IN939 ist ein beliebtes Superlegierungspulver auf Nickelbasis, das in verschiedenen Hochtemperaturanwendungen wie Gasturbinen und Flugzeugtriebwerken eingesetzt wird. Dieser Leitfaden bietet einen umfassenden Überblick über IN939 Pulver, einschließlich seiner Eigenschaften, Anwendungen, Lieferanten, Preise, Installation, Betrieb und Wartung.
Überblick über IN939-Pulver
IN939 ist eine ausscheidungsgehärtete Superlegierung auf Nickelbasis, die hervorragende mechanische Eigenschaften und eine hohe Beständigkeit gegen thermische Ermüdung und Kriechen bei hohen Temperaturen aufweist. Einige der wichtigsten Merkmale von IN939-Pulver sind:
- Hohe Festigkeit und Härte - Bietet im Vergleich zu anderen Legierungen eine höhere Zug- und Streckgrenze. Die Härte reicht von 35-45 HRC.
- Hervorragende Kriechfestigkeit - Hervorragende Zeitstandfestigkeit bis zu 700°C (1300°F).
- Beständigkeit gegen thermische Ermüdung - Widersteht Rissen bei wiederholten Heiz- und Kühlzyklen.
- Oxidationsbeständigkeit - Bildet eine schützende Oxidschicht, die Korrosion und Oxidation verhindert.
- Schweißbarkeit - Kann mit herkömmlichen Schweißverfahren geschweißt werden. Erfordert eine Wärmebehandlung nach dem Schweißen.
- Vielseitige Anwendungen - für Verbrennungsauskleidungen, Übergangskanäle, Turbinenschaufeln, Schaufeln, Raketendüsen usw.
IN939 ist in Pulverform für die additive Fertigung erhältlich, so dass komplexe Geometrien direkt aus dem Pulver hergestellt werden können. Die wichtigsten Eigenschaften und Anwendungen von IN939-Pulver sind unten aufgeführt:
Eigenschaften von IN939-Pulver
Eigenschaften | Einzelheiten |
---|---|
Zusammensetzung | Nickelbasis mit Zusätzen von Titan, Aluminium und Chrom |
Dichte | 8,2 g/cm3 |
Schmelzpunkt | ~1350°C |
Wärmeleitfähigkeit | 11 W/m-K bei 20°C |
Wärmeausdehnungskoeffizient | 13,0 x 10-6 /°C |
Zugfestigkeit | 1310 MPa bei 20°C |
Streckgrenze | 1210 MPa bei 20°C |
Dehnung | 16% bei 20°C |
Härte | 35-45 HRC |
Oxidationsbeständigkeit | Ausgezeichnet bis zu 1150°C |
Korrosionsbeständigkeit | Widersteht Heißkorrosion und Oxidation |
Anwendungen von IN939-Pulver
Anwendungen | Einzelheiten |
---|---|
Gasturbinen | Verbrennungseinsätze, Übergangskanäle, Düsen |
Flugzeugtriebwerke | Turbinenschaufeln, Leitschaufeln, Brennkammern, Nachbrenner |
