|
Sandvik | Global supplier of Osprey® IN939 powders for AM |
Carpenter Technology | Producer of high-performance alloys like IN939 |
Praxair | Supplies a wide range of metal powders |
AP&C | Specializes in spherical powders for AM |
LPW Technology | Offers custom alloy development |
Things to consider when selecting an IN939 powder supplier:
- Technical expertise in manufacturing and sieving powder to application requirements
- Ability to customize particle size distribution, morphology, and impurity levels
- Stringent quality control of powder characteristics and consistency
- Responsiveness to quantity and lead time requirements
- Competitive pricing of powder suitable for industrial use
- Reputable name and experience in aerospace and industrial markets
IN939 Powder Pricing
IN939 powder is more expensive than standard alloys due to the proprietary compositions and specialized gas atomization process. Typical pricing ranges:
Powder Form | Price Range |
---|---|
IN939 for laser PBF | $180 – $220 per kg |
IN939 for binder jetting | $150 – $200 per kg |
IN939 for DED | $140 – $180 per kg |
- Prices vary based on order quantity, particle size range, quality level, etc.
- Economies of scale can be achieved with bulk orders of over 500 kg.
- Highly spherical and low impurity powder commands premium pricing.
- Recycled powder can cost 20-30% less than virgin powder.
Ways to reduce IN939 powder costs:
- Order larger quantities or customized particle distributions
- Consider recycled or lower grade powder if applicable
- Discuss payment terms and lead time flexibility
- Leverage competition between multiple suppliers
- Enter long term supply agreements for volume discounts
Installing an IN939 Powder Bed System
Installing and setting up a powder bed fusion system for IN939 requires careful planning:
Facility Considerations
- Allocate space for entire system footprint plus powder handling areas
- Ensure stable temperature/humidity for powder storage and handling
- Provide sufficient power requirements for system operation
- Have compressed air and inert gas supplies available
Equipment Setup
- Unpack machine components according to manual
- Install cooling and chiller systems if needed
- Connect power supply and inlet gas lines
- Level build platform and ensure all axes move smoothly
- Integrate monitoring and control software
First Article Procedures
- Test run machine using inert gas and dummy material
- Verify powder handling accessories function correctly
- Print simple geometries to confirm proper spreading, melting, etc.
- Optimize process parameters on initial test builds
- Adjust hardware and software based on first article results
Personnel Training
- Train staff on equipment operation, maintenance, and safety
- Go over powder handling procedures thoroughly
- Review software settings for building parts
- Discuss post-processing like supports removal and heat treating
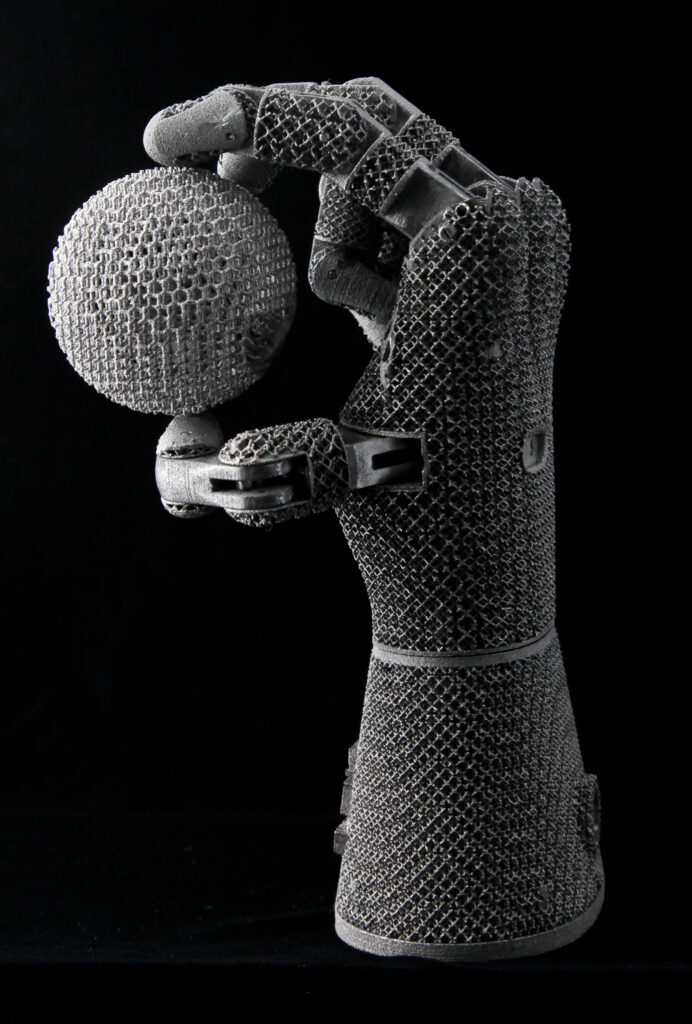
Operating an IN939 Powder Bed Machine
Consistent procedures must be followed when operating a powder bed system for IN939 builds:
Powder Handling
- Use appropriate PPE – nitrile gloves, dust mask, protective eyewear
- Carefully sieve powder to specification before use
- Avoid powder contact with moisture; store sealed with desiccant