Raketentriebwerke | Raketendüsen, Brennkammern |
Stromerzeugung | Wärmetauscher, Rekuperatoren |
Chemische Verarbeitung | Ventile, Rohrleitungen, Wärmetauscher |
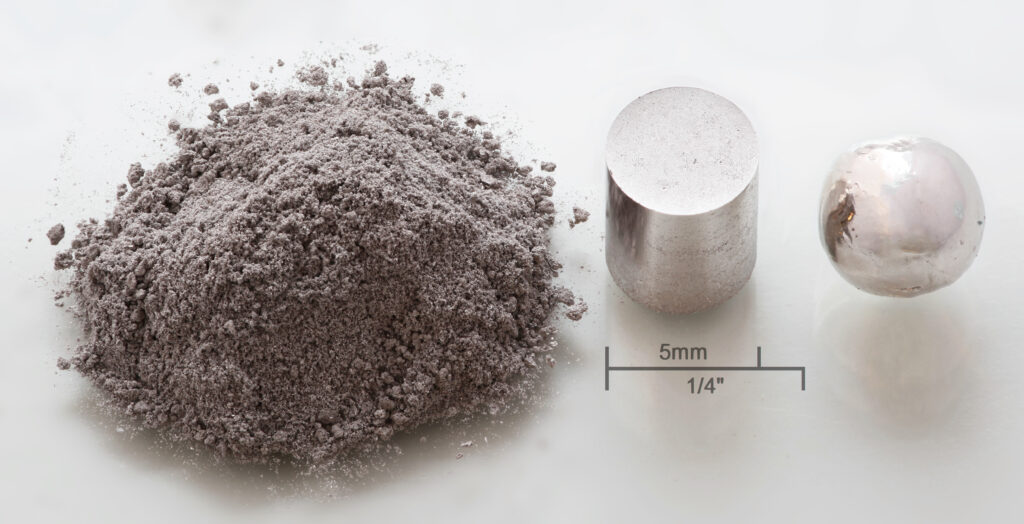
IN939 Pulvertypen
IN939-Pulver ist im Handel in verschiedenen Größen erhältlich, die für unterschiedliche additive Fertigungsverfahren optimiert sind:
- Laser-Pulverbettschweißen: 15-45 Mikrometer
- Binder Jetting: 38-106 Mikrometer
- Gezielte Energiedeposition: 45-150 Mikrometer
Feinere Pulverpartikel ermöglichen eine höhere Auflösung, können aber schwierig zu handhaben und zu fließen sein. Gröbere Partikel haben eine bessere Fließfähigkeit, bieten aber eine geringere Auflösung.
IN939 Pulvereigenschaften
Parameter | Typischer Bereich |
---|---|
Partikelform | Sphärisch |
Scheinbare Dichte | 2,5-4,5 g/cm3 |
Dichte des Gewindebohrers | 4-5,5 g/cm3 |
Durchflussmenge | 25-35 s/50g |
Restlicher Kohlenstoff | <0,1 wt% |
Restsauerstoff | 0,06 wt% |
- Die kugelförmige Morphologie ermöglicht einen reibungslosen Pulverfluss und eine gleichmäßige Ausbreitung.
- Eine höhere Abstichdichte verbessert die Packung des Pulverbettes und verringert die Porosität.
- Schnellere Durchflussraten bedeuten bessere Handhabung und Verteilung auf dem Pulverbett.
- Niedrige Verunreinigungsgrade wie Sauerstoff und Kohlenstoff verhindern Defekte.
Anwendungen von IN939-Teilen
Die additiv gefertigten IN939-Bauteile werden in den folgenden Hochtemperaturanwendungen eingesetzt:
Gasturbinenteile
- Verbrennungsauskleidungen
- Übergangskanäle
- Turbinen-Düsen
- Leichentücher
Widersteht heißen Verbrennungsgasen bis zu 1150 °C und ist fest, kriechfähig und oxidationsbeständig. Komplexe Kühlkanäle können in die Teile eingearbeitet werden.
Triebwerkskomponenten für Flugzeuge
- Turbinenschaufeln und Schaufeln
- Teile für Nachbrenner
- Kraftstoffdüsen
- Brennkammern
Wird für höhere Schubkraft- und Leistungsanforderungen verwendet. Bietet leichte und dennoch haltbare Komponenten. Widersteht Ermüdungsrissen durch Motorzyklen.
Düsen und Kammern von Raketentriebwerken
Herstellung komplizierter Düsengeometrien mit verbesserter Wärmeübertragung. Bewältigen extreme Temperaturen und Drücke bei Raketenstarts und -betrieb.
Wärmetauscher und Rekuperatoren
Optimierung komplexer Wärmetauscherkonstruktionen mit konformen Kanälen, die keine internen Stützen benötigen. Verbesserte Effizienz der Wärmeübertragung zwischen Flüssigkeiten.
IN939 Pulver Lieferanten
IN939-Pulver wird von führenden Metallpulverherstellern und spezialisierten Pulverproduzenten für die additive Fertigung geliefert:
Anbieter | Beschreibung |
---|---|
Sandvik | Weltweiter Anbieter von Osprey® IN939-Pulvern für AM |
Tischlertechnik | Produzent von Hochleistungslegierungen wie IN939 |
Praxair | Liefert eine breite Palette von Metallpulvern |
AP&C | Spezialisiert auf sphärische Pulver für AM |
LPW-Technologie | Bietet kundenspezifische Legierungsentwicklung |
Was ist bei der Auswahl eines Lieferanten für IN939-Pulver zu beachten?
- Technisches Fachwissen bei der Herstellung und dem Sieben von Pulver nach Anwendungsanforderungen
- Möglichkeit der individuellen Anpassung von Partikelgrößenverteilung, Morphologie und Verunreinigungsgrad
- Strenge Qualitätskontrolle der Pulvereigenschaften und -konsistenz
- Reagieren auf Mengen- und Vorlaufzeitanforderungen
- Wettbewerbsfähige Preise für industriell verwendbares Pulver
- Renommierter Name und Erfahrung auf den Märkten der Luft- und Raumfahrt und der Industrie
IN939 Pulver Preisgestaltung
IN939-Pulver ist aufgrund der besonderen Zusammensetzung und des speziellen Gasverdüsungsverfahrens teurer als Standardlegierungen. Typische Preisspannen:
Pulverform | Preisspanne |
---|---|
IN939 für Laser PBF | $180 - $220 pro kg |
IN939 für Bindemittelstrahlverfahren | $150 - $200 pro kg |
IN939 für DED | $140 - $180 pro kg |
- Die Preise variieren je nach Bestellmenge, Partikelgrößenbereich, Qualitätsniveau usw.
- Bei Großbestellungen von über 500 kg können Größenvorteile erzielt werden.
- Hochgradig kugelförmiges und verunreinigungsarmes Pulver erzielt Spitzenpreise.
- Recyceltes Pulver kann 20-30% weniger kosten als Neupulver.
Möglichkeiten zur Senkung der Kosten für IN939-Pulver:
- Bestellen Sie größere Mengen oder individuelle Partikelverteilungen
- Gegebenenfalls recyceltes oder minderwertiges Pulver in Betracht ziehen
- Erörterung der Zahlungsbedingungen und der Flexibilität der Vorlaufzeit
- Nutzen Sie den Wettbewerb zwischen mehreren Anbietern
- Abschluss langfristiger Liefervereinbarungen für Mengenrabatte
Installation eines IN939-Pulverbettsystems
Die Installation und Einrichtung eines Pulverbettschmelzsystems für IN939 erfordert eine sorgfältige Planung:
Überlegungen zur Einrichtung
- Zuweisung von Platz für die gesamte Systemgrundfläche plus Bereiche für die Pulververarbeitung
- Gewährleistung einer stabilen Temperatur/Luftfeuchtigkeit für die Lagerung und Handhabung von Pulver
- Ausreichender Strombedarf für den Systembetrieb
- Druckluft- und Inertgasvorräte bereithalten
Einrichtung der Ausrüstung
- Auspacken der Maschinenkomponenten entsprechend der Anleitung
- Installation von Kühl- und Kältesystemen, falls erforderlich
- Strom- und Gaszufuhrleitungen anschließen
- Nivellieren Sie die Bauplattform und stellen Sie sicher, dass sich alle Achsen reibungslos bewegen.