- Fill/recover powder in ventilated environment or glove box
- Mix small batches of used and fresh powder to control reuse
Part Building
- Prepare build platform with release agent or abrasion blasting
- Evenly spread thin layers of powder 80-150μm deep
- Use optimized scan patterns and temperature profiles
- Maintain ambient temperatures of 20-25°C throughout print
- Monitor the build in-process and abort if any defects detected
Post Processing
- Allow parts to cool slowly before removing to prevent cracking
- Use powder blasting to remove loose powder from surfaces
- Cut away supports carefully, grind down surface roughness
- Hot isostatic press to eliminate internal voids and porosity
- Apply heat treatments to achieve required microstructure and relieve stresses
Maintenance
- Clean optics regularly to maintain laser power and spot size
- Verify powder bed, recoater, and dispensers moving smoothly
- Check inert gas filters and change as needed
- Calibrate levels, temperatures and atmosphere sensors
- Monitor power supply, chillers, and exhaust systems
Maintaining IN939 Printed Parts
To sustain optimal performance, IN939 printed components should follow standard high-temperature alloy maintenance procedures:
Cleaning
- Remove surface deposits and dirt regularly
- Allow soaking for strong adhered contaminants
- Use alkaline based cleaners compatible with IN939
- Rinse thoroughly after cleaning
Inspections
- Check for cracks, warping, oxidization, and erosion
- Perform scheduled visual and NDT inspections
- Monitor dimensions to identify deformation trends
Repairs
- Weld repair small cracks and defects (PTAW/GTAW)
- Machining and grinding can refurbish worn-out sections
- Replace components showing widespread damage
Coatings
- Apply oxidation or corrosion resistant coatings
- Use aluminum/platinum diffusion coatings up to 2 mils thick
- Re-coat after stripping damaged layers
Records
- Document operating hours and duty cycles
- Log all inspections, repairs, and maintenance
- Track lifecycle costs for replacement planning
Buying an IN939 Powder Bed Printer
Here are key considerations when investing in a powder bed fusion system for IN939:
Build Envelope
- Match envelope size to your application and throughput needs
- Larger capacity >500 mm x 500 mm x 500 mm for high production
- Smaller <300 mm x 300 mm x 300 mm for research or prototypes
Laser Power
- Higher power >400 W allows faster builds of larger parts
- Lower power <200 W suitable for smaller components with fine features
Temperature Control
- Tightly controlled preheating up to 200°C for reduced stresses
- High temperatures >1500°C needed for sintering IN939 properly
Powder Handling
- Closed loop powder systems prevent oxidation and contamination
- Automated powder sieving and mixing improves reuse
- Vacuum or inert gas chambers give highest quality
Software
- User-friendly interface for preparing and optimizing builds
- Precision monitoring and diagnostics during build
- Tools for workflow automation from order to post-processing
Costs
- Industrial systems over $500,000, research systems below $200,000
- Operating costs depend on materials usage and post-processing
- Optimize production planning to maximize system utilization
Service and Support
- Look for responsive technical support and maintenance