- Integration von Überwachungs- und Steuerungssoftware
Erster Artikel Verfahren
- Testlauf der Maschine mit Inertgas und Dummy-Material
- Überprüfen Sie die korrekte Funktion des Zubehörs für die Pulverförderung
- Drucken Sie einfache Geometrien, um die korrekte Ausbreitung, das Schmelzen usw. zu überprüfen.
- Optimierung von Prozessparametern bei ersten Testläufen
- Anpassung von Hardware und Software auf der Grundlage der Ergebnisse des ersten Artikels
Ausbildung des Personals
- Schulung des Personals in Betrieb, Wartung und Sicherheit der Geräte
- Gehen Sie die Verfahren zur Handhabung von Pulver gründlich durch
- Überprüfen der Softwareeinstellungen für Gebäudeteile
- Erörterung der Nachbearbeitung wie Entfernen von Auflagen und Wärmebehandlung
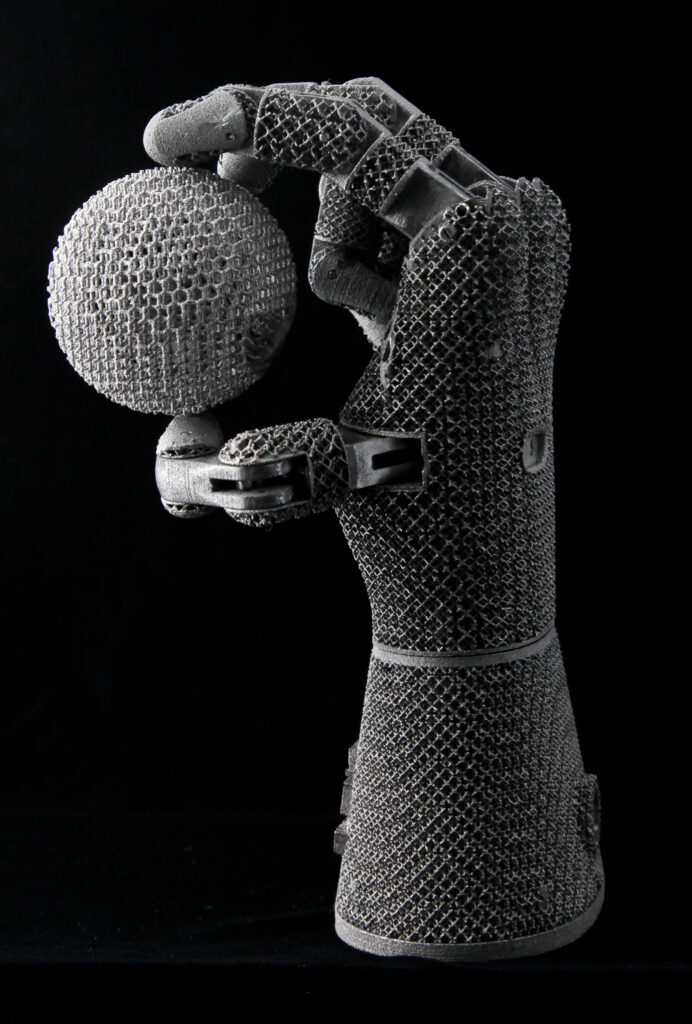
Bedienung einer IN939-Pulverbettmaschine
Beim Betrieb eines Pulverbettsystems für IN939-Aufbauten müssen einheitliche Verfahren eingehalten werden:
Handhabung von Pulver
- Geeignete PSA verwenden - Nitrilhandschuhe, Staubmaske, Schutzbrille
- Pulver vor der Verwendung sorgfältig nach Spezifikation absieben
- Vermeiden Sie den Kontakt des Pulvers mit Feuchtigkeit; lagern Sie es versiegelt mit einem Trockenmittel.
- Pulver in einer belüfteten Umgebung oder in einem Handschuhfach abfüllen/zurückgewinnen
- Mischen Sie kleine Chargen von gebrauchtem und frischem Pulver, um die Wiederverwendung zu kontrollieren.
Teil Gebäude
- Vorbereitung der Bauplattform mit Trennmittel oder Abrasionsstrahlen
- Gleichmäßige Verteilung dünner Pulverschichten von 80-150μm Tiefe
- Verwendung optimierter Scanmuster und Temperaturprofile
- Halten Sie während des gesamten Druckvorgangs eine Umgebungstemperatur von 20-25 °C aufrecht.
- Überwachen Sie die Erstellung während des Prozesses und brechen Sie den Vorgang ab, wenn ein Fehler entdeckt wird.
Nachbearbeitung
- Lassen Sie die Teile vor dem Ausbau langsam abkühlen, um Risse zu vermeiden.
- Verwenden Sie Pulverstrahlen, um loses Pulver von Oberflächen zu entfernen
- Stützen vorsichtig wegschneiden, Oberflächenrauhigkeit abschleifen
- Heißisostatisches Pressen zur Beseitigung von inneren Hohlräumen und Porosität
- Wärmebehandlungen zur Erzielung des gewünschten Gefüges und zum Abbau von Spannungen
Wartung
- Reinigen Sie die Optik regelmäßig, um die Laserleistung und die Spotgröße zu erhalten.
- Überprüfen Sie, ob sich Pulverbett, Rückstrahler und Dosierer reibungslos bewegen.
- Inertgasfilter prüfen und bei Bedarf wechseln
- Kalibrierung von Füllständen, Temperaturen und Atmosphärensensoren
- Überwachung der Stromversorgung, der Kühlanlagen und der Abluftanlagen
Pflege der IN939-Druckteile
Um eine optimale Leistung aufrechtzuerhalten, sollten die gedruckten IN939-Bauteile nach den Standardverfahren für Hochtemperaturlegierungen gewartet werden:
Reinigung
- Oberflächenablagerungen und Schmutz regelmäßig entfernen
- Einweichen lassen bei stark anhaftenden Verunreinigungen
- Verwenden Sie alkalische Reiniger, die mit IN939 kompatibel sind.
- Nach der Reinigung gründlich ausspülen
Inspektionen
- Prüfen Sie auf Risse, Verformung, Oxidation und Erosion
- Planmäßige visuelle und NDT-Inspektionen durchführen
- Überwachung der Abmessungen zur Ermittlung von Verformungstrends
Reparaturen
- Reparatur kleiner Risse und Defekte durch Schweißen (PTAW/GTAW)
- Durch Bearbeitung und Schleifen können verschlissene Abschnitte aufgearbeitet werden
- Ersetzen Sie Komponenten, die große Schäden aufweisen
Beschichtungen
- Auftragen von oxidations- oder korrosionsbeständigen Beschichtungen
- Verwendung von Aluminium/Platin-Diffusionsbeschichtungen mit einer Dicke von bis zu 2 Millimetern
- Neubeschichtung nach dem Abziehen beschädigter Schichten
Aufzeichnungen
- Betriebsstunden und Arbeitszyklen dokumentieren
- Protokollierung aller Inspektionen, Reparaturen und Wartungsarbeiten
- Verfolgen Sie die Lebenszykluskosten für die Ersatzplanung
Kauf eines IN939-Pulverbettdruckers
Hier sind die wichtigsten Überlegungen für die Investition in ein Pulverbettschmelzsystem für IN939:
Umschlag bauen
- Passen Sie die Umschlaggröße an Ihre Anwendung und Ihren Durchsatzbedarf an
- Größere Kapazität >500 mm x 500 mm x 500 mm für hohe Produktion
- Kleinere <300 mm x 300 mm x 300 mm für Forschung oder Prototypen
Laserleistung
- Höhere Leistung >400 W ermöglicht schnellere Fertigung größerer Teile
- Geringere Leistung <200 W, geeignet für kleinere Bauteile mit feinen Merkmalen
Temperaturkontrolle
- Streng kontrollierte Vorwärmung auf bis zu 200°C für reduzierte Spannungen
- Hohe Temperaturen >1500°C erforderlich, um IN939 richtig zu sintern
Handhabung von Pulver
- Geschlossene Pulversysteme verhindern Oxidation und Verunreinigung
- Automatisierte Pulversiebung und -mischung verbessert die Wiederverwendung
- Vakuum- oder Inertgas-Kammern bieten höchste Qualität
Software
- Benutzerfreundliche Schnittstelle zur Vorbereitung und Optimierung von Builds
- Präzise Überwachung und Diagnose während des Baus
- Tools für die Workflow-Automatisierung von der Bestellung bis zur Nachbearbeitung
Kosten
- Industrielle Systeme über $500.000, Forschungssysteme unter $200.000
- Betriebskosten hängen vom Materialverbrauch und der Nachbearbeitung ab
- Optimierung der Produktionsplanung zur Maximierung der Systemauslastung
Service und Unterstützung
- Suchen Sie nach reaktionsschneller technischer Unterstützung und Wartung
- Anwendungswissen über Hochtemperaturlegierungen ist entscheidend
- Schulungen zu bewährten Verfahren, die auf Ihre Prozesse zugeschnitten sind
Vor- und Nachteile der IN939 Pulverbettfusionstechnologie
Vorteile | Benachteiligungen |
---|---|
Komplexe Geometrien und Gitternetze möglich | Begrenzte Größe aufgrund des Bauraums |
Minimale Bearbeitung und Anpassung erforderlich | Relativ langsame Aufbauraten |
Weniger Abfall im Vergleich zu subtraktiven Methoden | Hohe Ausrüstungs- und Materialkosten |
Eigenschaften vergleichbar mit geschmiedeten Materialien | Anfällig für Porosität und Eigenspannungen |
Kann Komponenten herstellen, die durch Gießen/Schmieden nicht zu erreichen sind | Entparzellierung und Nachbearbeitung erhöhen die Kosten |
Nettoformfertigung minimiert den Rohstoffbedarf | Anfällig für Verformung und Rissbildung an Teilen |
Verbessert das Verhältnis von Kauf zu Flug auf bis zu 1:1 | Erfordert Stützstrukturen und Entfernung |
IN939 Pulver vs. gegossenes vs. geschmiedetes Material
Parameter | Pulverbett Fusion | Gießen | Geschmiedet |
---|---|---|---|
Kosten | Hoch | Niedrig | Mäßig |
Dichte | Mäßig, abhängig von der Porosität | Hoch | Höchste |
Stärke | Hoch | Mäßig | Höchste |
Duktilität | Mäßig | Niedrig | Höchste |