- Application expertise in high-temperature alloys is vital
- Training on best practices tailored to your processes
Pros and Cons of IN939 Powder Bed Fusion Technology
Advantages | Disadvantages |
---|---|
Complex geometries and lattices possible | Limited size based on build envelope |
Minimal machining and customization required | Relatively slow build rates |
Reduced waste compared to subtractive methods | High equipment and material costs |
Properties comparable to wrought materials | Prone to porosity and residual stresses |
Can produce components unattainable by casting/forging | Depowdering and post-processing increase costs |
Net shape manufacturing minimizes raw material required | Susceptible to distortion and cracking of parts |
Improves buy-to-fly ratio up to 1:1 | Requires support structures and removal |
IN939 Powder vs Cast vs Wrought Material
Parameter | Powder Bed Fusion | Cast | Wrought |
---|---|---|---|
Cost | High | Low | Moderate |
Density | Moderate, depends on porosity | High | Highest |
Strength | High | Moderate | Highest |
Ductility | Moderate | Low | Highest |
Oxidation Resistance | Similar | Similar | Similar |
Maximum Size | Limited by build volume | Very large sections possible | Limited by forging equipment |
Post Processing | Moderate | Minimal | High |
Lead Times | Rapid prototyping possible | Slow pattern production | Slow forming steps |
Geometry | Most complex shapes | Moderate complexity | Simple shapes |
Surface Finish | Rough | Moderate | Smoothest |
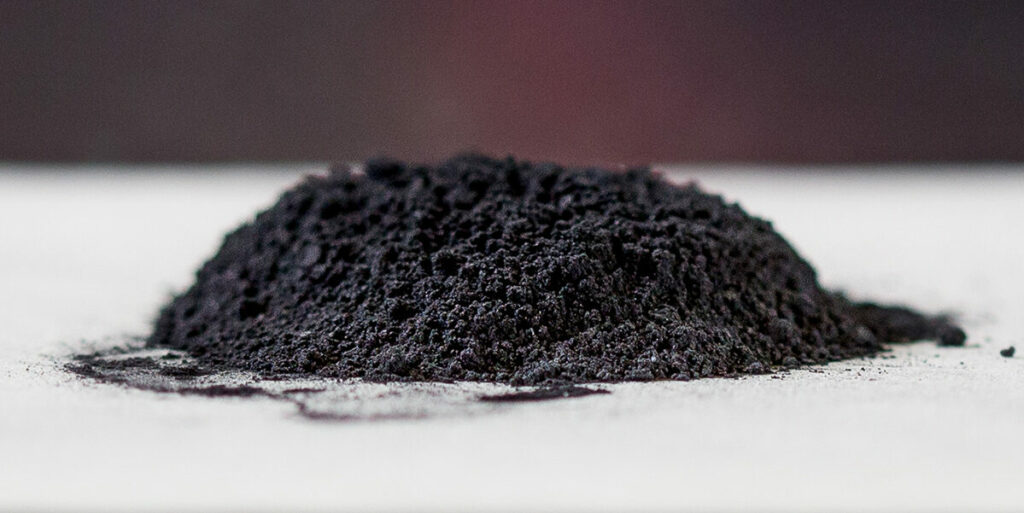
FAQ
Here are answers to some frequently asked questions about IN939 powder:
Q: What particle size is best for laser powder bed fusion of IN939?
A: A particle size range of 15-45 microns is recommended, with the majority between 20-35 microns for optimal packing density and resolution.
Q: Does reused IN939 powder have the same properties as virgin powder?
A: With controlled blending and sieving, reused IN939 powder can approach virgin powder properties. But higher reuse fractions may cause lower density and mechanical properties.
Q: What heat treatments are used for IN939 parts?
A: Solution heat treatment above 1260°C, followed by aging at 850-980°C is typically used to achieve optimal microstructure and properties.
Q: Does IN939 require hot isostatic pressing (HIP) post-processing?
A: HIP is highly recommended for fully dense IN939 parts, in order to eliminate internal voids and achieve maximum fatigue resistance.
Q: What defect repair methods can be used for IN939 components?
A: Welding techniques like PTAW and GTAW allow localized repair of cracks and defects. Machining can also refurbish damaged or worn sections.
Q: What are common applications for binder jetting using IN939?
A: Binder jet IN939 is used for less demanding applications like prototypes, tooling components, and industrial parts operating below 1000°C.
Q: Is IN939 compatible with direct energy deposition (DED) processes?
A: Yes, IN939 performs well in DED although higher porosity is observed compared to powder bed methods.
Q: Does IN939 require any coatings or surface treatments?
A: IN939 parts can be coated with aluminide or platinum diffusion coatings to further enhance oxidation and corrosion resistance at high temperatures.