Oxidationsbeständigkeit | Ähnlich | Ähnlich | Ähnlich |
Maximale Größe | Begrenzt durch das Bauvolumen | Sehr große Abschnitte möglich | Begrenzt durch die Schmiedeausrüstung |
Nachbearbeitung | Mäßig | Minimal | Hoch |
Vorlaufzeiten | Schnelles Prototyping möglich | Langsame Musterproduktion | Langsame Umformungsschritte |
Geometrie | Komplexeste Formen | Mäßige Komplexität | Einfache Formen |
Oberfläche | Raue | Mäßig | Glatteste |
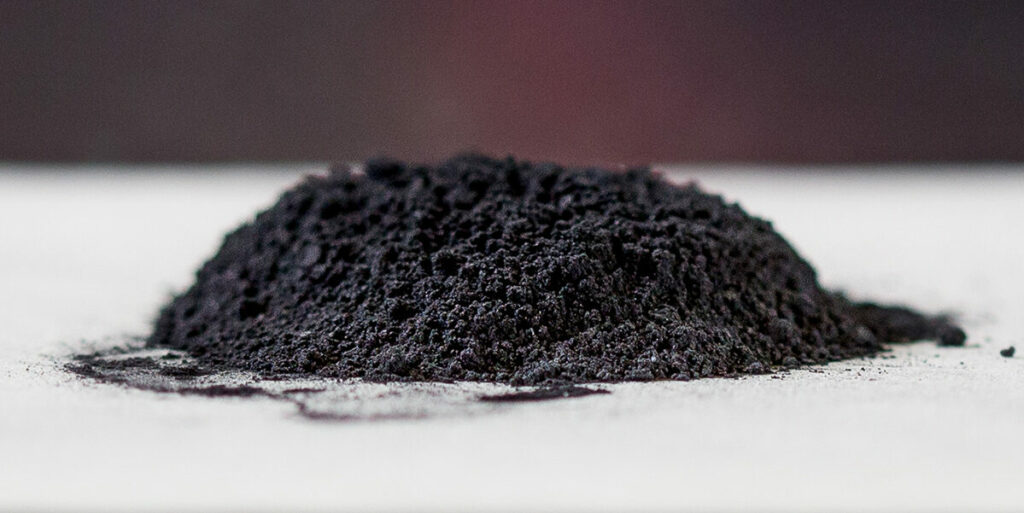
FAQ
Hier finden Sie Antworten auf einige häufig gestellte Fragen zu IN939-Pulver:
F: Welche Partikelgröße eignet sich am besten für das Laser-Pulverbettschmelzen von IN939?
A: Es wird ein Partikelgrößenbereich von 15-45 Mikron empfohlen, wobei der Großteil zwischen 20-35 Mikron liegt, um eine optimale Packungsdichte und Auflösung zu erreichen.
F: Hat wiederverwendetes IN939-Pulver die gleichen Eigenschaften wie Neupulver?
A: Bei kontrolliertem Mischen und Sieben kann wiederverwendetes IN939-Pulver die Eigenschaften von Neupulver erreichen. Höhere Wiederverwendungsanteile können jedoch zu einer geringeren Dichte und geringeren mechanischen Eigenschaften führen.
F: Welche Wärmebehandlungen werden für IN939-Teile verwendet?
A: Eine Lösungsglühung bei über 1260 °C und eine anschließende Alterung bei 850-980 °C werden in der Regel eingesetzt, um ein optimales Mikrogefüge und optimale Eigenschaften zu erzielen.
F: Ist für IN939 eine Nachbearbeitung durch heißisostatisches Pressen (HIP) erforderlich?
A: HIP wird für vollständig dichte IN939-Teile dringend empfohlen, um innere Hohlräume zu beseitigen und eine maximale Ermüdungsfestigkeit zu erreichen.
F: Welche Reparaturmethoden können für IN939-Bauteile verwendet werden?
A: Schweißtechniken wie PTAW und GTAW ermöglichen die örtliche Reparatur von Rissen und Defekten. Durch maschinelle Bearbeitung können auch beschädigte oder abgenutzte Abschnitte aufgearbeitet werden.
F: Was sind gängige Anwendungen für die Bindemittelausspritzung mit IN939?
A: Binder Jet IN939 wird für weniger anspruchsvolle Anwendungen wie Prototypen, Werkzeugkomponenten und Industrieteile verwendet, die bei Temperaturen unter 1000°C arbeiten.
F: Ist IN939 mit Verfahren der direkten Energieabscheidung (DED) kompatibel?
A: Ja, IN939 eignet sich gut für die DED, obwohl im Vergleich zu Pulverbettverfahren eine höhere Porosität zu beobachten ist.
F: Sind für IN939 irgendwelche Beschichtungen oder Oberflächenbehandlungen erforderlich?
A: IN939-Teile können mit Aluminid- oder Platindiffusionsbeschichtungen versehen werden, um die Oxidations- und Korrosionsbeständigkeit bei hohen Temperaturen weiter zu verbessern.